Digital Maintenance Management: Asset Strategy Revolution
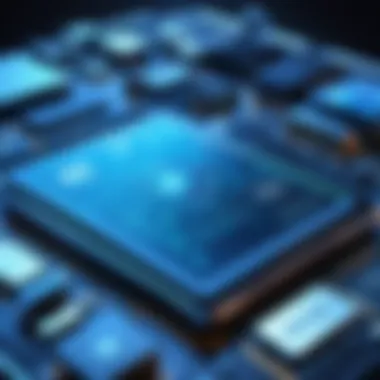
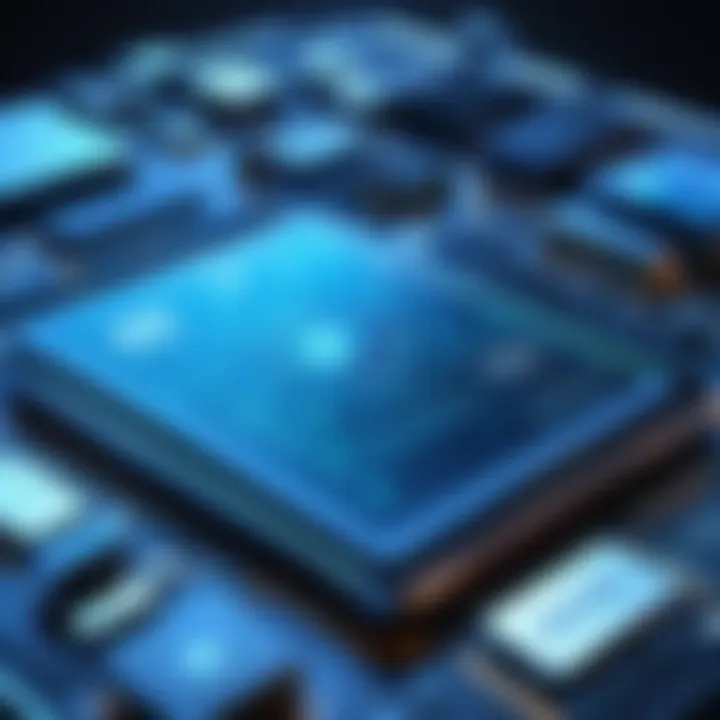
Intro
In the rapidly evolving world of asset management, digital maintenance management has emerged as an essential approach that combines technology with traditional practices. This article delves into how businesses can leverage digital tools to optimize their asset performance while minimizing costs. The integration of concepts like data analytics and IoT plays a pivotal role in this transformation, ensuring that organizations not only maintain but also enhance their operational capabilities.
Maintenance is often undervalued in asset management strategies. However, with the advent of digital solutions, organizations can shift from a reactive to a proactive maintenance culture. This shift leads to reduced downtime, increased lifespan of assets, and ultimately, significant cost savings. Understanding digital maintenance management equips decision-makers with the skills to transform their asset management strategies effectively.
Key Software Features
Digital maintenance management software is built on a foundation of essential functionalities designed to streamline operations. Organizations need to consider these core capabilities:
- Asset Tracking: Real-time monitoring of assets helps in reducing loss and ensuring accountability.
- Work Order Management: Efficient scheduling and tracking of maintenance tasks improve productivity and resource allocation.
- Inventory Management: Keeping track of spare parts and supplies can help avoid delays and minimize the costs associated with excess stock.
- Reporting and Analytics: Robust reporting tools offer insights into maintenance performance, enabling proactive decision-making.
In addition to these essential functionalities, advanced capabilities can set top-tier software apart. These may include:
- Predictive Maintenance: Using data analytics to forecast potential failures and schedule maintenance accordingly.
- Mobile Compatibility: Allowing technicians to access information and update tasks in real-time while in the field.
- Integration with IoT Devices: Enhancing data gathering and analysis from connected machines, ensuring that all relevant information is available for decision-making.
"Digital tools are redefining the operational landscape of asset management, paving the way for smarter and more efficient practices."
Comparison Metrics
When evaluating digital maintenance management solutions, organizations must establish relevant comparison metrics to ensure informed decisions. Two primary areas for analysis include:
Cost analysis
Estimating the total cost of ownership, including software licensing fees, implementation costs, and ongoing maintenance expenses, is crucial. Moreover, consider potential savings from increased efficiency and reduced downtime, which often offset initial investments.
Performance benchmarks
Organizations should measure key performance indicators such as:
- Reduction in equipment failures
- Increased asset availability
- Lower maintenance costs
- Enhanced employee productivity
These performance benchmarks equip decision-makers with the insights needed to select the most effective digital maintenance management solution for their needs.
Understanding Digital Maintenance Management
Digital maintenance management represents a pivotal shift in how organizations approach asset lifecycle strategies. It encompasses a holistic view of maintaining, monitoring, and optimizing assets through digital tools and technologies. The primary aim is to enhance asset performance while minimizing operational costs. By integrating digital solutions, businesses can transition from reactive maintenance tactics to more proactive practices, ultimately transforming their approach to asset management.
Definition and Overview
At its core, digital maintenance management refers to the use of technology to improve the efficiency and effectiveness of maintenance processes. It involves leveraging data analytics, Internet of Things (IoT) devices, and cloud-based systems to create a more streamlined approach to asset management. By utilizing these tools, organizations can gain insight into their assets’ conditions and performance, allowing for timely interventions that prevent costly failures. Understanding this definition is crucial, as it sets the stage for recognizing the profound impact that digital maintenance can have on operational success.
The Evolution of Maintenance Practices
Maintenance practices have evolved significantly over the years. In the past, many organizations relied heavily on reactive maintenance—fixing equipment only after it failed. This approach often resulted in extended downtimes and increased repair costs. However, with advancements in technology, maintenance strategies have transitioned toward predictive and preventive methods.
Today’s digital maintenance management enables continuous monitoring of asset conditions, forecasting potential failures based on data trends. This evolution is driven by the increasing availability of data and the tools to analyze it efficiently. Organizations that adapt to these changing practices not only reduce costs but also improve overall asset reliability and performance.
Key Components of Digital Maintenance Management
Several components are integral to implementing effective digital maintenance management strategies. These include:
- Data Analytics: The backbone of digital maintenance lies in analyzing data collected from assets. This analytics enables organizations to identify patterns and predict when maintenance should occur, which can significantly reduce unplanned downtimes.
- IoT Integration: The use of IoT devices facilitates real-time monitoring of equipment. These sensors can provide valuable insights into the operational status of assets, ensuring timely maintenance actions can be taken.
- Cloud Computing: Storing maintenance data in the cloud allows for easy access and sharing across departments. Cloud solutions support collaborative maintenance efforts and can enhance efficiency through centralized data management.
Digital maintenance management is not merely a trend; it is a strategic necessity in an increasingly competitive business landscape. By understanding its components and evolution, organizations can harness its full potential to optimize asset lifecycle strategies and drive operational excellence.
The Benefits of Digital Maintenance Management
Digital maintenance management plays a crucial role in today's asset management landscape. It enables organizations to leverage technology. This is not just a trend, but a necessity for maintaining competitive edge. By adopting digital maintenance strategies, businesses can witness various significant advantages. These benefits include increased asset longevity, cost savings through predictive maintenance, and enhanced operational efficiency. These aspects outline why digital maintenance management is essential for decision-makers.
Increased Asset Longevity
Increasing the lifespan of assets is one of the primary benefits of digital maintenance management. Advanced techniques can lead to substantial improvements in how assets are managed. With the right tools, organizations can monitor equipment in real-time. This monitoring allows for timely interventions before issues escalate.
For example, utilizing sensors can track metrics such as temperature and vibration. If anomalies are detected, alerts can be triggered to prompt staff to examine the equipment. Proactive maintenance reduces the likelihood of failures and extends asset life. Consequently, organizations can achieve more from their investments.
- Improved tracking of asset condition
- Proactive identification of issues
- Reduction in unexpected breakdowns
Cost Savings Through Predictive Maintenance
Predictive maintenance is a cornerstone of digital maintenance management. It revolutionizes how organizations address potential failures. Unlike traditional maintenance, which is often reactive, predictive methods use data analysis to forecast issues before they occur. This foresight allows for planned maintenance schedules rather than emergency repairs.
By investing in predictive maintenance tools, companies can significantly reduce operational costs. For instance, servicing an asset during routine maintenance is less costly than repairing it after a failure. Some key components include:
- Use of analytics to predict failures
- Scheduled maintenance based on data
- Optimization of maintenance resources
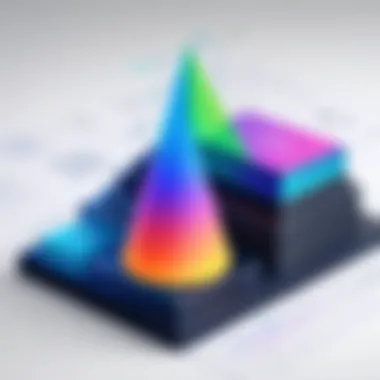
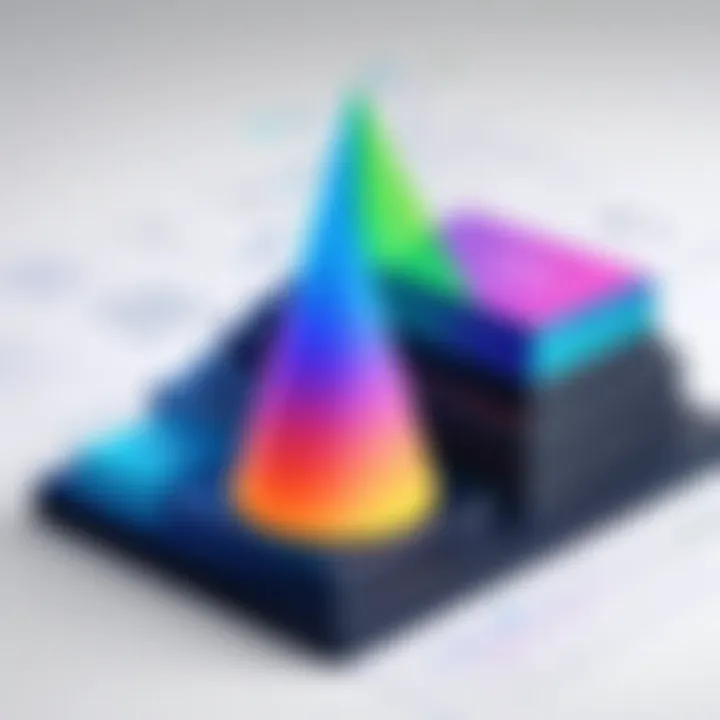
"Predictive maintenance can reduce maintenance costs by as much as 30% and increase equipment lifespan by up to 20%."
Enhanced Operational Efficiency
Digital maintenance management fosters operational efficiency in several ways. When systems and processes are streamlined, teams can focus more on their core responsibilities. With the integration of tools like IoT and data analytics, real-time insights can improve decision-making.
In addition, the automation of maintenance tasks minimizes human error and frees up staff for more strategic roles. An efficient maintenance program leads to:
- Faster response times to issues
- Better resource allocation
- Increased productivity across departments
By adopting digital methodologies, organizations can transform their asset management strategies. The benefits outlined here articulate the essential nature of digital maintenance management. As the field continues to evolve, staying informed about these advantages becomes increasingly significant for professionals aiming to optimize their operations.
Integrating Technology into Maintenance Processes
Integrating technology into maintenance processes is a critical aspect of digital maintenance management. It enables organizations to streamline operations, enhance productivity, and ultimately safeguard assets. The core of this integration lies in the adoption of modern tools and practices that facilitate data-driven decision-making. By leveraging technology, businesses can shift from reactive to proactive maintenance strategies, leading to better resource utilization and cost efficiencies.
Data Analytics and Maintenance Strategies
Data analytics plays an essential role in enhancing maintenance strategies. It allows businesses to collect, analyze, and interpret vast amounts of data from various sources. This information can reveal patterns and trends that were previously invisible. The insights garnered from data analytics help in predicting asset failures and optimizing maintenance schedules.
The benefits of integrating data analytics into maintenance strategies include:
- Improved fault detection: Organizations can quickly identify potential issues before they escalate into serious problems.
- Data-driven decisions: Decisions based on real-time data ensure better allocation of resources.
- Increased uptime: By minimizing unplanned downtimes, companies can maintain production efficiency.
Implementing data analytics requires a structured approach. Organizations need to first determine what data is critical for their operations and then establish systems to collect it effectively.
Role of IoT in Maintenance Management
The Internet of Things (IoT) has revolutionized maintenance management by connecting devices and systems through the internet. IoT sensors continuously monitor the health and performance of equipment, providing real-time data that can drive maintenance decisions.
Key advantages of incorporating IoT into maintenance processes include:
- Real-time monitoring: With IoT, businesses can monitor asset performance at all times, enabling quick response to any anomalies.
- Predictive maintenance: IoT data helps in predicting when an asset will require maintenance, thus reducing unexpected breakdowns.
- Enhanced collaboration: Remote access to live data improves communication between teams and stakeholders.
For optimal results, organizations should focus on integrating IoT solutions into existing systems. This can lead to a more unified maintenance strategy.
Utilizing Cloud Computing for Data Management
Cloud computing offers significant advantages for managing maintenance-related data. Storing information in the cloud provides flexibility, scalability, and accessibility that are not achievable with traditional on-premises solutions. Organizations can store vast amounts of data without the need for extensive physical infrastructure.
Benefits of cloud computing in digital maintenance management include:
- Centralized data access: Teams can access maintenance data from any location, enhancing collaboration.
- Cost-effective solutions: Businesses can save on hardware costs and only pay for the resources they use.
- Improved security measures: Cloud providers invest heavily in security protocols to protect data integrity.
When employing cloud computing, organizations must choose providers based on their security measures and data management capabilities.
"Integrating technology into maintenance processes is not just a trend; it’s a necessity for modern businesses aiming to enhance their operational efficiency and asset management strategies."
Implementing Digital Maintenance Solutions
Implementing digital maintenance solutions is essential for organizations aiming to optimize their maintenance operations. This process does not merely involve adopting new technologies; it requires a holistic approach to change management, workforce training, and process integration. When executed effectively, these solutions can greatly enhance asset performance, improve reliability, and reduce operational costs.
Identifying Suitable Technologies
When looking to implement digital maintenance solutions, the first step involves identifying technologies that align with organizational goals. This requires an analysis of current processes and pain points. For instance, are machines frequently breaking down? Is there a need for predictive maintenance? Understanding these factors will guide the selection of appropriate tools, such as maintenance management software or sensor technology for IoT integration.
Among the possible technologies are software platforms like IBM Maximo, SAP EAM, or Oracle EAM, which provide functionalities for tracking asset life cycles, scheduling maintenance tasks, and collecting data for analysis. Evaluating these platforms helps ensure that their features meet the specific needs of the business. Additionally, smaller businesses may benefit from cloud-based solutions that reduce upfront costs and require minimal IT infrastructure.
Developing a Strategic Implementation Plan
A strategic implementation plan is crucial for successful digital transformation. This plan should outline the steps necessary to integrate new technologies into existing maintenance processes. It begins with a needs assessment, where stakeholders list objectives and desired outcomes. Following this, a timeline should be created that defines key milestones and responsibilities.
It is important to prioritize communication throughout this phase. Engaging with all levels of staff can assist in identifying potential challenges and opportunities for improvement. Additionally, this collaboration promotes buy-in from all stakeholders, critical for the strategy's success. Finally, budget considerations must be factored into the plan, ensuring that there are available resources to support the initiative without excessive strain on the organization.
Training Staff for Digital Integration
Training staff is also a significant element in the implementation of digital maintenance solutions. New technologies often require new skills and knowledge, which can create resistance among employees. Therefore, investing in comprehensive training programs is vital. These programs should cover how to operate new systems, interpret data generated by these systems, and engage in proactive maintenance strategies.
Training should be tailored to various roles within the organization. For example, maintenance workers need hands-on training with new software and equipment, while management may require insights into data analytics for decision-making purposes. Furthermore, continuous education should be encouraged to keep staff updated on technological advancements.
"Successful digital maintenance solutions rely heavily on effective training and staff engagement. Without these, even the most advanced technology can fall short of expectations."
Establishing Maintenance Protocols
Establishing maintenance protocols is integral to the success of digital maintenance management. These protocols guide organizations in adopting systematic procedures that enhance asset reliability and performance. By developing well-defined maintenance strategies, companies can realize significant cost savings while optimizing their operational efficiency.
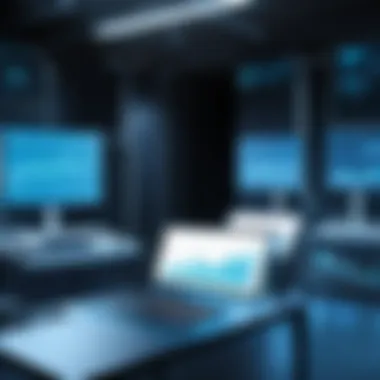
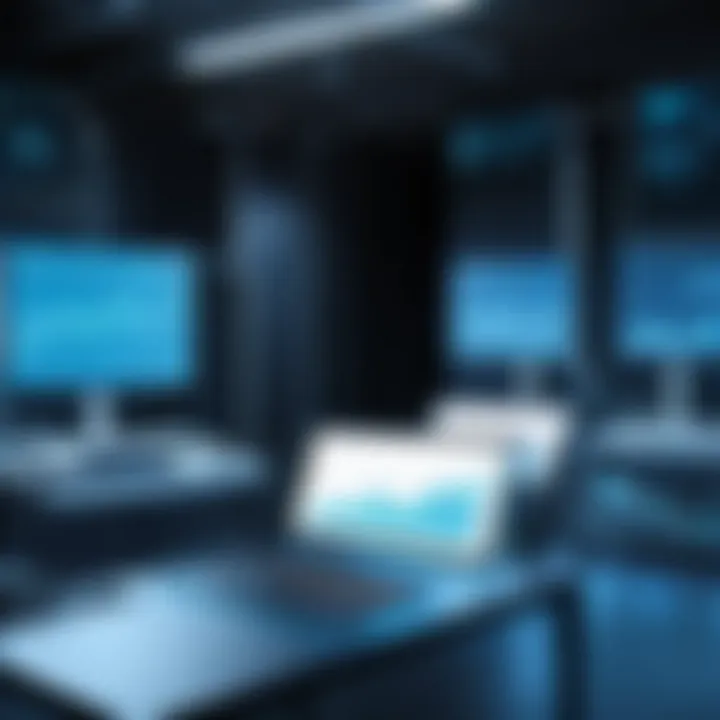
The key to effective maintenance protocols lies in their standardization, which ensures consistency across all processes involved. This standardization fosters an environment where all team members understand their roles and responsibilities, eliminating uncertainties that often lead to ineffective maintenance practices.
Standardization of Maintenance Procedures
Standardizing maintenance procedures means unifying the practices used for asset management. This includes setting uniform guidelines for routine inspections, repairs, and replacements. When procedures are consistent, it reduces variability, which can otherwise lead to errors and inefficiencies.
By implementing standardized procedures, organizations can achieve several advantages:
- Improved Coordination: All staff members follow the same guidelines. This ensures better teamwork and communication.
- Training Simplification: New employees can be trained quicker when methods are standardized. They can learn a set process without variation.
- Easier Compliance: Adhering to industry regulations becomes simpler. Standardized procedures often align with compliance requirements.
To motivate adherence, tools such as checklists and digital maintenance management systems can be employed. These tools can enable real-time reporting and provide reminders to follow established protocols.
Documentation and Record Keeping
Documentation and record keeping are critical aspects of maintenance protocols. Proper records help maintain a comprehensive history of maintenance activities. This historical data is invaluable for decision-making, helping organizations identify recurring issues and trends.
The following points underscore the importance of effective documentation:
- Asset Performance Tracking: Accurate records help in tracking the performance of each asset over time. This can highlight patterns indicative of impending failures.
- Regulatory Compliance: Many industries require specific documentation for maintenance activities. Keeping thorough records ensures compliance with these regulations.
- Knowledge Sharing: Capturing maintenance activities in documents fosters a culture of knowledge sharing. Team members can refer to past experiences to inform future maintenance actions.
In digital maintenance management, tools like cloud storage solutions or dedicated software can streamline the documentation process. These systems allow for easy access to records from various locations, improving collaboration and decision-making.
Performance Metrics for Maintenance Activities
Establishing performance metrics for maintenance activities is another vital step. These metrics provide quantifiable insights into how well maintenance protocols are being followed and their effectiveness.
Common performance metrics include:
- Mean Time Between Failures (MTBF): This measures the average time an asset operates before it fails. A higher MTBF indicates better reliability.
- Maintenance Cost per Asset: Analyzing costs associated with maintenance helps organizations manage expenditures and identify cost-saving opportunities.
- Work Order Completion Rates: Monitoring how quickly work orders are addressed can provide insights into operational efficiency.
By closely monitoring these metrics, businesses can identify areas for improvement. Continuous tracking allows organizations to refine their maintenance processes, ultimately leading to improved asset performance and reduced downtime.
Establishing comprehensive maintenance protocols is not just about implementing new systems. It's about creating a cultural shift towards proactive asset management that employs data analysis, standard practices, and effective communication among teams.
"Standardization and documentation in maintenance can improve communication and efficiency significantly, especially in complex organizations."
Ultimately, the pursuit of effective maintenance protocols is a pursuit of enhanced asset reliability and overall business success.
The Role of Collaboration in Maintenance Management
Collaboration plays a critical role in digital maintenance management. Effective maintenance strategies are not achieved solely through technology; they also rely heavily on people and processes. Building an environment where cross-departmental teams work together can lead to improved communication, better decision-making, and ultimately, enhanced asset management.
Effective collaboration ensures that all stakeholders understand their roles and responsibilities. This promotes a culture of transparency and accountability. It becomes easier to identify problems early when teams communicate well. This early identification minimizes downtime and maintenance costs, which are crucial to any organization’s bottom line.
One focus in establishing collaboration should be fostering relationships among various departments. Maintenance, production, and IT teams must work hand-in-hand. Each department offers unique perspectives and expertise. Combining these angles creates a more robust maintenance strategy. Having regular meetings and joint projects can help achieve this integration. Furthermore, engaging frontline staff in decision-making can yield compelling insights that top management may overlook.
"Effective communication is the cornerstone of successful digital maintenance management."
Cross-Departmental Coordination
Cross-departmental coordination is essential for maximizing the advantages of digital maintenance management. Different departments contribute varied knowledge that enhances the overall maintenance effort. For instance, the IT department can implement advanced technologies, while the maintenance team understands the practical aspects of tools and machines.
Coordination can help align goals across departments. For example, if production goals are set without considering maintenance schedules, unexpected downtime may occur. By working together, departments can create a balanced approach where production targets account for maintenance needs.
Communication platforms that allow for real-time updates can aid in coordination efforts. Systems like Slack or Microsoft Teams facilitate instant messaging and file-sharing. This immediacy can lead to quicker problem-solving and reduces the chance of miscommunication. Moreover, establishing a joint calendar that notes important maintenance dates and production schedules encourages synchronization and mutual respect among departments.
External Partnerships and Vendor Management
External partnerships and vendor management are significant aspects of collaboration in digital maintenance management. Collaborating with vendors allows organizations to leverage expert knowledge and the latest technologies. Through these partnerships, internal teams can gain insights into best practices that enhance maintenance processes.
Finding the right vendors is vital. An ideal vendor should not only supply quality products but also engage in proactive support. Regular check-ins and updates from vendors can assist maintenance teams in keeping up with the latest industry trends. In some cases, vendors may offer training programs to help staff understand new tools better.
Furthermore, clear communication between internal teams and external partners can minimize misunderstandings. Setting expectations and establishing service-level agreements (SLAs) is necessary to ensure a positive working relationship. This way, prompt service or product replacements become a standard part of the partnership.
In summary, collaboration across departments and with external partners is essential for effective digital maintenance management. By building strong relationships and maintaining open lines of communication, organizations can realize the full potential of their maintenance initiatives.
Measuring Success in Digital Maintenance Management
In the realm of Digital Maintenance Management, understanding how to measure success is crucial. This section discusses the methodologies and approaches that can be employed to gauge the effectiveness of digital maintenance initiatives. By systematically tracking performance, organizations can ensure that their maintenance strategies are not only relevant but also effective in achieving desired outcomes.
Metrics that reflect real improvements can guide a company's asset lifecycle, enabling more informed decision-making and robust resource allocation. By knowing what to measure and how to interpret the results, businesses can pivot strategies as needed, maximizing the benefits of their digital investments.
Establishing Key Performance Indicators
Key Performance Indicators, or KPIs, serve as a foundation for measuring success in digital maintenance management. Establishing relevant KPIs enables organizations to assess the efficiency of their maintenance processes. These indicators should reflect both the operational goals and organizational objectives.
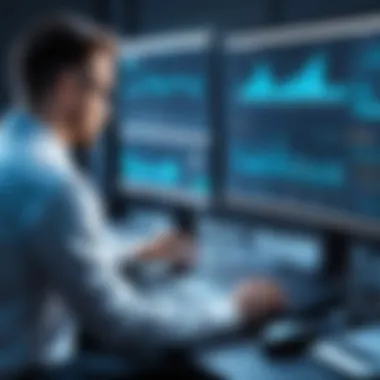
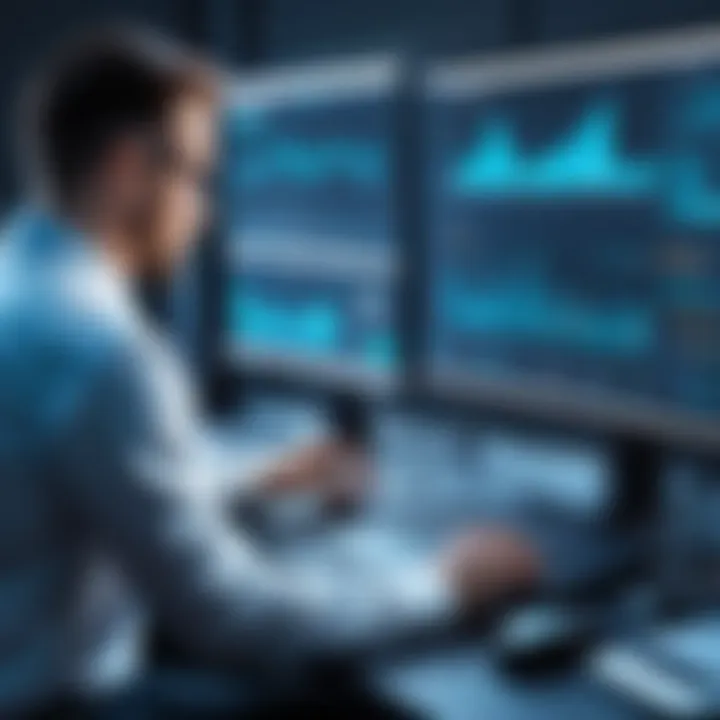
Some essential KPIs to consider include:
- Mean Time Between Failures (MTBF): This measures the average time between equipment failures, giving insight into reliability.
- Mean Time To Repair (MTTR): This measures the average time taken to repair equipment and restore it to operational status.
- Overall Equipment Effectiveness (OEE): This comprehensive measure takes into account the performance, availability, and quality of equipment.
- Cost Per Maintenance Activity: This assesses the expenses incurred for each maintenance task, allowing for a clearer understanding of cost implications.
By choosing KPIs that align with business objectives, organizations can create a clear picture of maintenance performance and areas needing improvement.
These KPIs must be regularly reviewed and adjusted to reflect the company's evolving priorities. Additionally, it is important to involve all stakeholders in defining these benchmarks to ensure relevance across departments.
Analyzing Maintenance Data for Continuous Improvement
The analysis of maintenance data plays a pivotal role in fostering a culture of continuous improvement. Once relevant KPIs are established, the next step involves collecting and analyzing data over time. This process reveals patterns and trends that can inform future maintenance decisions. Digital tools facilitate this analysis by providing real-time data, ensuring swift responses to emerging issues.
Some key points to consider when analyzing maintenance data:
- Regular Data Review: Set a schedule for reviewing maintenance data to quickly identify anomalies or trends.
- Benchmarking: Compare your data against industry standards to determine how well your maintenance processes perform relative to competitors.
- Feedback Loops: Encourage team members to provide feedback on processes, identifying pain points or bottlenecks that can be addressed.
- Predictive Analysis: Employ predictive analytics to forecast potential equipment failures. By analyzing historical data, organizations can anticipate maintenance needs and avoid costly downtimes.
This analytical approach not only aids in achieving immediate benefits but also drives long-term enhancements in maintenance strategies. Continuous improvement is vital for staying ahead in an ever-evolving technological landscape.
In summary, measuring success in digital maintenance management hinges on establishing relevant KPIs and employing ongoing data analysis. This dual approach empowers organizations to refine their maintenance practices, ultimately enhancing asset performance and achieving operational excellence.
Challenges and Considerations in Digital Maintenance Management
Digital maintenance management holds promise for optimizing asset lifecycle strategies. However, the journey to fully realizing its benefits is riddled with challenges. Addressing these challenges is crucial not only for successful implementation but also for sustaining long-term growth and agility in operations. Understanding the dynamics of these challenges can streamline decision-making and foster a favorable environment for digital transformation.
Overcoming Resistance to Change
Resistance to change often emerges as a significant barrier in the adoption of digital maintenance management practices. Employees may feel threatened by new technologies, fearing displacement or the need for new skills they haven't acquired yet. To navigate this issue, it is important to establish a culture that embraces change. A few strategies can be employed to overcome this resistance:
- Education and Training: Implement comprehensive training programs that empower employees with the skills needed to operate new tools and systems.
- Involvement in Decision-Making: Engage employees early on in the process. When they feel that their opinions matter, they are more likely to accept changes.
- Demonstration of Benefits: Show how digital tools can make their work easier and more efficient. Use data to illustrate potential time savings and improved performance metrics.
By addressing resistance, organizations can facilitate smoother transitions and integration of digital maintenance systems.
Addressing Data Privacy and Security Issues
Data privacy and security concerns are paramount when implementing digital maintenance management solutions. These technologies often require the use and sharing of sensitive information. Failure to protect this data can lead to legal consequences and damage to the organization’s reputation. Organizations need to consider several points:
- Compliance with Regulations: Adhere to applicable laws and standards surrounding data protection. Regulations such as GDPR emphasize the importance of data privacy.
- Robust Security Measures: Implement advanced security protocols, including encryption and regular audits, to safeguard data.
- Employee Training on Cybersecurity: Ensure that employees understand their role in maintaining data security. Regular training sessions can keep them informed about best practices.
By prioritizing data privacy and security, organizations can foster trust among stakeholders and minimize risks associated with digital transformation.
“Embracing digital maintenance management without addressing challenges can lead to significant setbacks. - Anonymous
In summary, navigating the challenges of resistance to change and data privacy is vital for harnessing the potential of digital maintenance management. These considerations are essential for creating an environment conducive to innovation and efficiency.
Future Trends in Digital Maintenance Management
The dynamics of maintenance management are changing rapidly due to technological advancements. Future trends will significantly impact how organizations manage their assets, ultimately improving their lifespan and efficiency. Recognizing these trends is critical for decision-makers, as adopting cutting-edge practices can lead to substantial benefits. Key elements such as artificial intelligence and the integration of emerging technologies will play pivotal roles in evolving digital maintenance management strategies.
Impact of Artificial Intelligence
Artificial intelligence (AI) is reshaping various industries, including maintenance management. Its implementation provides unique opportunities to enhance the reliability and efficacy of maintenance processes. AI can analyze large datasets, enabling predictive maintenance practices that foresee equipment failures before they occur. This transition from reactive to proactive strategies reduces downtime, minimizes repair costs, and improves operational performance.
In addition, AI-powered tools can optimize resource allocation by predicting maintenance schedules. This leads to improved planning and management of assets, resulting in a seamless workflow. It is crucial for organizations to invest in AI solutions to stay competitive. However, it also requires a shift in the existing employee skill set. Training staff to effectively utilize AI tools is a significant consideration when implementing these technologies.
Emerging Technologies and Their Adoption
The emergence of new technologies continues to redefine how maintenance is conducted. Internet of Things (IoT), machine learning, and advanced analytics are just a few examples of innovations reshaping the landscape.
IoT Integration
The integration of IoT devices allows for real-time monitoring of equipment. Sensors can provide valuable data about machine performance, thus facilitating immediate action when issues arise. This not only improves fault detection but also helps in enhancing equipment uptime.
Machine Learning Implementation
Machine learning algorithms can analyze past maintenance data to identify patterns and inform future strategies. Utilizing this technology assists in refining the maintenance workflow. By continuously learning from previous cycles, businesses can improve their overall efficiency and reduce operational costs.
Organizations looking to adopt these technologies should consider key factors such as infrastructure readiness and alignment with organizational goals. Collaborative efforts across departments are essential to ensure a smooth transition into these innovative practices.
Ending and Strategic Recommendations
In today's rapidly evolving landscape, understanding and adopting digital maintenance management is more crucial than ever. This discipline not only streamlines asset management but also fosters a culture of efficiency within organizations. The key takeaway from this article emphasizes how digital tools can significantly transform traditional maintenance strategies into proactive frameworks.
Recap of Key Points
- Digital Transformation: The shift from conventional maintenance practices to digital frameworks enhances asset reliability and reduces operational costs.
- Integration of Technologies: Leveraging data analytics, IoT, and cloud computing plays a pivotal role in optimizing maintenance processes.
- Employee Training: Ensuring that staff are equipped with the necessary skills to utilize digital tools minimizes resistance to change and enhances overall performance.
- Standardization and Protocols: Establishing clear maintenance procedures and documentation practices leads to better outcomes in performance measurement.
- Collaboration across Departments: Engaging different teams boosts communication and increases efficiency in handling maintenance tasks.
- Future Readiness: Staying ahead with emerging technologies and trends, such as artificial intelligence, positions organizations for long-term success in digital maintenance management.
Steps for Effective Implementation
- Assess Current Practices: Conduct a thorough review of existing maintenance strategies. Identify inefficiencies and areas for improvement.
- Define Clear Objectives: Establish what you seek to achieve with digital maintenance management. Objectives could include cost reduction, increased uptime, or enhanced asset performance.
- Select Appropriate Technologies: Choose technologies that align with your objectives. Consider systems like SAP, IBM Maximo, or other suitable solutions that meet your needs.
- Engage Stakeholders: Collaborate with all departments. Encourage input and prepare them for the coming changes.
- Develop a Training Program: Create a detailed plan for training employees. Ensure they can use new tools and understand new processes.
- Implement Gradually: Take a phased approach to roll out digital maintenance solutions. Monitor progress and adapt as needed based on feedback and performance data.
- Measure and Adapt: After implementation, continuously monitor performance metrics. Use this data to make adjustments that drive further improvements.
Organizations that integrate digital maintenance management are better positioned to adapt to future challenges and seize opportunities in asset management.
By following these strategic recommendations, organizations can not only enhance their operational efficiency but also establish a solid foundation for future advancements in digital maintenance management.