SPC Excel Add-In: Functions, Benefits, and Strategies
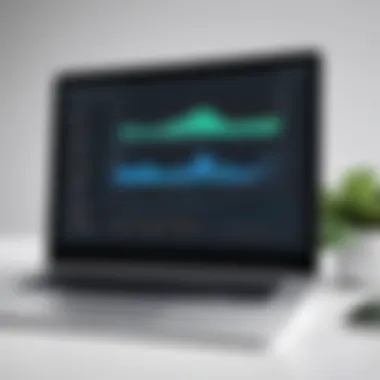
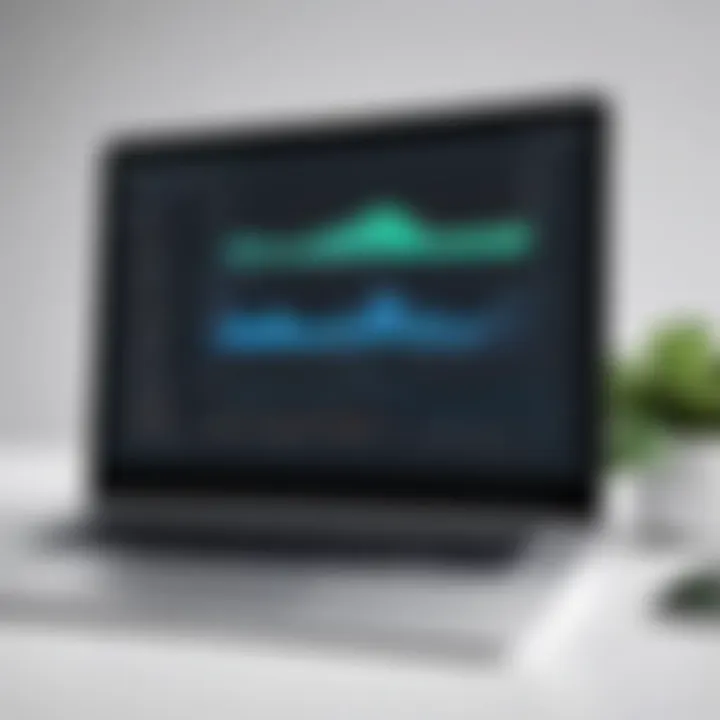
Intro
In the fast-paced world of business, maintaining quality and optimizing processes is crucial. This is where Statistical Process Control (SPC) comes into play. By utilizing statistical methods, organizations can monitor and control their processes effectively, leading to improved quality and operational efficiency. With the introduction of the SPC Excel Add-In, businesses now have the ability to seamlessly incorporate these statistical tools directly into their daily operations. This allows for quick data analysis without needing extensive training in specialized software.
Using Excel as a platform is incredibly advantageous because it is a widely recognized tool in many industries. Almost everyone has at least a basic understanding of it. The SPC Excel Add-In enhances this familiarity, providing functionalities that enable users to apply SPC principles without steep learning curves. Essentially, it acts as a bridge between statistical concepts and practical applications.
In this article, we will delve into the key features of the SPC Excel Add-In, compare its metrics, and explore various applications across industries. Through an exploration of case studies and best practices, this guide aims to empower decision-makers, IT professionals, and entrepreneurs to make informed choices about incorporating this tool into their processes.
Prelude to SPC and Excel
In today's fast-paced business environment, the significance of effective data management and quality control cannot be overstated. Statistical Process Control (SPC) has become a cornerstone for organizations aiming to enhance their operational efficacy. This section serves as the gateway to understanding how integrations like the SPC Excel Add-In can optimize these processes. By delving into SPC, we uncover tools that empower organizations, enable informed decision-making, and ultimately drive performance.
Understanding Statistical Process Control
Statistical Process Control is a method used to monitor and control processes to ensure they operate efficiently and produce conforming products. It's a proactive approach that emphasizes the idea that preventing defects is preferable to detecting them after production. By applying statistical methods, businesses can identify trends and variations that may elevate or diminish quality, thus allowing them to respond before costly errors escalate.
SPC is not just about charts and numbers; it’s about creating a culture focused on quality. Implementing SPC in an organization can facilitate remarkable transformation in operations. For instance, consider a manufacturing plant that uses SPC to monitor daily output rates. Early identification of deviations from expected results allows the team to investigate potential causes, which could range from equipment malfunctions to employee performance. Thus, the crux of SPC lies in its capacity to bring insight into process performance while minimizing waste and improving consistency.
Role of Excel in Data Management
Excel is an indispensable tool in the business landscape, known far and wide for its versatility. It can be used for a myriad of functions, from simple budgeting to complex statistical analysis. Its role in data management, particularly in conjunction with SPC, is pivotal. With the SPC Excel Add-In, users are equipped with specialized functionalities that streamline data analysis significantly.
Why does Excel matter in this context? For one, it holds the ability to handle substantial amounts of data efficiently, allowing businesses to perform statistical analyses without the need for complex software. Excel's grid format presents data in a manner that's easy to digest, helping teams visualize their results effectively.
Moreover, integrating SPC into Excel not only simplifies the calculation and visual representation of various metrics but also makes real-time analysis feasible. Teams can quickly generate control charts and analyze process capability, fostering informed decisions based on up-to-date data. This agility is precious for decision-makers who need to respond promptly to issues as they arise.
The Significance of SPC Excel Add-In
The SPC Excel Add-In plays a pivotal role in modern data analysis, especially for industries focused on quality control. It offers a tailored set of tools that facilitate the application of Statistical Process Control methodologies directly within Excel. Businesses that integrate this add-in can significantly enhance their data management capabilities and foster an environment conducive to continuous improvement.
One of the standout features of the SPC Excel Add-In is its user-friendliness. It's designed to empower users, irrespective of their statistical prowess. This means that even those who might not be number-savvy can utilize it effectively. By bridging the gap between complicated statistical concepts and everyday business operations, the add-in is not just a tool but a catalyst for productivity.
"Empowering users with intuitive tools leads to better decisions and improved outcomes."
Benefits of Using the Add-In
Streamlined Analysis
Streamlined analysis refers to the ability to process and interpret large sets of data swiftly without getting bogged down by complex procedures. This is central to maintaining efficiency in any operation. The SPC Excel Add-In simplifies the steps needed to perform statistical analyses, saving time that can be utilized for more strategic endeavors.
Its intuitive interface allows users to generate various types of control charts or conduct capability studies at the click of a button. A unique feature of this aspect is its automation capabilities, meaning repetitive tasks can be performed with minimal input from the user. This reduces human error and enhances the reliability of the information produced. However, it's essential to remain cautious as over-reliance on automation can sometimes lead to overlooking critical details in the data.
Real-Time Data Visualization
Real-time data visualization is about presenting data as it's being collected, which is increasingly crucial in today's fast-paced environment. This function of the SPC Excel Add-In allows users to observe trends and anomalies instantly, enhancing their ability to make informed decisions on the fly.
The visual element is a key characteristic here; by transforming raw data into easy-to-understand graphs and charts, users can quickly grasp complex information. The unique feature associated with this benefit is the customization of visual outputs, enabling users to tailor presentations that resonate with their audience. This means while it has the advantage of providing insights quickly, analysts need to ensure that the visuals accurately represent the underlying data and avoid misleading interpretations.
Enhanced Decision-Making
Enhanced decision-making is at the heart of adopting any statistical tool. The SPC Excel Add-In steps in here by providing analytics that helps users sift through data and extract valuable insights. By streamlining information flow, organizations can cultivate a data-driven culture where decisions are supported by concrete evidence rather than gut feelings.
A standout element is the predictive analysis feature that enables forecasting potential issues before they materialize, allowing for preemptive action. This proactive approach is highly beneficial, but it requires the user’s experience to interpret predictions correctly. Misunderstanding the forecasts can result in misguided strategies, thus illustrating the importance of proper training and knowledge in using these tools effectively.
Target Audience for SPC Tools
Manufacturing Sector
In the manufacturing realm, precision is king. The SPC Excel Add-In shines here due to its capability to closely monitor production processes and variance. Its specific aspect helps in identifying inefficiencies or deviations from the standard early on. Manufacturers can reap the benefits of reduced waste and enhanced quality assurance.
The unique feature of real-time tracking of production metrics means that any anomalies can be addressed immediately, paving the way for faster corrective actions. However, it does come with its challenges; not all manufacturing environments have the infrastructure to support such tools, and that might limit their effectiveness.
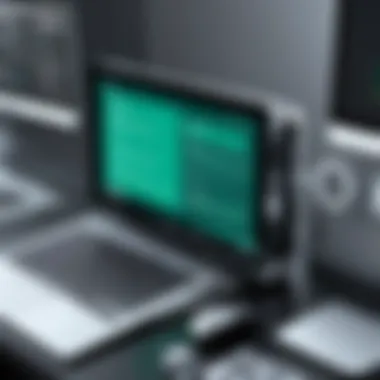
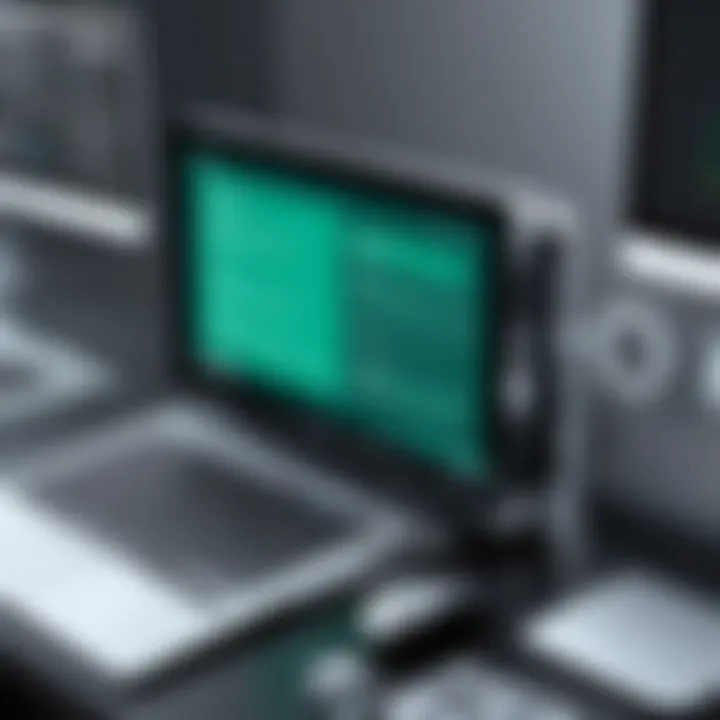
Quality Assurance Teams
For quality assurance teams, the SPC Excel Add-In represents a game-changer. Its systematic approach to error identification and process improvement directly supports their mandate of maintaining high standards. The add-in provides a structured methodology to validate processes, which is critical in industries where regulatory compliance is paramount.
One of the distinctive traits is the ability to quickly generate reports that comply with industry standards. While this is an advantage, the reliance on precise data collection means that ongoing training on data integrity is essential; otherwise, the output reports may not reflect reality.
Business Analysts
Business analysts find the SPC Excel Add-In particularly valuable for conducting thorough data assessments across various domains. Its capacity to distill vast datasets into actionable insights aligns perfectly with their roles. Analysts can dive deep into data trends, identifying opportunities for optimization that can lead to cost savings or enhanced operational efficiencies.
This tool's strength lies in its analytical depth, allowing professionals to perform advanced evaluations easily. However, analysts must remain vigilant about not losing sight of the broader context, as excessive focus on data minutiae can obscure strategic vision.
By understanding the significance of the SPC Excel Add-In, readers can appreciate how it revolutionizes the way data is managed and analyzed, ultimately paving the way for more informed and strategic decision-making across various sectors.
Installation Process of SPC Excel Add-In
Installing the SPC Excel Add-In is a critical step that lays the foundation for effective data analysis and quality management. This process not only provides access to a range of specialized tools but also contributes to better decision-making and streamlined operations within organizations. Without the right setup, even the most powerful analytical capabilities can fall flat. The installation process can seem daunting at first, but breaking it down into manageable steps makes it straightforward.
System Requirements
Before diving into the installation process, it’s essential to ensure your system meets the necessary requirements to run the SPC Excel Add-In effectively. Below are the general prerequisites you should consider:
- Operating System: Windows 10 or later versions are often recommended for optimal performance.
- Excel Version: The add-in typically works with Microsoft Excel 2016 and newer editions. Ensure you have the latest updates installed to avoid compatibility issues.
- RAM: At least 4 GB of RAM is generally sufficient for standard operations; however, 8 GB or more is ideal for heavy data processing.
- Disk Space: Ensure you have a minimum of 100 MB of free space but more may be necessary based on additional tools you plan to utilize.
- Internet Connection: A reliable internet connection might be required for downloading updates or accessing specific features.
Step-by-Step Installation Guide
Once you confirm that your system meets the outlined requirements, follow these straightforward steps to install the SPC Excel Add-In:
- Download the Add-In: Visit the official website where the SPC Excel Add-In is hosted. Look for the "Download" button and click on it to start the downloading process.
- Open Excel: Launch Microsoft Excel on your computer.
- Access the Add-Ins Menu: From the top menu, navigate to the "File" tab and select "Options." In the Excel Options dialog box, select "Add-Ins" from the left-hand side.
- Install the Add-In: At the bottom of the window, find the "Manage" dropdown menu, select "Excel Add-ins," and click the "Go" button. In the Add-Ins dialog box, click on "Browse" to locate the downloaded SPC Excel Add-In file on your computer. Select it and confirm by clicking "OK."
- Enable the Add-In: After installing, ensure that the SPC Excel Add-In is checked in the list. Click "OK" to enable it within Excel.
- Restart Excel: Close and reopen Excel to finalize the installation process. Look for the add-in tab, usually appearing as "SPC" or a similar title on the ribbon.
Troubleshooting Common Installation Issues
It’s not uncommon to run into hiccups during the installation of new software, and the SPC Excel Add-In is no exception. Here are some typical problems users might face along with potential solutions:
- Failed to Download: If the download fails, try switching browsers or connecting to a different network.
- Compatibility Issues: Verify that your version of Excel is compatible. You might need to update Excel from the Microsoft website.
- Add-In Not Visible: If the add-in doesn’t appear on the ribbon, repeat the installation steps and ensure it’s enabled in the Add-Ins menu.
- Performance Problems: Should the software run sluggishly, check your system resources. Closing unnecessary applications or upgrading RAM may help.
- Error Messages: If you encounter cryptic error messages, searching online forums or the official documentation can provide clarity.
By taking the time to properly install the SPC Excel Add-In and resolving any issues that arise, users set themselves up for success in analyzing data and improving processes.
Key Features of SPC Excel Add-In
The SPC Excel Add-In is more than just a tool; it’s a companion in the journey of data-driven decision making. By offering a suite of features tailored for statistical analysis, it empowers professionals to glean insights from raw data. Understanding these key features helps harness their full potential, ensuring that the tool contributes meaningfully to quality control processes.
Control Chart Generation
Control charts are at the nucleus of Statistical Process Control. They serve as a visual representation of process variance over time and alert users to any anomalies. The SPC Excel Add-In streamlines this task by enabling users to generate control charts with a few clicks. With just the right inputs, you can easily plot data points against the control limits and observe trends that might require intervention.
The ability to customize chart settings, such as adding specific control limits or adjusting the chart's look, is particularly advantageous for tailoring presentations to stakeholders. Moreover, being able to spot shifts or trends that go against the grain quickly allows organizations to act before any small problems snowball into larger issues. In essence, control chart generation not only enhances visibility into the workings of processes but also underpins data-driven decision-making.
Process Capability Analysis Tools
Process capability analysis tools are vital for assessing how well a process can produce output within specified limits. The SPC Excel Add-In comes equipped with robust analytical tools that quantify this capability, often presenting metrics like Cp, Cpk, Pp, and Ppk in user-friendly formats. Understanding these metrics is critical for quality assurance teams who need to align their processes with industry standards and customer expectations.
Utilizing the add-in's analysis tools also allows teams to evaluate historical data, providing an insight into long-term performance. By setting a benchmark, users can measure continuous improvement and identify areas where efficiencies can be found. Educating staff about these metrics can further enhance the processes, leading to a culture of quality that resonates throughout the entire organization. When teams share and interpret these results together, it fosters collaboration and collective ownership of quality management.
Data Distribution Analysis
Another useful feature of the SPC Excel Add-In is its data distribution analysis capabilities. This feature allows users to identify how data is distributed across different processes. It’s crucial for understanding variations and ensuring that processes operate within desired parameters. By utilizing tools like histograms and probability plots, users can visualize the data’s distribution patterns and detect any irregularities that may indicate a need for process adjustments.
Understanding the distribution of data also opens the door to advanced analyses, like normality tests and fitting distributions. By comprehending the nature of the data at hand, teams can refine their approaches to control limits and process capability analyses. This can ultimately lead to more efficient processes and informed decisions that drive quality improvements.
In summary, the features of the SPC Excel Add-In not only enhance the way quality control is implemented but also fundamentally change how data is perceived and utilized in decision-making.
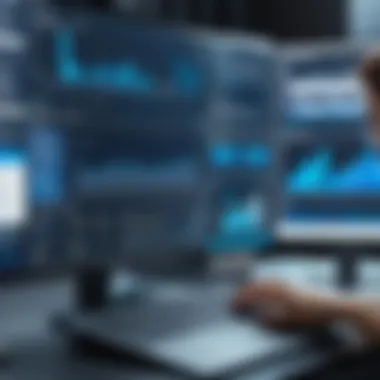
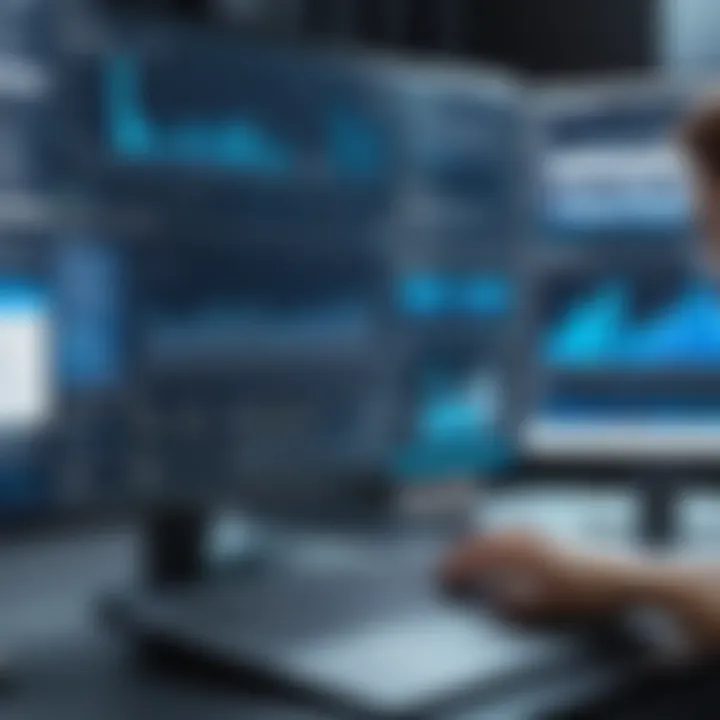
With a deeper understanding of these tools, decision-makers and IT professionals alike can optimize operations within their fields, ensuring superior quality and efficiency.
Utilizing SPC Excel Add-In in Various Industries
The utilization of the SPC Excel Add-In across different industries reflects a growing trend in data-driven decision-making. This powerful tool allows organizations to harness the capabilities of data analysis to enhance quality control and streamline operations. By integrating statistical process control into everyday spreadsheet use, professionals can identify and rectify issues before they escalate, ensuring efficiency and high standards of quality. This section delves into the specific applications of the SPC Excel Add-In in manufacturing, healthcare, and service industries, showcasing the versatile benefits it provides across sectors.
Manufacturing Applications
In the manufacturing sector, the SPC Excel Add-In is a game changer. Production processes often involve complex data that must be monitored continuously to maintain quality. Using this add-in allows manufacturers to easily generate control charts and analyze process capabilities. One concrete example is a widget manufacturer that implemented the SPC tool. They were able to monitor defect rates in real-time. This won’t just show where problems are occurring, but it also helps in tracing back to the root cause, whether it’s a faulty machine or an issue with materials.
Additionally, the ability to visualize data trends through real-time charts empowers manufacturing teams. These insights lead to quicker decision-making, allowing teams to shift production strategies promptly to adapt to quality fluctuations. Moreover, it supports training efforts, helping new technicians get familiarized with data interpretations faster.
Healthcare Sector Applications
The healthcare industry is another domain where the SPC Excel Add-In shines. Hospitals and clinics generate a plethora of data daily, from patient outcomes to operational metrics, and needing consistent analysis to optimize care delivery. For instance, a hospital employing this add-in might track patient wait times across various departments. By analyzing this data, they could identify bottlenecks, whether it is a staffing issue during peak hours or inefficiencies in procedures. This immediate feedback loop not only improves patient satisfaction but also enhances healthcare delivery.
Moreover, the SPC Excel Add-In allows for monitoring critical quality indicators, which is vital for compliance with regulations and standards such as those set by the Joint Commission. As practices adjust to changing healthcare demands, they can use historical data from the add-in to forecast future needs and allocate resources efficiently.
Service Industry Implementation
The service industry, encompassing businesses from restaurants to consulting firms, can also benefit significantly from the SPC Excel Add-In. Consider a chain of cafes monitoring their customer service scores. By collecting feedback data, these businesses can visualize performance metrics over time. With the insights gained, management can implement staff training initiatives aimed at improving customer service quality, which directly affects repeat business and overall brand loyalty.
Additionally, project-based service firms can apply SPC principles when evaluating project timelines and client satisfaction levels. By identifying areas where delays or setbacks occur frequently, teams can implement preventative measures that mitigate risks associated with future projects. This proactive stance not only preserves budgets but also protects the company’s reputation.
In summary, leveraging the SPC Excel Add-In across various industries presents a vast array of benefits. From reducing defect rates in manufacturing to enhancing patient care in healthcare, and improving customer service in the service sector, the potential applications are broad and impactful, positioning organizations for success in today's data-centric environment.
Best Practices for Implementing SPC Using Excel
Implementing Statistical Process Control (SPC) in Excel can transform operational processes and enhance productivity, but it requires careful planning and execution. Proper practices not only make your analysis more accurate but also ensure that your findings lead to meaningful improvements. This section dives into essential strategies and techniques for successful implementation of SPC using Excel, ultimately streamlining operations and promoting a culture of continuous improvement.
Data Collection Strategies
To get the ball rolling with SPC, effective data collection is key. Here are some practices to keep in mind:
- Define Clear Objectives: Before starting, pinpoint what you aim to achieve with your SPC approach. Be it reducing defect rates or increasing process speed, clarity sets the stage for targeted data collection.
- Select Appropriate Data Points: Choose metrics that align with your operational goals. If you're looking at product quality, consider measuring dimensions, weights, or defect counts. Be deliberate about what data you need and how you will collect it.
- Utilize Standardized Forms and Checklists: Implementing standard forms for data entry reduces errors and fosters consistency. This is where Excel shines—custom forms can be created or existing templates modified, making data entry straightforward.
An example could be a daily production log that allows for immediate recording of defects, ensuring real-time data capture.
Monitoring and Reporting Techniques
Once your data is collected, the next stage is proactively monitoring and generating reports. Establish routine checks to assess process stability and performance.
- Set Up Control Charts: Excel's capabilities allow users to create control charts that visually represent process stability over time. These charts can alert you to trends, shifts, or abnormalities that require immediate attention.
- Schedule Regular Review Meetings: Bringing teams together regularly to review SPC reports engenders accountability and keeps quality at the forefront. Discuss findings, trends observed in control charts, and possible improvements.
- Hair it Down to Actionable Insights: Regular reports should not just present numbers but also strive to provide actionable insights. Highlight changes in processes and performance metrics that warrant a deeper dive.
"The effectiveness of SPC not only relies on its data analysis but substantially depends on how that data is reported and acted upon."
Continuous Improvement Processes
Adopting SPC is not a one-time deal; it invokes a culture of continuous improvement. Here's how to do it right:
- Encourage Employee Involvement: Feedback loops should be established where employees’ suggestions on process improvements are welcomed. They are often closer to the action and can offer insights that management might overlook.
- Integrate Lean Principles: Lean management techniques can complement SPC initiatives. For instance, after identifying waste through SPC, strategic lean methods can be applied to eliminate non-value-added activities.
- Training and Development: Continuous education for staff on SPC tools and methods help sustain momentum. Workshops and training keep everyone aligned on objectives and methodologies, ensuring that the team isn’t just reactive but proactive.
In summary, implementing SPC in Excel is about establishing solid data practices, fostering a continuous improvement mindset, and understanding the value of effective reporting. By keeping these best practices at the forefront, organizations can more effectively harness the power of SPC and drive lasting improvements.
Analyzing Case Studies
Analyzing case studies is a crucial part of understanding the real-world applications and effectiveness of the SPC Excel Add-In. Through actual stories and examples, we can see how various organizations have implemented this tool for significant improvements. This section dives into specific elements that showcase the positive impact of utilizing the SPC Excel Add-In, emphasizing benefits like increased efficiency, better decision-making, and enhanced quality control. Case studies not only provide a practical insight but also serve as a source of inspiration for decision-makers and stakeholders considering adopting such tools. By examining the successes and challenges faced by various industries, we can garner deeper insights into the practicalities and benefits of statistical process control in daily operations.
Success Stories in Manufacturing
In the manufacturing realm, there are numerous success stories that highlight the transformative power of the SPC Excel Add-In. One notable example is a prominent automotive manufacturing company that integrated the add-in to monitor its production processes. By analyzing data trends in real-time, the company was able to identify bottlenecks and areas of waste efficiently. A control chart they implemented showed variations in their assembly line that, prior to using the add-in, went unnoticed. The result? They reduced defects by 25%, ultimately improving both product quality and customer satisfaction.
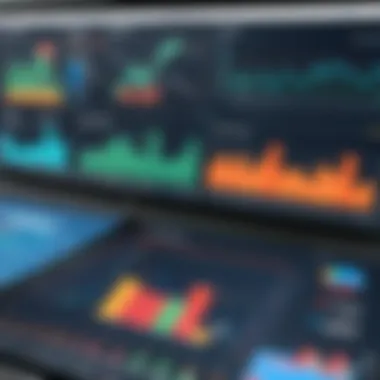
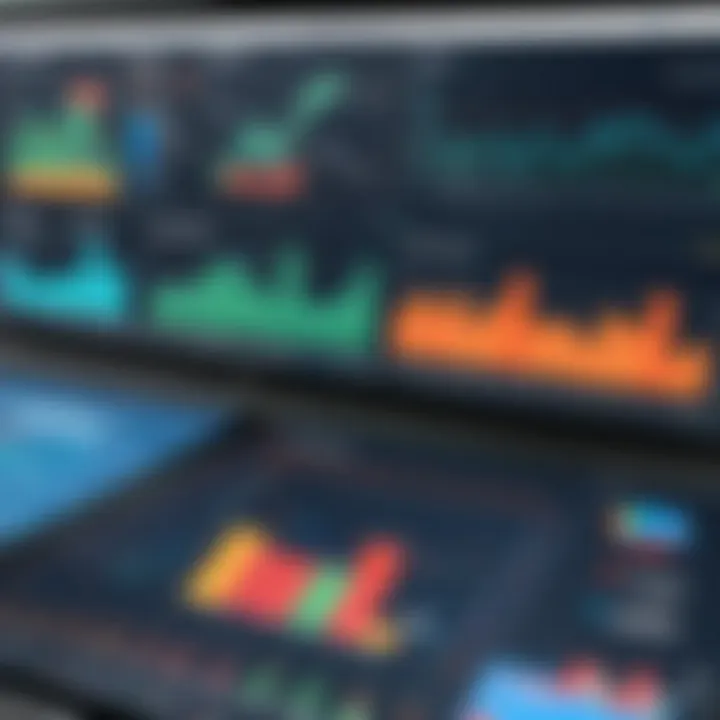
This case illustrates the add-in's robust capabilities for monitoring manufacturing processes. Leveraging the data visualizations available through the SPC add-in allowed managers to make informed decisions swiftly. They could pivot strategies based on real-time data insights and optimize production without lengthy delays. It's not merely about using data; it's about translating that data into action—this is where the SPC Excel Add-In proves invaluable.
Healthcare Improvements through Data Analysis
The healthcare sector has also reaped significant benefits from the integration of the SPC Excel Add-In. A case that stands out is from a mid-sized hospital where quality improvement teams used the add-in to analyze patient wait times in the emergency room. By establishing control charts to visualize patient flow, they identified peak times and uncovered inefficiencies in resource allocation.
As a result, the hospital implemented a streamlined triage process based on the data findings, which contributed to a remarkable 30% decrease in average wait times. Furthermore, staff reported feeling less overwhelmed during peak periods. This case study emphasizes that data analysis is not just a task; it directly impacts patient care and operational efficiency. The SPC Excel Add-In becomes a fundamental tool for healthcare providers seeking to enhance patient experiences and optimize service delivery.
Service Efficiency Gains Using SPC
The service industry often faces unique challenges concerning quality and efficiency. One notable case involved a leading restaurant chain that used the SPC Excel Add-In to enhance service delivery and customer satisfaction. They collected data on customer feedback, employee performance, and service times.
By utilizing tools within the add-in, such as process capability analysis, the management gleaned valuable insights into which locations were struggling and why certain times of the day led to higher customer complaints regarding service speed. Adjustments made—like staff reallocations during busy hours based on data analysis—led to a significant 15% increase in positive customer reviews over three months.
This illustrates how organizations, even in the service sector, can harness the power of statistical process control. The SPC Excel Add-In not only aids in identifying problems but serves as a springboard for actionable insights leading to more streamlined and efficient service management.
Future of SPC Tools in Excel
The future of SPC tools within Excel is a topic that holds significant importance in the realm of data analytics and operational excellence. As businesses navigate increasingly complex datasets, the demand for efficient, user-friendly tools becomes paramount. Adapting to these needs, the SPC Excel Add-In continues to evolve, providing not only enhanced functionalities but also improved ways to harness data for actionable insights. This section delves into the elements shaping the future landscape of SPC tools and the benefits they offer to decision-makers across various sectors.
Emerging Trends in Data Analytics
In the sphere of data analytics, trends are steering organizations toward a more integrated and insightful approach to data handling. Here are several key trends currently shaping the field:
- Predictive Analytics: By using historical data, many companies can foresee trends and customer behavior. This foresight can significantly improve quality control processes.
- Real-Time Data Processing: Organizations are increasingly focused on acquiring data instantly rather than relying on historical snapshots. This ability to assess current conditions allows for prompt adjustments in operations.
- Machine Learning Integration: The incorporation of machine learning algorithms is becoming more prevalent, enabling users to automate data analysis and yield advanced insights from large data sets.
- Cloud-Based Analytics: With cloud solutions, data can be accessed anywhere, anytime, leading to better collaboration and sharing of SPC insights among teams.
- User-Centric Design: There’s a shift toward making SPC tools more intuitive. This aids users who may not have specialized training in data analytics, allowing broader teams to engage with the data meaningfully.
Embracing these trends will allow organizations to enhance their SPC capabilities, driving productivity and quality improvements.
Advancements in Excel Add-Ins
As the digital landscape rapidly evolves, Excel add-ins are becoming increasingly sophisticated. The advancements in the SPC Excel Add-In reflect this progress:
- Interactive Dashboards: Modern add-ins come with features that allow users to create dynamic dashboards. These dashboards provide visual representations of data, aiding in better understanding and quicker decision-making.
- Integration with Other Tools: Current versions of the add-in are better integrated with other software platforms, such as Power BI and SharePoint. This seamless connectivity allows for enhanced reporting and visualization.
- Enhanced Security Features: With data privacy becoming more crucial, advancements in security measures ensure that sensitive information remains protected.
- Customization Options: Users now can tailor add-in functionalities more easily to meet specific analytical needs or to align with industry standards.
- Support for Advanced Statistical Techniques: The capacity to employ sophisticated statistical methods directly within Excel streamlines analysis and interpretation, contributing to effective decision-making.
In summary, the future of SPC tools in Excel is bright, with emerging trends in data analytics and advancements in add-in capabilities. These factors together pave the way for enhanced decision-making and operational efficiencies in various industries.
Closure
In the realm of Statistical Process Control (SPC), the Excel Add-In stands as a formidable ally for professionals aiming to enhance their operations. The insights gleaned from utilizing this tool are not merely beneficial; they can be transformative. Integrated analysis, real-time monitoring, and informed decision-making are just a slice of what adopting this add-in brings to the table. In a world that’s increasingly data-driven, harnessing the capabilities of this add-in allows teams to respond swiftly to fluctuations in processes, thereby maintaining the quality and efficiency that is expected in today’s fast-paced environments.
Summary of Key Points
Throughout this article, we explored the distinctive features and operational advantages of the SPC Excel Add-In. Key takeaways include:
- Benefits: Improved efficiency in data analysis leads to better quality control and decision-making.
- Installation: A straightforward setup process encourages quick implementation, minimizing downtime.
- Uses Across Industries: Whether in manufacturing, healthcare, or services, the applications are wide-ranging and impactful.
- Best Practices: Adopting effective data collection and reporting methods promotes continuous improvement.
- Future Trends: Awareness of emerging analytics trends and advancements ensures that users stay ahead of the curve.
Final Thoughts on Adoption
In closing, the decision to adopt the SPC Excel Add-In should be viewed as a strategic move in the right direction for any organization committed to quality management. It’s not just a tool; it’s a game-changer that encapsulates the essence of modern business practices focused on operational excellence. Investing the time to learn and implement this add-in can yield significant returns in terms of process improvements and data-driven insights.
As industries continue to evolve, understanding the nuances of such tools will be indispensable. The knowledge gained through this article can help professionals navigate the complexities of quality control, ensuring that they make informed choices that resonate throughout their operations.
"In the world of data, those who harness it effectively hold the keys to innovation and progress." - Unknown
By adopting the SPC Excel Add-In, organizations not only equip themselves with an influential instrument but also lay a solid groundwork for future advancements and sustainable quality management.
Importance of Citing Sources
Listing references allows readers to dive deeper into the topics discussed. This is especially true for decision-makers and IT professionals who might seek to investigate related studies, industry standards, or software reviews before implementation. For instance, sources such as Wikipedia and Britannica often provide accessible summaries of concepts, while in-depth articles on platforms like Reddit can showcase real-world applications and community discussions. These insights can help users grasp not just the theoretical underpinnings but also practical experiences and outcomes.
Benefits of Well-Curated References
- Enhanced Credibility: Quality references demonstrate that the content is well researched, earning the trust of a discerning audience.
- Supporting Evidence: References provide the necessary backing when presenting statistics or case studies, allowing professionals to see the broader implications of using tools like the SPC Excel Add-In.
- Opportunity for Further Learning: A well-organized reference section acts as a gateway for readers who wish to explore the subject matter more thoroughly. This includes finding additional literature on statistical process control techniques or ways to effectively utilize Excel add-ins.
Considerations When Citing Sources
While compiling references, it's crucial to maintain a balance between diverse fields and contextually relevant content. For specialized topics like SPC tools, references should ideally include:
- Academic Articles: Peer-reviewed works that outline the fundamental principles or new findings in SPC can enrich the narrative significantly.
- Industry Reports: Documents from reputable organizations that focus on quality management and analytics often provide current trends and benchmarks.
- User Guides and Tool Documentation: Specific documentation for Excel add-ins can greatly assist users in maximizing the functionality and applications of the tool, ensuring they are following best practices.