Understanding Inventory Management Strategies
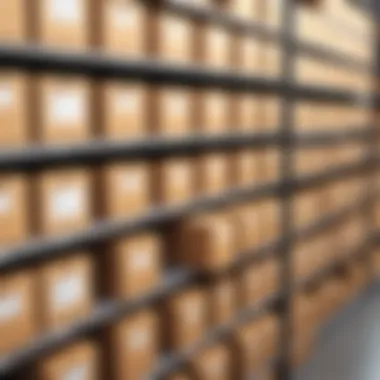
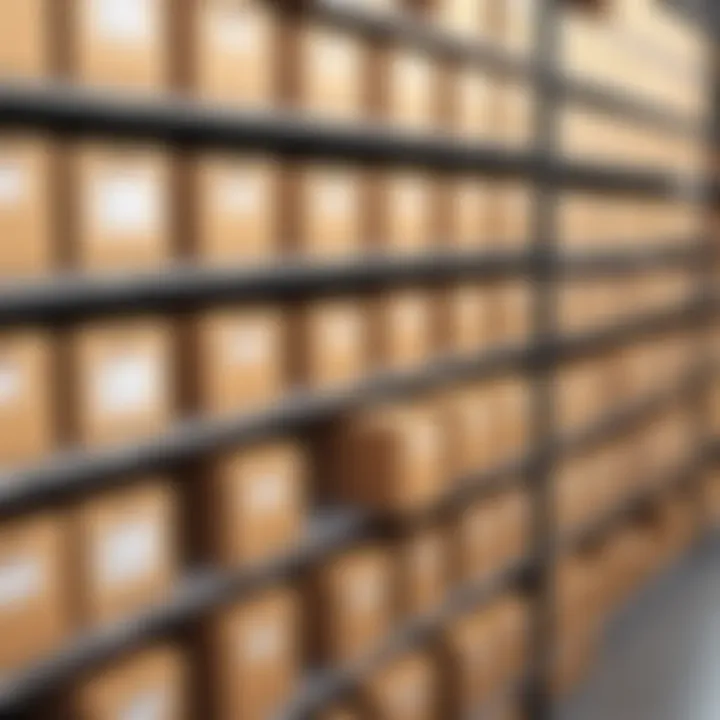
Intro
In today’s competitive landscape, effective inventory management defines the line between success and downfall for many organizations. A sound inventory strategy ensures not only that products are available when needed but also minimizes excess stock, which can tie up capital. This article serves as a comprehensive guide, illuminating the various types of inventory management methodologies businesses draw upon to meet their goals efficiently.
Acknowledging the need for an optimal balance, we will explore both traditional and innovative methods. We aim to arm decision-makers, IT professionals, and entrepreneurs with the knowledge needed to refine their inventory strategies. By dissecting crucial software features, comparison metrics, and other pertinent factors, our objective is to provide practical insights that can enhance operational efficiency and profitability.
Key Software Features
To streamline inventory processes, businesses depend heavily on specialized software. Understanding the key features of this software can assist in selecting the right tools.
Essential functionalities
Inventory management software typically encompasses a range of essential functionalities:
- Stock tracking: This feature allows businesses to monitor their inventory levels in real-time, facilitating informed decision-making concerning stock replenishment.
- Order management: Managing both purchase orders and customer orders is vital. Good software automates these tasks to ensure timely fulfillment without overcommitting stock.
- Reporting and analytics: Robust reporting tools offer insights into stock levels, sales trends, and areas needing improvement. This information can guide inventory decisions.
Advanced capabilities
In addition to the essentials, many software options offer advanced capabilities:
- Integration with other systems: Software that integrates seamlessly with ERP or CRM can enhance data accuracy and improve coordination across departments.
- Multi-location support: For businesses operating in multiple locations, this feature allows for centralized inventory tracking. It simplifies inventory adjustments, transfers, and assessments.
- Demand forecasting: Utilizing historical data, some software can predict future demand. This allows businesses to optimize stock levels proactively, rather than reactively.
"Effective inventory management is not just about keeping count. It’s about making informed decisions that affect the whole business."
Comparison Metrics
When evaluating inventory management strategies, several comparison metrics can aid decision-making.
Cost analysis
Cost efficiency is paramount. It's not only about purchasing the software but also considering the overall cost of implementation, maintenance, and potential savings that can arise from improved inventory practices. Key points include:
- Initial costs: Upfront costs associated with software can vary widely.
- Operational savings: In assessing long-term value, businesses must weigh savings against expenditures that arise from holding excess stock.
Performance benchmarks
Performance benchmarks can illustrate how well a particular inventory method or software performs. This includes:
- Turnover rates: How quickly inventory cycles through the system.
- Stockouts and overstock situations: Measuring frequency can show how effectively a strategy meets demands.
Evaluating these metrics provides valuable insights, enabling informed comparisons across various methodologies and solutions.
In summary, understanding the nuances of inventory management can empower organizations to enhance their operational effectiveness. By exploring software features and comparison metrics, this article aims to offer valuable insights for optimizing inventory strategies.
Overview of Inventory Management
Effective inventory management serves as a cornerstone of operational success across various industries. It involves tracking and controlling inventory levels to ensure that the right amount of stock is available at any given time. The significance of inventory management cannot be overstated; it affects cash flow, operational efficiency, and customer satisfaction. Without an efficient system, organizations risk incurring unnecessary costs or, alternatively, losing sales due to stock shortages.
Definition and Importance
Inventory management refers to the processes and systems that oversee the ordering, storage, and utilization of inventory. This encompasses raw materials, work-in-progress products, and finished goods. The primary goal is to maintain optimal stock levels that align with demand while minimizing waste and inefficiencies.
The importance of inventory management lies in its direct impact on a company's bottom line. A well-structured inventory system can lead to:
- Cost Efficiency: Reducing excess stock lowers holding costs.
- Increased Profitability: Timely stock ensures sales opportunities are not missed.
- Improved Customer Satisfaction: Availability of products leaves customers happy, ultimately driving repeat business.
In essence, accurate inventory management creates a balance between supply and demand that is critical for continued success.
Key Concepts
Understanding the key concepts related to inventory management is essential for anyone aiming to refine their approach. Below are several concepts that highlight the complexity of inventory management:
- Stock Levels: The various states of inventory need careful oversight to avoid overstocking or stockouts.
- Lead Time: This is the time taken from placing an order to its receipt. Reducing lead time increases responsiveness to demand changes.
- Turnover Rate: This metric tracks how often inventory is sold and replaced over a specific period. A higher turnover rate indicates effective sales and inventory replenishment.
- Safety Stock: This is the extra inventory kept to mitigate the risk of stockouts due to demand fluctuations or supply chain disruptions.
By grasping these key concepts, decision-makers are better positioned to implement effective strategies that optimize inventory management. Understanding these principles sets the groundwork for exploring specific inventory systems and methodologies in subsequent sections.
Types of Inventory Systems
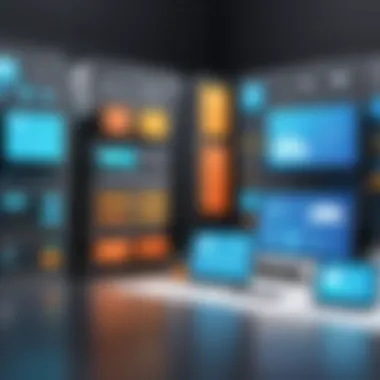
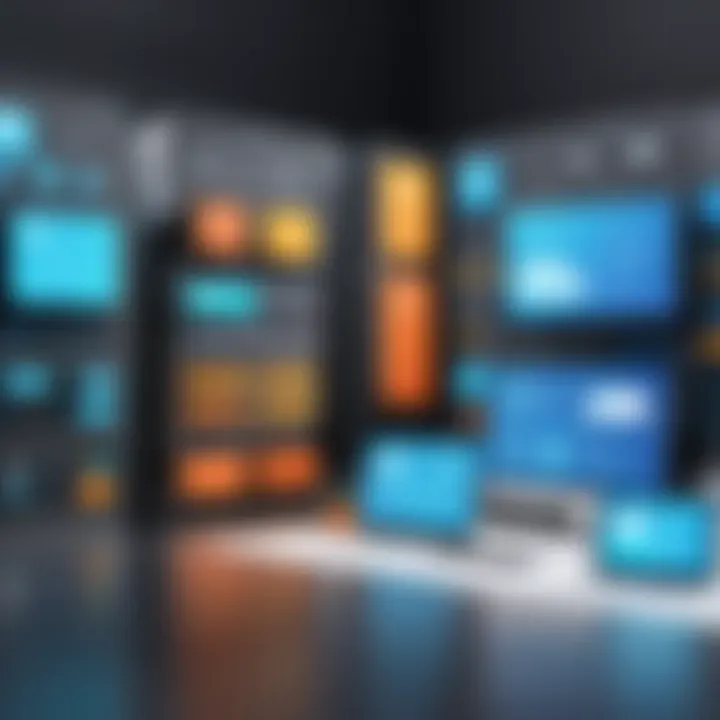
Inventory systems play a crucial role in ensuring the smooth operation of business processes. Organizations must manage their stock levels effectively to meet customer demand while minimizing costs. Selecting the right inventory system contributes significantly to achieving these goals. The appropriate system can lead to better visibility of stock levels, enhance forecasting accuracy, and streamline inventory operations.
When it comes to types of inventory systems, two principal methodologies emerge: the Perpetual Inventory System and the Periodic Inventory System. Each of these systems has distinct characteristics, advantages, and considerations that can significantly impact a business's overall inventory management strategy.
Perpetual Inventory System
The Perpetual Inventory System is a method that provides real-time tracking of inventory levels. This system relies on continuous updates to inventory records, allowing businesses to maintain an accurate view of stock quantities at all times. Each transaction, whether it is a sale or a purchase, immediately updates the inventory count.
Advantages
- Real-Time Data: This system delivers accurate, up-to-date inventory information, which can be crucial for timely decision-making.
- Improved Inventory Control: Organizations can minimize the risk of stockouts and overstock situations, thus improving customer satisfaction.
- Easier Auditing Processes: Since inventory records are consistently updated, auditing becomes more straightforward.
Considerations
- Implementation Costs: Setting up a perpetual system may require investment in inventory management software and training, which can be a barrier for some businesses.
- Data Management: Collecting and maintaining accurate data is essential. Inaccurate data entry can lead to problems in inventory tracking.
Periodic Inventory System
In contrast to the perpetual approach, the Periodic Inventory System involves counting the inventory at specific intervals, such as weekly, monthly, or annually. During these periodic counts, businesses assess the stock on hand and adjust their records accordingly.
Advantages
- Simplicity and Cost-Effectiveness: This system can be easier to implement and requires less sophisticated technology, making it suitable for small businesses.
- Lower Operational Costs: Fewer transactions to record can reduce administrative overhead.
Considerations
- Less Accurate: Since major adjustments happen at set intervals, discrepancies may go unnoticed leading to potential stockouts or excess inventory.
- Time Consuming: Physical counts can be labor-intensive and disruptive to normal business operations.
Inventory Management Methodologies
Inventory management methodologies are essential in organizing and controlling stock levels effectively. These methodologies help businesses optimize processes, reduce costs, and improve service levels. Implementing the right methodology allows companies to respond swiftly to market shifts while minimizing waste. Each methodology presents unique benefits and drawbacks, making it crucial for decision-makers to align them with organizational goals. Choosing the appropriate strategy can significantly impact inventory effectiveness, operational efficiency, and overall profitability.
Just-In-Time (JIT)
Just-In-Time is a management strategy aimed at reducing flow times within production systems as well as response times from suppliers and to customers. Under the JIT system, inventory arrives only as needed in the production process, minimizing stock carrying costs and reducing waste. Companies like Toyota have successfully implemented JIT principles, highlighting its effectiveness in automotive manufacturing.
The primary benefit of JIT lies in its ability to lower inventory costs and increase cash flow. However, a challenge is the reliance on suppliers. Any disruptions in the supply chain can severely affect production schedules. Therefore, careful consideration of supplier relationships and their reliability is critical when using this method.
ABC Analysis
ABC Analysis is an inventory categorization method that divides inventory into three categories based on importance. The categories are:
- A items: High-value items that require tight inventory control.
- B items: Moderate-value items that need frequent review.
- C items: Low-value items requiring less control.
Implementation of ABC Analysis enables businesses to focus efforts on managing the most critical items effectively. This categorization enhances inventory management, allowing for personalized approaches towards inventory control, thus conserving resources and focusing efforts where they matter most. Yet, a potential disadvantage is that this method may overlook trends in lower-value items, which could become significant in unexpected ways.
First-In, First-Out (FIFO)
First-In, First-Out is an inventory valuation method assuming that the oldest inventory items are sold first. This method is particularly important for perishable goods and products with limited shelf life. By adopting FIFO, businesses can minimize the chances of unsold inventory becoming obsolete. It ensures that inventory is rotated correctly, minimizing waste. FIFO's simplicity is its strongest point. It is easy to implement in most businesses, making it a widely favored method. However, market fluctuations can impact this methodology, particularly if prices are rising. It could lead to potential profit loss if older items are consistently undervalued.
Last-In, First-Out (LIFO)
Last-In, First-Out assumes that the latest inventory items purchased are the first to be sold. This method can be beneficial in times of rising prices as it allows businesses to deduct the higher cost of goods sold against revenues. As a result, this strategy can lead to tax advantages.
Nevertheless, LIFO is less common due to its potential pitfalls. It can distort profits and misrepresent inventory value, leading to financial statements that do not accurately reflect the current market value. This method may also complicate inventory management, as older items can remain in stock longer than optimal.
Inventory Management Techniques
Effective inventory management techniques play a critical role in ensuring that organizations maintain optimal stock levels while minimizing costs. These techniques assist businesses in streamlining their inventory processes, responding effectively to market demands, and improving overall operational efficiency. The strategic application of these techniques can lead to enhanced customer satisfaction, reduced waste, and improved profitability.
Given the complexities of modern supply chains and diverse customer expectations, understanding the various inventory management techniques available is essential for decision-makers and entrepreneurs alike.
Dropshipping
Dropshipping is a retail fulfillment method where the seller does not keep goods in stock. Instead, when a store sells a product, it purchases the item from a third party and ships it directly to the customer. This technique has gained popularity for several reasons:
- Low Startup Costs: Since inventory is not held, the required initial investment is significantly lower.
- Reduced Overhead: Dropshippers do not need to invest in warehousing or handling.
- Increased Flexibility: Businesses can quickly adapt to market changes without the burden of unsold inventory.
However, dropshipping does have its challenges. The retailer relies heavily on suppliers for inventory accuracy and shipping timeliness. Problems in either area can lead to customer dissatisfaction. Efficient communication and collaboration with suppliers are vital.
Consignment Inventory
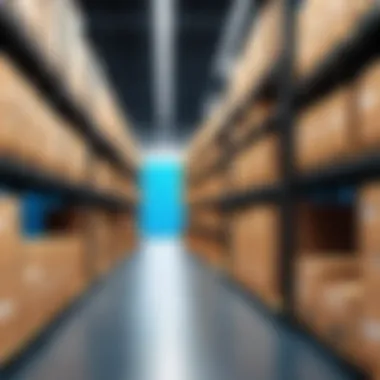
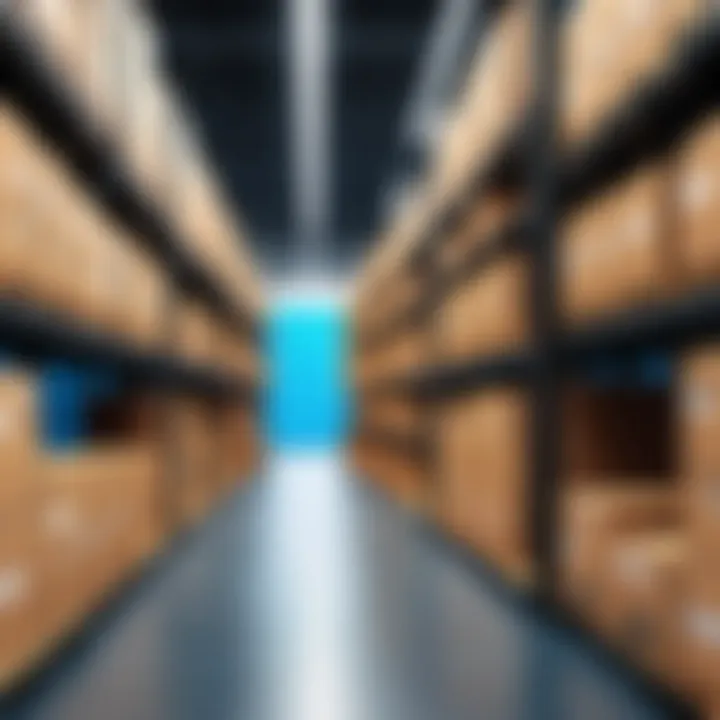
Consignment inventory involves a supplier placing its products in the retailer's location, but the retailer only pays for the stock sold. This approach offers several advantages:
- Lower Financial Risk: Retailers are only charged for inventory once it is sold, reducing upfront costs.
- Increased Selection: Retailers can offer a wider variety of products without the risk of overstock.
Yet, consignment inventory can also present difficulties. Retailers may face challenges managing stock levels and ensuring the proper turnover of goods. Regular communication with suppliers is necessary to assess stock performance and align inventory with demand.
Economic Order Quantity (EOQ)
The Economic Order Quantity is a formula utilized by businesses to determine the optimal order quantity that minimizes total inventory costs. This includes costs related to ordering, holding, and stockouts. The formula assists in striking a balance between ordering too frequently and incurring higher ordering costs, versus ordering too much and facing high holding costs.
Benefits of EOQ include:
- Cost Efficiency: By determining the ideal amount to order, businesses can avoid overstock and stockout scenarios.
- Improved Cash Flow: Better management of ordering reduces unnecessary capital tied up in inventory.
Though EOQ is effective, it does have limitations. It assumes consistent demand and lead time, which may not reflect real-world fluctuations. Factors such as seasonal demand changes or unexpected supply chain disruptions must be considered when applying EOQ.
By integrating effective inventory management techniques such as dropshipping, consignment inventory, and EOQ, businesses can enhance their inventory processes, leading to better financial outcomes and customer satisfaction.
Benefits of Effective Inventory Management
Effective inventory management is critical for businesses seeking to maintain competitiveness and profitability. Understanding its benefits equips decision-makers to implement strategies that not only streamline operations but also directly contribute to the bottom line. Organizations that optimize their inventory practices can expect significant improvements in various aspects of their operations. Below are three primary advantages of effective inventory management, which serve as vital components for any business model.
Cost Reduction
Effective inventory management can lead to substantial cost reductions. First, by accurately forecasting demand and monitoring stock levels, companies can avoid overstocking, which ties up capital and incurs additional storage costs. Less inventory means lower holding costs, such as insurance, depreciation, and obsolescence.
In addition, effective inventory control minimizes the risks associated with stockouts. When products are out of stock, businesses often face lost sales opportunities, unwarranted discounts, and customer dissatisfaction. Thus, maintaining optimal inventory levels directly affects profitability.
"Proper inventory management is not just about tracking products; it's about managing resources and ensuring maximum return on investment."
Customer Satisfaction
Customer satisfaction is paramount in today's competitive landscape. An efficient inventory management system ensures that the right products are available at the right time. Quick response to customer demands helps build trust and loyalty.
When businesses can meet customer expectations consistently, it enhances their reputation. Customers are more likely to return and even recommend the brand to others. Conversely, ineffective inventory management can lead to frustrated customers, which can harm a company's image. Maintaining a positive relationship with customers is essential for long-term growth.
Operational Efficiency
Operational efficiency is a direct outcome of effective inventory management. Streamlined operations lead to reduced waste and improved productivity. By utilizing methodologies such as Just-In-Time, companies can optimize their supply chain processes, thereby minimizing delays.
Efficient handling of inventory can also reduce the time employees spend on stock checks and order processing. Focusing on core activities rather than inventory issues creates a more productive work environment, allowing businesses to focus their resources where they are needed most.
In summary, the benefits of effective inventory management extend beyond mere organization; they encapsulate crucial cost reduction, heightened customer satisfaction, and operational efficiency. These elements are indispensable for decision-makers and professionals aiming to refine their inventory strategies and enhance overall business performance.
Challenges in Inventory Management
Inventory management is essential for any organization that relies on products and services. However, it comes with its unique challenges. Understanding these challenges enables decision-makers to devise effective strategies, increasing efficiency and minimizing risks. This section will explore critical elements surrounding these challenges, including the issues of overstock and stockouts, and the impact of supply chain disruptions.
Overstock and Stockouts
Overstock and stockouts are two sides of the same coin. Both situations can lead to significant financial losses and operational disruptions. Overstock occurs when a company holds more inventory than it can sell. This often results in increased holding costs, potential waste, and a decreased cash flow. Warehousing expenses, insurance, and obsolescence risks are just a few examples of costs associated with overstocking.
On the other hand, stockouts happen when inventory levels are insufficient to meet demand. This can lead to lost sales, dissatisfied customers, and damage to a company's reputation. Replacing stock quickly can result in higher procurement costs, especially if rushing to meet demand.
To manage these inventory issues effectively, organizations must implement robust forecasting techniques, which can enhance the accuracy of demand predictions. Tools like just-in-time (JIT) inventory systems can also help mitigate these risks. Balancing inventory levels is key; it requires continuous monitoring and adjustment based on sales trends and market conditions.
Supply Chain Disruptions
Supply chain disruptions are another critical challenge for inventory management. Events such as natural disasters, political instability, or issues with suppliers can create significant obstacles in maintaining adequate stock levels. Organizations may face delays in receiving goods or increased costs in sourcing alternatives. The recent global events have highlighted the fragility of supply chains, compelling many businesses to rethink their strategies.
Addressing supply chain disruptions involves diversifying suppliers, strategically locating warehouses, and adopting supply chain risk management practices. This approach not only reduces dependence on a single supplier but also fosters resilience by enabling quick responses to unexpected changes.
Ultimately, businesses need to be proactive and prepare for potential disruptions. Building strong relationships with suppliers and improving communication channels can also aid in managing inventory more effectively during uncertain times.
"Success in inventory management is determined not just by how much is in stock but by how well organizations anticipate their needs and manage complexities within the supply chain."
In summary, recognizing and addressing the challenges in inventory management is crucial for maintaining operational efficiency and customer satisfaction. By taking measured steps to optimize stock levels and preparing for market fluctuations, organizations can navigate the complexities of inventory management more effectively.
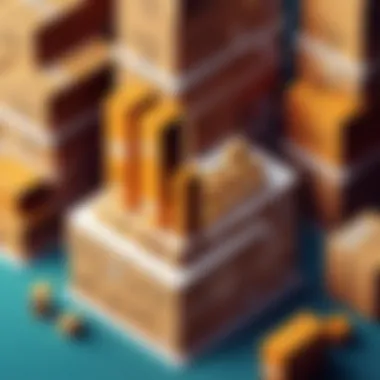
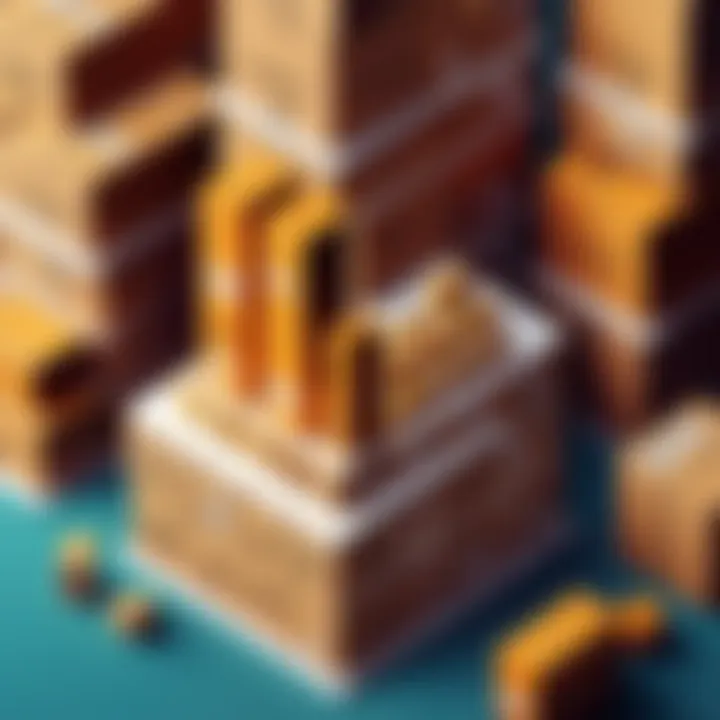
Technology in Inventory Management
In the fast-paced world of business, technology plays a crucial role in transforming inventory management practices. Companies seek to optimize their operations, reduce costs, and improve accuracy. The integration of various technological solutions can lead to more effective inventory control. Advanced tools not only streamline the processes but also provide data analytics that can enhance decision-making.
The significance of technology in inventory management cannot be overstated. With the rise of e-commerce and globalization, businesses face increasing competition. As such, efficient inventory management becomes necessary for survival and growth. Technology aids in tracking stock levels in real-time, forecasting demand, and automating repetitive tasks. This can ultimately result in increased efficiency and reduced waste.
Inventory Management Software
Inventory management software is an essential tool for businesses aiming to maintain accurate stock records. These systems allow companies to monitor inventory levels, sales, and orders effortlessly. One of the core benefits is the ability to centralize data, providing insights that manual tracking cannot offer.
Some of the notable features of inventory management software include:
- Real-time Tracking: Users can see updated stock levels at any moment, which facilitates better decision-making.
- Reporting and Analytics: Sophisticated reporting capabilities enable businesses to analyze trends and performance metrics.
- Integration with Other Systems: Many software solutions can connect with accounting, sales, and shipping software, streamline operations, and reduce errors.
Several prominent inventory management solutions exist, such as Fishbowl, TradeGecko, and SAP Business One. Each software has unique features and caters to different industries and business sizes. Therefore, selecting the right one depends on specific needs and budget constraints.
Automation Tools
Automation tools are another game-changer in inventory management. They help eliminate manual errors, improve efficiency, and save time. Automation can cover various aspects, from stock replenishment to sales order processing. Companies benefit by freeing up staff to focus on more strategic activities rather than routine tasks.
Key aspects of automation tools include:
- Automated Reordering: Businesses can set minimum stock levels, triggering automatic orders when stocks fall below those levels.
- Integration with Supply Chain Management: By connecting with suppliers, firms can streamline their procurement processes.
- Batch Tracking: Some tools allow businesses to track products in batches, ensuring compliance and traceability.
Using tools like Skubana or Zoho Inventory can significantly enhance operational workflows. These systems can help businesses manage their inventories more effectively, thus contributing to overall business success.
Effective technology adoption in inventory management boosts operational performance, enhances customer satisfaction, and drives profitability.
Future Trends in Inventory Management
As businesses continue to evolve in an increasingly competitive environment, the need for efficient inventory management strategies is more critical than ever. Understanding future trends in inventory management is essential for decision-makers, IT professionals, and entrepreneurs. These trends can enhance operational efficiency, improve customer satisfaction, and ultimately lead to greater profitability.
Integration of Technology
New technologies are redefining how companies manage their inventories. Businesses must consider how these innovations can optimize their processes. Key technologies driving this evolution include Artificial Intelligence (AI) and machine learning, along with sustainability practices. Their integration can offer insights into inventory levels and consumer behavior while minimizing waste.
The following point outline some benefits of monitoring these trends:
- Efficiency Improvement: Automation reduces labor costs and human error.
- Data-Driven Decisions: AI analyzes vast amounts of data, providing actionable insights.
- Sustainable Practices: Emphasis on eco-friendly methods resonates with consumers, enhancing brand reputation.
Understanding the trends in inventory management can significantly elevate a company’s operational and strategic capabilities.
Artificial Intelligence and Machine Learning
Artificial Intelligence and machine learning play a pivotal role in the future of inventory management. These technologies improve forecasting accuracy. Better forecasts ensure that stock levels align closely with demand.
AI algorithms process historical sales data and predict future demand patterns. This means organizations can adjust their stock levels proactively. Additionally, machine learning enhances inventory tracking. By analyzing trends, businesses can identify slow-moving products and eliminate excess stock efficiently. A more accurate understanding of inventory can lead to improved cash flow as well.
Considerations for Implementation
Implementing AI and machine learning involves some challenges. Organizations must invest in suitable technology and employee training. Furthermore, integrating these systems with existing inventory management software can be complex.
Sustainability Practices
Sustainability in inventory management is becoming a significant trend. Consumers are more conscious of environmental issues. Therefore, organizations that adopt sustainable practices can gain a competitive edge.
Sustainable inventory management involves minimizing waste, efficient resource use, and optimizing supply chains.
Incorporating sustainability offers various benefits:
- Brand Loyalty: Consumers prefer brands that are environmentally responsible.
- Cost Savings: Reducing waste lowers costs in the long run.
- Regulatory Compliance: Sustainability initiatives often help organizations comply with environmental laws.
Finale
In this article, we explored the intricate landscape of inventory management, unearthing its various types and methodologies. Effective inventory management is critical for organizations that aim to optimize stock levels and improve operational efficiency. It not only impacts profitability but also affects customer satisfaction and overall business performance.
Summary of Key Points
- Diverse Types of Inventory Systems: We analyzed perpetual and periodic inventory systems, highlighting their respective benefits and drawbacks. The choice between these systems can significantly influence how a company tracks its stock and responds to changes in demand.
- Management Methodologies: Different methodologies, such as Just-In-Time, ABC Analysis, FIFO, and LIFO, serve particular business needs. Understanding these methodologies helps organizations choose the right strategy that aligns with their operational goals.
- Techniques in Practice: Techniques like dropshipping and consignment inventories provide innovative solutions for managing stock while minimizing overhead. These practices assist businesses in responding to supply chain dynamics while keeping costs down.
- Technology's Role: The integration of inventory management software and automation tools marks a significant advancement in the field. These technologies enable real-time tracking and analytics, which can enhance decision-making.
- Emerging Trends: Finally, trends such as artificial intelligence and sustainability are reshaping how inventory management is approached. Companies increasingly leverage AI to predict inventory needs and ensure eco-friendly practices are in place.
Final Thoughts
As we conclude our exploration of inventory management, it is clear that the right choice of system, methodology, and technology is paramount. Organizations must continually assess their inventory practices to align with changing market conditions and consumer expectations. Decision-makers should embrace these insights to refine their strategies. The future of inventory management lies in adaptability and efficiency, driving businesses toward sustainable growth.
"Inventory management is not just about tracking stock; it is about making informed decisions that underpin business success."
In summary, a thorough understanding of inventory management types equips decision-makers with the knowledge to implement strategies that not only meet but exceed market demands.