Understanding MRP vs ERP: Key Differences Explained
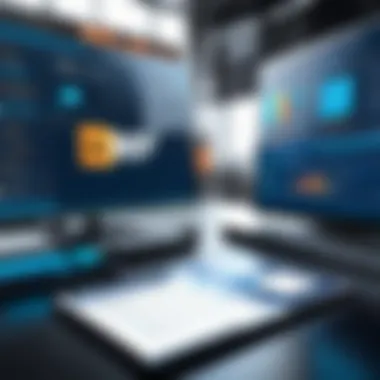
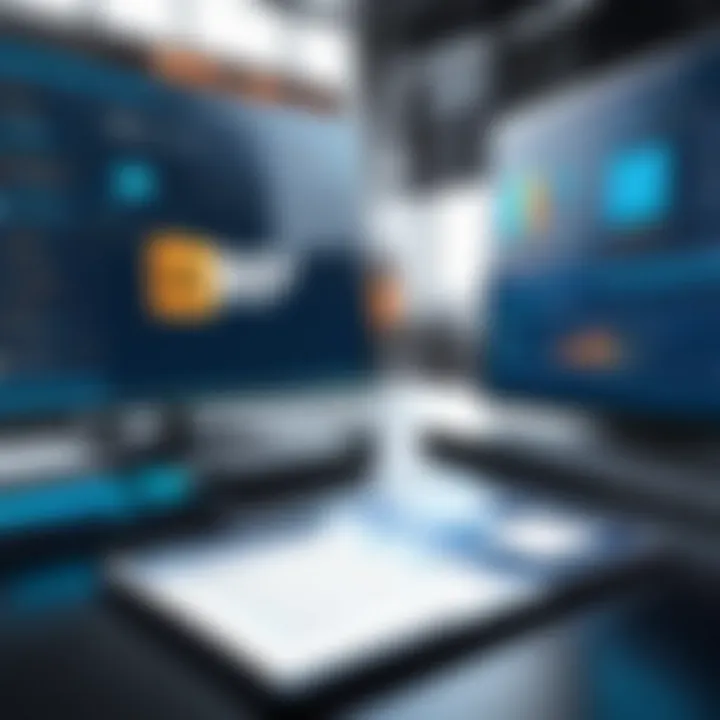
Intro
In today’s complex business landscape, organizations often face the challenge of selecting appropriate software systems to enhance their operations. Two prominent systems that frequently arise in such discussions are Material Requirements Planning (MRP) and Enterprise Resource Planning (ERP). Understanding the distinctions between these two systems is vital for decision-makers, IT professionals, and entrepreneurs. This examination will provide insights into the unique features, advantages, and practical applications of both MRP and ERP.
Organizations must comprehend their operational requirements before making software selections. Each tool offers distinct functionalities catering to scaled needs within production management and overall enterprise functions. This article will delve deeply into key software features, comparison metrics, and their implications for your business strategy.
Key Software Features
Essential functionalities
MRP systems focus primarily on managing materials and inventory levels. They ensure that materials and components are available for production, facilitating efficient scheduling and optimizing inventory management. Core functionalities include:demand forecasting, inventory control, and production planning.
On the other hand, ERP systems encompass a broader scope. They integrate various business processes, including finance, human resources, supply chain, and customer relationship management. Essential functionalities of ERP systems comprise of:
- Financial management
- Supply chain management
- Project management
- Risk management
Advanced capabilities
MRP systems can handle complex production schedules but often lack the comprehensive integration found in ERP systems. For example, while MRP can inform purchasing decisions based on inventory needs, it does not provide insights into overall financial health or customer relationship management. Conversely, ERP systems are designed to provide advanced capabilities such as:
- Real-time data analytics
- Interdepartmental communication
- Workflow automation
This expansive outlook enables ERP systems to promote enhanced collaboration and streamline operations across various functions within the organization.
Comparison Metrics
Cost analysis
When choosing between MRP and ERP, cost plays a significant role. MRP systems are generally more affordable as they focus on single, specific functions. However, the longer-term expenses may rise with the need for add-ons or upgrades as business requirements grow. ERP implementations involve greater initial investments but often yield higher returns through efficiency and enhanced data utilization over time.
Performance benchmarks
Performance benchmarks also offer insight into the effectiveness of each system. To evaluate which system aligns better with an organization’s goals, metrics may include:
- Return on investment (ROI)
- User satisfaction
- System uptime and reliability
ERP systems frequently show improved performance metrics due to their robust architecture, allowing organizations to scale their operations easily and adapt to changing market demands.
In an era where operational efficiency is paramount, understanding these metrics aids in making informed choices regarding software implementations.
When considering both MRP and ERP systems, a thorough evaluation of these distinctions is essential. By comprehending the key features and comparison metrics, decision-makers can strategically choose a system that aligns with their objectives, ultimately enhancing organizational performance.
Preamble to MRP and ERP
In today's dynamic business environment, understanding the role of both Material Requirements Planning (MRP) and Enterprise Resource Planning (ERP) systems is critical. These systems provide essential support for operational efficiency and strategic alignment across various organizational functions. Recognizing their distinctions can help decision-makers choose wisely which system fits their business needs.
Definition of MRP
Material Requirements Planning (MRP) is a production planning, scheduling, and inventory control system used to manage manufacturing processes. The main aim of MRP is to ensure that materials are available for production while minimizing inventory levels. This system focuses mostly on the manufacturing process. It does so by calculating material requirements based on production schedules, customer orders, and inventory levels. Through effective MRP implementation, companies can enhance production efficiency, improve delivery performance, and reduce excess inventory.
Definition of ERP
Enterprise Resource Planning (ERP) goes beyond the scope of MRP by integrating all functional areas of an organization into a single comprehensive system. ERP systems combine finance, HR, manufacturing, supply chain, and other essential business functions in a unified framework. This integration allows for real-time data sharing across departments, providing a holistic view of business processes. An effective ERP system can drive operational efficiencies, support better decision-making, and improve overall organizational agility.
Historical Context
The origins of MRP can be traced back to the late 1960s, where it began as a tool for managing inventory in manufacturing. Initially focused solely on materials and production, MRP evolved through the 1980s and culminated in more sophisticated systems often referred to as MRP II, which included additional functions like capacity planning.
ERP, on the other hand, emerged in the 1990s as businesses sought integrated solutions that connected all facets of their operations. With advancements in technology and software development, ERP systems transformed the landscape of business management by breaking down silos and promoting a more cohesive operational strategy.
Understanding these historical developments allows organizations to appreciate how each system has evolved to meet contemporary needs. This knowledge will support informed decisions about which system to adopt or continue using.
Core Functionalities of MRP Systems
Material Requirements Planning (MRP) systems are vital tools for managing production processes and inventory levels. Understanding their core functionalities offers insights into how they contribute to operational efficiency. In this section, we will explore three key areas: inventory management, production planning, and resource allocation. Each aspect not only supports daily operations but also enhances overall productivity within manufacturing and production environments.
Inventory Management
Inventory management is one of the critical functionalities of MRP systems. This process involves tracking the quantity of materials and products at every stage of production. An effective MRP system ensures that the right amount of inventory is in place, preventing shortages or overstock situations.
Benefits of Efficient Inventory Management:
- Cost Reduction: Reduces costs associated with excess inventory including storage fees.
- Increased Efficiency: Minimizes delays in production caused by lack of materials.
- Enhanced Order Accuracy: Improves the fulfillment rates by ensuring the availability of required materials.
With the capability to analyze historical data, MRP systems can forecast future inventory needs. This capability enables organizations to respond proactively to changes in demand, thereby minimizing waste and optimizing resource usage.
Production Planning
Another essential functionality of MRP systems is production planning. This process allocates available resources most effectively to ensure timely completion of production schedules. MRP software facilitates detailed scheduling of manufacturing processes, taking into account various factors like lead time, production rates, and capacity constraints.
Key Considerations for Production Planning:
- Lead Time Management: The MRP system calculates how long it takes to procure materials and process them, allowing for realistic timelines.
- Flexibility: It allows adjustments in production plans based on real-time data, enhancing responsiveness to market conditions.
- Resource Optimization: Helps in maximizing the use of labor, machinery, and materials, which streamlines operations.
By aligning production plans with inventory levels and demand forecasts, MRP systems enable streamlined operations and better customer satisfaction through on-time deliveries.
Resource Allocation
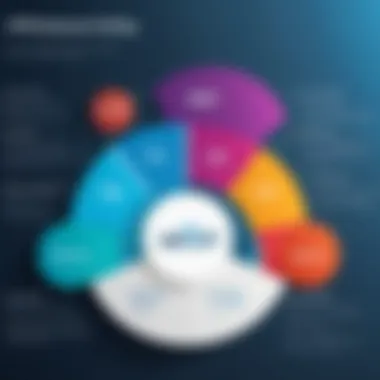
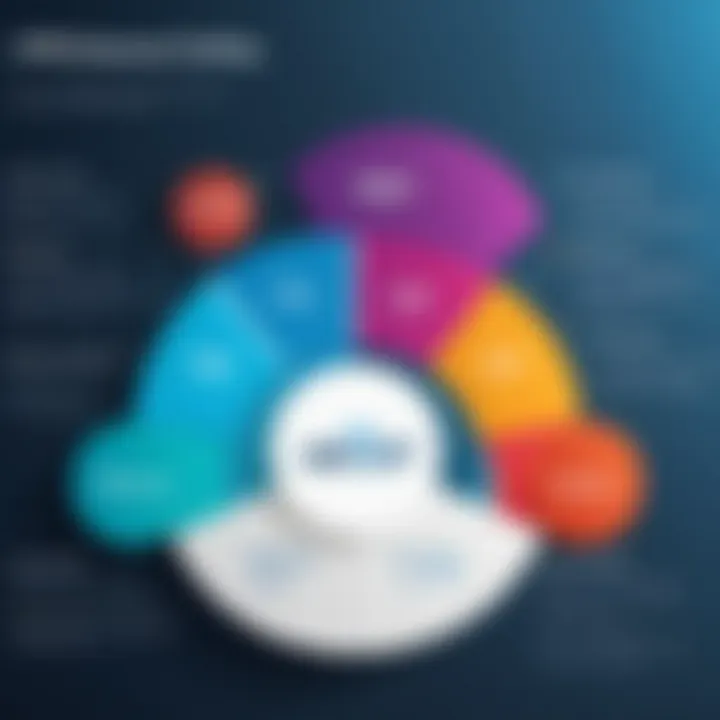
Resource allocation is another core functionality of MRP systems that focuses on the effective distribution of resources across various production activities. This functionality ensures that all necessary inputs, such as raw materials, labor, and equipment, are available for the manufacturing process.
Importance of Resource Allocation:
- Preventing Bottlenecks: By understanding which resources are needed when, MRP helps prevent delays in the production chain.
- Cost Management: Efficient allocation reduces waste and optimizes use of resources, contributing to overall cost savings.
- Production Efficiency: Ensures that production lines function smoothly as resources are aligned with production schedules.
MRP systems take into account all these factors, enabling organizations to manage their resources effectively, thereby enhancing operational efficiency.
"The effectiveness of MRP systems lies in their ability to match supply with demand, ensuring production processes run smoothly and efficiently."
Understanding these core functionalities illustrates the importance of MRP systems in modern production environments. They offer decisive tools for inventory management, production planning, and resource allocation, helping organizations achieve their operational goals.
Core Functionalities of ERP Systems
Enterprise Resource Planning (ERP) systems play a crucial role in the comprehensive management of an organization’s resources. By integrating various business processes and functions into a unified system, ERPs facilitate better data flow and communication among departments. Understanding these core functionalities is vital for decision-makers aiming to enhance operational efficiency.
Integrated Business Processes
At the heart of ERP systems lies the capability for integrated business processes. This means that several different functions, such as finance, HR, and supply chain management, work seamlessly together within one platform. This integration eliminates data silos, reduces redundancy, and improves accuracy.
Benefits of integrated processes include:
- Streamlined workflows across departments
- Enhanced collaboration and communication
- Real-time visibility into operations
Decision-makers benefit from clearer insights and can drive improvements throughout the organization. Thus, organizations can respond better to market demands and internal needs.
Real-Time Data Management
Real-time data management is another pillar of ERP systems. This functionality allows organizations to gather, analyze, and act on data as it occurs. Timely access to information is essential in making informed decisions. The ability to view real-time metrics significantly enhances responsiveness.
Key advantages include:
- Greater accuracy in reporting
- Immediate tracking of inventory and sales
- Agile decision-making based on current data
Having this capability reduces the risk of errors and fosters a more proactive approach to business challenges.
Financial Management Functionalities
Financial management is a core function of ERP systems, designed to streamline and enhance accounting processes. This includes budgeting, forecasting, and financial reporting. With robust financial management tools, organizations can ensure compliance, adjust budgets, and analyze financial performance.
Important aspects include:
- Automated invoicing and billing processes
- Comprehensive financial reporting capabilities
- Improved cash flow management
These functionalities provide clarity and insight into the financial health of the organization, allowing for data-driven strategic planning.
Successful ERP implementations emphasize the need for understanding these core functionalities. Addressing specific business needs while leveraging these advantages can lead to substantial operational improvements.
Key Differences Between MRP and ERP
Understanding the differences between MRP and ERP is crucial for organizations seeking to optimize operations and enhance efficiency. The distinctions guide the selection of the right system based on specific needs, goals, and existing infrastructure. Each system has unique characteristics, advantages, and limitations that can significantly influence a company’s operational success. By recognizing these differences, decision-makers can better assess which solution aligns with their strategic objectives.
Scope and Focus
The scope of MRP focuses primarily on inventory and production planning. MRP systems are designed to manage the materials required for manufacturing, ensuring that the right amount of materials is available at the right time. This system centers on supply chain activities needed for production. MRP streams help in forecasting demand, scheduling production runs, and maintaining an optimized inventory level.
Conversely, ERP systems have a much broader scope. They integrate various business processes across departments, including finance, human resources, customer relationship management, and supply chain management. The primary focus of ERP is to provide a unified view of the organization, facilitating data flow between all business functions. Therefore, while MRP serves a specific purpose in production, ERP offers an all-encompassing approach that connects different functions of a business.
Complexity of Implementation
The complexity of implementing MRP systems tends to be lower compared to ERP systems. MRP solutions can often be deployed rapidly and without extensive changes to an organization's existing processes. A smaller company or a department within a larger organization may find MRP systems more accessible because they usually require fewer resources and less training than ERP systems.
In contrast, ERP implementations generally involve significant changes across multiple departments. The complexity arises from the need for data integration from various business areas. As a result, the implementation process can be lengthy and resource-intensive. Organizations must consider their readiness for this change, as the shift to an ERP framework often demands careful planning, involvement from multiple stakeholders, and comprehensive training.
User Base and Accessibility
When it comes to user base, MRP systems are typically designed for users within the production or manufacturing departments. These users often have specific, technical roles focused on inventory and resource management. MRP systems may serve a narrower audience, which can limit accessibility for decision-makers and team members in other departments.
On the other hand, ERP systems cater to a wider user base. They are suitable for diverse roles across an organization, from financial analysts to human resource professionals. Their functionality allows information exchange among departments, promoting cross-functional collaboration. However, this broad user base requires effective training and user-friendly interfaces to ensure all employees can leverage the system efficiently.
Choosing the right system should reflect not only the organization's immediate needs but also long-term strategic objectives.
By understanding these key differences, organizations can navigate their decision-making processes more effectively. MRP and ERP systems serve different functions and choosing one over the other—or considering their integration—depends on business size, industry, and operational goals.
Common Misconceptions
In the realm of business software, numerous misunderstandings circulate regarding Material Requirements Planning (MRP) and Enterprise Resource Planning (ERP) systems. Addressing these misconceptions is crucial as it prevents organizations from making uninformed decisions that could impact their operations negatively. A clear distinction between MRP and ERP can empower decision-makers and IT professionals. Misinterpretation may lead to inappropriate software selection, inefficient resource allocation, and ultimately less than optimal operational efficiency.
MRP as a Subset of ERP
One common misconception is the belief that MRP is merely a subset of ERP systems. While MRP systems focus specifically on the logistics of manufacturing operations, ERP systems encompass a much broader scope. ERP aims to integrate all facets of a business, including finance, HR, inventory, and customer relations, alongside manufacturing needs.
Often, people assume that by implementing ERP, they are automatically covered for MRP functions. However, this is not always the case. An ERP might include MRP functionalities, but not all ERP systems are configured to optimize production and inventory schedules adequately. Therefore, understanding the distinct needs of an organization is vital when choosing the right system.
Functional Overlap
Another misconception relates to the perceived functional overlap between MRP and ERP systems. While it’s true that both systems handle inventory management and production scheduling, their objectives differ markedly. MRP systems are designed primarily for planning and controlling manufacturing processes. They focus on ensuring material availability and minimizing production delays.
In contrast, ERP systems are meant for broader business process integration. They provide insights across departments. These insights help in strategic decision-making. Despite these differences, the functionalities can intersect. Many ERP systems include MRP-style features, causing confusion about their distinct roles.
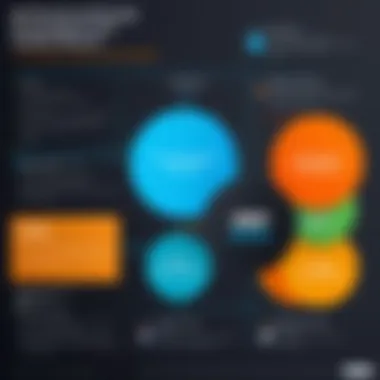
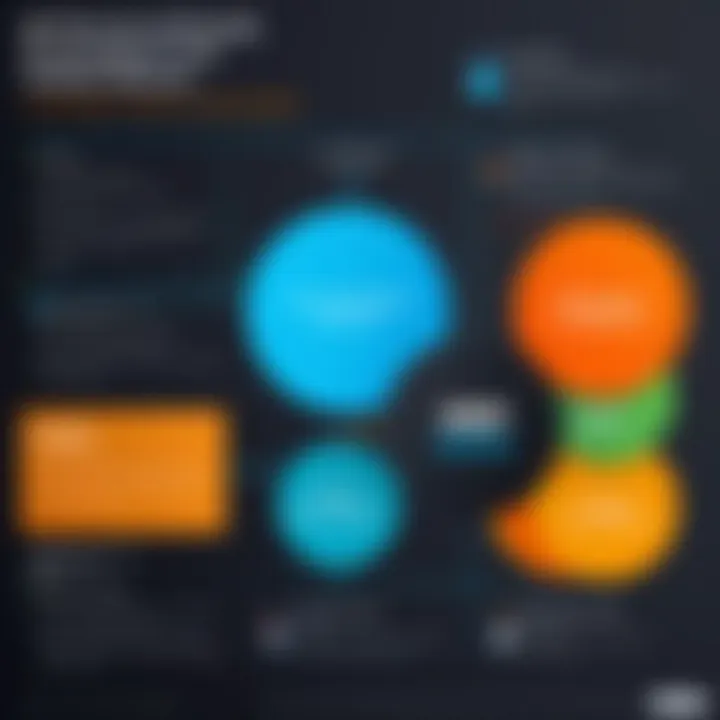
"Choosing between MRP and ERP systems based on misconceptions can lead to inefficiencies and wasted resources."
Recognizing the boundaries and the specific strengths each system offers can assist decision-makers in making better choices tailored to their business's unique landscape. Understanding these misbeliefs helps in aligning the choice of system with organizational objectives.
Advantages of MRP
Material Requirements Planning (MRP) systems have distinct advantages that are critical for manufacturing companies and related sectors. This section discusses the importance and specific benefits of MRP systems, emphasizing cost efficiency and improved production scheduling.
Cost Efficiency
Cost efficiency is one of the primary advantages of MRP systems. By optimizing inventory levels, MRP reduces excess stock while ensuring that production processes are adequately supplied. This leads to a significant reduction in carrying costs. Carrying excess inventory ties up capital that could be used elsewhere in the business.
With MRP, companies can align their purchasing strategies with demand forecasts. This means raw materials are ordered only when necessary. Efficiently managing stock levels reduces waste. Less waste translates into lower costs over time. The ability to foresee demand ensures that production runs smoothly without unnecessary delays or idle machinery. The result is a lean manufacturing approach that maximizes resource use and enhances financial performance.
"Cost savings achieved through MRP implementation can be substantial, often leading to improved overall profit margins."
In addition, accurate planning helps in negotiating better terms with suppliers. Since MRP facilitates timely orders based on precise requirements, suppliers are more likely to offer favorable pricing. This can further enhance the overall cost efficiency of businesses utilizing MRP.
Improved Production Scheduling
Improved production scheduling is another key advantage of MRP systems. These systems allow manufacturers to develop more effective schedules. By determining the exact timing and quantity of materials needed, MRP helps to prevent production delays. This is especially crucial in industries where timely product delivery is essential to maintain customer satisfaction.
MRP provides visibility into the production process. It enables managers to identify bottlenecks and adjust schedules accordingly. This adaptability enhances the ability to respond to changes in market demand. Moreover, optimized production scheduling ensures that resources are utilized to their fullest extent. This can lead to increased output without significant investments in additional equipment or labor.
The ability to synchronize production plans with sales forecasts aids companies in minimizing downtime and increasing business agility. Therefore, improved production scheduling contributes not only to operational efficiency but also to better strategic alignment with market conditions.
Advantages of ERP
Enterprise Resource Planning (ERP) systems provide a range of advantages that can significantly enhance business operations. Understanding these advantages is essential for decision-makers who must weigh the benefits against the associated costs and implementational complexities of ERP solutions. The advantages of ERP systems extend beyond mere efficiency — they encompass vital elements that can drive an organization towards achieving its strategic goals.
Holistic Business Insights
One of the most significant benefits of ERP systems is their ability to deliver holistic business insights. ERP systems consolidate data from various business functions into a single, unified platform. This integration facilitates real-time data analytics and reporting, which are crucial for informed decision-making.
With access to comprehensive data, managers can analyze trends, monitor performance, and make proactive decisions. For instance, a finance department can access sales data while the sales team can see inventory levels, which can lead to better alignment between departments. By breaking down silos, ERP promotes a culture of collaboration and transparency.
Additionally, having a centralized database enhances data integrity. Organizations can reduce the risk of errors caused by data duplication or inconsistencies. Accurate data leads to improved forecasting, budget planning, and resource management. These insights can ultimately shape strategic initiatives, enabling organizations to respond swiftly to market changes.
"In an era where data drives decision-making, the holistic view provided by ERP systems is not just a luxury — it is a necessity."
Scalability and Integration
Another key advantage of ERP systems is their scalability and integration capabilities. As businesses evolve, their operational requirements change. An ERP system can grow alongside the organization, allowing for flexibility in adapting to new processes or additional departments. This scalability is particularly important for companies looking to expand their reach or diversify their products and services.
Moreover, modern ERP systems are designed with integration in mind. They can seamlessly connect with other software applications and technologies, including supply chain management tools, customer relationship management systems, and more. This interconnectedness ensures that all components of the organization work coherently, optimizing overall performance.
For example, if a business implements a new sales tool, it can often integrate this tool directly with its ERP system instead of requiring a completely new infrastructure. As a result, businesses can utilize their existing processes and data without significant disruptions, further increasing efficiency.
Challenges Associated with MRP
Material Requirements Planning (MRP) systems are vital for organizations aiming to optimize their manufacturing processes. However, they come with specific challenges that need to be understood for effective decision-making. Recognizing these limitations is essential for businesses, particularly larger enterprises that face unique operational demands. The subsequent subsections examine the primary challenges associated with MRP systems, providing insight into their implications.
Limited Scope for Larger Enterprises
One significant drawback of MRP systems is their limited scope when applied to larger enterprises. MRP primarily focuses on production planning and inventory control, making it suitable for small to mid-sized operations. However, for larger organizations, the intricate nature of their operations demands more comprehensive solutions.
Large enterprises often have complex supply chains and diverse product lines. MRP may not adequately manage these complexities, leading to inefficiencies. For instance, coordination issues across various departments can arise, resulting in delayed deliveries and increased costs.
Additionally, larger companies may require functionalities that extend beyond traditional MRP capabilities, such as financial integration and human resources management. This limitation forces firms to consider implementing ERP systems instead, which offer a broader scope and can support integrated business processes.
Sensitivity to Demand Changes
Another critical challenge of MRP systems is their sensitivity to demand changes. MRP relies heavily on accurate forecasting to maintain inventory levels and schedule production effectively. However, market conditions often fluctuate unpredictably, and this can throw MRP systems off balance.
When demand spikes unexpectedly, the MRP system may struggle to adjust. This results in stockouts, delayed production, or excessive inventory buildup. Conversely, during downturns, companies could find themselves with surplus stock, tying up capital and increasing holding costs.
In high-volatility markets, businesses need to address these sensitivity issues. Continuous monitoring and adjustment of forecasts are essential. Furthermore, the integration of advanced analytics and AI could help mitigate these problems, but such enhancements may not exist within basic MRP systems.
MRP systems can falter when faced with sudden market changes; being aware of this helps companies strategize effectively.
Understanding these challenges surrounding MRP systems enables decision-makers to weigh the pros and cons. Knowing the limitations helps organizations to better align their choice of software with their operational needs, encouraging a more strategic approach to resource planning.
Challenges Associated with ERP
Understanding the challenges associated with Enterprise Resource Planning (ERP) systems is crucial for any organization contemplating their implementation. ERP systems, while powerful, come with unique difficulties that can impede operational success if not properly managed. Highlighting these challenges offers decision-makers insights into the potential hurdles they may face, allowing for informed strategy development prior to investments in such complex software.
High Implementation Costs
One of the most significant challenges of ERP systems is the high implementation costs. This encompasses not only the initial acquisition costs but also the expenses related to installation, customization, and ongoing maintenance. Companies often underestimate the total cost of ownership.
Factors contributing to high costs include:
- Licensing Fees: Most ERP vendors charge substantial fees for software licenses.
- Customization Needs: Organizations frequently customize ERP systems to fit their unique needs, driving up costs.
- Consultant Hiring: Many businesses require external consultants for smooth implementation, further increasing expenses.
Considering these aspects, firms must develop a clear financial plan. The potential return on investment should also be analyzed deeply. This evaluation helps in justifying the expenses against expected improvements in efficiency and productivity.
Complex User Training Requirements
Another challenge associated with ERP systems is the complexity of user training requirements. ERP systems encompass multiple business processes and functionalities, which can overwhelm employees during the transition phase. Effective training is necessary to ensure users utilize the system efficiently. Key points to consider include:
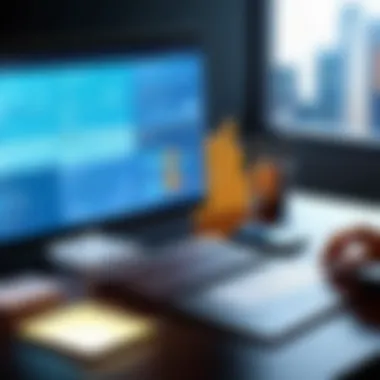
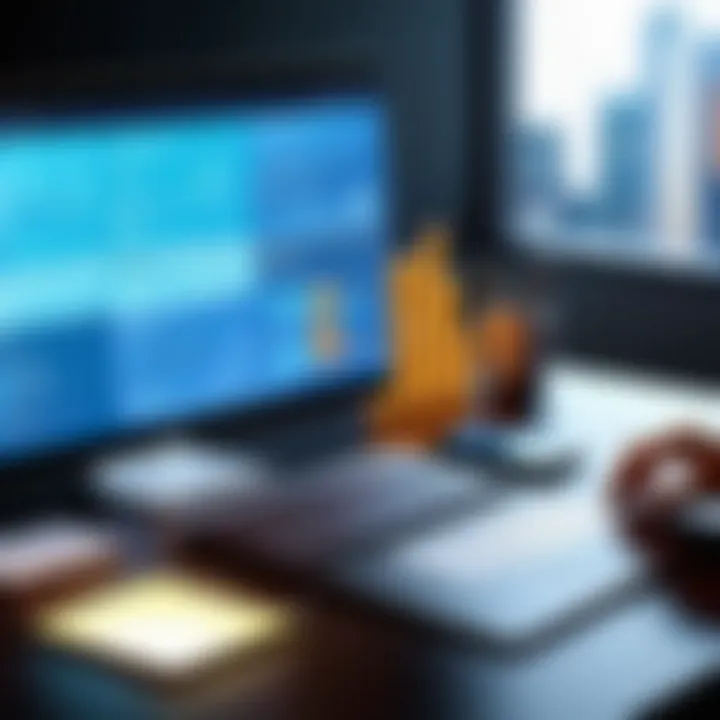
- Diverse User Roles: Employees from various departments may need different training approaches based on their specific requirements. This necessitates a tailored training program.
- Time Investment: Significant time may be required to train staff adequately, affecting daily operations.
- Ongoing Support: After initial training, continued user support is essential for addressing questions and enhancing skills.
Implementing comprehensive training strategies can alleviate some of these challenges. Engaging training sessions that involve hands-on experience allow users to better adapt to the ERP system. Investing in user training ultimately reduces resistance and enhances productivity.
"Effective training can significantly reduce the implementation burden and improve overall user satisfaction with the ERP system."
Integration of MRP and ERP Systems
Integrating Material Requirements Planning (MRP) and Enterprise Resource Planning (ERP) systems can significantly impact operational efficiency and decision-making in an organization. Both systems, while distinct, share data requirements and can complement each other when aligned correctly. Understanding how to effectively combine these systems is critical for businesses aiming to improve productivity and streamline workflows.
In today's fast-paced business environment, integration ensures that an organization can make informed decisions based on real-time data from multiple sources. This connection allows for a smoother flow of information between various departments, from manufacturing and inventory management to finance and sales.
When to Integrate
Integration is most beneficial during specific scenarios, including:
- Growing Business Needs: As a company expands, its operational needs become more complex. At this stage, integrating MRP with ERP can provide a comprehensive view of resources, facilitating better management decisions.
- Data Silos: If different departments use separate systems that do not communicate efficiently, integration can break down these silos, allowing for a unified data source.
- Change in Business Strategy: A shift towards a more integrated approach in management can prompt the need for an aligned system that combines the functionalities of both MRP and ERP.
Determining the right time to integrate requires a thorough assessment of existing processes and a clear understanding of organizational goals. Decision-makers must evaluate the current systems in place and identify gaps in data flow and operational efficiency.
Benefits of Integration
The integration of MRP and ERP provides several advantages, including:
- Enhanced Visibility: A combined system offers a holistic view of business operations, making it easier to identify bottlenecks and inefficiencies.
- Improved Decision-Making: With access to real-time data across departments, organizations can make quicker, data-driven decisions.
- Streamlined Operations: Integration minimizes redundancy in data entry and maintenance, saving time and reducing the risk of errors.
- Better Resource Management: Accurate and updated information on inventory and resources can lead to more effective planning and allocation efforts.
"Integrating MRP and ERP is not just a technological challenge; it is a strategic step towards operational excellence."
Moreover, integrating these systems can enhance customer satisfaction by enabling a more responsive supply chain. For example, better inventory management leads to faster order fulfillment and improved service levels.
Industry-Specific Applications
Understanding how MRP and ERP systems function across various sectors is crucial for organizations aiming to optimize their operations. The distinct requirements of each industry shape the functionalities and benefits these systems can provide. By leveraging the unique features that cater to specific applications, companies can improve efficiency, reduce costs, and enhance overall productivity.
Manufacturing Sector
In the manufacturing sector, MRP systems are essential for managing inventory and production schedules. These systems allow manufacturers to plan their production processes more effectively, taking into account the availability of raw materials and the production capacity. This ensures that the right amount of product is manufactured just in time to meet customer demands, minimizing excess inventory.
Key benefits of MRP in manufacturing include:
- Enhanced Production Efficiency: MRP systems provide detailed insights into what materials are needed when. By optimizing stock levels, manufacturers can streamline their production processes.
- Reduced Lead Times: By accurately predicting material requirements, MRP helps shorten lead times, allowing for faster order fulfillment.
- Cost Control: With better inventory management, operational costs are kept in check, directly impacting profit margins.
"Effective utilization of MRP in the manufacturing sector leads to significant operational improvements and cost reductions."
Retail Sector
In the retail sector, ERP systems play a dominant role. They provide a comprehensive view of business operations, which is essential for retailers managing multiple facets such as inventory, sales, and customer relationships. Retailers benefit from real-time data analysis that allows for strategic decision-making.
Important aspects of ERP in retail include:
- Integrated Operations: ERP systems integrate various business functions, allowing retailers to manage stock levels, sales data, and customer feedback in one platform.
- Enhanced Customer Experience: With access to real-time inventory levels, retailers can ensure stock availability, directly improving customer satisfaction.
- Data-Driven Insights: Retailers can gather and analyze sales trends, enabling them to make informed decisions about promotions, pricing, and stock management.
Future Trends in MRP and ERP Systems
The landscape of business technology is evolving rapidly. For decision-makers and IT professionals, understanding these shifts is crucial for maintaining operational efficiency. The focus on future trends in MRP and ERP systems highlights critical developments that could redefine how organizations manage resources and processes. By recognizing these trends, businesses can better adapt and innovate, ensuring they remain competitive in a dynamic market.
Cloud-Based Solutions
Cloud-based solutions have fundamentally changed how MRP and ERP systems function. The shift from on-premise installations to cloud environments offers multiple advantages.
- Flexibility and Scalability: Companies can easily scale their operations. They can adjust resources according to needs without major overhauls of infrastructure.
- Cost Savings: Many businesses see reduced costs with cloud solutions. There is less need for investment in server hardware and maintenance.
- Accessibility: Data in cloud systems can be accessed anywhere. This mobility is crucial for remote teams and global operations.
- Automatic Updates: Providers often manage updates. This means organizations can benefit from the latest features without interruptions.
"The cloud has made ERP systems more accessible and cost-effective, enabling even small businesses to leverage its power."
However, companies must consider data security and compliance. Trusting a third party with stringent data can be a challenge. It's essential to evaluate providers carefully and ensure they meet necessary legal standards.
Artificial Intelligence Applications
The incorporation of artificial intelligence into MRP and ERP systems is another significant trend. AI technologies improve operational efficiency and decision-making by utilizing data in novel ways.
- Predictive Analytics: Businesses can forecast demand more accurately. This leads to better inventory and resource management.
- Process Automation: AI can automate repetitive tasks, allowing staff to focus on higher-level responsibilities. This can enhance productivity and morale.
- Enhanced Decision-Making: By analyzing large datasets, AI systems provide insights that support strategic planning and operational improvements.
- Customization: AI allows systems to adapt based on user behavior, creating a more personalized experience.
The challenge lies in the complexity of implementing AI solutions. Businesses must be prepared to invest in training and integration processes. That said, the potential return on investment can be substantial.
In summary, the future trends in MRP and ERP systems focus heavily on cloud technologies and artificial intelligence. As organizations navigate these changes, understanding their implications will be vital for achieving strategic objectives.
Epilogue
The conclusion serves as a vital component of this article, reinforcing the essential differences and synergies between Material Requirements Planning (MRP) and Enterprise Resource Planning (ERP) systems. It encapsulates the primary insights gleaned through the discussion, providing decision-makers and IT professionals the clarity needed to navigate the complexity of these systems.
Summarization of Key Points
In reviewing the primary themes addressed in the article, several key points emerge:
- Distinct Functions: MRP focuses on the management of manufacturing processes and material requirements, while ERP encompasses a broader scope, integrating various business functions beyond production, including finance and human resources.
- Integration and Complexity: ERP systems tend to be more complex and require greater resources for implementation compared to MRP solutions, which are generally simpler and more focused.
- User Accessibility: The audience for each system differs, with MRP being more beneficial for manufacturing-focused teams and ERP appealing to a wider audience across an organization.
- Future Trends: Advancements in technology, such as cloud-based solutions and artificial intelligence, are shaping the future of both MRP and ERP systems, enhancing their functionalities and accessibility.
By synthesizing these points, organizations can better understand their options and align their operational needs with the right system.
Considerations for Decision-Making
When considering whether to implement MRP, ERP, or an integrated solution, several factors come into play:
- Business Needs: Assess the specific requirements of your organization. If your focus is on optimizing inventory and production schedules, an MRP system may serve you well. Conversely, if you seek comprehensive insights across departments, ERP may be more suitable.
- Budget Constraints: Evaluate the financial implications of each system. MRP systems often present lower upfront costs, making them more attractive for smaller businesses. ERP implementations, while costly, can yield significant long-term benefits through efficiency and integration.
- Scalability: Consider the future growth of your enterprise. ERP systems are designed to scale with your business, accommodating increased complexity over time, while MRP may demonstrate limitations as the size and scope of operations expand.
- Training and Support: Recognize the resources needed for successful user adoption. An ERP system typically demands more extensive training, as its functionalities are varied and comprehensive.
Ultimately, the decision should weigh the specific operational goals against the strengths and limitations of MRP and ERP systems, leveraging insights gained from this analysis to foster organizational success.