Preventive Maintenance Strategies in Manufacturing
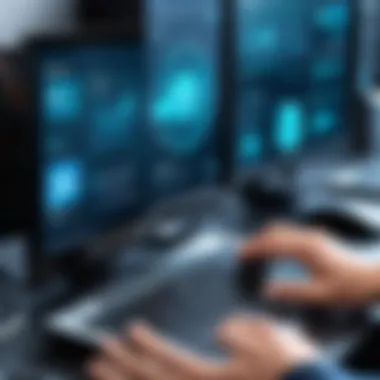
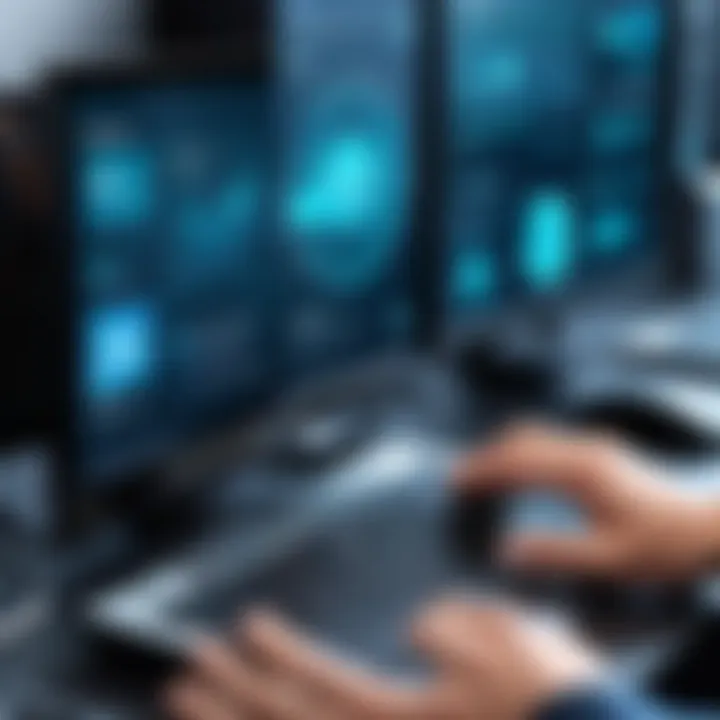
Intro
In the ever-evolving world of manufacturing, where competition is fierce and margins are often slim, understanding preventive maintenance becomes not just beneficial but essential. The manufacturing sector, with its complex systems and machinery, faces unique challenges. Unscheduled downtimes can lead to significant lost revenue, frustrated employees, and production delays. Therefore, preventive maintenance emerges as a strategic cornerstone. It’s about being proactive, ensuring that machinery is not only operational but optimized.
Preventive maintenance emphasizes regular checks and timely interventions, countering wear and tear before it leads to failures. The significance here lies not just in the maintenance itself, but also in cultivating a culture that prioritizes efficiency and reliability. Without a solid maintenance strategy, manufacturers risk falling behind, both technologically and economically.
As we delve deeper into the crux of preventive maintenance, this exploration will cover essential strategies, innovative methods, and the technology that can elevate a manufacturing facility's operational capacity. We will not only touch on theoretical aspects but also examine real-world case studies that illustrate success driven by meticulous maintenance practices.
From understanding key software features that empower maintenance teams, to analyzing cost metrics and performance benchmarks, each section will contribute to a robust framework aimed not merely at understanding but mastering the art of preventive maintenance. This guide is tailored for decision-makers, IT professionals, and entrepreneurs who look beyond the basics to enhance their maintenance strategies.
"Preventive maintenance is the key to avoiding the trap of costlier repairs and downtime, ensuring a smooth manufacturing process."
Thus, embarking on this journey, ready your minds for insights that promise to sharpen the competitive edge in a highly dynamic manufacturing landscape.
Understanding Preventive Maintenance
Preventive maintenance holds a fundamental role in ensuring the efficient operation of manufacturing processes. It refers to the practice of routine maintenance and systematic inspections, aiming to keep machinery and equipment in good working order. By addressing potential issues before they escalate into significant problems, organizations can minimize unexpected breakdowns, leading to smoother production lines and increased operational efficiency.
Definition and Key Concepts
At its core, preventive maintenance encompasses various strategies designed to perform maintenance tasks before equipment failure occurs. This approach is not solely about repairing machinery after faults arise; rather, it focuses on implementing measures that can predict and prevent potential failures.
Key components of preventive maintenance include:
- Scheduled inspections: Regular evaluations of equipment to identify wear and tear.
- Lubrication: Ensuring all moving parts are adequately lubricated to prevent friction and overheating.
- Parts replacement: Changing out parts that have a predetermined lifespan before they fail.
- Performance monitoring: Using tools and software to track the operation of machinery, identifying any abnormalities.
The benefits of such an approach are numerous. Not only does it prolong the lifespan of equipment, but it also enhances workplace safety by reducing the risks associated with equipment malfunctions. It’s the same as checking your car before a long trip - a little precaution can save a lot of trouble.
Historical Context in Manufacturing
The concept of preventive maintenance isn’t novel but has evolved significantly over the decades. In earlier manufacturing settings, maintenance was often reactive, with operators fixing equipment only after it failed. This led to significant downtime and costly repairs, not to mention the impact on production schedules.
As production demands increased in the mid-20th century, industries began exploring strategies that could minimize disruptions. The introduction of Total Quality Management (TQM) in the 1980s also played a pivotal role in prioritizing preventive routines. With a greater emphasis on maintaining quality standards, industries clearly saw the link between preventive maintenance and production efficiency.
Today, preventive maintenance is considered a best practice across many manufacturing sectors. Organizations are increasingly investing in training, technology, and structured programs to ensure their maintenance practices are proactive rather than reactive.
"An ounce of prevention is worth a pound of cure." This old adage rings especially true when it comes to manufacturing, emphasizing the value of preventive measures.
Understanding the evolution of preventive maintenance allows manufacturers to appreciate its critical role within modern operations. This strategic shift from being merely reactive to proactive has not only influenced maintenance philosophies but has become vital for staying competitive in a fast-paced market.
The Rationale Behind Preventive Maintenance
Preventive maintenance stands at the fore of operational strategies in manufacturing, showcasing not only its necessity but also its multifaceted benefits. Understanding the rationale behind this proactive approach reveals significant advantages that go beyond merely fixing issues as they arise. In an industry where time is of the essence, the importance of sticking to a preventive maintenance schedule cannot be overstated.
Cost-Efficiency Considerations
When manufacturers ponder the allocation of their budgets, preventive maintenance often proves to be the smarter investment in the long run. By prioritizing regular servicing and addressing potential problems before they escalate, organizations can avoid the punishing costs associated with unexpected breakdowns.
- Reduced Downtime: One of the most glaring advantages stems from minimized equipment stoppage. The loss accruing during unplanned downtime can skyrocket, affecting production schedules and, consequently, revenue streams. Thus, developing a preventive maintenance schedule often translates to increased operational time.
- Financial Benefits: A well-implemented preventive maintenance strategy often brings along notable financial benefits. Consider the savings associated with minor repairs compared to the hefty expenses tied to major overhauls.
- Efficiency Gains: Preventive practices lead to streamlined operations, as machinery operates more effectively. Improved equipment performance can mean producing more in less time, which is always a win for the bottom line.
In short, these cost-efficiency considerations make clear that investing in preventive maintenance should be a cornerstone of any modern manufacturing strategy.
Enhancing Equipment Lifespan
An often-overlooked perk of preventive maintenance is how it can extend the lifespan of machinery and equipment. When machines are cared for rigorously, they last longer, and this longevity translates to further cost savings.
- Regular Check-ups: Just like regular medical check-ups are essential for human health, periodic inspections and assessments are vital for machinery. By identifying wear and tear early, businesses can act swiftly to repair or replace components, delaying the inevitable need for total equipment replacement.
- Focus on Performance: When machines are well-maintained, not only do they last longer, but they also perform better. This means products are not only made faster but often in greater quality.
- Stability in Production: A reliable set of machinery facilitates a consistent production environment. When equipment fails less frequently, employees waste less time troubleshooting issues, focusing instead on quality and speed, which enhances overall productivity.
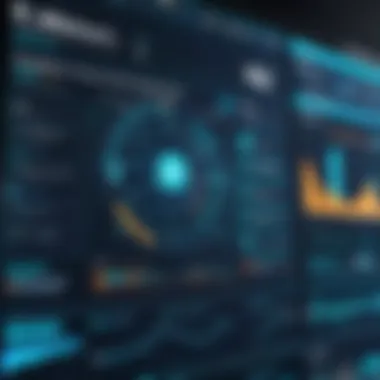
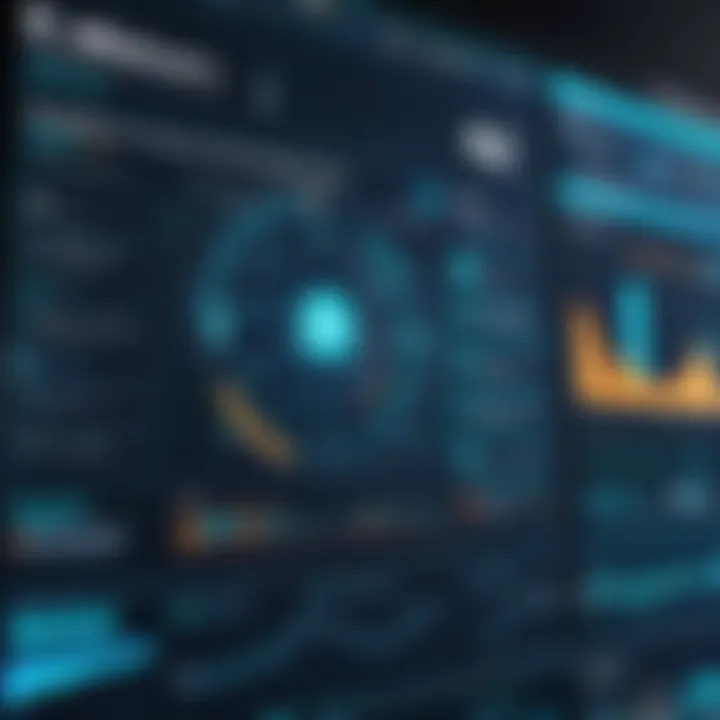
In essence, focusing on the upkeep of equipment through preventive maintenance provides a sturdy foundation that leads to impressive results in both the short and long term.
Key Strategies in Preventive Maintenance
Implementing effective preventive maintenance (PM) strategies is fundamental to ensuring the longevity and reliability of machinery in the manufacturing sector. Companies that adopt these strategies not only experience enhanced operational efficiency but also incur less cost in the long run. Typically, a structured approach that incorporates several elements—such as scheduled inspections, predictive analytics, and employee training—provides a sturdy framework for success. These key strategies serve to minimize downtime, optimize resource utilization, and foster a culture of continuous improvement within an organization.
Scheduled Inspections
One of the cornerstones of preventive maintenance is the practice of scheduled inspections. This involves routinely checking equipment and machinery at predetermined intervals. The process typically includes a visual examination of components, checking for wear-and-tear, lubrication levels, and ensuring that systems operate within their intended parameters. While this might seem basic, consistent inspections can catch issues before they escalate, saving not only money but also time.
Implementing a structured inspection schedule can mitigate unexpected breakdowns and ensure smoother operations. Manufacturers often utilize software systems that can automate scheduling, allowing operators to focus on performing maintenance tasks rather than managing them.
Moreover, inspections can serve multiple roles:
- Documenting Equipment History: Keeping records of each inspection provides valuable insights into machinery performance over time.
- Identifying Trends: Patterns can emerge from inspection data, leading to insights about potential failures days, months, or even years ahead of time.
- Ensuring Compliance: Many industries have regulatory requirements on equipment safety. Scheduled inspections help ensure compliance with these regulations, avoiding costly fines.
The simple act of setting up a rigorous inspection routine can shift the tide in favor of operational reliability.
Predictive Analytics Integration
The integration of predictive analytics into preventive maintenance represents a leap into the future of manufacturing health management. It combines real-time data collection with advanced algorithms to predict when equipment failures might occur. By harnessing sensor data via IoT devices, manufacturers can obtain a treasure trove of information on equipment performance.
Rather than relying solely on fixed schedules, predictive maintenance leverages machine learning to analyze patterns and detect anomalies. This enables:
- Proactive Repairs: Rather than waiting for a machine to fail, technicians can address issues before they happen, minimizing downtime.
- Optimized Resource Allocation: Maintenance resources can be allocated more effectively, focusing on machines that require immediate attention, as opposed to all machines equally, which wastes time and material.
Predictive analytics can greatly enhance maintenance decision-making processes. However, it does require an initial investment in technology and training. The benefits, though, often far outweigh the costs, leading to reduced operational disruptions and enhanced productivity over time.
Employee Training and Engagement
Last but not least, employee training and engagement are critical components of an effective preventive maintenance strategy. A well-informed workforce is essential for the successful implementation of any maintenance program. Staff should understand not just how to perform maintenance tasks but also why these tasks matter.
Investing in continuous training can empower employees to make informed decisions regarding equipment use and care. Engaged employees are more likely to spot issues early, adhere to maintenance schedules, and provide valuable feedback on process improvements.
Furthermore, fostering a culture where maintenance is prioritized encourages:
- Shared Responsibility: Everyone in a manufacturing environment from operators to maintenance personnel becomes an integral part of the PM process.
- Improved Morale: When employees feel their contributions matter, job satisfaction increases, which can lead to lower turnover rates.
Challenges in Implementing Preventive Maintenance
Implementing preventive maintenance presents a series of challenges that can hinder even the most well-intentioned initiatives. Understanding these challenges is vital for any organization looking to improve its maintenance strategies. When a company adopts preventive maintenance practices, it sets itself on a path toward increased efficiency and reduced downtime. However, it must navigate the rocky terrain of resource allocation and the cultural resistance that often accompanies change. By addressing these challenges head-on, organizations can smoothen the transition and reap the benefits of effective preventive maintenance.
Resource Allocation Issues
Resource allocation is frequently a make-or-break aspect when it comes to preventive maintenance programs. To deploy an effective program, companies need to invest in various resources: technology, personnel, training, and time. However, capturing and maintaining these resources often presents a significant challenge.
From the outset, companies might underestimate the budget required to initiate a preventive maintenance program. Equipment maintenance isn’t just a cost; it’s an investment that requires a financially sound commitment. Allocating funds too thinly can backfire, leading to poorly executed maintenance tasks and higher long-term costs.
Moreover, getting the right people involved—those who have both the technical expertise and the inclination to prioritize maintenance—can prove tricky. If an organization fears a shortage of skilled workers, it may hesitate to invest in staff training, resulting in a workforce ill-prepared to manage preventative tasks effectively. In light of these challenges, organizations must engage in meticulous planning and open discussions about priorities and resource needs.
Cultural Resistance to Change
Cultural resistance to change is another formidable obstacle that organizations encounter when integrating preventive maintenance practices. Humans are creatures of habit, and shifting mindsets within a workplace often requires persistent effort and strategic initiatives.
Employees may be skeptical about adjustments in routines or the new systems being put in place. They might question the necessity of preventive maintenance compared to seemingly more urgent day-to-day tasks. Unless employees see clear value in these changes, they might continue to default to old habits, thus stifling any potential improvements in efficiency.
"The hardest thing about changing a culture is convincing your people that change is necessary and beneficial."
For organizations to overcome this resistance, communication is key. Management needs to effectively articulate the benefits of preventive maintenance—such as reduced downtime and prolonged equipment lifespan. It becomes crucial to engage employees in discussions about the expectations and realities of new practices. Furthermore, including them in the transition process can ease anxieties and foster a sense of ownership over the changes.
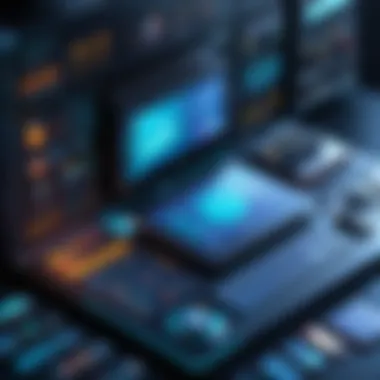
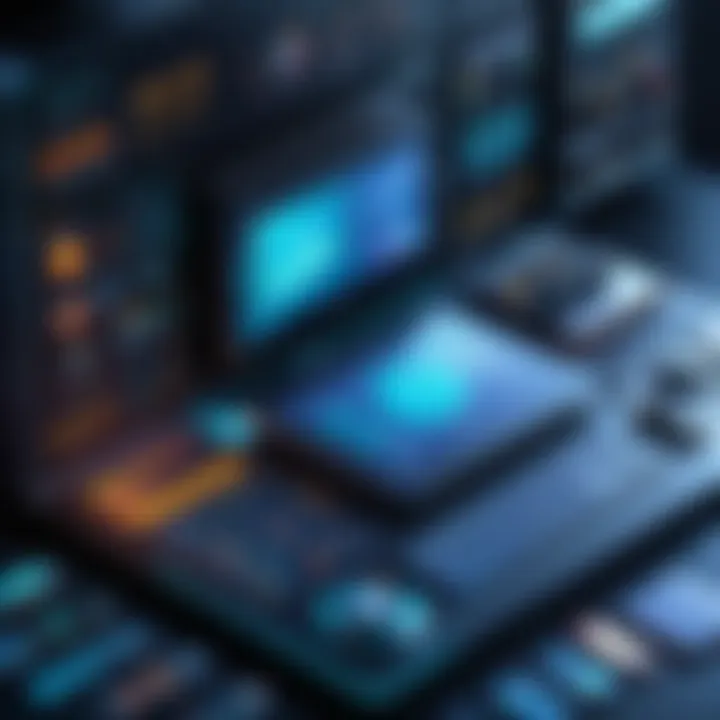
In summary, for preventive maintenance to be successfully implemented, organizations must pay thoughtful attention to resource allocation and cultural dynamics. Addressing financial and personnel challenges while actively managing and fostering an accepting culture can pave the way for a more streamlined and effective maintenance program.
Technological Advances in Maintenance Strategies
As we navigate through the ever-changing landscape of manufacturing, the impact of technological advances in maintenance strategies cannot be overstated. In a world where efficiency is king, embracing new technologies is no longer optional—it's essential. Companies looking to stay ahead must integrate modern tools and methodologies to bolster their maintenance routines. With the advent of technologies like the Internet of Things (IoT) and automation, manufacturers have new ways to optimize operational processes, reduce downtime, and enhance productivity.
IoT and Smart Manufacturing
The Internet of Things, or IoT, represents a paradigm shift in how manufacturers approach preventive maintenance. By connecting machines and equipment via sensors, companies can gather real-time data about their performance and wear. This is not just some fancy tech gimmick; it's a means to anticipate challenges before they become apparent.
Consider a typical production line with diverse machinery. Every piece of equipment, from conveyor belts to robotic arms, can now relay crucial information about its operational health. For instance, sensors might indicate excessive vibration in a motor, which could lead to imbalance or failure if left unaddressed. By dealing with problems as they arise, factories can schedule maintenance more strategically. That leads to a significant reduction in unscheduled downtime, allowing for smoother operations.
Moreover, IoT facilitates the collection of vast amounts of data, which can be analyzed to predict when equipment is likely to fail. This predictive maintenance approach can save both time and money. Organizations no longer operate with a ‘repair it when it breaks’ mentality. Instead, they adopt a proactive stance on managing equipment, fostering a more predictable production environment.
"Using IoT in maintenance isn't just about fixing things; it's about understanding and anticipating."
Automation in Maintenance Processes
Shifting gears to automation, this technology plays a crucial role in redefining maintenance approaches. Automated systems for routine tasks not only streamline processes but also free up resources for more strategic initiatives. For example, routine cleaning, parts replacement, or system checks can be automated, allowing maintenance teams to focus on complex challenges that require human intervention.
The integration of automated systems can also enhance safety in the workplace. Dangerous tasks that would typically require human hands can now be performed by robots or automated machines, thus reducing the risk of accidents or injuries. This advancement also has implications for worker morale. When people are relieved of monotonous, hazardous work, they can invest more energy into creative and innovative tasks.
In addition, automation leads to quicker response times. With systems that can alert workers of potential issues, less time is wasted, and production flow remains unobstructed. A classic example is the use of scheduling software that can manage maintenance tasks based on machine availability and operational demands. This not only streamlines the process but mitigates the risk of significant disruptions.
In summary, the infusion of IoT and automation into maintenance strategies represents a game changer in manufacturing. As industries continue to evolve, the thoughtful implementation of these technologies not only ensures efficiency but also aligns with a broader trend toward smarter, safer, and more sustainable production practices.
Case Studies in Successful Implementation
The exploration of case studies in the realm of preventive maintenance serves as a beacon, illuminating both the challenges and triumphs that various manufacturing firms face. These studies not only shed light on effective strategies but also provide a roadmap for others aiming to optimize their maintenance practices. By learning from real-world applications, manufacturers can understand the significance of adapting proven methods tailored to their specific environments. Emphasizing specific elements, the benefits of these case studies are manifold:
- Learn from Mistakes: A thorough analysis of past errors can guide future decisions.
- Benchmarking Success: Companies can measure their performance against industry leaders, setting realistic goals.
- Practical Insights: Theories turning into practice offer tangible solutions that can be directly applied.
Ultimately, the lessons gleaned from these implementations thread together a narrative of progress, inspiring manufacturers to embrace preventive maintenance as a pillar of operational excellence.
Manufacturing A: A Focus on Efficiency
In the case of Manufacturing A, the firm faced persistent equipment failures that cost them dearly—not only in financial terms but also in morale. This company's scenario was like a broken watch: it occasionally worked, but more often than not, it was simply a source of frustration and downtime. Recognizing the need for a game plan, they embarked on a journey towards a more efficient maintenance strategy.
The first step was to analyze their existing maintenance schedules. They found that most actions were reactive, often responding to machinery breakdowns rather than preventing them. After conducting a thorough review, a rigorous scheduled inspection process was implemented. Here’s what they did:
- Evaluated Equipment Needs: Each machine was assessed for its specific maintenance requirements, paving the way for targeted attention.
- Developed a Maintenance Calendar: This allowed for regular checks, ensuring potential issues were identified before they escalated.
- Empowered Employees: Training sessions were conducted, allowing staff to recognize signs of wear and tear.
The results were notable. Manufacturing A saw a decrease in unplanned downtimes by nearly 30% within the first quarter, a statistic that galvanized the entire team. This shift towards efficient practices not only saved costs but also rekindled employee engagement, proving that forethought and planning could lead to a more harmonious workplace.
Manufacturing B: Leveraging Technology
Contrasting with Manufacturing A’s focus on systematic scheduling, Manufacturing B opted to leverage technology as the cornerstone of their maintenance strategy. They recognized that the shift towards a more digital landscape opened numerous doors. Their implementation of predictive analytics became a transformative force in their operations.
Here’s a glimpse into their strategic approach:
- Sensor Integration: Machines were equipped with sensors that continuously monitored operational parameters such as temperature, vibration, and noise levels.
- Data Analytics Platforms: The collected data fed into advanced analytics software, allowing for real-time assessment of machine health.
- Proactive Maintenance Triggered by Data: Instead of waiting for scheduled maintenance, alerts were generated before a potential failure occurred.
This transition reduced their operational disruptions significantly. Manufacturing B reported a whopping 40% increase in productive time, with their technology-driven approach enabling maintenance interventions at the most opportune moments. Their embrace of modernity stands as a testament to how the right tools can reshape an entire maintenance paradigm, marrying innovation with practicality.
"Success leaves clues. Don't be afraid to learn from others."
By integrating these approaches, both traditional and technological, firms can find their own way to achieve a robust preventive maintenance strategy, essential in today’s relentlessly competitive landscape.
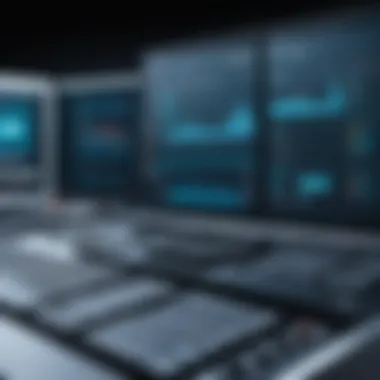
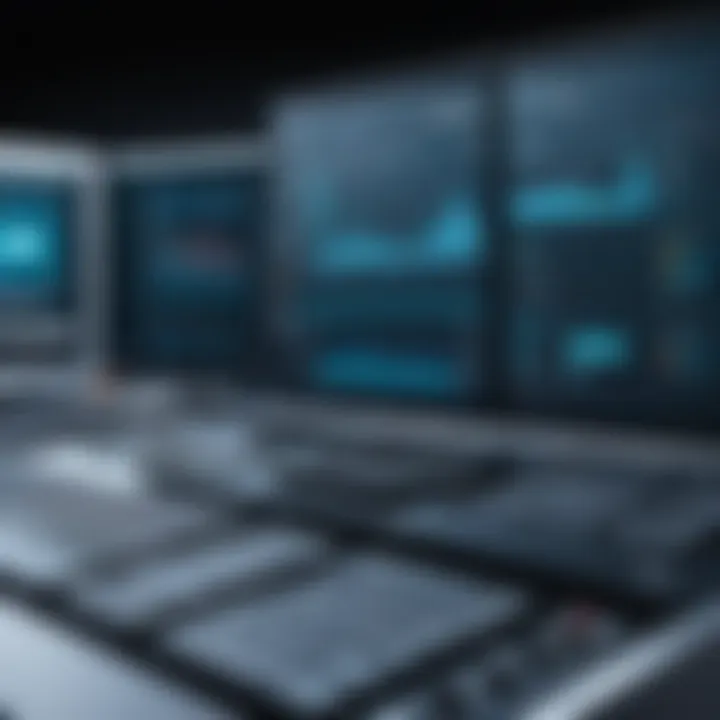
Measuring the Success of Preventive Maintenance
Evaluating the effectiveness of preventive maintenance is crucial for any manufacturing entity that wants to thrive. It isn’t just about putting out fires or reacting to problems when they occur; it involves having a keen eye on the metrics that indicate how well the maintenance strategy is functioning. Gauging success helps organizations identify areas of improvement, allocate resources more effectively, and ultimately enhance overall productivity.
Key Performance Indicators
When it comes to measuring success, the choice of Key Performance Indicators (KPIs) plays a significant role. The right KPIs can offer invaluable insights into how preventive maintenance strategies perform. Here are some key indicators to consider:
- Maintenance Costs: Regularly tracking how much is spent on maintenance helps in understanding whether the costs are increasing or decreasing. It provides an idea of whether the approach is cost-effective.
- Downtime: Monitoring machine downtime is essential. Less downtime indicates an effective maintenance schedule. Comparing the current downtime with historical data gives organizations a sense of where they stand.
- Failure Rates: Keeping tabs on equipment failures before scheduled maintenance can signal whether preventitive measures are doing their job. A decreasing trend implies better maintenance practices.
- Mean Time Between Failures (MTBF): This is a critical indicator in manufacturing. A higher MTBF signifies that machinery operates without interruption for longer periods, which is a positive sign.
- Overall Equipment Effectiveness (OEE): This composite metric includes availability, performance, and quality. It’s a holistic approach to assess how well manufacturing is running in relation to its total productive capacity.
"What gets measured gets managed." - This adage rings especially true in the realm of preventive maintenance.
These indicators help decision-makers like plant managers or IT professionals assess the overall health of their maintenance strategy and make data-driven decisions.
Return on Investment Analysis
Conducting a Return on Investment (ROI) analysis for preventive maintenance is essential to understand its financial impact. Sometimes, showcasing maintenance as a cost center leads to hesitance in investing in preventive initiatives. However, a thorough ROI analysis can change that narrative. Here’s how to approach it:
- Identify Costs: Calculate all costs associated with preventive maintenance. This includes labor, materials, and any overhead.
- Estimate Savings: Consider the savings brought about by reducing equipment failures or downtime. Include any tangible gains from increased efficiency or output.
- Calculate ROI: Use the formula:A positive ROI number indicates that the preventive measures are paying off, while a negative figure suggests that reevaluation might be necessary.
- Consider Intangible Benefits: Some benefits, like enhanced employee morale and safety, might not directly translate into numbers. Still, they significantly contribute to the overall success and sustainability of all operations.
In summary, through diligent monitoring of KPIs and careful analysis of ROI, manufacturers can effectively measure the success of their preventive maintenance strategies. This analytical approach empowers organizations to adapt and optimize maintenance practices, steering them toward a more productive and sustainable future.
Future Trends in Preventive Maintenance
As the manufacturing landscape evolves, future trends in preventive maintenance become crucial for the continued success of operations. These advancements not only improve efficiency but also help companies adapt to changing environments. Prioritizing proactive maintenance strategies will yield substantial benefits, ranging from optimized processes to enhanced sustainability efforts. While the fundamentals of preventive maintenance continue to be relevant, integrating innovative approaches can unlock new pathways in operational excellence.
Moving Towards Predictive Maintenance
Stepping beyond traditional preventive strategies, the shift towards predictive maintenance is becoming increasingly significant. By using data analytics and real-time monitoring tools, manufacturers can anticipate equipment failures before they happen. This approach can be viewed as a safety net, offering insights based on equipment health and performance metrics.
Benefits of Predictive Maintenance
- Cost Savings: By addressing issues before they escalate, companies can avoid expensive repairs and replacements.
- Reduced Downtime: Predictive maintenance allows for scheduling repairs at convenient times, ensuring minimal disruption to production.
- Enhanced Decision-Making: Data-driven insights empower managers to make informed choices about equipment upgrades and replacements.
Moving forward, companies should consider investing in technologies such as the Internet of Things (IoT). For instance, devices can be equipped with sensors that provide valuable data about operational performance. This is especially beneficial in sectors where machinery plays a vital role, ensuring that maintenance is strictly aligned with actual conditions rather than arbitrary timelines.
Sustainable Practices in Maintenance
Another important trend is the integration of sustainable practices in maintenance strategies. As environmental regulations tighten and societal demands shift toward greener solutions, manufacturers must embrace practices that minimize waste and reduce energy consumption. This not only benefits the planet but can also enhance a company's reputation and align with consumer preferences.
Key Aspects of Sustainable Maintenance
- Energy Efficiency: Identifying and implementing energy-saving measures can lead to significant reductions in operational costs.
- Waste Reduction: Streamlining maintenance processes to minimize waste can contribute to operational efficiency.
- Lifecycle Assessment: Evaluating the environmental impact of machinery across its lifecycle helps in understanding the balance between resource use and efficiency.
By combining sustainability with preventive maintenance, manufacturers position themselves as forward-thinking organizations committed to both operational excellence and corporate responsibility. Efforts in sustainable practices not only mitigate environmental impact but also often result in improved profitability through better resource management.
"Integrating predictive and sustainable practices into preventive maintenance is not just a trend; it’s a new standard of operation that prioritizes efficiency and responsibility."
The End: The Road Ahead for Manufacturing Maintenance
As we navigate the ever-evolving landscape of the manufacturing sector, the significance of preventive maintenance takes center stage. This concluding section serves not just as a closure to our detailed exploration but as a beacon guiding manufacturers toward a future marked by resilience, efficiency, and sustainability.
"Preventive maintenance isn't just a method; it's a mindset that fosters a culture of continuous improvement."
Recap of Key Insights
Throughout this discourse, we've highlighted the essence of preventive maintenance, emphasizing its necessity for reducing downtime and enhancing productivity. Some key insights include:
- Definition and importance: Understanding that preventive maintenance goes beyond mere repairs to encompass a holistic strategy that includes timely inspections and proactive replacements.
- Historical context: Noting how preventive maintenance has evolved from traditional methods to its current automated, data-driven approaches.
- Strategic frameworks: Recognizing the power of scheduled inspections, predictive analysis tools, and thorough employee training in fostering a robust maintenance culture.
- Technological integration: Understanding how IoT and automation have changed the dynamics of maintenance, allowing for real-time monitoring and quicker responses.
- Measuring success: Learning to assess the impact of preventive maintenance through Key Performance Indicators (KPIs) and Return on Investment analysis.
Strategic Directions for Future Success
The road ahead is paved with opportunities for innovation and efficiency. Here’s how manufacturers can situate themselves for future success in preventive maintenance:
- Leverage Data Analytics: Data is the new gold. Manufacturers should invest in predictive maintenance technologies that harness big data for making informed decisions. By analyzing equipment wear and tear trends, businesses can anticipate failures before they occur, leading to substantial cost savings.
- Embrace a Continuous Improvement Philosophy: Organizations should cultivate a culture that encourages ongoing feedback and improvements in maintenance processes.
- Invest in Training Programs: Continuous training of staff is essential. Ensure employees are well-versed in handling advanced machinery and that they appreciate the value of preventive maintenance in their daily operations.
- Promote Collaboration Between Departments: Break down silos within your organization. Maintenance teams should work closely with production and design teams to align objectives and optimize machinery usage from the inception phase.
- Focus on Sustainability: As the world shifts towards greener practices, manufacturers have to consider eco-friendly technologies. Sustainable maintenance practices not only help in meeting regulatory demands but also appeal to modern consumers.