Comprehensive Analysis of Warehouse and Inventory Management Systems
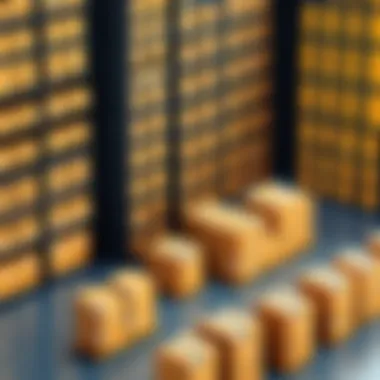
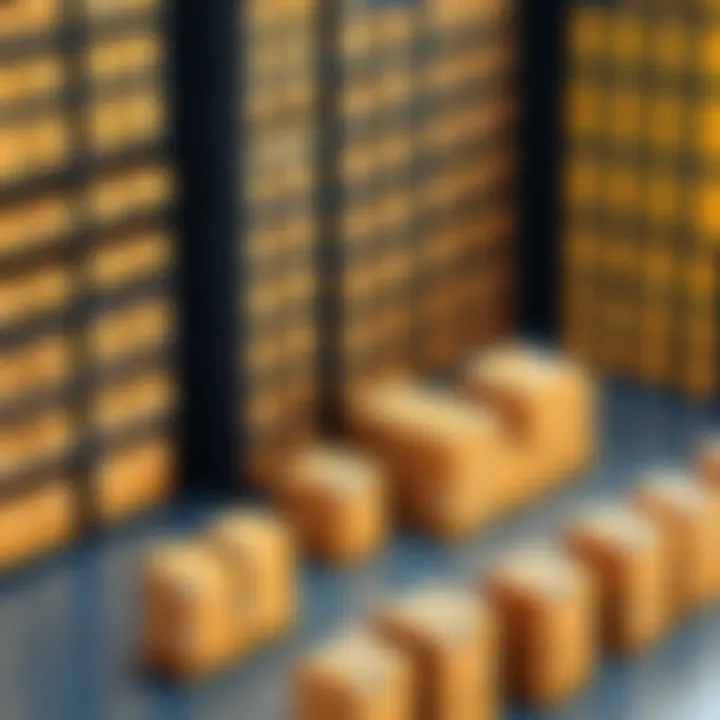
Intro
In today's competitive landscape, effective warehouse and inventory management is crucial for businesses aiming to operate efficiently. The systems utilized in these areas are not mere tools; they are vital components that can significantly influence operational success. As companies strive to meet increasing customer expectations, understanding these systems becomes paramount. They enable organizations to handle stock levels, minimize costs, and ensure timely deliveries.
Warehouse and inventory management systems encompass various technologies and practices designed to oversee the flow of goods from suppliers to warehouses and eventually to customers. This includes everything from tracking inventory levels to managing order fulfillment and anticipating stock needs.
Key Software Features
Selecting the right software for warehouse and inventory management is crucial. Effective systems must possess certain essential functionalities to ensure smooth operations.
Essential functionalities
- Real-time tracking: The ability to monitor inventory movement continually, reducing discrepancies and increasing accuracy.
- Inventory optimization: Tools that help in maintaining ideal stock levels, avoiding both overstocking and stockouts.
- Order management: Efficient processes for managing sales orders, returns, and fulfillment.
- Reporting and analytics: Features that provide insights into inventory trends, helping in making informed decisions.
Advanced capabilities
As businesses grow, their needs may evolve. Advanced capabilities in warehouse and inventory management software can provide additional value:
- Integration with other systems: Seamless connectivity with ERP, CRM, and e-commerce platforms ensures data consistency across departments.
- Automation: Features that automate repetitive tasks, increasing productivity and reducing human error.
- Cloud-based solutions: Accessibility from anywhere and scalability as the business expands.
Comparison Metrics
When choosing between different warehouse and inventory management systems, it's critical to use appropriate metrics for comparison. This can aid in identifying the most suitable software for specific business needs.
Cost analysis
Evaluating software involves understanding the complete cost structure. This includes initial costs, subscription fees, training expenses, and ongoing maintenance. Businesses should also consider potential savings from improved efficiency and accuracy.
Performance benchmarks
Establishing performance metrics like speed of inventory turnover and accuracy rates help gauge a system's effectiveness. A good system should improve these metrics over time, thus enhancing overall operations.
"An effective warehouse management system is a backbone for operational efficiency."
Understanding Warehouse Management Systems
In an increasingly competitive business landscape, the importance of understanding warehouse management systems cannot be overstated. These systems play a crucial role in enhancing operational efficiency and accuracy in inventory handling. Warehouse management systems (WMS) are designed to optimize warehouse functionality by managing the flow of goods within and outside the warehouse. This encompasses everything from inventory tracking to order fulfillment, making it essential for businesses seeking to improve their supply chain processes.
Definition and Purpose
A warehouse management system is a software solution that streamlines and automates the warehousing process. Its primary purpose is to manage inventory levels, track stock movements, and enhance overall warehouse productivity. This system provides real-time visibility of inventory, enabling companies to make informed decisions regarding stock levels and order management.
The main aims of a WMS can be summarized as follows:
- Enhancing Accuracy: Accurate inventory levels help reduce errors in order fulfillment and minimize stockouts.
- Improving Efficiency: Automation of manual processes leads to faster throughput and reduced labor costs.
- Providing Visibility: Real-time tracking of goods ensures timely information for better decision-making.
Understanding these aspects is critical for decision-makers, IT professionals, and entrepreneurs looking to implement or improve their warehouse management strategies.
Key Components
A comprehensive warehouse management system consists of several key components that contribute to its functionality. These components work in tandem to create a system that not only meets but exceeds operational needs of a warehouse.
- Inventory Management: This allows businesses to track inventory from the moment it arrives until it is dispatched. Effective inventory management helps in optimizing stock levels.
- Order Management: WMS capabilities include order processing and tracking, ensuring that orders are filled accurately and delivered on time.
- Shipping and Receiving: Efficient management of incoming and outgoing shipments is critical. This includes scheduling, tracking, and documentation which minimises delays.
- Warehouse Layout and Design: A well-organized warehouse layout improves pick and pack processes. A good WMS incorporates design aspects for optimal use of space.
- Reporting and Analytics: Providing insights on performance metrics, inventory turnover rates, and labor productivity allows businesses to identify areas for improvement.
This understanding of key components offers substantial insights for organizations aiming to derive maximum benefits from a warehouse management system.
Inventory Management Fundamentals
Understanding inventory management is essential in enhancing operational efficiency and satisfaction in the business environment. Inventory management refers to the process of ordering, storing, and utilizing the inventory a company holds, which may include raw materials, work-in-progress items, and finished goods. Effective management of inventory ensures that the right products are in the right place at the right time, mitigating excess costs while maximizing sales opportunities.
Definition of Inventory Management
Inventory management is the systematic approach to sourcing, storing, and selling inventory, both raw materials and finished goods. It involves maintaining an optimal amount of stock to not only meet customer demand but also manage financial resources effectively. The primary goal of inventory management is to ensure that the company can fulfill customer orders without delay while reducing holding and ordering costs. By accurately tracking inventory levels, businesses can prevent stockouts, reduce wastage, and improve overall productivity.
Types of Inventory
Businesses engage with various types of inventory based on their operational needs.
- Raw Materials: These are the fundamental components that are processed to create finished goods.
- Work-in-Progress (WIP): Items that are in the production process but not yet completed.
- Finished Goods: These are products ready for sale to end customers.
- Maintenance, Repair, and Operations (MRO): Supplies that are used in production but not part of the final product.
Understanding each type of inventory allows businesses to tailor their management strategies effectively. For example, raw materials require different handling compared to finished goods. As a result, businesses can optimize storage, reduce costs, and enhance customer satisfaction.
In summary, mastering inventory management fundamentals is vital for organizations aiming to thrive in today's competitive landscape. Integrating solid inventory practices leads to better resource management, streamlined operations, and improved customer relationships.
Importance of Warehouse and Inventory Management
Warehouse and inventory management is crucial in today's business environment. It directly affects the operational effectiveness and financial performance of a company. The management of these systems ensures that products are stored, organized, and tracked efficiently, leading to better service levels, reduced waste, and overall profitability. The use of effective warehouse and inventory management practices can help businesses respond more swiftly to demand fluctuations and market changes.
In an era where consumer expectations continue to escalate, an optimal management system becomes a competitive advantage. Firms with strong operational protocols are able to minimize delays, enhance fulfillment speed, and elevate satisfaction. In essence, proper management in these areas signifies not just efficiency, but also is pivotal for long-term sustainability in business operations.
Operational Efficiency
Operational efficiency centers around maximizing resource use while minimizing waste. A robust warehouse management system can lead to significant improvements in how goods are handled. Automation tools streamline processes, facilitating faster inventory checks and reducing manual errors. When operations run smoothly, companies can process orders quickly and maintain a steady flow of goods, which is essential in maintaining customer satisfaction.
Employing barcodes or RFID technologies enhances tracking and facilitates real-time updates on inventory levels. This level of accuracy helps eliminate issues like stockouts or overstocking, further leading to enhanced operational harmony.
In summary, improved operational efficiency results from clear visibility of inventory, optimized storage solutions, and the ability to make fast adjustments to inventory levels based on real-time data.
Cost Management
Cost management in warehouse and inventory management involves the careful monitoring of expenses, directly related to the storage and handling of stock. A comprehensive approach to this facet ensures that companies can effectively allocate resources and eliminate unnecessary costs.
Costs can accumulate from various sources, including:
- Storage Costs: Including space, utilities, and maintenance.
- Labor Costs: Related to the workforce involved in handling, managing, and processing inventory.
- Shrinkage: Loss of inventory due to theft or damage.
By implementing effective inventory systems, businesses can optimize their inventory turnover rates, reducing holding costs significantly. Additionally, the integration of software solutions allows for more informed forecasting, ensuring that stock levels align with market demand, which minimizes dead stock.
Investing in the right warehouse practices generates a favorable return by cutting wasted resources and enhancing profitability. Ultimately, effective cost management through sound inventory practices can transform how businesses perceive their operational costs.
Challenges in Warehouse and Inventory Management
In the dynamic landscape of warehouse and inventory management, organizations face various challenges that can hinder operational efficiency and profitability. Understanding these challenges is fundamental for creating effective strategies that enhance inventory control, reduce costs, and optimize warehouse processes. Properly addressing these challenges can lead to significant competitive advantages, allowing businesses to adapt to the ever-changing demands of the market.
Data Accuracy Issues
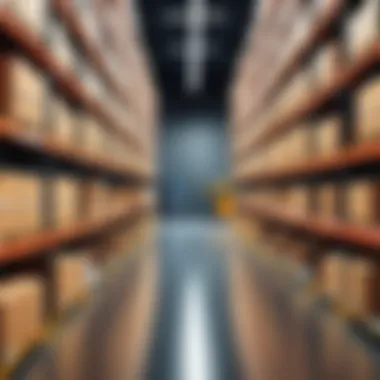
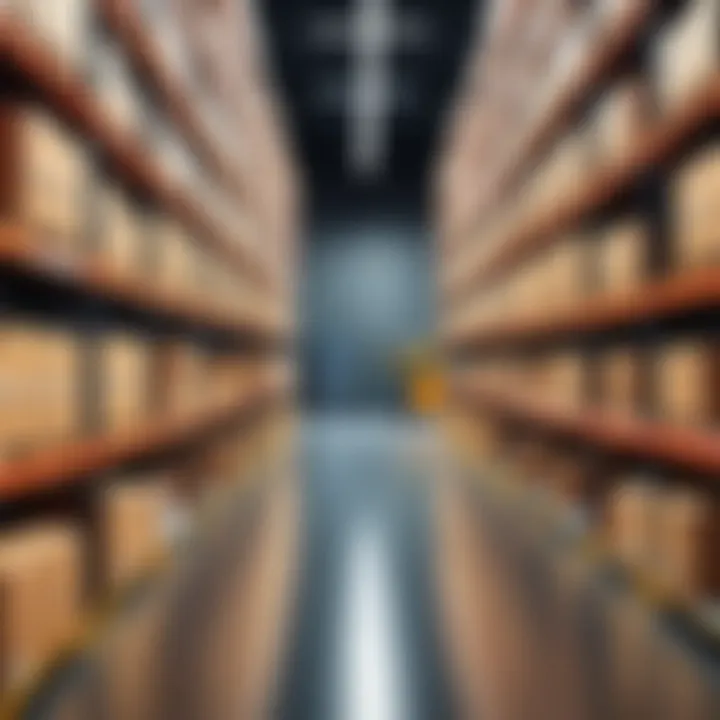
Data accuracy is one of the most critical challenges in warehouse and inventory management. Inaccurate data can lead to discrepancies between what is recorded in the system and what is physically available in the warehouse. This situation can arise from several factors, including human error during data entry, outdated information not being updated in real-time, or lapses in inventory counting processes.
The consequences of data accuracy issues are far-reaching. They can contribute to stockouts, where key items are unavailable for sale, and overstock situations, where excess inventory ties up valuable resources. Ensuring high levels of data accuracy is essential to avoid these pitfalls. Organizations can implement regular audit processes and automated scanning technologies to maximize accuracy and maintain reliable inventory records.
Additionally, adopting advanced inventory management systems that emphasize real-time data integration can mitigate accuracy-related challenges. These systems help synchronize information across various channels, reducing the likelihood of errors. By nurturing a culture of accountability and continuous improvement in data management, businesses can enhance their inventory practices significantly.
Space Utilization
Another significant challenge relates to space utilization within warehouses. As businesses expand, they often face the dilemma of maximizing available space while still meeting operational needs. Inefficient space utilization can lead to overcrowding, which not only hampers productivity but also increases the risk of damage to inventory and safety hazards for employees.
Properly analyzing space usage is paramount for alleviating this challenge. Techniques such as slotting optimization can help determine the best locations for items, based on their picking frequency and volume. Moreover, organizations can utilize vertical storage solutions to make the most of vertical space, contributing to more effective inventory management.
In combating space utilization issues, it is beneficial to assess the flow of operations routinely. This includes evaluating the movement of goods in and out of storage. By understanding the patterns in inventory flow, companies can adjust layouts, shelving, and storage practices to foster a more efficient environment. Improving efficiency in warehouse space utilization aligns closely with overall better operational practices, thus enabling organizations to handle higher volumes with the same footprint.
Technology Integration in Warehousing
Technology integration plays a crucial role in the evolution of warehouse and inventory management systems. Effective integration of technology can lead to enhanced operational efficiency, improved data accuracy, and better decision-making capabilities. Businesses are increasingly turning towards modern solutions to optimize their warehousing processes and accommodate the demands of dynamic market environments. The ability to utilize advanced technologies is not merely a competitive edge; it has become a necessity.
Key elements of technology integration include automation, robotics, data analytics, and cloud-based systems. By leveraging these technologies, warehouses can streamline operations, minimize human error, and achieve greater flexibility in their inventory management practices. This section will elaborate on the two primary aspects of technology integration: the role of automation and the implications of adopting cloud-based systems.
Role of Automation
Automation in warehousing involves the use of technology to execute tasks with minimal human intervention. Tasks such as inventory tracking, picking, and sorting can be automated, leading to several benefits. First, automation significantly reduces the time required to process orders. Faster order fulfillment translates to better customer satisfaction and retention.
Second, automating repetitive tasks lowers labor costs and minimizes human errors. Humans are prone to making mistakes in manual processes, but automated systems can work consistently with high precision. It is also important to consider the upfront investment for automation technology. While the initial costs can be high, the long-term savings and efficiency gains often justify the expenditure.
Some commonly used automated technologies in warehouses include:
- Automated guided vehicles (AGVs)
- Robotic picking systems
- Conveyor systems
- Automated inventory tracking systems
By merging automation with smart inventory management systems, companies can achieve real-time visibility over their stock levels and operations.
Cloud-Based Systems
Cloud-based systems represent another significant advancement in warehouse management technology. These systems are hosted on remote servers and enable organizations to access their data from anywhere with an internet connection. The shift towards cloud-based solutions offers distinct advantages, making them essential for modern warehousing.
One primary benefit of cloud-based systems is the scalability they provide. As businesses grow or as demand fluctuates, cloud services can adjust resources accordingly without requiring substantial infrastructure changes. This flexibility is particularly useful in a volatile market where inventory demands can change rapidly.
Moreover, cloud-based systems enhance collaboration among different departments and stakeholders. Teams can access real-time data, leading to more informed decision-making and increased operational transparency.
Another aspect to consider is the cost-effectiveness of cloud technology. Organizations can often reduce their IT expenses significantly by adopting cloud services, as they eliminate the need for on-premise hardware and maintenance. However, data security must also be a key consideration when integrating cloud solutions into warehouse management systems.
"The benefits of technology integration far outweigh the risks, as long as proper precautions and strategic planning are employed."
In summary, technology integration in warehousing transforms the way inventory is managed and fulfills orders. Automation and cloud-based solutions emerge as pivotal components that drive efficiency, productivity, and enhanced responsiveness to market changes.
Software Solutions for Inventory Management
In today's fast-paced business environment, effective inventory management is vital. Software solutions for inventory management play a key role in optimizing operations. They provide tools to track stock levels, manage orders, and forecast demand. Using these systems can lead to significant improvements in efficiency and accuracy.
These solutions automate many tasks that traditionally required a large amount of manual effort. This automation reduces human error and increases the speed of processing. Furthermore, integration with other business systems improves data flow and visibility. When chosen correctly, these tools can enhance decision-making and reduce costs, ultimately impacting the bottom line positively.
Comparative Analysis of Leading Tools
Several software tools stand out in the market for inventory management. Notable options include Oracle NetSuite, SAP Business One, and Fishbowl Inventory. Each offers different functionalities suited for unique business needs.
- Oracle NetSuite: This solution is cloud-based and provides real-time inventory tracking and management. Its flexibility allows businesses to tailor the software according to their requirements.
- SAP Business One: This tool provides a complete view of inventory and is integrated with financial data. It is ideal for businesses looking for comprehensive enterprise resource planning.
- Fishbowl Inventory: Known for its ease of use, Fishbowl focuses on manufacturing and warehouse management. It helps streamline operations with features that allow users to manage parts and products throughout the supply chain.
"Before investing in any inventory tool, it is essential to understand the specific needs of your business."
Evaluation Criteria for Selection
Selecting the right software tool requires careful consideration. Here are key factors to keep in mind:
- Functionality: Ensure the tool meets all necessary inventory management tasks, such as order tracking, stock level monitoring, and reporting.
- Scalability: The software should accommodate future growth, whether it involves increasing inventory or expanding into new markets.
- Ease of Use: A user-friendly interface is critical for effective utilization. A complex system may hinder user adoption and productivity.
- Integration Capabilities: Check if the software can integrate with other systems like ERP, accounting, or e-commerce platforms.
- Cost: Consider long-term costs, including subscription fees, maintenance, and any potential hidden costs associated with implementation or training.
By using these criteria, decision-makers can make a more informed choice about which inventory management software aligns best with their operational goals.
Data Analytics in Inventory Management
Data analytics plays a crucial role in the domain of inventory management. As businesses increasingly rely on data-driven strategies, the synthesis of analytics within inventory processes becomes fundamental. Organizations must leverage data analytics to enhance efficiency, reduce costs, and adapt to market fluctuations. By meticulously analyzing historical data, companies can identify patterns and trends that inform inventory decisions, leading to improved service levels and profitability.
Importance of Data-Driven Decisions
Incorporating data analytics into inventory management empowers decision-makers to make informed choices rather than relying on intuition or outdated practices. Data-driven decisions allow organizations to:
- Optimize stock levels: By analyzing sales trends, businesses can adjust inventory levels to meet customer demand without overstocking or understocking.
- Identify slow-moving items: Regular analysis can pinpoint items that are not selling well, allowing managers to take necessary actions, such as discounting or promotional efforts.
- Enhance supplier management: Keeping track of supplier performance through data can help companies negotiate better terms and manage lead times effectively.
- Forecast demand accurately: By utilizing historical data, it becomes possible to predict future demand with much higher precision.
"Data-driven decision-making transforms the way organizations view and manage inventory, giving them a competitive edge in today's fast-paced market."
Forecasting Trends
Accurate demand forecasting is integral to effective inventory management. By leveraging data analytics, retailers can anticipate future sales based on various factors, including seasonality, market trends, and consumer behavior. Forecasting trends enables inventory managers to prepare adequately, thus minimizing the risk of running out of stock or carrying excess inventory. Some key elements include:
- Utilization of predictive analytics tools: These tools assess historical data and apply algorithms to forecast future sales, offering significant insights into upcoming trends.
- Incorporation of external factors: External influences such as economic conditions, promotions, or shifts in consumer preferences must be accounted for when forecasting. This brings a holistic view that further refines predictions.
- Continuous adjustment and monitoring: Incorporating regular reviews of forecasting models ensures they remain relevant and reflect current market realities. Adjusting forecasts based on new data enhances accuracy and responsiveness.
As data analytics evolves, its application in inventory management continues to become more sophisticated. By making data-driven decisions and improving the forecasting process, organizations can navigate challenges more effectively and bolster their operational efficiency.
Best Practices for Effective Inventory Control
Effective inventory control is essential for the operational success of any business. It ensures that the right products are available at the right time, which directly impacts customer satisfaction and profitability. By adopting best practices, organizations can minimize waste, reduce costs, and enhance their overall productivity. This section will discuss two critical best practices: Cycle Counting and the implementation of FIFO (First In, First Out) and LIFO (Last In, First Out) approaches.
Cycle Counting
Cycle counting is a technique used to audit inventory levels on an ongoing basis. Instead of performing a full inventory count at one time, businesses can count a subset of items at specified intervals throughout the year. This method has several key benefits:
- Increased Accuracy: Regular cycle counts help identify discrepancies in inventory records, allowing for corrections to be made promptly.
- Reduced Disruption: Frequent counts mean that full shutdowns for physical inventory are not necessary, which keeps operations running smoothly.
- Flexible Scheduling: Companies can prioritize counting high-value or fast-moving items more frequently, based on their specific needs.
Implementing a cycle counting routine requires careful planning. Companies must decide which items to count, how often to count them, and ensure that staff receive proper training. It is important to have reliable documentation and a clear process to address any issues that may arise during the counting process.
Implementing FIFO and LIFO Approaches
The management of inventory can significantly benefit from the application of the FIFO and LIFO methods. These approaches control inventory turnover and accounting practices effectively.
FIFO (First In, First Out)
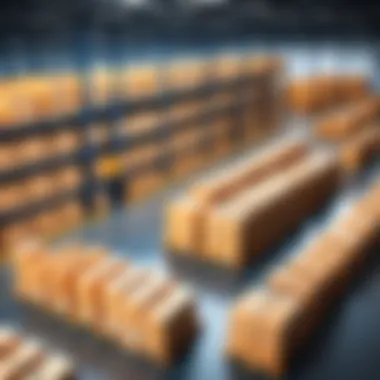
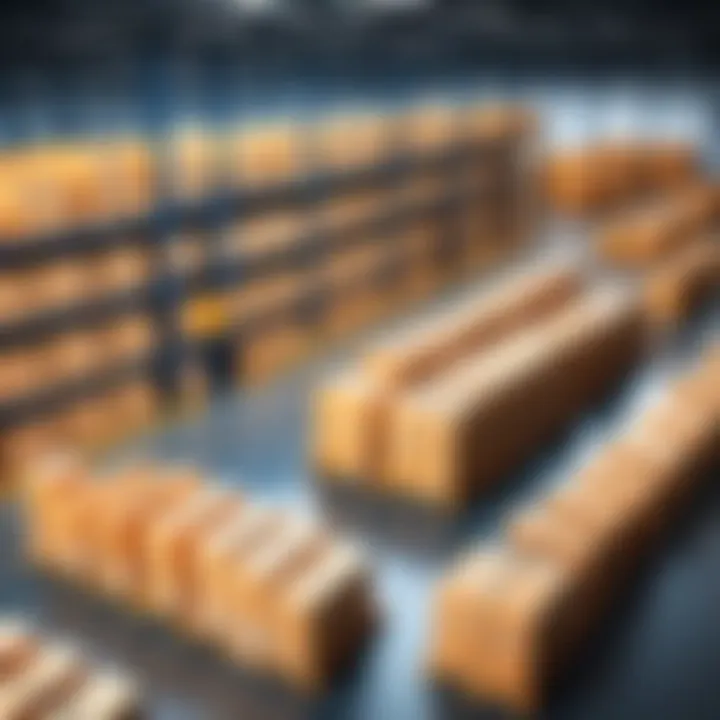
Under FIFO, the oldest inventory items are sold first. This method is particularly useful for products that have a limited shelf life, such as perishable goods. The advantages of the FIFO method include:
- Reduction in Waste: By selling older stock first, businesses can minimize the risk of expired items.
- Accurate Financial Reporting: FIFO typically leads to higher profit margins during inflationary periods since older, cheaper items are recorded as sold first.
LIFO (Last In, First Out)
Conversely, LIFO assumes that the most recently acquired inventory items are sold first. This method can be beneficial in certain scenarios:
- Tax Benefits: During periods of inflation, LIFO can result in lower taxable income since higher cost recent items reduce reported profits.
- Cash Flow Management: By matching current costs with revenues, LIFO can enhance cash flow.
Choosing between these two methods should align with the company's financial goals and inventory type. While FIFO is generally favored for perishables, LIFO might be more advantageous in industries experiencing volatile prices.
"The right inventory strategy can either make or break your operational efficiency. Understanding and applying these approaches can lead to significant improvements in both inventory management and financial performance."
Regulatory Considerations
Regulatory considerations play a crucial role in warehouse and inventory management systems. As businesses operate in increasingly complex environments, understanding the legal frameworks is essential. Compliance with regulations ensures that inventory practices meet safety standards and legal obligations. This understanding can also mitigate risks associated with operational disruptions or penalties from non-compliance.
Compliance Requirements
Compliance requirements encompass various standards that organizations must adhere to in their inventory management practices. These may include local, national, and international regulations. Key aspects of compliance often involve:
- Safety Standards: Many industries face stringent safety regulations. For instance, the handling of hazardous materials is governed by specific guidelines which organizations must follow.
- Quality Control: Certain sectors, such as pharmaceuticals or food production, require adherence to quality assurance processes. This ensures that products meet defined standards before they are shipped.
- Environmental Regulations: As sustainability becomes more prominent, regulations regarding the environmental impact of operations are also being enforced. Companies must manage waste and minimize environmental footprints.
Organizations need to continuously monitor these requirements as they evolve. This includes engaging with regulatory bodies and industry groups to stay informed on changes that may affect their operations.
Data Protection and Security
With the growing reliance on technology, data protection, and security have become paramount. Businesses face increasing threats to their digital information, particularly in warehouse and inventory management systems where sensitive data is stored. Key points related to data protection include:
- Regulatory Compliance: Laws such as the General Data Protection Regulation (GDPR) set strict guidelines on how organizations manage personal data. Adhering to these laws is vital to avoid hefty fines.
- Cybersecurity Measures: Implementing robust security measures, such as encryption and firewalls, can protect against unauthorized access to data. This is particularly important for e-commerce transactions which involve customer information.
- Training Staff: Regular training on data handling practices can help minimize the risk of internal breaches. Ensuring that personnel understand the importance of security protocols is essential for effective data protection.
"A well-structured data protection strategy not only secures sensitive information but also builds trust with customers."
As firms navigate these challenges, they must prioritize both compliance and robust security measures in their strategies. This will enhance the overall efficiency of warehouse and inventory systems while mitigating potential risks.
The Future of Warehouse and Inventory Management
The future of warehouse and inventory management is pivotal in shaping how businesses adapt to rapid changes in technology and consumer expectations. As demand for efficiency and precision grows, organizations must embrace new developments to stay competitive. By focusing on emerging technologies and sustainable practices, companies can enhance their operations, reduce costs, and contribute positively to the environment.
Emerging Technologies
Emerging technologies are set to redefine warehouse and inventory management. Technologies such as artificial intelligence (AI), the Internet of Things (IoT), and blockchain promise to enhance accuracy and efficiency.
- AI and Machine Learning: These tools can analyze vast amounts of data, optimize inventory levels, and predict future trends. They help in automating routine tasks, enabling employees to focus on higher-level functions.
- IoT Devices: These devices improve tracking and monitoring of inventory in real-time. For instance, RFID tags and smart shelves can provide valuable data about item conditions and location.
- Blockchain: This technology increases transparency in the supply chain. It ensures that data is tamper-proof, thereby enhancing trust between suppliers and clients.
These technologies not only streamline operations but also improve decision-making. They embed flexibility into the supply chain, which is critical in today's volatile market.
Sustainability in Warehousing
Sustainability is becoming an integral component of warehouse and inventory management. Companies are realizing that adopting eco-friendly practices can lead to substantial benefits. This commitment to sustainability is seen in several areas:
- Green Warehousing: Utilizing energy-efficient systems and renewable energy sources reduces the carbon footprint. Solar panels and energy-efficient lighting are examples of such initiatives.
- Waste Reduction: Implementing recycling programs and optimizing packaging are essential to minimize waste. This not only meets regulatory requirements but also resonates with environmentally conscious consumers.
- Sustainable Transportation: Companies are investing in electric vehicles and efficient logistics strategies to reduce emissions during shipping.
Holistically, sustainability strengthens brand image and can lead to cost savings in the long term. Companies that prioritize these practices can differentiate themselves in a crowded marketplace.
Case Studies of Successful Implementations
Case studies showcasing successful implementations of warehouse and inventory management systems are vital for understanding real-world applications. These cases reveal effective strategies, pinpoint potential obstacles, and underline the importance of adaptability in various industries. By analyzing these examples, decision-makers can discern best practices and adapt lessons learned to their own contexts. These studies provide practical insights, demonstrating how tailored solutions can yield significant benefits in efficiency and cost management.
Retail Industry Examples
In the retail sector, effective inventory management is crucial for customer satisfaction and profitability. A well-documented case is that of Zara, the fashion retailer, which has revolutionized inventory processes. Their approach focuses on just-in-time inventory replenishment, enabling them to maintain low stock levels while meeting customer demand swiftly.
Zara's system employs timely updates derived from sales data gathered at the point of sale. This data informs supply chain decisions, allowing the company to react promptly to trends. As a result, Zara significantly reduces excess inventory, thereby minimizing storage costs. Retailers can learn from Zara's model and consider integrating real-time data analytics into their operations.
Another noteworthy example is Amazon, which utilizes advanced robotics and machine learning in their warehouses. These technologies streamline operations by optimizing product placement and enhancing pick-and-pack processes. By employing a network of fulfillment centers strategically located near major markets, Amazon improves delivery times, thereby boosting customer satisfaction and loyalty.
Manufacturing Sector Insights
The manufacturing sector also provides insightful examples of successful warehouse management implementations. A prominent case is that of Toyota, known for its renowned lean manufacturing processes. Toyota employs a Kanban system for inventory control, which helps regulate the supply of materials to production lines without overstocking. This method has allowed Toyota to achieve high levels of efficiency while minimizing waste.
Through frequent assessment and continuous improvement, Toyota maintains an agile supply chain that adapts to changes in production demand. This flexibility is essential for staying competitive in the fast-paced manufacturing environment. Other manufacturers can analyze Toyota’s methodologies and consider adopting similar inventory control systems to optimize their processes.
Another significant example in the manufacturing domain is Boeing, which has implemented a sophisticated inventory management solution to cope with the complexity of its supply chain. Boeing utilizes a centralized data system that integrates real-time information from various suppliers, helping to manage parts and materials efficiently. This system minimizes downtime caused by shortages and helps maintain the production schedule.
In summary, these examples from the retail and manufacturing sectors provide valuable lessons on the effectiveness of tailored inventory management systems. They illustrate the importance of incorporating technology and data-driven strategies to enhance operational efficiency and achieve better customer satisfaction. By studying these cases, businesses can gain insights that may guide their own practices and decision-making processes.
Cost-Benefit Analysis of Inventory Systems
The cost-benefit analysis of inventory systems plays a crucial role in determining the effective allocation of resources within supply chain management. This analysis helps organizations weigh the initial expenses against the ongoing benefits of implementing effective inventory management systems. It assists decision-makers in understanding whether the investment will yield substantial returns while improving operational efficiency.
Cost-benefit analysis can guide companies to make informed decisions about inventory technology investments. It highlights potential savings that can arise from enhanced inventory tracking, reduced wastage, and improved use of space. Additionally, such analyses often lead to increased accuracy and better customer satisfaction.
"A well-conducted cost-benefit analysis is not just about numbers; it reflects a strategy's value in enhancing overall business operations."
Initial Investment vs. Long-term Savings
When assessing inventory systems, the initial investment is often a significant consideration. Upfront costs can include purchasing software, implementing technology, and training employees. However, understanding these costs in the context of potential long-term savings is essential.
Organizations that invest in advanced systems might pay more initially but can expect:
- Reduced labor costs: Automation can decrease the workforce needed for manual tasks.
- Minimized stockouts: Improved management often leads to fewer lost sales due to out-of-stock items.
- Lower carrying costs: Efficient inventory practices can help reduce excess stock, decreasing storage needs and costs.
- Increased sales: Streamlined processes often lead to faster delivery times, which can attract more customers.
Ultimately, while the initial expense may seem daunting, the potential for long-term savings can justify the outlay.
Return on Investment Calculations
Measuring the return on investment (ROI) for inventory systems is vital for understanding the impact of expenditures. ROI calculations help businesses assess the profitability of their investments in inventory technology. It involves comparing net profit gained from the investment to the costs incurred.
To effectively calculate ROI for inventory systems, companies should follow these steps:
- Determine Total Costs: Include initial and ongoing costs such as software, hardware, maintenance, and training.
- Calculate Net Profit: Account for the revenue increase attributed to better inventory management, considering factors like reduced losses and increased efficiency.
- Apply the ROI formula:[ ROI = \fracNet ProfitTotal Costs \times 100 ]
This calculation enables organizations to assess whether the benefits of a new inventory system outweigh the costs. An acceptable ROI figure varies by industry, but decision-makers should aim for metrics that demonstrate significant financial and operational improvements.
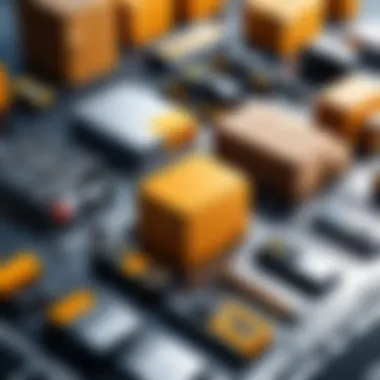
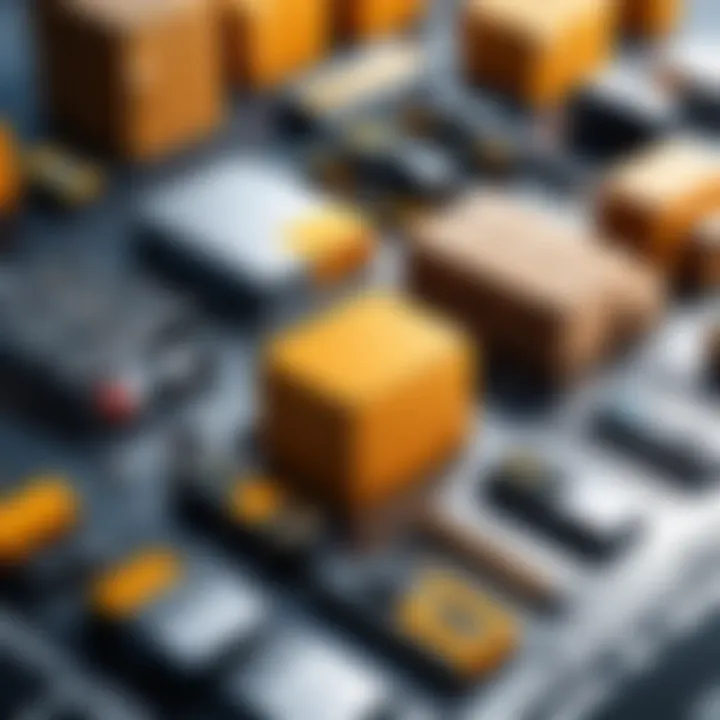
Overall, both the initial investment and ROI calculations provide critical insights into the cost-effectiveness of inventory management systems. Understanding these areas helps decision-makers strategize effectively and optimize supply chain performance.
Integrating E-commerce with Inventory Management
In the contemporary landscape of retail and logistics, the integration of e-commerce with inventory management systems is paramount. This integration not only enhances operational efficiency but also addresses the evolving expectations of consumers who demand speed and accuracy. With e-commerce on the rise, businesses are compelled to adapt their inventory strategies to manage online sales effectively while sustaining physical store operations.
Central to this integration is the capacity to synchronize stock levels across multiple channels. Without real-time data on inventory, e-commerce operations risk overselling, leading to customer dissatisfaction. The relevance of this topic lies in the growing interdependence between inventory systems and e-commerce platforms, dictating that businesses prioritize this integration to maintain competitiveness in a digital-first marketplace.
Challenges of E-commerce Fulfillment
The challenges inherent in e-commerce fulfillment are multifaceted. Companies face the issue of inaccurate inventory data, which can stem from bad data entry practices or insufficient technology infrastructure. This leads to complications such as:
- Stockouts: An inability to meet customer demand can result in potential sales loss.
- Overstock: Conversely, excess stock can lead to wastage and higher holding costs.
- Complex Logistics: Managing returns and exchanges adds layers of complexity that can strain resources and lead to inefficiencies.
Moreover, seasonal fluctuations in demand create an additional layer of challenge. Anticipating spikes in sales, like during holidays, requires advanced planning and flexible inventory systems. A comprehensive understanding of these challenges is critical for organizations aiming to streamline their e-commerce operations.
Strategies for Seamless Integration
To tackle the challenges of integrating e-commerce with inventory management, several strategies can be employed to ensure a smooth process:
- Implementing Real-Time Inventory Tracking: Utilizing technologies like RFID and barcode scanning can offer accurate, immediate insights into stock levels. This aids in maintaining accurate records and fosters more informed decision-making.
- Centralized Inventory Management Software: Opting for software solutions, such as SAP or Oracle Netsuite, creates a unified view of inventory across all channels. Such systems allow stakeholders to monitor stock in real-time and adjust quickly to changing demands.
- Collaboration with Suppliers: Building solid relationships with suppliers can lead to better stock management. Utilizing vendor-managed inventory (VMI) systems can empower suppliers to monitor stock levels and ensure timely replenishment.
Integration is not merely a technical requirement; it is a strategic imperative that influences customer experience, operational costs, and overall efficiency. A well-integrated inventory management system can become a competitive advantage in the rapidly evolving world of e-commerce.
"E-commerce has transformed the retail landscape. Businesses must adapt their inventory strategies to thrive in this environment."
Training and Workforce Management
Training and workforce management represent a crucial aspect of warehouse and inventory management systems. When organizations invest in training, they enhance the overall capabilities of their workforce, which translates into improved operational efficiency and effectiveness. Without proper training, even the best systems may not yield optimal results. Staff competency is directly linked to productivity and error reduction in warehouses.
In today's fast-paced market, companies cannot afford to overlook the significance of workforce training. Developed skills lead to greater engagement and lower turnover rates, which are essential for maintaining a stable environment. Organizations must cultivate a culture of continuous learning to foster adaptability and promote best practices in managing warehouse tasks.
Skill Development for Staff
Skill development for staff is a central component of training initiatives. Staff must possess a diverse set of skills to successfully manage inventory and operate warehouse technologies. Some essential skills include:
- Knowledge of warehouse management software, such as SAP or Oracle
- Proficiency in inventory tracking techniques
- Understanding safety regulations and best practices
- Strong communication skills for teamwork and coordination
Ongoing skill development encourages employees to stay updated with industry trends. It also prepares them for future changes in technology or processes. Organizations should also facilitate coaching and mentorship opportunities. This not only enhances skills but also builds a supportive company culture.
Technology Usage Training
Technology usage training is critical in today's automation-driven warehouse environments. Staff must understand how to utilize various technological solutions effectively. Outdated practices can lead to mistakes and wasted resources. As new systems are implemented, tailored training sessions help staff adapt seamlessly.
Training can include:
- Hands-on workshops for new software and hardware
- Online courses for self-paced understanding
- Scheduled refresher courses to reinforce knowledge
Moreover, leveraging simulation programs can provide employees with practical experience without risks associated with real operations. Comprehensive training on technology builds confidence among staff, leading to more informed decision-making and efficient warehouse operations.
"Investing in workforce training is not just about compliance; it’s about cultivating excellence and agility in warehouse management."
Supplier Relationship Management
Supplier relationship management (SRM) is a crucial element in the realm of warehouse and inventory management systems. It encompasses strategies and practices that organizations implement to manage their interactions with suppliers effectively. In a landscape where efficiency and reliability are key, robust SRM can enhance supply chain performance and drive value.
The benefits of strong supplier relationships cannot be overstated. Companies that invest in SRM often experience improved product quality, timely deliveries, and reduced costs. Taking the time to build these relationships allows businesses to better negotiate favorable terms and can even lead to innovation through collaboration with suppliers. A strong partnership can ensure that suppliers understand the company’s needs, allowing both parties to work hand in hand toward common goals.
Building Strong Supplier Partnerships
Building strong supplier partnerships involves understanding the dynamics of each relationship. It is important to identify the right suppliers—not just those who offer the lowest prices, but those who have a track record of reliability, quality, and communication. Regularly assessing supplier performance is a good practice in maintaining these relationships.
Several key elements contribute to building these partnerships:
- Open Communication: Both parties should engage in regular, transparent dialogue. This ensures that expectations are clear and that any issues can be resolved swiftly.
- Mutual Benefits: Relationships that focus on win-win scenarios enhance trust and create a collaborative environment.
- Long-term Engagement: Engagement that goes beyond price negotiations encourages innovation and continuous improvement.
- Feedback Mechanisms: Providing constructive feedback helps suppliers understand how they can improve and incentivizes them to do so.
Adopting these practices allows companies to create synergies that benefit both the business and its suppliers. Strong partnerships can also lead to strategic alliances that further enhance competitive advantage.
Negotiating Terms and Conditions
Negotiating terms and conditions effectively is vital for optimizing supplier relationships. This process should not merely focus on costs but also take into account service levels, quality standards, and delivery schedules. Here are some strategies to consider during negotiations:
- Researching Market Prices: Understanding market benchmarks enables more informed conversations about pricing and service levels.
- Clarifying Expectations: Clearly defining what is expected from the supplier regarding quality, delivery times, and communication can prevent misunderstandings.
- Flexibility: Being open to negotiation on both sides fosters a stronger relationship and demonstrates commitment to partnership.
- Documenting Agreements: Written agreements provide a reference point for both parties and help avoid potential disputes in the future.
Successful negotiations lead to terms that are beneficial and sustainable. This enhances the overall performance of both parties and minimizes risks associated with supply chain disruptions.
Effective supplier relationships are not just transactional; they are strategic assets that can significantly impact an organization's operational efficiency and competitiveness.
Streamlining Processes through Lean Management
Lean management is a strategy that focuses on minimizing waste while maximizing productivity. In the context of warehouse and inventory management systems, this approach proves to be invaluable. It enables organizations to enhance efficiency, reduce operational costs, and improve service quality. Streamlining processes through lean management involves several critical elements that are essential for decision-makers and IT professionals to understand.
Principles of Lean Management
- Value Identification: The first principle revolves around identifying what constitutes value from the customer's perspective. It requires understanding customers' needs and eliminating any activities that do not add value.
- Value Stream Mapping: This principle involves analyzing the flow of materials and information to identify areas of waste. Mapping out the entire process helps visualize which steps are necessary and which can be eliminated or improved.
- Continuous Improvement: Often referred to as Kaizen, this principle emphasizes ongoing, incremental improvements. It encourages teams to constantly seek efficiencies and suggest enhancements to processes, creating a culture of innovation.
- Pull System: Instead of pushing inventory through the supply chain, lean management advocates for a pull system where inventory is only produced or ordered in response to actual demand. This reduces overproduction, one of the primary forms of waste.
- Empowerment of Employees: Engaging employees in decision-making not only leads to better solutions but also fosters a sense of ownership and accountability. When employees are empowered to improve processes, organizations often see significant gains.
Application in Warehouse Operations
Implementing lean management principles in warehouse operations can result in tangible benefits.
- Optimized Workflow: By mapping value streams, organizations can design workflows that minimize movement and maximize efficiency. A well-organized warehouse reduces time spent searching for items.
- Inventory Reduction: Lean practices reduce excess inventory by adopting a pull system. This saves on storage costs and decreases the likelihood of obsolescence.
- Space Utilization: Effective use of space is critical. Lean management encourages layout rearrangements that minimize waste and enhance accessibility.
- Improved Response Times: By streamlining processes, warehouses can achieve faster order fulfillment. This is crucial for customer satisfaction and maintaining competitiveness in the market.
"Lean management in warehousing is not a one-time event; it is a continuous journey toward excellence."
Culmination and Recommendations
In the realm of warehouse and inventory management, a comprehensive understanding of systems and practices is crucial. The conclusion acts not merely as a summary but also as a critical pathway for direction in future endeavors. The effectiveness of warehouse operations hinges on the integration of efficient strategies, leveraging technology, and aligning processes with business objectives.
The recommendations outlined here aim to enhance operational efficiency, mitigate risks, and ensure sustainable growth. Stakeholders should prioritize training programs focused on both emerging technologies and foundational practices. Understanding the interplay between these systems allows for better decision-making and ultimately, improved performance metrics.
Key Takeaways
- Integration of Technology: Leverage automation tools and cloud-based systems to enhance efficiency and data accuracy.
- Data-Driven Decisions: Utilize analytics to interpret inventory trends and forecast demands.
- Continuous Improvement: Regularly review and optimize inventory processes. Techniques like cycle counting can lead to better accuracy.
- Supplier Relationships: Build strong partnerships with suppliers to ensure the smooth flow of materials and mitigate risks associated with supply chain disruptions.
- Training and Development: Invest in workforce skill enhancement to keep pace with technological advancements and operational methodologies.
"Continuous improvement in warehouse systems is not just beneficial; it is essential for survival in a competitive market."
Future Considerations
As we look toward the future, several factors will shape warehouse and inventory management practices.
- Emerging Technologies: Artificial intelligence, machine learning, and Internet of Things will redefine operational efficiency. Companies must be prepared to adopt these technologies to stay relevant.
- Sustainability Goals: Environmental concerns will drive changes in inventory practices. Integrating sustainable methods into warehousing operations will not only comply with regulations but can also enhance brand reputation.
- Global Supply Chain Dynamics: The future of inventory management will involve adapting to shifts in global supply chains influenced by geopolitical and economic factors. Strategic flexibility will be key.
- Regulatory Changes: Keeping abreast of changes in compliance requirements related to data protection and security will be vital as regulations continue to evolve.