Dynamics of Leading Manufacturing Companies Explained
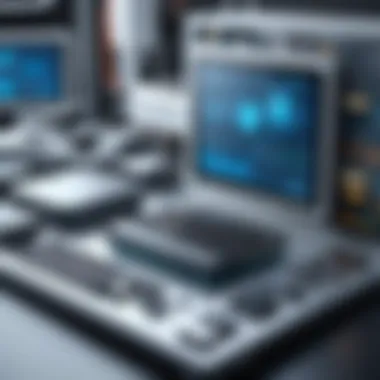
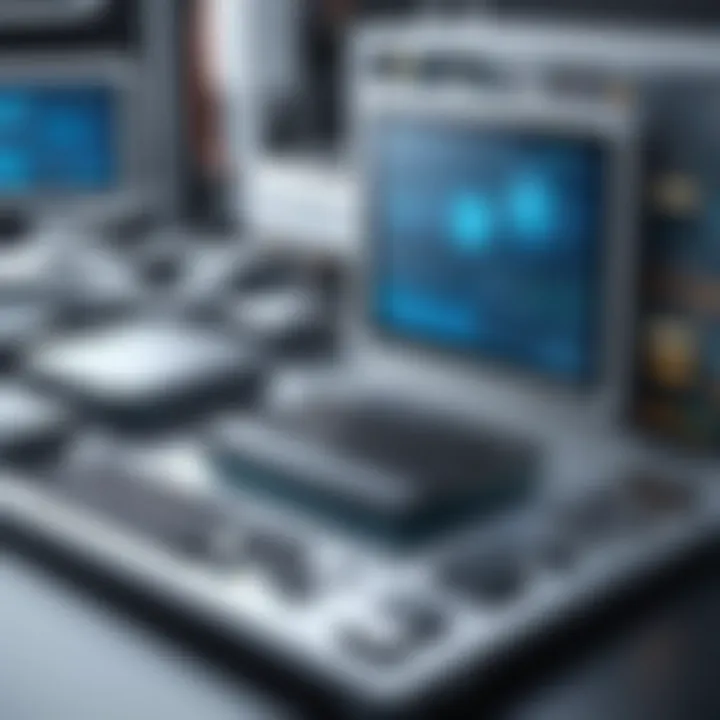
Intro
In today's competitive landscape, the operation of a leading manufacturing company involves a complex interplay of various elements. Understanding these dynamics is essential for decision-makers wanting to succeed. The next sections will focus on specific aspects that define these companies, including their key software features, comparison metrics, and more.
Navigating these complexities can provide insights into how these companies maintain their edge in the global market. This is crucial for industry professionals and entrepreneurs aiming to enhance their strategic approach.
Key Software Features
To maintain efficiency and competitiveness, manufacturing companies often rely on robust software systems. These systems can significantly enhance operations, helping to streamline processes and improve output.
Essential functionalities
- Inventory Management: This function helps track stock levels, manage orders, and avoid excess. Accurate inventory data is vital for just-in-time manufacturing processes.
- Production Planning: Advanced tools assist in scheduling production runs, ensuring optimal use of resources. This minimizes downtime and maximizes throughput.
- Quality Control: Quality management tools monitor production standards. Software solutions often integrate statistical process control to maintain product quality.
- Supply Chain Coordination: Effective coordination with suppliers and distributors enhances the overall performance of manufacturing operations. This feature helps establish a responsive and resilient supply chain.
Advanced capabilities
As manufacturing evolves, companies must adapt to new technological advancements. Here are some sophisticated capabilities that modern manufacturing software offers:
- Data Analytics: Utilizing big data, manufacturers can derive useful insights from production metrics, leading to informed decision-making.
- Automation Integration: With IoT devices and robotics, companies automate repetitive tasks, significantly increasing productivity.
- Real-time Monitoring: Many software systems now provide live updates on production processes, allowing for swift identification of issues and adjustments.
"Embracing modern software solutions can be a game changer for manufacturers seeking to optimize their operations and achieve sustainable growth."
Comparison Metrics
In evaluating the effectiveness of a manufacturing company, specific metrics are useful. These metrics allow stakeholders to assess how well a company is performing compared to competitors.
Cost analysis
A thorough cost analysis incorporates direct costs like materials and labor, as well as indirect costs like overhead and maintenance. Understanding this gives companies a clearer picture of their profitability:
- Fixed Costs: These remain constant regardless of production level, such as rent and salaries.
- Variable Costs: These fluctuate with production volume, including raw materials and utilities.
Performance benchmarks
Establishing performance benchmarks helps in comparing effectiveness across various sectors. Key benchmarks include:
- Overall Equipment Effectiveness (OEE): A composite metric that indicates how well a manufacturing operation is utilized compared to its full potential.
- First-Pass Yield (FPY): Indicates the percentage of products manufactured correctly without rework, which is essential for measuring efficiency.
These metrics play a vital role in shaping strategic decisions. They not only measure past performance but also guide future efforts to enhance operations.
Foundations of Manufacturing Excellence
In the realm of manufacturing, laying a solid foundation is crucial for achieving long-term success. Foundations of Manufacturing Excellence encompasses key principles and strategies that guide organizations toward operational efficiency and competitive advantage. It serves as a roadmap, illuminating essential criteria that leading companies prioritize to meet industry standards and customer expectations.
A strong emphasis on foundational elements enhances product quality, streamlines processes, and cultivates a culture of continuous improvement. Implementation of methodologies such as Lean Manufacturing and Six Sigma often illustrates this focus. These practices not only minimize waste but also improve overall productivity. Adopting these principles leads to better resource allocation and enhanced capability to respond to market changes.
Furthermore, the concept of manufacturing excellence extends to fostering innovation as a core value. Leading companies recognize that stagnant practices can hinder growth. Thus, they invest in research and development, encouraging ingenuity among employees. This investment translates into not just improved products but also streamlined processes that catalyze future advancements. Elements such as employee engagement, technology integration, and strategic supply chain management coalesce into a comprehensive framework that propels a firm into a leadership position within the competitive landscape.
Adopted principles of excellence aren't merely guidelines but rather are ingrained into corporate culture, resulting in sustainable practices that align with global standards. Consequently, understanding the foundations of manufacturing excellence equips industry professionals and decision-makers with the insights needed to implement effective strategies.
Defining Manufacturing Leadership
Manufacturing leadership is defined through the lens of effective management practices and industry influence. It involves guiding organizations in pursuit of innovation, operational efficiency, and employee satisfaction. Well-defined leadership secures the trust of stakeholders and contributes significantly to the overall performance of the manufacturing firm. Leadership extends beyond mere authority; it emphasizes creating a vision that inspires the workforce while making informed decisions based on data and market dynamics.
On a practical level, strong manufacturing leaders demonstrate adaptability, enabling their organizations to weather disruptions. They actively nurture relationships within their ecosystems, including suppliers and customers, thus creating a harmonious workflow that enhances productivity.
Historical Context of Manufacturing
The historical context of manufacturing provides a backdrop for current practices and trends. Manufacturing has evolved dramatically over decades, transitioning from artisanal practices to the industrial revolution's mechanized processes. Understanding this evolution is essential for recognizing how foundational principles emerged. Historical insights reveal the shifts in consumer demands and technological advancements that have shaped contemporary manufacturing.
Developments such as the assembly line, introduced by Henry Ford, revolutionized production efficiency and underscored the importance of standardized processes. Such historical milestones illustrate how manufacturing principles have been structured around societal needs and technological capabilities. Recognizing these patterns not only honors the legacy of the field but also informs future strategies, reinforcing the importance of adapting and evolving within an ever-changing marketplace.
Innovative Practices in Manufacturing
Innovative practices are crucial for any leading manufacturing company aiming to maintain a competitive edge. These practices are not only about the adoption of new technologies but also encompass the entire approach to processes, products, and business models. Emphasizing innovation ensures that companies stay relevant and respond effectively to market demands.
The benefits of embracing innovative practices include:
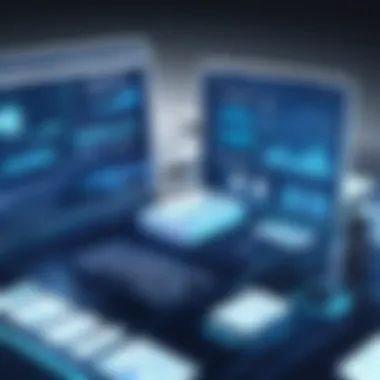
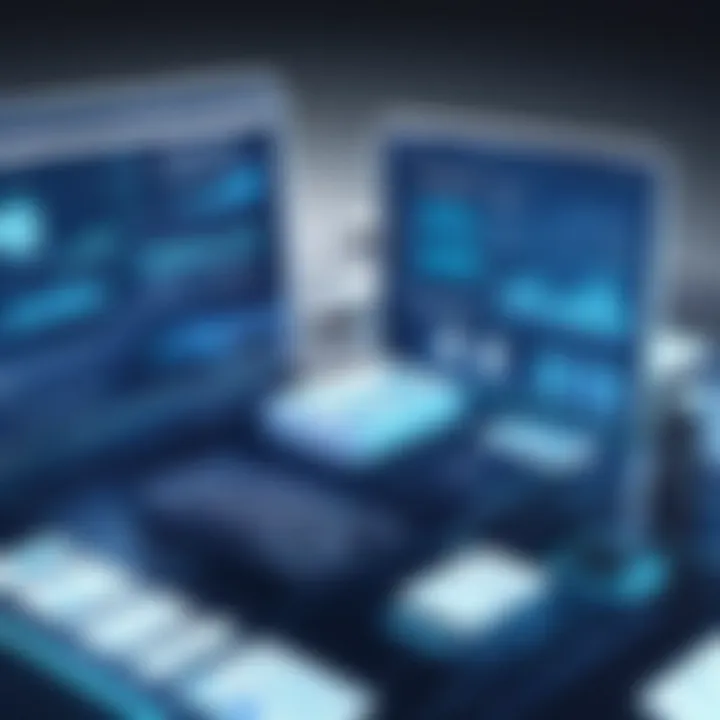
- Increased Efficiency: Streamlining operations often leads to reduced costs and higher productivity.
- Improved Quality: Advanced techniques and technologies help achieve more consistent and higher quality outputs.
- Enhanced Flexibility: Innovative manufacturing allows companies to adapt quickly to changing consumer preferences or external market pressures.
- Sustainability: Incorporating eco-friendly practices can enhance corporate reputation and compliance with regulations.
Considerations about innovative practices involve investment decisions, risk management, and the capability to integrate new technologies while ensuring that staff are equipped to operate within these new frameworks.
Adoption of Advanced Technologies
The adoption of advanced technologies is a pillar of innovative manufacturing practices. Technologies such as automation, AI, and IoT are revolutionizing the sector. These innovations lead to significant changes in how products are designed, produced, and delivered.
- Automation: Robotic process automation allows for repetitive tasks to be performed more efficiently, thereby freeing up human resources for more complex problem-solving tasks.
- Artificial Intelligence: AI applications can optimize production schedules, foresee maintenance needs, and even predict consumer trends. This strategic use of data interpretation can result in better product offerings.
- IoT Integration: The Internet of Things enables machines to communicate, thus improving operational visibility and maintenance processes. This connectivity helps in gathering data for continuous improvement.
Organizations that have implemented these technologies often experience lower operational costs and increased output capacity. Companies such as General Electric and Siemens exemplify success in this sphere.
Research and Development Investments
Investing in research and development (R&D) is an essential element for any manufacturing firm that seeks to lead the market. R&D promotes the creation of new products and the enhancement of existing ones. This investment supports innovation at the core level and enables businesses to explore new market opportunities.
The importance of R&D investments can be highlighted in several key areas:
- Product Innovation: R&D activities can lead to breakthrough products that significantly alter market dynamics, making a company the first choice for consumers.
- Process Improvement: Ongoing research ensures that manufacturing processes evolve to become more efficient, reducing time-to-market and production costs.
- Competitive Advantage: A strong focus on R&D allows firms to stay ahead of competitors, as they can quickly adapt to market changes and consumer needs.
- Collaboration and Knowledge Sharing: Engaging with universities and technology providers often leads to shared innovations and valuable insights.
Supply Chain Management Strategies
Supply chain management strategies are fundamental to the operations of a leading manufacturing company. The dynamics of supply chains are complex and involve multiple factors that impact overall performance. A well-structured supply chain is not only about the flow of goods but also encompasses information flow, financial flow, and relationships between all parties involved.
An effective supply chain management strategy can lead to significant benefits. These include reduced operational costs, improved service delivery, enhanced customer satisfaction, and ultimately, increased profitability. A leading manufacturing company places a strong emphasis on optimizing its supply chain to achieve these benefits, as well as to maintain a competitive position within the market.
Key considerations for supply chain management strategies in manufacturing include:
- Visibility and Transparency: Clear visibility throughout the supply chain enhances decision-making processes.
- Agility: The ability to respond quickly to changes in market demand is crucial for maintaining efficiency.
- Risk Management: Identifying potential disruptions and planning responses in advance is essential for continuity.
Investing in technology that supports these strategies can further enhance efficiency and productivity.
Optimization Techniques
Optimization techniques in supply chain management focus on improving processes, reducing waste, and ensuring timely delivery of products. Data analytics plays a critical role in this area. Companies utilize analytics tools to assess patterns, predict demand fluctuations, and make informed decisions.
Some effective optimization techniques include:
- Lean Manufacturing: This approach minimizes waste without sacrificing productivity. It focuses on delivering value to customers while reducing costs.
- Just-In-Time (JIT) Inventory: JIT aims to keep inventory levels low, reducing holding costs and ensuring that resources meet the precise demands of production schedules.
- Automated Supply Chain Platforms: Leveraging digital platforms for managing the supply chain allows real-time tracking and faster decision-making.
Supplier Relationship Management
Supplier relationship management (SRM) is a vital component of supply chain management. Establishing strong relationships with suppliers can lead to better pricing, quality materials, and improved collaboration. A leading manufacturing company understands the importance of nurturing these relationships.
Key aspects of SRM include:
- Communication: Maintain regular communication to ensure alignment of goals and timelines.
- Supplier Evaluation: Periodically assess supplier performance against established criteria to ensure quality and reliability.
- Collaboration: Engage suppliers in the innovation process to derive mutual benefits and explore new opportunities.
"The strength of a supply chain lies in its relationships. Strong suppliers can lead to sustained manufacturing excellence."
By prioritizing these strategies, a leading manufacturing company can navigate the complexities of supply chains efficiently, thereby positioning itself as a leader within the industry.
The Workforce Behind Manufacturing Success
The success of a manufacturing company largely hinges on its workforce. Humans are a vital asset, not only in terms of operational efficiency but also in fostering innovation and maintaining competitive advantage. This section will shed light on two key areas: talent acquisition and retention, as well as training and development programs.
Talent Acquisition and Retention
Talent acquisition is a critical process. It involves attracting, selecting, and onboarding individuals with the appropriate skills and attitudes. Companies that excel in this area tend to have a clearer understanding of their immediate and future needs. They develop a strong employer brand which speaks not just to job seekers, but to potential clients and stakeholders as well.
The ability to retain skilled workers is equally important. The manufacturing industry recognizes that turnover can be costly, impacting production timelines and morale among remaining staff members. To address these challenges, firms employ various strategies:
- Competitive salaries and benefits: Offering pay rates that reflect market demands.
- Employee engagement: Creating a workplace that values contributions and fosters a sense of belonging.
- Opportunities for growth: Providing clear paths for career advancement can keep employees motivated.
Overall, companies must prioritize these aspects to secure a loyal and skilled workforce that drives success.
Training and Development Programs
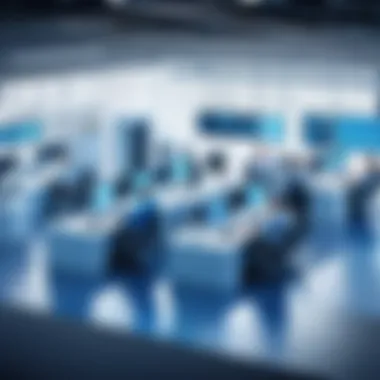
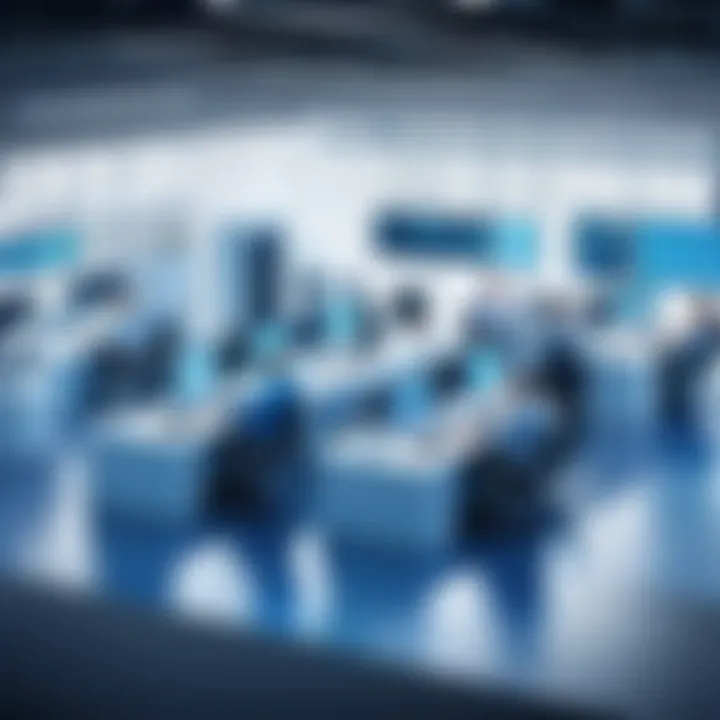
Even with the right talent, the effectiveness of a workforce heavily depends on continuous training and development. In the manufacturing sector, technologies evolve rapidly, making ongoing education vital. Training programs should not only aim at enhancing technical skills but also at improving soft skills like teamwork and communication.
Key points about effective training programs include:
- Tailored training: Customized sessions based on specific roles and technologies. This ensures precision in skill development.
- Hands-on experience: Simulations and real-life projects provide valuable practical exposure, bridging the gap between theory and application.
- Feedback mechanisms: Regular assessments help identify areas needing attention and foster an environment for continuous improvement.
"A company's greatest asset is its people. Without them, success is just a dream."
By investing in these workforce dynamics, manufacturing companies secure not only their operational functions but also their innovative capabilities and market position.
Financial Performance Indicators
Financial performance indicators represent a crucial aspect in understanding how well a manufacturing company functions. They provide measurable data that is essential for evaluating the company’s financial health, efficiency, and overall market performance. By scrutinizing these indicators, stakeholders can gain insights about the effectiveness of management decisions, operational processes, and market competitiveness. This segment aims to elucidate the significance of financial performance indicators and how they reflect the underlying dynamics of a leading manufacturing firm.
Key Metrics for Evaluation
Key metrics offer detailed insights about specific areas within financial performance. Among the most critical metrics to consider are:
- Gross Profit Margin: Indicates the percentage of revenue that exceeds the cost of goods sold. High margins suggest strong pricing strategies or effective production controls.
- Net Profit Margin: This reflects the actual profitability after all expenses, taxes, and interest. Companies with a high net profit margin are usually more resilient in economic downturns.
- Return on Assets (ROA): This metric assesses how effectively a company utilizes its assets to generate earnings. A higher ROA indicates more efficient asset management.
- Return on Equity (ROE): It measures profitability relative to shareholders’ equity. A higher ROE signifies effective utilization of capital, attracting investors.
These metrics not only allow for internal assessments but also provide a benchmark against competitors in the industry. As decision-makers analyze these numbers, they obtain vital information relevant to operational adjustments or strategic shifts.
Market Positioning Analysis
Market positioning analysis ties closely with financial indicators. It helps in understanding how a manufacturing company stands in relation to its competitors in a specific market segment. Critical components of market positioning include:
- Market Share: The percentage of an industry or market's total sales attributed to a company. A growing market share often correlates with higher sales and profitability.
- Competitive Advantage: This entails identifying what differentiates a company from others. Strong brands or proprietary technologies often create a favorable positioning.
- Customer Segmentation: Understanding the target audience is essential for tailoring products and services that meet specific needs.
Evaluating these aspects alongside financial metrics aids in forming a comprehensive view of a company’s operational efficacy and strategic direction. In summary, financial performance indicators are not mere numbers but fundamental tools for leaders aiming to steer their companies toward sustained success.
"Financial performance indicators are the compass that guide decision-makers amid the complexities of manufacturing industry dynamics."
By keeping a keen eye on these indicators, leaders can drive their organizations with data-backed insights, ensuring responsiveness to market trends and fostering long-term sustainability.
Sustainability in Manufacturing Practices
Sustainability in manufacturing practices represents a strategic shift that addresses growing environmental concerns while enhancing operational efficiency. It has emerged as an essential element for leading manufacturing companies in today's marketplace. Such practices not only help in reducing ecological footprints but also align with consumer expectations and regulatory requirements. A commitment to sustainability can lead to long-term benefits, including cost savings, enhanced brand reputation, and improved competitiveness.
Companies adopting sustainable practices are more likely to attract eco-conscious customers and investors. Furthermore, they often enjoy operational advantages due to efficient resource use. This includes reduced waste and energy consumption, which can result in significant savings over time. In an era where consumers are increasingly making purchasing decisions based on a company's environmental policies, sustainability can become a key differentiator in crowded markets.
Environmental Impact Assessments
Environmental Impact Assessments (EIAs) are crucial in identifying and mitigating potential negative effects that manufacturing processes might have on the ecosystem. It involves a comprehensive evaluation of the environmental consequences of decisions before they are made. Leading manufacturers leverage EIAs to ensure compliance with environmental regulations and to safeguard against potential liabilities.
Moreover, EIAs provide valuable insights that can guide companies toward refining their processes. For instance, an EIA may reveal the need for improved waste management systems or alternatives to harmful substances. By implementing changes based on these assessments, companies not only comply with laws but also strengthen public perception and stakeholder trust.
"Sustainability requires a transition from conventional practices to innovative solutions that foster respect for the environment."
Sustainable Materials and Processes
The use of sustainable materials and processes is another pivotal aspect of manufacturing sustainability. Sourcing environmentally friendly raw materials can significantly reduce the manufacturing net ecological footprint. For example, using recycled materials, biodegradable alternatives, or sustainably sourced inputs can promote a circular economy.
Furthermore, optimizing manufacturing processes to minimize resource utilization is essential. Techniques such as lean manufacturing focus on eliminating waste and improving efficiency. This, combined with adopting renewable energy sources, can drastically lower carbon emissions associated with production. By investing in sustainable materials and processes, a manufacturing company can thus achieve not only compliance with new regulations but also leverage cost efficiencies over time.
In summary, sustainability in manufacturing is not merely a trend; it is a critical component for success in today's global landscape. Manufacturers that prioritize sustainability are likely to thrive in a competitive environment, benefiting from both operational efficiencies and a stronger market position.
Market Trends Affecting Manufacturing
Understanding market trends is crucial for leading manufacturing companies. These trends shape operational strategies, influence investment decisions, and ultimately define market positioning. In an era of rapid change, businesses must remain agile and adapt to dynamic market conditions. This section discusses two important trends: global market dynamics and shifts in consumer demand.
Global Market Dynamics
The global marketplace is characterized by various factors that influence how manufacturing companies operate. Trade policies, political stability, and technological advancements all play significant roles. The interconnectivity of economies means that changes in one region can have ripple effects worldwide.
- Trade Agreements: Companies must understand how international trade agreements affect tariffs, import/export regulations, and competition. For example, the United States-Mexico-Canada Agreement (USMCA) reshaped trade relations between these countries. - Emerging Markets: Manufacturers often look to emerging markets for expansion opportunities. Nations like India and Brazil present new customer bases but also unique challenges such as regulatory compliance and local manufacturing standards. - Technological Innovations: The proliferation of digital technologies is transforming manufacturing. Automation and artificial intelligence increase efficiency, but companies must invest wisely to integrate these technologies into their processes.
"Staying ahead of global market trends ensures that manufacturers can pivot quickly and effectively, preparing them for changes in demand or disruptions."
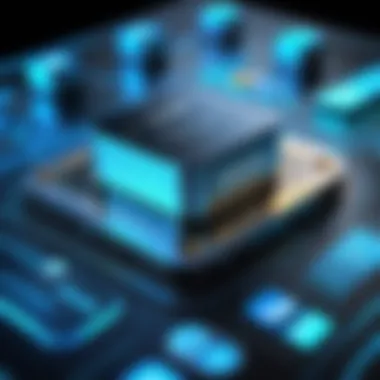
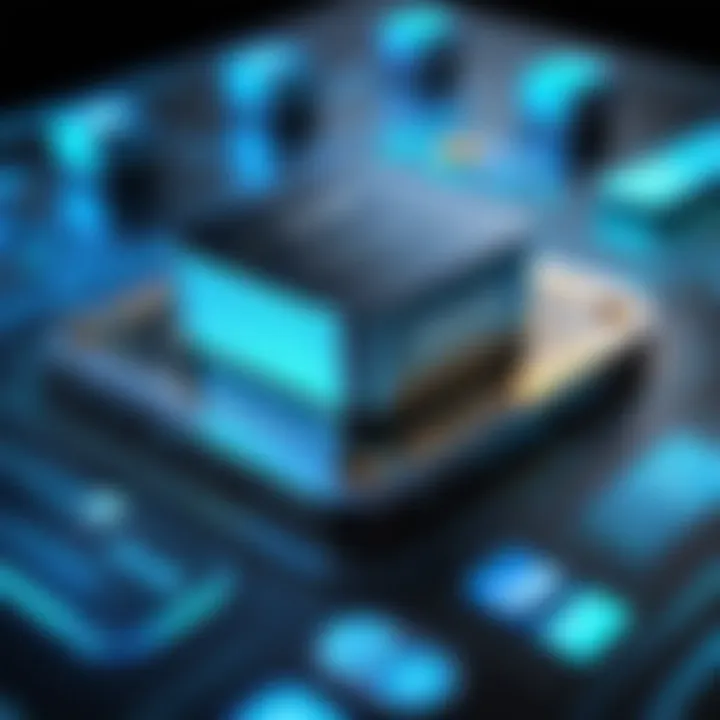
Consumer Demand Shifts
Consumer preferences are continually evolving, driven by factors such as demographic changes and technological advancements. Understanding these shifts is vital for manufacturers who want to remain competitive.
- Customization: Modern consumers increasingly seek personalized products. Manufacturers must leverage technologies that allow for customization at scale. - Sustainability: There is a growing demand for environmentally friendly products. Consumers are more likely to support brands that demonstrate a commitment to sustainable practices. - Digital Experiences: The rise of e-commerce has changed the way consumers interact with brands. Manufacturers should focus on creating seamless online experiences to meet evolving expectations.
In summary, market trends significantly impact manufacturing companies. Those who can anticipate and adapt to global dynamics and shifts in consumer demand will maintain a competitive edge. Strategic responses to these trends will be essential for long-term success.
Navigating Regulatory Frameworks
Navigating regulatory frameworks is crucial for leading manufacturing companies to maintain operational integrity and sustain competitive advantage. Understanding the various regulations influencing manufacturing helps companies ensure compliance and drive continuous improvement. Companies must be aware of local, national, and international laws that govern production processes, environmental standards, employee safety, and product quality. This awareness is not just about avoiding penalties; it is about building a reputable brand that customers can trust.
A well-structured approach to compliance involves analyzing regulations and designing processes that meet or exceed these requirements. This proactive stance can improve operational efficiency and reduce risks associated with non-compliance. For industry leaders, remaining compliant can enhance market position and foster consumer confidence.
Compliance Challenges
Compliance challenges in manufacturing can vary significantly. These challenges often arise from the complexity of regulations, which can affect multiple aspects of manufacturing activities. For instance, companies might deal with conflicting standards from different jurisdictions, complicating adherence. Another challenge could stem from frequent changes in regulatory requirements. Keeping up with these changes demands vigilance and flexibility.
In addition, smaller manufacturers may find it particularly difficult to comply due to limited resources. Larger organizations often have dedicated teams to address compliance; smaller ones might struggle without such support. The implications include potential fines, production delays, and damage to reputation.
Addressing these compliance challenges can bring about opportunities for improvement. For example, integrating compliance management systems is a beneficial initiative. Such systems can streamline processes, ensuring companies consistently align with required standards.
Safety and Quality Standards
Safety and quality standards are non-negotiable pillars in manufacturing. Adhering to these standards helps safeguard both employees and customers. Regulations like OSHA's safety guidelines in the United States reinforce the significance of workplace safety. For instance, having proper equipment and training can minimize workplace accidents.
Similarly, adhering to quality standards ensures that products meet customer expectations, fostering brand loyalty. ISO 9001, an international standard, serves as a benchmark for maintaining quality management systems. Adopting such standards can lead to more efficient practices and reduce waste.
"Quality is not an act, it is a habit." – Aristotle, underscoring the necessity of integrating quality standards into the ethos of a manufacturing culture.
Future of Manufacturing
The future of manufacturing is critical for understanding how leading companies will operate in an ever-evolving global landscape. This section discusses emerging trends and innovative practices that can redefine production methods. As businesses face challenges like competition and resource scarcity, focusing on foresight in manufacturing becomes increasingly relevant.
Emerging Technologies
Emerging technologies are the backbone of future manufacturing processes. Companies are rapidly incorporating tools like artificial intelligence, machine learning, and the Internet of Things into their operations. These technologies enable real-time data analysis, leading to more informed decision-making. Furthermore, automation reduces the risk of human error, thus improving efficiency and productivity.
The benefits of adopting these technologies include:
- Increased Efficiency: Automation allows tasks to be completed faster with high precision.
- Cost Reduction: Smart manufacturing can lower operational costs through optimized resource use.
- Enhanced Quality Control: Real-time monitoring helps identify defects early in the production process.
However, companies must consider several aspects before embracing these technologies. For instance, integrating new systems often requires significant investment and staff retraining. Additionally, cybersecurity threats are a growing concern as more systems become interconnected.
Evolution of Industry Standards
The evolution of industry standards plays a significant role in shaping the future of manufacturing. As technologies advance, so do the regulations and guidelines that govern production practices. New standards often aim to address safety, environmental concerns, and quality control.
Understanding evolving standards is crucial for:
- Compliance: Companies must stay updated with regulations to avoid legal repercussions.
- Market Competitiveness: Adhering to or exceeding standards can enhance a company's reputation.
- Sustainability: New regulations often promote better environmental practices, which can be advantageous in today’s market.
"Staying ahead in industry standards not only protects a business but also signals commitment to quality and sustainability to consumers."
End: The Path Forward
The Conclusion of an article serves as a critical point that synthesizes the information, drawing insights from the previous sections. In the context of this discussion, it provides a gateway to shaping practical strategies for manufacturing leaders. It encapsulates the essence of how companies evolve within the intricate landscape of manufacturing. Understanding the dynamics presented is crucial since they outline the blueprint for future competitiveness and sustainability.
Strategic Recommendations for Leaders
Manufacturing leaders must adopt a proactive stance in navigating the industry’s complex realities. Here are several key recommendations:
- Embrace Technological Advancements: A commitment to integrating cutting-edge technologies is vital. This includes automation, artificial intelligence, and data analytics. Leaders should invest in systems that streamline operations and enhance productivity.
- Prioritize Sustainability: Sustainability cannot be an afterthought. Companies should evaluate and implement green practices. This enhances brand loyalty and aligns with global environmental initiatives.
- Cultivate Workforce Competence: A skilled workforce is crucial. Investing in training programs ensures that employees are equipped with necessary skills. Retaining talent through robust development opportunities cuts down on recruitment costs.
- Foster Innovation: Leaders must create an environment that encourages innovation. This can be done by setting up dedicated teams for R&D and supporting new ideas. The aim is to continually adapt and overcome market challenges.
*"The future of manufacturing lies in the hands of those who dare to innovate and adapt."
- Enhance Supply Chain Resilience: Understanding and mitigating risks in the supply chain is essential. Forming strong relationships with suppliers and seeking alternatives can secure operations against disruptions.
The Role of Innovation in Sustaining Leadership
Innovation is not just an option; it is the bedrock of leadership in manufacturing. Continuous innovation allows companies to refine products and processes, maintaining relevancy in fast-paced markets. Key aspects include:
- Product Development: Regularly updating product lines ensures that consumer interests are met. Innovation leads to differentiated offerings that can command premium prices.
- Process Efficiency: Investing in new technologies improves efficiency. Optimized processes lower production costs and increase output quality, contributing to higher profit margins.
- Customer-Centric Approaches: Innovative strategies should revolve around consumer needs. This includes engaging customers for feedback during the development phase, leading to products that are more likely to succeed.
- Cross-Industry Collaboration: Innovations can also stem from partnerships across different industries. Collaborating with tech firms or sustainability-focused organizations can lead to breakthroughs that set a company apart.
In summary, the path forward involves strategic foresight, a commitment to innovation, and an unwavering focus on sustainability. For manufacturing leaders, this is not just about survival but thriving in an ever-evolving industry.