Revolutionizing Industry: Smart Manufacturing Systems
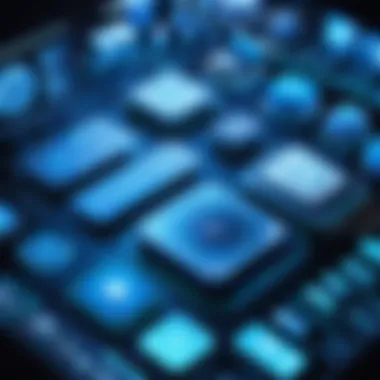
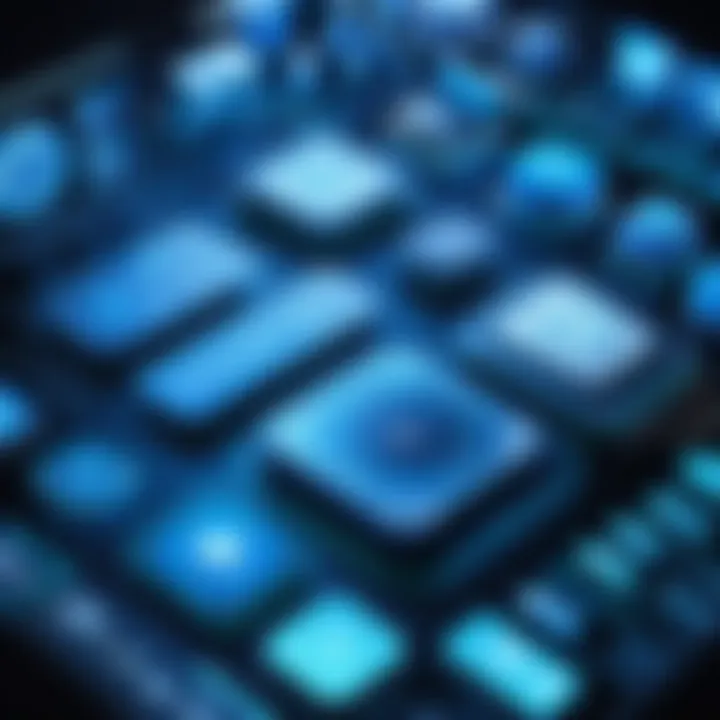
Intro
In today's industrial landscape, the concept of smart manufacturing systems has gained significant traction. These systems are not just a fleeting trend; they represent a profound shift in how industries operate, driven by technological advancements such as the Internet of Things (IoT), data analytics, and automation. Organizations are increasingly recognizing that these technologies can enhance operational efficiency, improve product quality, and boost overall competitiveness.
As industries evolve, understanding the implications of smart manufacturing becomes vital for decision-makers, IT professionals, and entrepreneurs. The integration of smart systems into manufacturing processes is reshaping how businesses manage resources, respond to market demands, and innovate. For industry leaders, grasping these changes is essential in optimizing operations and navigating the complexities inherent in modern manufacturing environments.
This article examines key features of smart manufacturing systems, compares performance and costs, and highlights challenges and considerations during implementation. By delving into these aspects, we aim to furnish readers with a solid foundation for understanding how smart manufacturing is transforming industry dynamics.
Prelude to Smart Manufacturing
Smart manufacturing is a crucial topic in today’s industrial environment. In an era defined by rapid technological advancements, understanding smart manufacturing systems becomes essential. These systems merge various technologies to optimize production processes, improve operational efficiency, and enhance product quality. As such, they are transforming traditional industrial dynamics and reshaping competitive advantages.
Defining Smart Manufacturing
Smart manufacturing can be defined as a holistic approach to manufacturing that leverages advanced technologies to create more efficient production processes. This includes the integration of digital and physical systems, enabling real-time data exchanges and enhancing overall productivity. Smart manufacturing is characterized by:
- Interconnectivity: Machines, devices, and systems are interconnected through the Internet of Things (IoT), which allows for seamless communication and data sharing.
- Data Utilization: Data analytics plays a significant role in smart manufacturing, helping companies derive actionable insights from realized data sets.
- Automation and Robotics: The integration of advanced robotics and automation significantly enhances efficiency, reduces human error, and lowers operational costs.
By capitalizing on these elements, organizations can maximize their production capabilities in a more adaptive and responsive manner.
Historical Context and Evolution
Understanding the historical context of smart manufacturing highlights how far the industry has come. The manufacturing sector has evolved through several phases:
- The Industrial Revolution: Originating in the late 18th century, this period marked the shift from handmade goods to mechanized production, laying the foundation for modern manufacturing.
- Automation and Computerization: In the latter half of the 20th century, automated systems and computers entered the production floor. This integration allowed for more precise control and efficiency in manufacturing processes.
- The Digital Age and Industry 4.0: The recent emergence of Industry 4.0 signifies the current era of manufacturing characterized by the amalgamation of cyber-physical systems, IoT technologies, and big data analytics.
The transition to smart manufacturing is crucial not only for enhancing productivity but also for fostering innovation, sustainability, and overall competitiveness in a global market that is increasingly interconnected.
"Smart manufacturing represents a paradigm shift in the way products are designed, produced, and delivered. It is not just about technology; it's about rethinking the processes."
Core Technologies in Smart Manufacturing
Smart manufacturing systems utilize various advanced technologies that play a vital role in reshaping industry dynamics. These technologies not only streamline operations but also enhance overall productivity and quality. By integrating capabilities like artificial intelligence, Internet of Things, and advanced robotics, manufacturers can operate with greater efficiency. The importance of these technologies stems from their ability to respond to consumer demands swiftly and adapt to changes in the competitive landscape.
Artificial Intelligence and Machine Learning
Artificial intelligence (AI) and machine learning (ML) are at the forefront of smart manufacturing. AI facilitates decision-making by processing vast amounts of data, enabling predictive insights that can lead to more informed choices. For instance, AI algorithms can analyze historical production data and predict equipment failures before they occur, allowing for timely interventions.
Machine learning enables systems to learn from data patterns and improve over time. This creates a feedback loop that enhances productivity. Automated quality inspection systems powered by ML can reduce defects substantially, improving product consistency.
Key benefits of incorporating AI and ML include:
- Predictive analysis for maintenance and operation.
- Optimized supply chain management through real-time data processing.
- Enhanced customer engagement via personalized products and services.
Internet of Things (IoT) Integration
The Internet of Things (IoT) is crucial in connecting machines, devices, and systems, allowing for seamless communication. IoT devices collect and exchange real-time data, leading to informed decision-making. Manufacturers can employ IoT sensors to monitor equipment performance and track processes, making operations more transparent and manageable.
The integration of IoT improves:
- Workflow efficiency by reducing downtime through automatic alerts.
- Resource management by optimizing inventory levels.
- Data visibility, leading to quicker response times to any operational challenges.
Furthermore, IoT can create a feedback mechanism between consumers and manufacturers, enabling customization and more effective product development based on customer usage data.
Advanced Robotics and Automation
Advanced robotics is transforming the landscape of manufacturing by automating repetitive and time-consuming tasks. Robots designed with AI capabilities are more flexible and can adapt to various production lines. This leads to improved accuracy and speed in tasks like assembly, painting, and packaging.
An important aspect of advanced robotics is collaborative robots, or cobots, that work alongside humans. They enhance productivity without eliminating jobs. Instead, they allow human workers to focus on more complex tasks that require creativity and problem-solving.
Benefits include:
- Increased production rates due to efficient automation.
- Improved safety by handling hazardous materials and tasks.
- Cost reductions in long-term labor expenses.
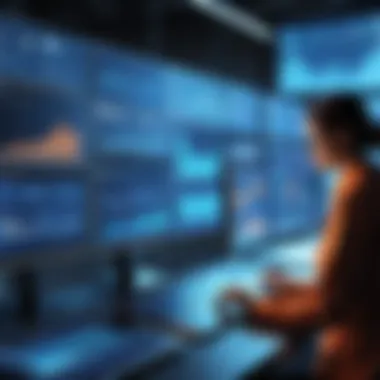
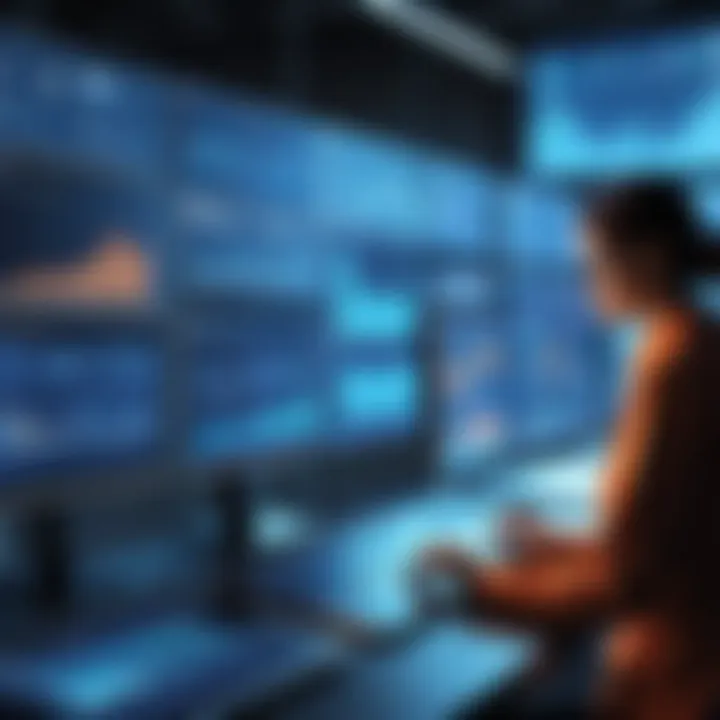
As smart manufacturing continues to evolve, understanding and implementing these core technologies effectively will be imperative for organizations that aspire to thrive in a competitive market.
The Role of Data Analytics
In the realm of smart manufacturing, data analytics emerges as a pivotal element. It empowers organizations to harness vast amounts of data generated during production processes. Understanding how to effectively analyze this data is critical for optimizing operations and enhancing decision-making capabilities.
Big Data in Manufacturing
The term "Big Data" refers to the massive volume of data, both structured and unstructured, that companies generate daily. In manufacturing, this data can originate from multiple sources, such as machinery, supply chains, and customer interactions. By employing advanced data analytics tools, manufacturers can extract valuable insights from this data. This allows them to identify inefficiencies, track production metrics, and forecast trends.
- Data Sources: Key data sources in manufacturing include:
- Production line sensors
- Quality control systems
- Machinery performance records
- Market demand data
Understanding these data points leads to better operational strategies. For instance, manufacturers can reduce waste and optimize resource allocation by analyzing the data generated from their production lines.
- Real-Time Analysis: Another significant aspect is the ability to analyze data in real-time. Immediate insights facilitate prompt adjustments in production processes. This capability is crucial for meeting consumer demands without overproducing, which can strain resources and affect profit margins.
"Harnessing big data in manufacturing not only drives efficiency but also fosters innovation and strategic planning."
Predictive Maintenance and Quality Control
Predictive maintenance is a vital application of data analytics in smart manufacturing. It involves using data from equipment sensors to predict when a machine is likely to fail. By anticipating failures before they occur, companies can avoid costly downtimes and maintain smooth operations.
- Key Benefits: The advantages of predictive maintenance include:
- Quality Control: Data analytics also plays a significant role in ensuring product quality. By analyzing data from production batches, companies can identify patterns that lead to defects. This proactive approach enables manufacturers to rectify issues before they escalate, enhancing overall product consistency.
- Reduced unplanned downtime
- Lower maintenance costs
- Extended equipment lifespan
Benefits of Smart Manufacturing Systems
Smart manufacturing systems bring numerous benefits that are essential for modern industrial practices. The integration of advanced technologies leads to optimized processes, which can significantly enhance operational performance. In this article, we will discuss three primary advantages: increased efficiency and productivity, enhanced product quality and consistency, and sustainability in production.
Increased Efficiency and Productivity
One of the hallmark benefits of smart manufacturing is the substantial increase in efficiency and productivity. Automation technologies, such as robotics and artificial intelligence, streamline numerous manufacturing processes. For example, an automated assembly line can operate for longer periods without breaks, reducing time lost to inefficiencies.
Moreover, data-driven decision-making enables companies to identify bottlenecks in the production cycle. With real-time data analytics, managers can make informed choices that enhance workflow.
- Key points on increased efficiency:
- Reduction in operational downtime.
- Better resource allocation.
- Streamlined communication between machines and systems.
Enhanced Product Quality and Consistency
Quality assurance is a critical concern in any manufacturing setting. Smart manufacturing systems contribute to enhanced product quality through consistent monitoring and precise control. By employing IoT devices, organizations can track production parameters closely.
In implementing predictive analytics, companies can foresee issues before they arise. For example, if a variance in a machine’s performance is detected, timely adjustments can prevent defects in the final product. Furthermore, products manufactured using these systems are often more uniform, leading to satisfied customers and reduced returns.
- Considerations regarding product quality:
- Continual monitoring and adjustments lead to fewer defects.
- Enhanced customization options for customer needs.
- Efficient feedback mechanisms from customers to improve products.
Sustainability in Production
Sustainable practices are increasingly becoming a focal point of manufacturing strategies. Smart manufacturing systems embedded with IoT technology can significantly lower energy consumption and waste production. Automation allows for better energy management and the reduction of material waste throughout the production process.
Adopting smart systems not only advances corporate responsibility but also generates cost savings that contribute to long-term viability. Companies implementing such practices can benefit from:
- Key points on sustainability:
- Reduced carbon footprint.
- Efficient use of resources leads to cost savings.
- Enhanced corporate image and customer loyalty.
"Investing in smart manufacturing technologies is not just a trend but a necessary evolution for industry sustainability and competitiveness."
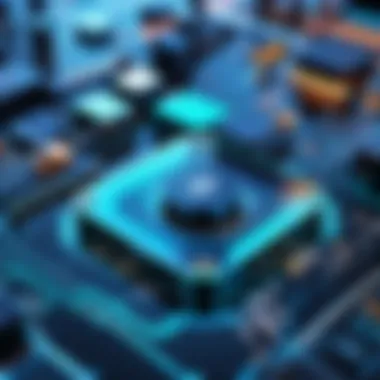
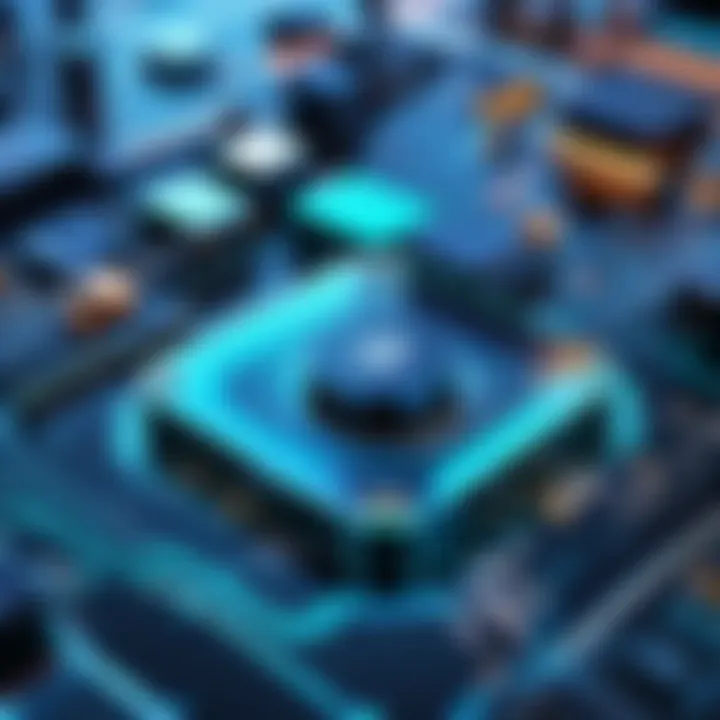
Challenges in Implementing Smart Manufacturing
The transition to smart manufacturing systems represents a significant shift in the operational dynamics of industries. However, this transformation does not come without its challenges. Organizations may encounter various barriers which can impede the implementation process. Recognizing these challenges is crucial for decision-makers and industry leaders. Addressing them head-on can lead to smoother integration processes and overall successful adoption of smart systems.
Integration with Legacy Systems
One of the primary issues in implementing smart manufacturing is the integration with legacy systems. Many manufacturing firms still rely on older technologies that may not seamlessly connect with new smart systems. This dissonance can lead to increased costs and extended timelines in adopting newer technologies.
To effectively tackle this issue, organizations need to evaluate their current systems and outline a clear strategy. Companies can choose several approaches such as:
- Incremental upgrades: Gradually introducing new systems while keeping legacy ones functional.
- Middleware solutions: Utilizing software that facilitates communication between old and new components.
- Total overhaul: Streamlining operations by replacing all outdated equipment with new technologies, albeit with higher initial investment.
A careful assessment and tailored strategy can aid in overcoming the complications posed by legacy integrations.
Data Security and Privacy Concerns
The rise of smart manufacturing inherently raises concerns about data security and privacy. As organizations incorporate IoT devices and fully connect their operations, the volume of data generated increases significantly. This creates vulnerabilities that cybercriminals may exploit. Keeping data secure becomes paramount when sensitive information is at stake.
Implementing robust cybersecurity measures is essential. Some of the critical strategies include:
- Regular software updates: Ensuring that systems are always equipped with the latest security patches.
- Access controls: Implementing strict user authentication and permissions to limit data access.
- Encrypting sensitive data: Using encryption technologies to protect data while stored and during transmission.
Organizations need to be proactive in establishing a strong cybersecurity framework to safeguard their systems against potential threats.
Skilled Workforce Shortage
Another significant hurdle in transitioning towards smart manufacturing is the shortage of a skilled workforce. The new technologies introduced in smart systems demand employees to possess advanced technical proficiencies. Many workers from traditional manufacturing backgrounds may lack the necessary training for these roles. This skills gap can slow down the implementation process and dilute the potential benefits of smart systems.
To address this shortage, companies can:
- Invest in training programs: Developing in-house training sessions tailored to specific technologies.
- Partner with educational institutions: Collaborating with universities and vocational schools to create relevant curricula.
- Promote STEM education: Encouraging a broader interest in science, technology, engineering, and mathematics careers from a young age.
By actively supporting workforce development, companies can close the skills gap and facilitate smoother transitions into smart manufacturing environments.
The successful implementation of smart manufacturing is contingent on addressing the challenges of legacy system integration, data security, and workforce readiness. Taking informed steps in these areas is critical to harnessing the benefits of modern manufacturing systems.
Case Studies: Success Stories in Smart Manufacturing
Case studies play a significant role in understanding smart manufacturing systems. These real-world examples provide valuable insights into how various industries are adopting smart technologies. They highlight successes, challenges, and best practices that can serve as guidance for other organizations.
Understanding these case studies allows decision-makers to see how smart systems can significantly improve operational efficiency and overall productivity. They also showcase the tangible return on investment that can be achieved when leveraging technologies like IoT, AI, and automation. In a rapidly evolving manufacturing landscape, these stories serve to inspire and ensure practitioners are aware of the innovative directions their peers are taking.
Case studies not only reveal the benefits of adopting smart systems but also illustrate the adaptability of these technologies in diverse contexts and sectors.
Industry Leaders Adopting Smart Systems
Some industry leaders are spearheading the adoption of smart manufacturing systems. Companies like Siemens and General Electric have implemented advanced systems that showcase the high impact of integrating technology into manufacturing processes.
Siemens has invested heavily in their digital factory division, employing IoT and AI technologies to optimize production lines. They utilize real-time data analytics to enhance decision-making, streamline processes, and reduce downtime. Their factories employ automation and robotics for repetitive tasks, allowing human workers to focus on complex problem-solving areas. This model not only boosts efficiency but also drives innovation.
Similarly, General Electric has embraced digital transformation through its Predix platform, which connects industrial assets to the cloud. This enables predictive maintenance, which reduces equipment failures and increases uptime. Both Siemens and General Electric serve as benchmarks in the field, illustrating how integrating smart systems can lead to substantial competitive advantages.
Small and Medium Enterprises Implementing Change
While large corporations often dominate discussions around smart manufacturing, small and medium enterprises (SMEs) also benefit significantly from these systems. For instance, a small manufacturing firm in the automotive sector integrated IoT sensors into its production line. This small change allowed real-time monitoring of machinery, leading to a 20% reduction in production time.
SMEs can find unique advantages by adopting smart systems tailored to their specific needs. Tools like market-ready software solutions provide affordable entry points into smart manufacturing, allowing these businesses to enhance productivity without significant upfront investment.
Collaboration with technology partners can also facilitate this transition. Local tech firms often provide bespoke solutions that cater specifically to SME challenges, aligning advanced technologies with their operational realities.
In summary, the path to smart manufacturing is not limited to industry giants. The success stories of SMEs reveal a landscape of opportunity, empowering smaller players to enhance their competitive edge through thoughtful technology adoption.
Current Trends and Future Directions
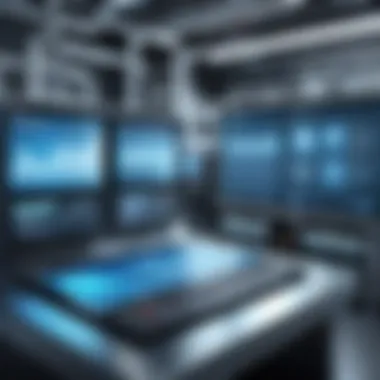
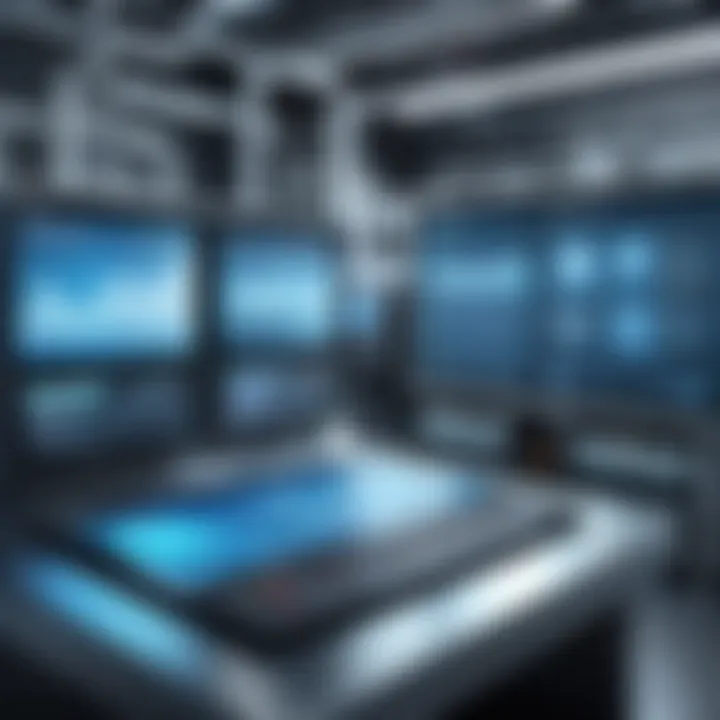
In the fast-evolving landscape of manufacturing, recognizing current trends is crucial to understanding how smart manufacturing systems will shape the future. These trends reflect not only technological advancements but also shifts in consumer demands and environmental considerations. Companies that adapt to these trends can gain a competitive edge and ensure long-term viability.
Emergence of Digital Twins
Digital twins represent a transformative trend within smart manufacturing. This technology involves creating a virtual replica of physical assets, systems, or processes. These twin models are deployed to simulate, analyze, and optimize performance in real-time.
One major benefit of digital twins is their ability to enhance decision-making. By using real-world data and predictive analytics, companies can foresee issues before they occur, leading to reduced downtime and maintenance costs. Moreover, they allow for remote monitoring, which is particularly beneficial when managing complex machinery across multiple locations.
When integrating digital twins, organizations can refine production processes. For instance, manufacturers can simulate different production scenarios to identify the most efficient setups. This was applied successfully by General Electric, which uses digital twins to enhance turbine performance while minimizing operational risks.
Advancements in Cyber-Physical Systems
Cyber-Physical Systems (CPS) are another significant trend in smart manufacturing. These systems bridge the gap between physical processes and computer-based algorithms. CPS enable the seamless interaction between software and hardware, leading to enhancements in operational efficiency.
The integration of CPS enhances flexibility on the production floor. It allows machines to communicate with one another, share data, and respond automatically to changes in their environment. For example, if a specific product demand increases, systems can automatically adjust production lines without the need for human intervention. This adaptability can significantly lower production costs and improve responsiveness to market changes.
Additionally, advancements in CPS contribute to better supply chain management. By leveraging real-time data, organizations can optimize logistics, track inventory levels, and manage resources more effectively.
Policy and Regulatory Aspects
The transformation of industry through smart manufacturing is not solely driven by technology. It is also inherently influenced by policies and regulations that govern the ecosystem in which these technologies operate. Addressing these aspects is crucial for understanding how smart manufacturing systems can be effectively implemented and sustained. Government initiatives, compliance with international standards, and the regulatory framework all play vital roles in shaping the environment that fosters innovation and growth.
"Regulatory frameworks must adapt to the rapid evolution of smart technologies to bolster competitive advantage and ensure sustainable practices."
Government Initiatives Supporting Smart Manufacturing
Governments worldwide are recognizing the need to adapt their strategies to support smart manufacturing. They are initiating various programs aimed at promoting technological advancements and facilitating the transition towards smart manufacturing systems. This includes funding research and development, providing incentives for implementation, and creating educational programs focused on training skilled professionals for the future workforce.
Some essential government initiatives include:
- Financial Incentives: Grants and subsidies to encourage businesses to invest in smart technologies.
- Research Collaborations: Partnerships between industry, government, and academic institutions to drive innovation.
- Infrastructure Development: Investments in upgrading technology infrastructure to support connectivity, such as expanding broadband access for IoT applications.
- Regulatory Support: Streamlining regulations to make it easier for companies to adopt new technologies without excessive compliance burdens.
These efforts not only accelerate the adoption of smart manufacturing but also enhance the competitiveness of nations on a global scale.
International Standards and Compliance
Establishing a robust framework of international standards is pivotal for ensuring that smart manufacturing systems can coexist and thrive in a global marketplace. Compliance with these standards enhances interoperability, safety, and reliability of systems across different sectors. Standards provide uniform guidelines that manufacturers can follow, which in turn fosters trust among consumers and businesses.
Key elements of international standards in smart manufacturing include:
- Interoperability Standards: Ensuring different machines and systems can communicate effectively.
- Safety Standards: Establishing guidelines for the safe operation of automated and robotic systems.
- Quality Assurance Standards: Ensuring products meet certain quality benchmarks throughout the manufacturing process.
- Data Protection Standards: Safeguarding sensitive data in an increasingly interconnected environment.
Adherence to these standards enables companies to align with best practices, improving their operational efficiency and advancing their commitment to quality and safety. Furthermore, regulatory compliance is not just about following rules; it is about building a culture of accountability that ultimately benefits stakeholders at all levels.
Finale
The exploration of smart manufacturing systems reveals their profound impact on the dynamics of modern industry. Through sophisticated integration of technology and innovative approaches, these systems enhance manufacturing efficiency, improve product quality, and foster sustainability. It is essential for decision-makers and industry stakeholders to understand the broader implications of these developments. The transition to smart manufacturing is not merely a shift in technology; it represents a fundamental change in the operational paradigms that govern production processes.
Insights derived from case studies underline that strategic implementation leads to measurable benefits, such as reduced downtime and optimized resource allocation. Companies leveraging smart manufacturing systems position themselves advantageously against competitors, especially in the increasingly volatile global market.
However, it's crucial to recognize the challenges that accompany this transition. Organizations must address potential integration issues with existing legacy systems and prioritize data security. Ensuring a skilled workforce capable of navigating these advanced systems is fundamental for sustained success.
"The Fourth Industrial Revolution fundamentally alters the way one does business, leading to improved competitiveness and efficiency."
In summary, the future of manufacturing lies in smart systems. This article emphasizes the necessity for organizations to adapt to this evolving landscape, embracing innovation as they navigate the complexities of modern production.
Summary of Strategic Insights
Understanding key elements from this article allows decision-makers to glean valuable strategic insights for their manufacturing operations. The adoption of smart manufacturing technologies offers:
- Enhanced Productivity: Systems integrate real-time data analytics for continuous process improvement.
- Quality Assurance: AI and machine learning tools ensure consistent product quality and early issue detection.
- Sustainability Efforts: By optimizing resource utilization, companies can reduce their environmental impact without sacrificing productivity.
- Competitive Advantage: Early adopters can outpace competitors and respond promptly to market demands.
These insights serve as a framework for organizations aiming to harness smart manufacturing's potential for their future projects.
The Future Landscape of Smart Manufacturing
As industries move forward, the future landscape of smart manufacturing will be defined by several emerging trends. Key points to consider include:
- Digital Twins: This technology allows for real-time simulations of physical systems, improving decision-making and reducing time-to-market.
- Expanded IoT Integration: Expectations for more interconnected devices will lead to even smarter operations, facilitating data sharing across the supply chain.
- Increased Focus on Cyber-Physical Systems: This integration of physical processes with computational ones will further advance operational efficiencies and predictive capabilities.
- Regulatory Compliance and Standards: As smart manufacturing grows, adherence to international standards will become increasingly crucial, influencing design and production methodologies.