Exploring the Siemens Manufacturing Execution System
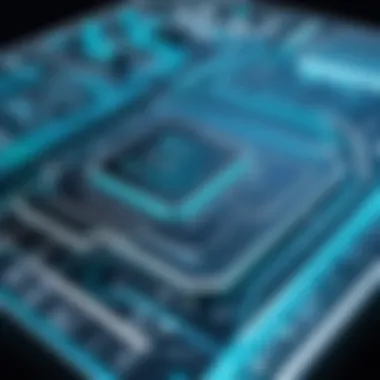
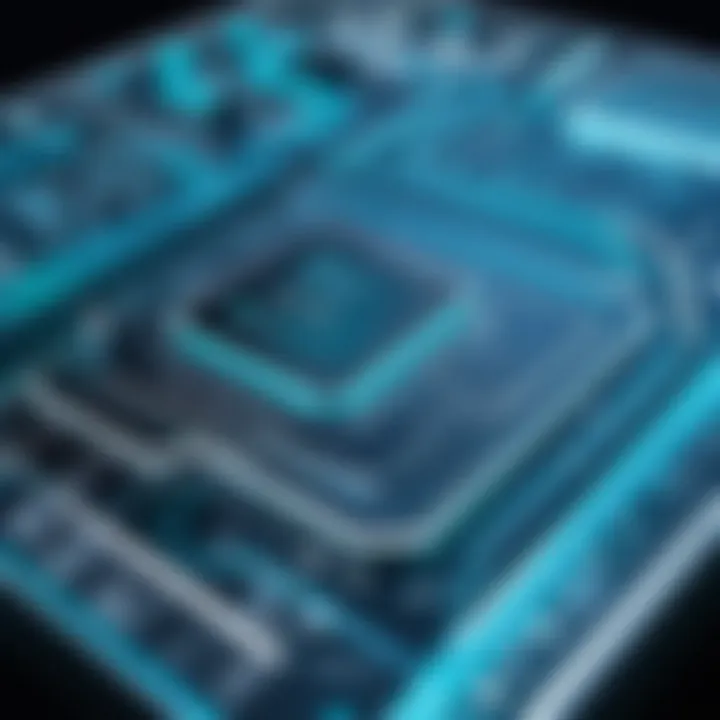
Intro
The conversation around manufacturing efficiency has shifted dramatically in the face of advanced technologies. At the forefront of this evolution is the Siemens Manufacturing Execution System (MES), a solution that not only streamlines operations but also enhances the overall production lifecycle. As competition rises and the demand for rapid, quality output increases, understanding how Siemens MES integrates into this landscape becomes crucial. This section sets the stage for a deep dive into the multi-faceted world of Siemens MES, where we will explore its core features, capabilities, and the ways it drives success in modern manufacturing.
Key Software Features
Siemens MES stands out in an increasingly crowded field, thanks to its robust features designed to meet the nuanced requirements of various industries.
Essential functionalities
At its core, Siemens MES offers several essential functionalities that help organizations maintain a competitive edge. Some of these include:
- Real-time production monitoring: This allows decision-makers to keep a finger on the pulse of their operations, ensuring that any issues can be addressed immediately. The capability to visualize production flows in real time helps in making informed decisions swiftly.
- Data collection and analysis: The system collects vast amounts of data throughout the production process. By analyzing this data, organizations can uncover inefficiencies and optimize workflows.
- Quality assurance and compliance: Siemens MES provides tools that ensure products meet quality standards and regulatory compliance. This is particularly important in sectors with strict guidelines, such as pharmaceuticals and food production.
Advanced capabilities
Beyond the basics, Siemens MES incorporates advanced capabilities that elevate it above traditional systems:
- Integration with IoT: In this era of connectivity, Siemens MES harnesses the Internet of Things (IoT), enabling seamless data exchange between machinery and the MES. This integration fosters predictive maintenance, reducing downtime and extending the lifespan of equipment.
- Customizable dashboards: Tailoring the dashboard for specific user needs allows for a more intuitive experience. Operational managers can choose the metrics and KPIs that matter most to them, facilitating quick assessments of performance.
- Scalability options: As businesses expand, their processes evolve. Siemens MES is built for scalability, meaning it can adapt as operations grow, minimizing disruptions during transitions.
"A well-implemented MES can be the bridge between strategy and execution, delivering visibility across operations and aligning production with business goals."
Comparison Metrics
When evaluating Siemens MES against competitors, certain metrics are indispensable for decision-making.
Cost analysis
Understanding the financial implications of implementing Siemens MES involves evaluating both upfront and ongoing costs. Although the initial investment might appear significant, the potential for enhanced productivity and reduced errors can deliver a favorable return on investment. Organizations often find that the long-term savings in operational costs far outweigh the initial expenditures.
Performance benchmarks
To assess the effectiveness of Siemens MES, a series of benchmarks can be employed:
- Efficiency rates: Measure the percentage increase in production throughput post-implementation.
- Error reduction metrics: Track the decline in production errors, aiming for continuous improvement.
- User adoption rates: Gauge how quickly and effectively staff adapt to the system; this can be a direct reflection of its usability.
In sum, Siemens MES is not just a tool; it’s a comprehensive approach to manufacturing strategy that encourages smarter, more informed decisions. As industries evolve, embracing its capabilities is crucial for any organization looking to thrive in today’s manufacturing ecosystem.
Understanding Manufacturing Execution Systems
Manufacturing Execution Systems (MES) play a crucial role in connecting the myriad of processes that occur on the shop floor with higher-level enterprise systems. Understanding these systems is paramount for any organization that aims to improve productivity, quality, and operational efficiency. MES serves as a bridge between manufacturing and management, enabling real-time data collection and analysis, thus optimizing production activities.
These systems are not just fancy software; they encapsulate a philosophy of continuous improvement. As the industry transitions into Industry 4.0, integrating advanced technology is becoming the name of the game. Here, MES provides the ability to adapt swiftly, which is key in environments that change faster than the blink of an eye.
Defining MES
Manufacturing Execution Systems can be defined as software applications that facilitate the execution of manufacturing processes. They track, document, and control the transformation of raw materials into finished goods in real-time. Simply put, they're the overseers of the production flow.
The core function of MES is to ensure that manufacturing operations are executed efficiently, minimizing downtime and waste. This often involves real-time monitoring of machines, scheduling of production run times, and workforce management. As per various sources, MES is reported to improve production output by as much as 25% in many cases.
Key Features of MES
When digging into the specifics, MES systems offer a slew of features, some of which can be highlighted as follows:
- Real-Time Data Collection: Enabling manufacturers to monitor production processes instantaneously.
- Production Scheduling: Assisting in allocating resources effectively to minimize delays.
- Quality Control: Incorporating tools for real-time inspection and compliance with safety standards.
- Traceability: Keeping comprehensive records of materials and processes for accountability and transparency.
These features come together to create a robust platform that not only simplifies complex operations but enhances decision-making capabilities through data-driven insights.
The Evolution of MES in Manufacturing
The evolution of MES has witnessed significant changes over the years. Initially, MES was a simple tool focused primarily on data collection. Nowadays, it's integrated into broader digital first-class strategies, often linking IoT devices and leveraging big data analytics.
In the earlier days, industries largely depended on manual processes, which limited their agility and response times. However, with the advent of digital technologies, the shift towards MES has radically transformed how manufacturers approach production.
Notably, there has been a shift towards cloud-based solutions, enabling manufacturers to access their systems anytime and anywhere. This democratization of data not only empowers factory workers but fosters a culture of transparency and efficiency.
"Manufacturing Execution Systems represent a quantum leap in operational efficiency and agility, perfectly aligning with the rapid pace of technological advancements in the industry."
In summary, understanding Manufacturing Execution Systems is not merely about grasping their definitions and features. Instead, it's about recognizing their transformative potential in modern manufacturing landscapes, presenting countless opportunities for operational excellence and innovation.
Siemens MES Overview
The Siemens Manufacturing Execution System (MES) stands as a pivotal solution in today’s manufacturing landscape. Understanding its overview is crucial for grasping how it impacts operational efficiency, quality control, and data management across various industries. This section will break down the central aspects of Siemens MES—including its core components, user experience, and integration capabilities—that underscore its significance.
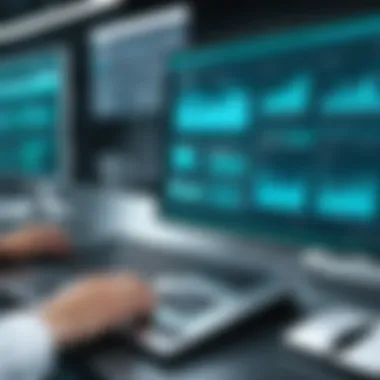
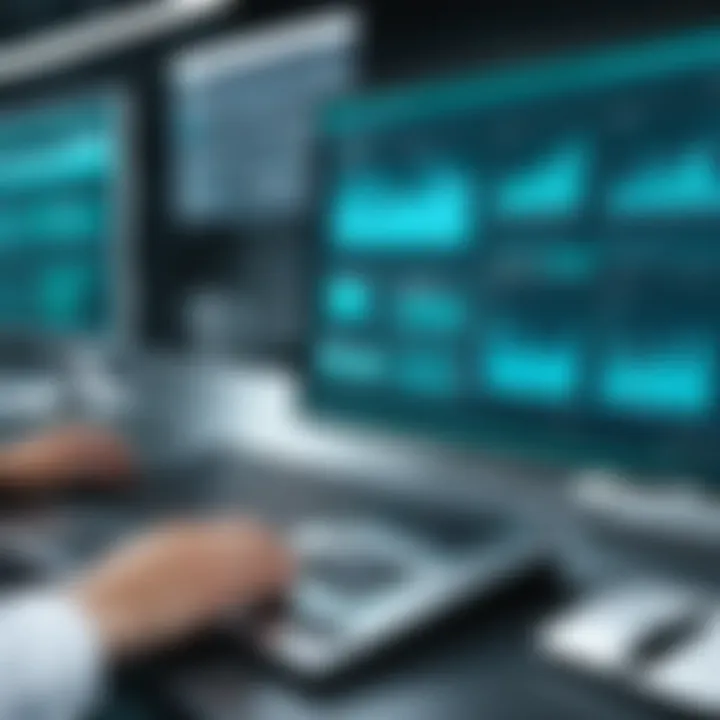
Core Components
The core components of Siemens MES are integral for seamless operation within a manufacturing environment. These components underpin the entire system, ensuring that relevant data is captured, processed, and utilized effectively. Key elements include:
- Data Collection: Siemens MES offers mechanisms for real-time data acquisition directly from machinery and processes. This allows for precise monitoring and decision-making.
- Production Monitoring: The system facilitates continuous oversight of production activities, ensuring that bottlenecks are identified and resolved swiftly.
- Analytics Engine: By harnessing raw data, Siemens MES provides actionable insights through advanced analytical tools. These insights enhance understanding of trends and operational efficiency.
- Reporting Tools: Built-in reporting functions enable teams to generate forecasts and summarize performance metrics, translating data into comprehensible formats for stakeholders.
If companies understand and leverage these components, they can significantly improve their manufacturing processes—mitigating downtime and enhancing productivity, which are essential in a highly competitive market.
User Interface and Experience
User experience is a considerable facet of any system, particularly for those at the forefront of managing manufacturing operations. Siemens MES excels here, delivering an interface that balances functionality with accessibility. Here are a few attributes:
- Intuitive Design: The layout is user-friendly, reducing the learning curve for professionals. Often described as easy to navigate, it’s designed with the user’s needs in mind.
- Customizability: Operators can tailor dashboards to display relevant metrics, making it easier for them to focus on their specific tasks and objectives.
- Real-Time Alerts: The interface integrates notifications that inform users of any unexpected changes in production, enabling quick reactions and mitigating potential issues before they escalate.
A strong user experience ensures that key personnel can access information swiftly and act decisively, enhancing overall operational efficiency.
Integration Capabilities
Integration capabilities are another cornerstone of Siemens MES, facilitating its adoption in existing manufacturing setups. The ability to connect with legacy systems, IoT devices, and other software solutions is crucial for businesses aiming to maintain a competitive edge. Important points include:
- Seamless Connectivity: Siemens MES is designed to communicate with various enterprise resource planning (ERP) systems, offering flexibility and ease of implementation within different IT environments.
- Interoperability: The system can work alongside existing machinery and software, ensuring that companies don’t face significant operational disruptions during deployment.
- Scalability: As manufacturing demands grow, Siemens MES can be expanded to incorporate additional capabilities, such as advanced data analytics or newer technologies, enabling firms to stay ahead of the curve.
"A successful integration of MES not only increases productivity but also generates a more agile and adaptive manufacturing environment."
Through its integration capabilities, Siemens MES empowers organizations to future-proof their operations, translating into increased adaptability and responsiveness to market dynamics.
Functionalities of Siemens MES
Understanding the functionalities of Siemens Manufacturing Execution System (MES) is vital for organizations to optimize their manufacturing processes. These functionalities play a crucial role in improving operational effectiveness, ensuring quality standards, and making informed decisions based on real-time data. In this section, we will delve into four core functionalities: Real-Time Data Monitoring, Production Planning and Scheduling, Quality Management, and Traceability and Compliance. Each of these elements contributes to enhancing overall performance in the manufacturing sector.
Real-Time Data Monitoring
One of the standout features of Siemens MES is its capability for real-time data monitoring. This isn't just a luxury—it's a necessity for modern manufacturing. By facilitating continuous tracking of production processes, decision-makers can obtain immediate insights into production status, machine performance, and overall workflow efficiency.
- Immediate Insights: Access to real-time data means issues can be identified and rectified almost instantaneously. For instance, if a machine is underperforming, operators are alerted right away, allowing them to take corrective action before it impacts production.
- Enhanced Visibility: This monitoring allows for comprehensive visibility across the production floor, which aids in understanding bottlenecks and inefficiencies. When teams can see exactly where delays are happening, it becomes easier to implement solutions.
"In the increasingly complex landscape of manufacturing, real-time data monitoring acts as the compass guiding companies through their operational journey."
Production Planning and Scheduling
Effective production planning is like a well-rehearsed dance—every step must be in sync to ensure seamless output. Siemens MES provides powerful tools that help in planning and scheduling tasks with precision.
- Resource Allocation: By analyzing current workload, resource availability, and production timelines, Siemens MES allows managers to allocate tasks effectively. This leads to better utilization of resources and minimization of idle time.
- Flexibility and Adaptability: In an ever-changing manufacturing landscape, the ability to adapt schedules on-the-fly is crucial. Siemens MES supports adjustments based on real-time changes such as machine breakdowns or supply chain disruptions, ensuring that production continues smoothly.
Quality Management
Quality is often the cornerstone of manufacturing success. With Siemens MES, organizations can implement robust quality management systems that help in maintaining standards throughout the production cycle.
- Standardization of Processes: MES ensures that manufacturing processes adhere to defined standards. This leads to consistency, reducing the occurrence of defects and variations in products.
- Real-Time Quality Checks: Frequent quality checks during the manufacturing process mean that defects can be detected early. This proactive approach not only saves time but also significantly cuts costs associated with post-production corrections.
Traceability and Compliance
In today’s manufacturing environment, compliance to regulations is paramount. Siemens MES excels in providing traceability features that meet global compliance standards.
- End-to-End Traceability: Tracking raw materials through to finished goods is vital for accountability. Siemens MES provides detailed logs that trace each product’s journey, ensuring organizations can easily provide evidence of compliance if questioned.
- Meeting Regulatory Standards: Different industries have varying regulations, and Siemens MES helps organizations navigate these standards without a hitch. This means businesses can operate smoothly without the fear of unexpected audits or penalties.
Benefits of Siemens MES in Manufacturing
The Siemens Manufacturing Execution System (MES) offers a range of important benefits that are pivotal for manufacturing organizations aiming to boost their operational prowess. In the current landscape, where competition is fierce and consumer expectations continue to rise, leveraging an effective MES is crucial. This section will discuss significant elements such as operational efficiency, product quality, data-driven decision-making, and cost reduction strategies that Siemens MES brings to the table.
Enhancing Operational Efficiency
Operational efficiency is the lifeblood of any successful manufacturing operation. Siemens MES facilitates this by providing a holistic view of the production process, thereby increasing visibility and control. For instance, real-time data tracking allows managers to respond promptly to any anomalies, reducing downtime substantially.
With features like automated production scheduling and resource allocation, manufacturers can optimize their workflows and ensure that every cog in the machinery is running smoothly. It’s akin to having a finely-tuned orchestra, where every player knows exactly when to come in and when to hold back.
- Key aspects of operational efficiency through Siemens MES include:
- Real-time data insights: This enables quick identification of bottlenecks and areas of improvement.
- Reduction in manual errors: Automation streamlines processes, thereby minimizing human errors.
- Optimal resource utilization: Ensures that materials and machines are used to their full potential, reducing wastage.
Improving Product Quality
One of the standout features of Siemens MES is its robust quality management capabilities. The system allows for stringent monitoring of quality metrics throughout the production lifecycle. By integrating quality checks at each stage, manufacturers can identify and rectify issues before they escalate.
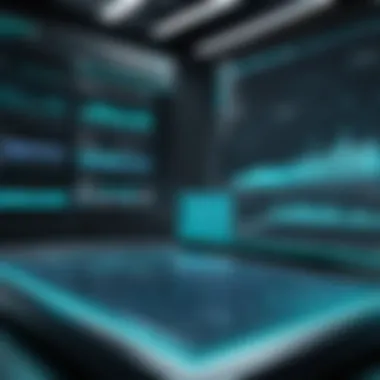
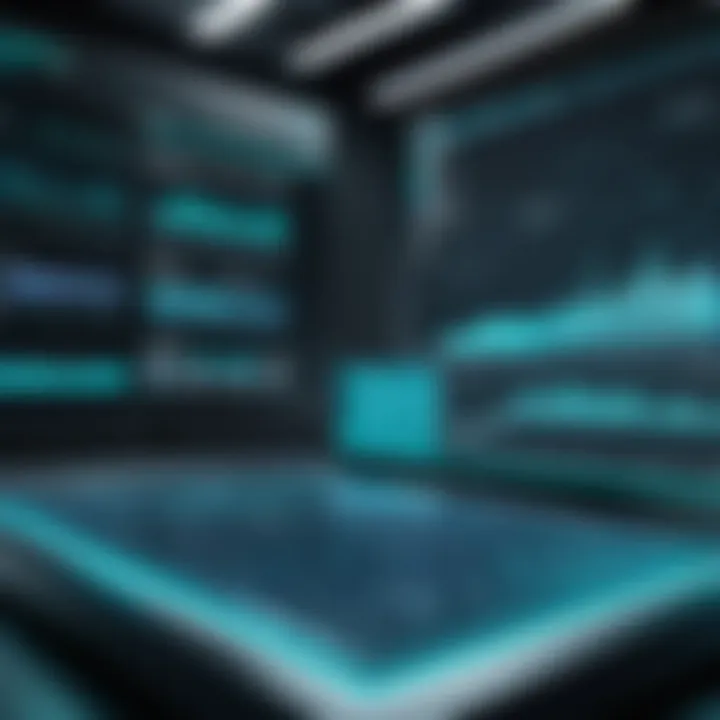
Imagine a scenario where defective products are intercepted earlier in the process instead of flowing through to the final inspection. This saves time, money, and enhances customer satisfaction.
- Key benefits of improved product quality include:
- Consistent quality control: Real-time feedback ensures adherence to standards.
- Fewer recalls and defects: By catching issues early, manufacturers can significantly cut down on costly recalls.
- Enhanced customer trust: High-quality products equate to satisfied customers, fostering loyalty and repeat business.
Data-Driven Decision Making
In today’s data-centric age, the ability to make informed decisions can set a company apart from its competitors. Siemens MES aggregates data from various points in the production process, providing comprehensive analytics that decision-makers can rely on.
Having a well of data at one's fingertips is like having a treasure trove of insights. Managers can analyze trends and patterns, enabling predictive maintenance and forecasting production demands with remarkable accuracy.
- Benefits of data-driven decision-making include:
- Improved forecasts: Accurately predict future production needs based on historical data.
- Responsive strategies: Quickly adapt to changes in market demand or supply chain disruptions.
- Strategic investments: Identify areas where investments can yield the highest returns.
Cost Reduction Strategies
Cost management is always a key concern for manufacturers. Siemens MES provides various avenues for reducing costs without compromising on quality or efficiency. By streamlining operations and improving processes, it helps to identify areas where expenditure can be minimized.
Analysis can help in spotting inefficiencies, whether that's reducing energy costs through better scheduling or minimizing material waste. The aim is not just to cut costs— it's about working smarter, not harder.
- Key strategies for cost reduction include:
- Identifying waste: Real-time tracking helps in recognizing and eliminating wasteful practices.
- Energy management: Optimizing production processes can lead to lower energy consumption.
- Resource optimization: Efficient use of materials can lead to substantial savings.
By embracing Siemens MES, manufacturers can not only improve their operational metrics but also position themselves favorably in a highly competitive market. The benefits extend beyond cost savings and efficiency increases; it's about establishing a sustainable future in manufacturing.
Implementation Challenges
Implementing the Siemens Manufacturing Execution System (MES) is not just a walk in the park. While the potential benefits are quite significant, there are also various challenges that organizations might face. Understanding these hurdles is essential for decision-makers and IT professionals to succeed in the integration of this robust system. Addressing these challenges proactively can help in smoother transitions and better outcomes.
Integration with Legacy Systems
A common headache for many organizations is integrating new technologies with existing legacy systems. Legacy systems often hold a treasure trove of data accumulated over years of operations, but they can also be rigid, outdated, or incompatible with modern MES solutions. The integration challenge here revolves around bridging the gap between old and new technology seamlessly. For example, a manufacturer using older machinery to generate reports may struggle in linking these systems with Siemens MES, affecting real-time performance.
Organizations often find themselves needing to invest further in middleware solutions or custom development to ensure that data flows between systems without a hitch. While this can lead to increased costs in the short term, the long-term benefits of a fully integrated solution—such as enhanced efficiency and foresight into production—can be worth the effort.
User Training and Adoption
Once integration is sorted, the next mountain to climb is user training and adoption. Simply put, having the best MES system in place won’t mean much if users are unsure how to utilize it effectively. Training is critical, but it can be a cumbersome process. Staff may resist learning new tools, especially if they’re accustomed to their old ways of working. It’s all too easy for the sentiment to be, “If it ain’t broke, don’t fix it.”
A successful approach often involves creating a well-structured training program that caters to various user levels. This could include:
- Hands-on workshops
- E-learning modules for remote staff
- Ongoing support and troubleshooting help
Encouraging a culture of continuous learning and providing incentives for adopting the new system can also promote user engagement. When employees see the direct benefits of the system, such as reduced workload or enhanced data accuracy, they are more likely to embrace it wholeheartedly.
Data Security Concerns
With the rise of digital systems, data security is an ever-present concern. As organizations implement Siemens MES, they must be acutely aware of the new vulnerabilities that may arise. Since this system deals with sensitive production information, a breach can lead not just to operational disruption, but potentially to hefty legal repercussions as well.
Organizations need to address several key data security points:
- Access controls must be tightly managed to ensure only authorized personnel can access sensitive data.
- Regular security audits can help identify weaknesses before they become problematic.
- Ensuring end-to-end encryption of data processes can safeguard against interception during transmission.
Comparison with Other MES Solutions
When evaluating the Siemens Manufacturing Execution System (MES), it's pivotal to place it in context against other systems in the market. This comparison not only highlights its unique attributes but also helps organizations understand their options better. Different MES solutions come with varying functionalities, strengths, and weaknesses, each providing a fitting solution dependent on an organization’s specific needs and goals.
Market Leaders and Alternatives
In the landscape of MES software, Siemens faces competition from several prominent market players, each with their own specialties. For instance, Rockwell Automation's FactoryTalk, Schneider Electric's Wonderware, and Honeywell's Manufacturing Execution System each cater to niche markets while providing robust functionality.
- Rockwell Automation - FactoryTalk: Renowned for its integration with automation products and strong data analytics capabilities. FactoryTalk is geared towards the manufacturing sector that heavily relies on Rockwell’s automation tools.
- Schneider Electric - Wonderware: Known for a user-friendly interface and strong visualizations, Wonderware appeals to those who prioritize ease of use and quick implementation. It provides solid real-time monitoring tools crucial for operators on the ground.
- Honeywell MES: This system emphasizes process quality, particularly in industries such as oil and gas or pharmaceuticals where compliance is critical.
As companies assess these alternatives, common criteria include scalability, user support, and the ease of integration with other systems. Such factors become pivotal as businesses grow and technology rapidly evolves.
Functionality Comparison
Comparing the functionalities of Siemens MES with its competitors requires a close look at core aspects like real-time data tracking, customizable dashboards, and industry-specific solutions.
- Data Monitoring: Siemens MES excels in real-time data integration, but Rockwell Automation offers cutting-edge predictive analytics that can foresee equipment failures, thus maximizing uptime.
- Flexibility: Siemens provides a strong suite of tools tailored for various industries, while Wonderware often wins on flexibility due to its extensive customization options. Companies can mold the software to fit existing workflows more seamlessly.
- Reporting Tools: Reporting capabilities are essential for informed decision-making. Siemens MES provides a comprehensive analytics suite, but Honeywell sometimes edges out in performance due to its specialized insights into process efficiencies relevant for regulated industries.
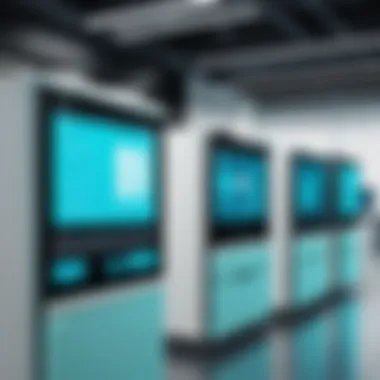
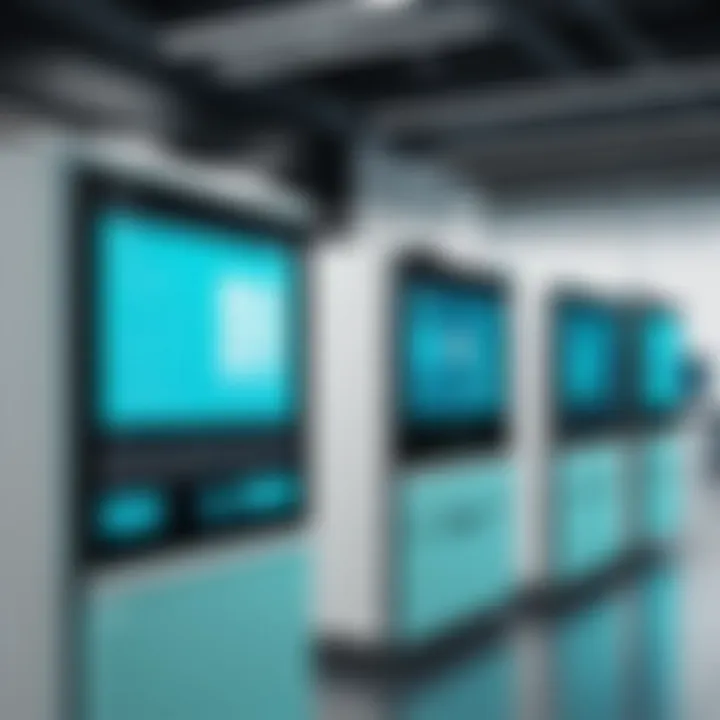
Ultimately, the choice here heavily relies on the specific needs and operational priorities of the organization.
Cost-Benefit Analysis
Price often becomes a deciding factor.
- Initial Setup Costs: Siemens MES, while sometimes appearing costly upfront, can lead to significant long-term savings through efficiency improvements and reduced waste. Each alternative has its pricing structure, but some may claim lower overall initial investments, potentially leading organizations to choose them without considering longer-term value.
- Return on Investment (ROI): Siemens MES often justifies its cost through enhanced production reliability and quality control, which can lead to higher customer satisfaction and reduced returns. The ROI from other systems may vary significantly, depending on how well they integrate with a company's existing processes and the specific metrics measured by each business.
In summary, comprehending these comparisons serves a dual purpose: it enables companies to make informed decisions about which MES solution aligns best with their strategic goals, and it sheds light on the overall market landscape, aiding in further innovation and operational excellence in manufacturing.
Future of Siemens MES
As industries worldwide set their sights on digital transformation, the future of Siemens Manufacturing Execution System (MES) holds promising possibilities. The integration of advanced technologies not only enriches operational intelligence, but also aligns manufacturing practices with the evolving market demands. The focus on making data accessible and actionable is crucial. It enables companies to react nimbly. Siemens MES is not simply a tool; it’s a method to fuel ongoing improvement in manufacturing processes.
The following sections explore two foundational aspects impacting the trajectory of Siemens MES: Technological Advancements and Sustainability Considerations.
Technological Advancements
Siemens MES is riding the wave of technological growth that includes the Internet of Things (IoT), Artificial Intelligence (AI), and Cloud Computing. These innovations act as catalysts, streamlining workflows and improving data interpretation. With IoT, machines can communicate in real-time, allowing for faster decision-making. Imagine a factory floor where machines send alerts before a breakdown occurs. This level of insight minimizes downtime and maximizes productivity.
- Adaptive Learning: Using AI, Siemens MES has the potential to improve through an ongoing learning process. For example, based on historical operational data, AI can recommend optimal production adjustments, ultimately leading to increased efficiency.
- Cloud Integration: Leveraging cloud technology offers scalability and flexibility that on-premises systems often struggle to provide. Companies can access real-time data and analytics, facilitating quicker responses to changes.
- Automation: Siemens MES promotes automated processes that not only enhance speed but reduce human error. This can be especially significant in quality control, where consistent standards are essential.
In short, staying ahead in a competitive market requires not just adopting new technologies, but integrating them holistically within the MES framework. A dynamic Siemens MES can differentiate a business from its rivals, making technology both a tool and strategic advantage.
Sustainability Considerations
Today, environmental responsibility is a growing demand from stakeholders across the board. Siemens MES plays an integral role in fostering sustainable practices within manufacturing environments. Manufacturers are often scrutinized for their environmental impact, and aligning with sustainability goals isn’t just beneficial; it’s necessary.
- Resource Optimization: By employing Siemens MES, companies can cut down on materials waste and optimize energy consumption. Data-driven insights help firms identify inefficiencies in resource usage, leading to reduced energy costs and a lighter environmental footprint.
- Regulatory Compliance: The landscape of manufacturing regulations is increasingly stringent. Siemens MES assists organizations in maintaining compliance with environmental standards, therefore reducing the risk of fines and improving public relations.
- Sustainable Supply Chains: With the use of advanced data analytics, Siemens MES facilitates the creation of greener supply chains. This means tracking supplier sustainability metrics as part of a broader commitment to environmental stewardship.
The focus on sustainability helps companies not only comply with regulations but also build a positive brand image. Companies that prioritize social responsibility frequently attract customers who value ethical practices, creating a win-win scenario.
The future of Siemens MES isn’t merely about technology; it’s about harmonizing those technologies with responsible practices to benefit the business and the environment.
Real-World Case Studies
In the realm of Manufacturing Execution Systems (MES), real-world case studies offer invaluable insights into how these systems, particularly the Siemens MES, have been effectively implemented in various industries. Looking at these cases, we get a clearer picture of practical applications, the nuances of deployment, and the tangible outcomes that can be expected. This not only adds credibility to the claims of effectiveness but also provides a roadmap for organizations considering similar paths.
Real-world examples showcase the practical benefits of Siemens MES beyond theoretical discussions. They illustrate how companies adapt the system solutions to fit their unique challenges and operational contexts. By examining these implementations, stakeholders can understand what works and what doesn't, thereby reducing the risks associated with MES adoption.
Successful Implementations
When we dive into successful implementations of Siemens MES, we see a variety of industries harnessing its capabilities to achieve significant operational improvements. For instance, a leading automotive manufacturer in Germany integrated Siemens MES to streamline production lines. This implementation allowed for real-time data tracking, thus enhancing their ability to manage inventory effectively. The results were striking: the plant saw a 20% reduction in waste and a 15% improvement in throughput.
Moreover, in the food and beverage sector, a regional producer utilized Siemens MES to ensure compliance with health regulations while maintaining quality during production. They could trace every batch of products back to the source materials, providing both transparency and accountability. Customers appreciated the enhanced safety measures, which led to a notable uptick in sales and brand loyalty.
Some key takeaways from these successful cases include:
- Customization: Tailoring the system to meet specific operational needs can yield impressive results.
- Training and Support: Adequate training for staff before and after implementation ensures smooth transitions and enhances system adoption.
- Continuous Improvement: Emphasizing iterative improvements post-deployment can help maximize the system’s potential.
Lessons Learned
As with any complex system, the journey to implementing Siemens MES also comes with its share of challenges and lessons learned. After evaluating multiple case studies, several common themes emerge that organizations can use to inform their approaches.
One common lesson is the need for comprehensive workflow assessments prior to integration. In some instances, companies rushed into the implementation without a thorough examination of existing processes. This oversight sometimes led to misalignment between the MES capabilities and the company's operational workflows. With a proper workflow mapping, many companies found they could better leverage the MES's functionalities.
Additionally, the necessity for ongoing engagement with the staff became a significant point of learning. Employees who felt disconnected from the MES deployment often resisted changes, which hindered efficiency gains. In contrast, organizations that prioritized communication and included their teams in the setup phases noted higher rates of acceptance and integration.
To summarize the lessons learned:
- Engage employees throughout the implementation process to boost acceptance and effectiveness.
- Conduct thorough assessments of existing processes to ensure compatible integration of the MES.
- Establish a robust support system for users, which helps resolve issues swiftly and maintain operational flow.
End and Final Thoughts
In wrapping up our exploration of the Siemens Manufacturing Execution System (MES), it's vital to emphasize the broader implications and significance of this sophisticated technology within the manufacturing landscape. As industries increasingly pivot towards digital transformation, systems like Siemens MES play a pivotal role in aligning operations with strategic business goals. This section encapsulates the importance of the key elements discussed throughout the article, underscoring why decision-makers must pay attention.
The core themes that emerge from the analysis of Siemens MES revolve around efficiency, adaptability, and data utilization. Through features like real-time monitoring and analytics, businesses can not just react to challenges, but also anticipate them, significantly cutting down on downtime and waste. The benefits of leveraging this technology go hands-in-hand with lowering costs and fostering a culture of continuous improvement. In an environment where competition is fierce and margins can be razor-thin, these advantages are as clear as day.
Here are some key insights derived from the article:
- Operational Efficiency: Siemens MES enables streamlined processes, allowing manufacturers to focus on core production tasks without the hindrance of manual interventions.
- Enhanced Quality Control: With integrated quality management, defects can be monitored and rectified in real-time, preventing larger issues down the line.
- Data-Driven Decisions: By mining data effectively, organizations can pivot strategies based on insights, a crucial factor in today's fast-paced market.
Moreover, considering the implementation challenges that surfaced—ranging from integration issues with legacy systems to the necessity of comprehensive user training—it's evident that awareness and preparation are key for a successful transition to a MES.
Looking Ahead
Looking to the future, the trajectories of manufacturing and technology are on a collision course, bringing both challenges and opportunities. It’s here that Siemens MES is poised to shine; its adaptability allows it to integrate upcoming technologies such as artificial intelligence and the Internet of Things (IoT). The potential move towards sustainability cannot be overlooked either. As green initiatives gain traction, MES systems will need to adapt, providing insights into resource utilization and waste management.
As businesses contemplate their next steps for growth and efficiency, they must do so with a keen eye on how MES tools like those from Siemens can mold their strategies. While there's no one-size-fits-all solution, the fundamental capabilities of such systems can be tailored to fit the unique needs of varied manufacturing environments. Understanding this can empower companies to make informed decisions that not only bolster their operational capabilities but also position them for a future where agility and data-driven methodologies will reign supreme.