Exploring the Best Quality Management Systems
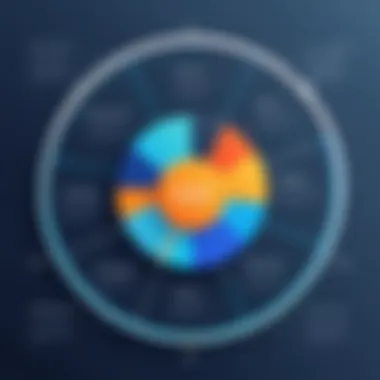
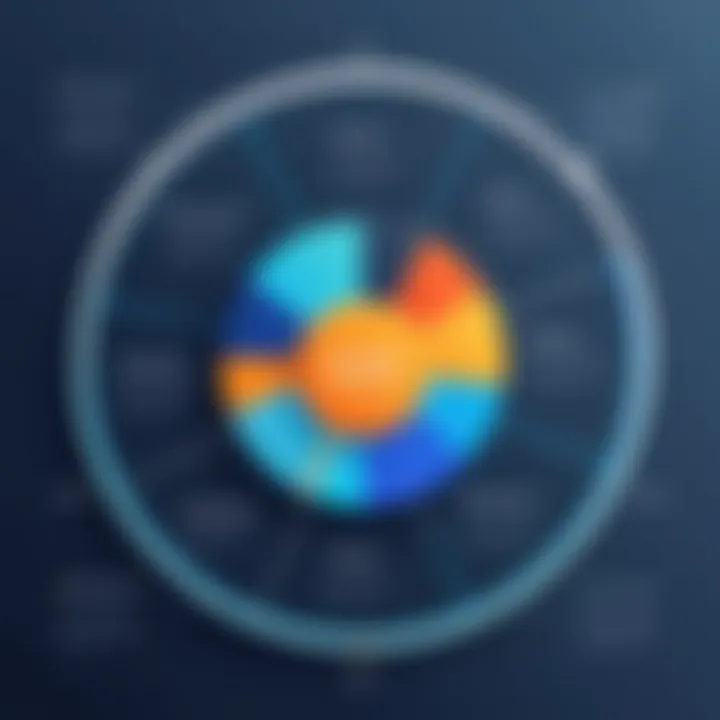
Intro
Quality management systems (QMS) play a critical role in how organizations operate, ensuring that products and services meet established standards. In a rapidly changing business environment, the ability to maintain high quality can be the differentiator for market success. From operating efficiency to customer satisfaction, every aspect is under the lens of quality management.
This guide delves into various systems and frameworks that govern quality management. It will explore essential components, define industry standards, and provide criteria for discerning the best solutions. As you navigate through this guide, you'll gain a comprehensive view of how QMS can enhance operational efficiency and product quality. This knowledge is invaluable for decision-makers and IT professionals looking to optimize their processes.
Key Software Features
Identifying quality management systems requires a look at the core features that contribute to their effectiveness in different industries. The right software not only facilitates compliance with standards but also enhances the overall quality processes.
Essential functionalities
The foundational features of any quality management system include:
- Document Control: Manage and store documents securely, ensuring they are easily accessible.
- Incident Management: Track and resolve quality issues promptly, allowing for constant improvement.
- Audit Management: Facilitate internal and external audits to evaluate compliance.
- Corrective and Preventive Actions (CAPA): Implement processes to address lapses and future risks quickly.
These functionalities serve as the backbone of a robust QMS, providing necessary tools for daily operations.
Advanced capabilities
In addition to essential features, advanced capabilities can significantly benefit organizations. Some notable functionalities are:
- Integration with Other Systems: Seamlessly connect with ERP, CRM, or other software for enhanced data visibility.
- Real-Time Analytics: Leverage data insights to make immediate decisions.
- Mobile Accessibility: Use mobile support to manage quality processes remotely.
- Customizable Dashboards: Allow users to tailor their views for better information management.
The combination of these advanced capabilities leads to better decision-making and a more agile quality management strategy.
Comparison Metrics
When evaluating different quality management systems, employing comparison metrics can illuminate the strengths and weaknesses of each option.
Cost analysis
Assessing cost is essential for decision-making. It includes:
- License fees: Understand the initial purchase cost of the software.
- Maintenance costs: Consider ongoing support and updates.
- Training expenses: Factor in the costs for training staff to use the new system.
- Scalability costs: Analyze how the cost is affected as your organization grows.
Understanding these costs helps businesses allocate resources more effectively.
Performance benchmarks
Performance benchmarks allow decision-makers to assess how well a particular QMS meets their needs. Key benchmarks include:
- User Satisfaction: Surveys or feedback from users can reveal system effectiveness.
- Implementation Speed: Evaluate how quickly the system can be deployed without disrupting operations.
- Error Reduction Rate: Track improvements in product quality over time.
- Regulatory Compliance Levels: Ensure the system consistently meets industry regulations.
These metrics provide a clearer picture of how a QMS aligns with business objectives.
Understanding the key features and metrics of quality management systems enables better organizational decision-making, ultimately affecting profitability and customer satisfaction.
Understanding Quality Management Systems
Quality Management Systems (QMS) are integral to any organization that aspires to improve its efficiency and product quality. Understanding these systems allows decision-makers to appreciate the structured approach to achieving this goal. In today's competitive landscape, organizations must not only deliver high-quality products or services but also demonstrate their reliability and commitment to continuous improvement. This section explores the definition, historical development, and core components that constitute a robust quality management system.
Definition and Purpose
A Quality Management System defines how an organization manages its processes, resources, and responsibilities to consistently provide products and services that meet customer expectations. The primary purpose of a QMS is to enhance customer satisfaction through effective quality management practices. In essence, it aims to ensure that every aspect of production and delivery aligns with defined quality standards. By implementing a QMS, organizations can efficiently address issues, minimize waste, and ensure compliance with regulatory requirements.
Historical Evolution
The evolution of Quality Management Systems is closely tied to the industrial revolution and the increasing need for standardized processes. Early methods focused primarily on inspection and quality control. Over time, this shifted toward a more systematic approach, thanks to the contributions of pioneers like W. Edwards Deming and Joseph Juran. These figures emphasized quality improvement as a collective responsibility. In the latter part of the 20th century, formalized standards such as ISO 9001 emerged. These standards provided a comprehensive framework for organizations across diverse sectors to manage quality effectively.
Key Components
Key components of a QMS play a crucial role in achieving its objectives. Each aspect complements the others to create a cohesive system.
Documentation
Documentation is an essential element of any quality management system. It serves as a roadmap for processes and ensures transparency. Proper documentation aids in maintaining consistent quality and enables organizations to adhere to standards effectively. A key characteristic of documentation is that it provides clear guidelines and procedures that employees must follow. Its benefits include fostering accountability and improving training. However, one potential disadvantage is if the documentation becomes too cumbersome, it may lead to employees bypassing procedures altogether.
Processes and Procedures
Processes and procedures outline the steps necessary to achieve quality objectives. They are critical in ensuring that all tasks are performed in a consistent manner. Having well-defined processes allows the organization to identify areas of improvement and implement corrective actions when needed. Key characteristics include efficiency and repeatability. A significant advantage of streamlined processes is the enhanced ability to monitor and optimize performance. On the downside, if procedures become excessively rigid, they can stifle creativity and flexibility within teams.
Performance Measurement
Performance measurement involves the specification and tracking of metrics to evaluate the effectiveness of the quality management system. This component is crucial for verifying that quality standards are met consistently. A notable characteristic of performance measurement is the use of quantitative data to provide insight into processes. The advantages include facilitating objective assessments and enabling informed decisions regarding resource allocation. However, an overemphasis on metrics can lead to a narrow focus, where qualitative aspects like customer feedback may be overlooked.
"A robust Quality Management System aligns processes with organizational objectives, ensuring a continuous focus on improvement."
Significant Quality Management Standards
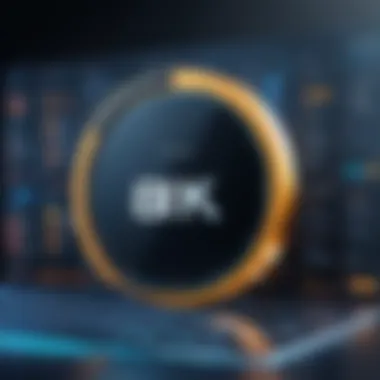
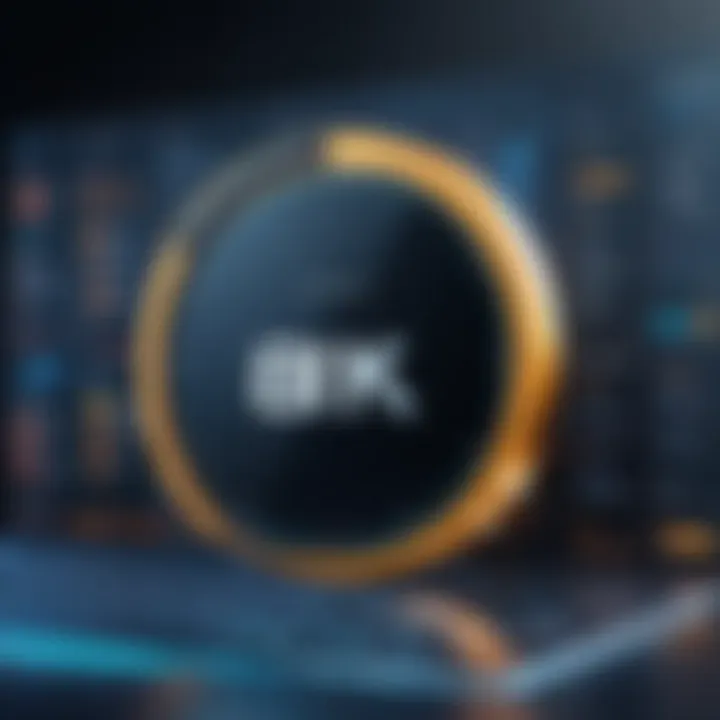
Significant quality management standards play a crucial role in defining and guiding practices that enhance product quality and operational efficiency across various industries. In this article, we explore three major quality management frameworks: ISO 9001, Total Quality Management (TQM), and Six Sigma. Understanding these standards not only provides insight into their structure and intended outcomes but also helps decision-makers align their business strategies to recognized benchmarks of quality.
Each standard addresses specific elements that can benefit organizations immensely. They often guide businesses in their efforts to meet customer expectations, increase efficiency, and minimize waste. Additionally, adhering to these standards can enhance the reputation of the organization, leading to competitive advantages in the market.
ISO Overview
ISO 9001 is perhaps the most recognized quality management standard worldwide. It lays down a clear framework for organizations to manage processes that improve customer satisfaction and ensure continuous improvement.
Key Features of ISO 9001:
- Customer Focus: Prioritizing customer needs helps organizations tailor their products and services effectively.
- Leadership: Strong leadership ensures that quality management is integrated into the strategic framework of the organization.
- Engagement of People: Involving all members of the organization in quality management processes fosters a culture of collaboration.
- Process Approach: Focusing on process efficiency helps organizations streamline operations and identify areas for improvement.
By implementing ISO 9001, companies can enhance internal processes, reduce errors, and ultimately improve customer satisfaction.
Total Quality Management (TQM)
Total Quality Management is an organization-wide approach aimed at continuously improving the quality of products and services. TQM emphasizes the importance of long-term success through customer satisfaction and involves all levels of an organization.
Core Elements of TQM:
- Commitment to Quality: Leaders advocate for quality as a fundamental organizational goal.
- Teamwork: Collaborative efforts among employees foster a sense of ownership in the quality processes.
- Continuous Improvement: TQM encourages ongoing refinement of processes and policies.
- Data-Driven Decision Making: Utilizing data helps in making informed choices regarding quality enhancements.
Unique to TQM is its holistic approach, as it involves every department paying attention to quality matters.
Six Sigma Fundamentals
Six Sigma is a disciplined, data-driven methodology primarily used to eliminate defects in any process—from manufacturing to transactional and from product to service. The goal is to achieve near perfection in performance by understanding and controlling variation.
Essential Components of Six Sigma:
- DMAIC Methodology: This five-phase process—Define, Measure, Analyze, Improve, Control—is central to achieving Six Sigma objectives.
- Data Analysis: Strong emphasis on statistical methods to make informed decisions.
- Cross-Functional Collaboration: Engaging different departments ensures that all aspects of a process are considered.
- Customer Focus: Prioritizing customer requirements determines how quality is gauged.
By adopting Six Sigma practices, organizations can expect substantial improvements in efficiency, reduced costs, and better overall quality.
Each of these standards offers valuable insights into structuring an effective quality management approach, greatly contributing to business success across industries.
Choosing a Quality Management System
Selecting the right Quality Management System (QMS) is critical for any organization aspiring to enhance its operational efficiency and product quality. A well-chosen QMS helps businesses meet their specific needs, maintain compliance with industry standards, and improve customer satisfaction. In this section, we will explore the essential elements involved in this decision-making process.
Identifying Business Needs
The first step in choosing a QMS is to identify your business needs clearly. This involves understanding the unique challenges your organization faces, as well as the objectives you aim to achieve. For example, different sectors have varying compliance requirements. A manufacturing company may need a system that addresses production quality, while a service provider might focus on customer service quality metrics. Conducting a thorough needs assessment enables you to align your selection with specific operational goals and establish measurable criteria for success.
Critical Features to Consider
When evaluating potential QMS options, there are several crucial features to keep in mind. These elements significantly affect how well the system can serve your organization.
Scalability
Scalability is a key aspect of any quality management system. It refers to the ability of the system to grow with your business. As an organization expands, the QMS should be able to accommodate increased processes and new functionalities without requiring a total overhaul. This flexibility makes it a beneficial choice for companies anticipating growth. However, it is important to assess the scalability features carefully. A system that lacks scalability can lead to operational restrictions as your business evolves.
Integration Capabilities
Integration capabilities determine how well a QMS can connect with existing software and systems within your organization. An effective QMS should seamlessly work with tools already in use, such as Customer Relationship Management (CRM) systems or Enterprise Resource Planning (ERP) solutions. This can streamline operations and provide a more holistic view of performance. Lack of integration can create data silos, making it difficult to get a complete picture of operational quality.
User Experience
User experience plays a vital role in the successful adoption of a QMS. A system should be intuitive and user-friendly, allowing employees to navigate it with ease. A well-designed interface can lead to higher user satisfaction and compliance with quality protocols. If users find a system cumbersome, they might underutilize its features, negating its benefits. Therefore, attention to usability is essential for achieving desired results in any quality management initiative.
Vendor Evaluation
Finally, evaluating potential vendors is essential in the selection process. Researching and comparing vendors based on their reputation, customer service, and support offerings gives you insight into which companies can meet your expectations. A vendor's experience in your specific industry can also be a deciding factor. You want a partner that understands the nuances of your market and can assist with customization and implementation. Additionally, reviewing customer testimonials or case studies may provide further clarity on the vendor's reliability and effectiveness.
Implementation Strategies for Quality Management Systems
Implementation strategies are critical for the success of any quality management system (QMS). A well-structured approach ensures that the system aligns with business goals, meets stakeholder needs, and contributes to operational efficiency. Without a solid implementation strategy, organizations may face challenges that hinder their ability to achieve desired outcomes. Therefore, understanding key elements in implementing a QMS can lead to enhanced product quality and overall organizational performance.
Planning for Implementation
Effective planning is the foundation for successful QMS implementation. This involves several steps, which include setting clear objectives, identifying resources, and defining timelines.
Firstly, organizations must clarify their goals. Is the aim to improve customer satisfaction or reduce defects? Identifying specific objectives helps in tailoring the system to meet those targets. Next, resource allocation becomes crucial. This means assessing current capabilities and determining what additional resources are necessary, such as software tools or personnel.
Furthermore, creating a detailed timeline ensures that all stakeholders understand the phases of implementation. A successful plan includes milestones that help track progress, allowing for adjustments if necessary.
Training and Development
Training and development play a significant role in the implementation of a QMS. Employees must understand the system's purpose, how it operates, and their specific roles within it. A well-informed team is more likely to embrace changes and contribute effectively to the QMS.
Training programs should be comprehensive, covering both theoretical aspects and practical applications. This might include workshops, online courses, or hands-on training sessions. Moreover, ongoing development is essential. As systems evolve, so too must the skills of the workforce. Regular updates and refresher courses can aid in maintaining knowledge and adaptability.
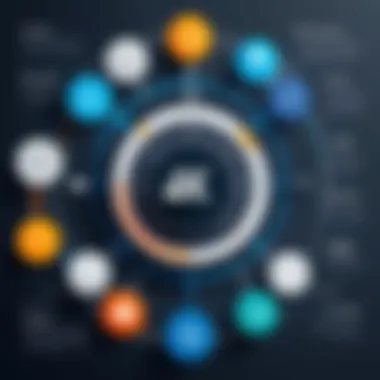
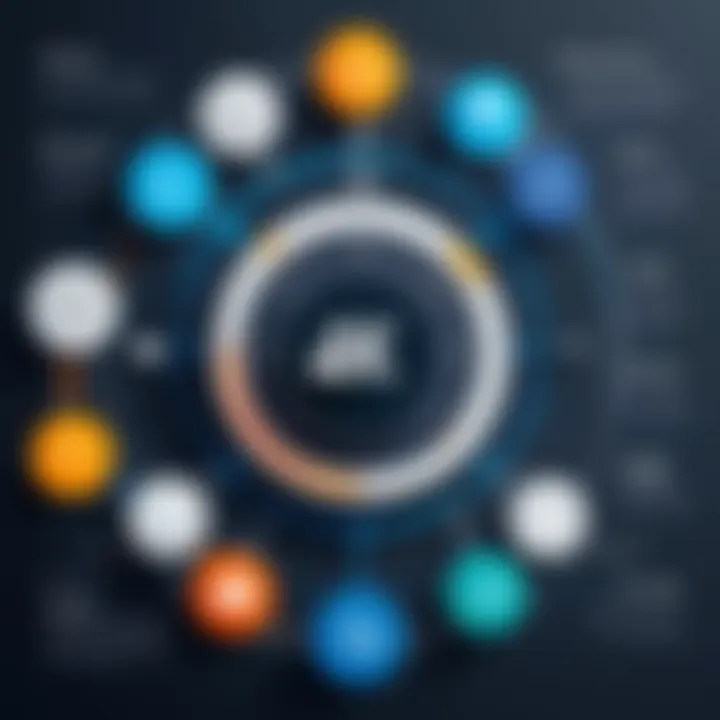
Monitoring Progress
Monitoring progress is vital for assessing the effectiveness of the implemented QMS. This encompasses tracking key performance indicators (KPIs) that relate directly to the goals established during the planning phase. Businesses should regularly collect data to evaluate performance against these KPIs.
Additionally, it is necessary to establish feedback mechanisms. This can involve surveys, regular meetings, or performance reviews to gather insights from employees and customers alike. Such feedback helps identify areas that may require adjustments.
Using a systematic approach for monitoring ensures that organizations can respond to challenges promptly, making it easier to maintain and improve quality standards.
In summary, successful implementation strategies for quality management systems encompass thorough planning, extensive training, and consistent monitoring. Each element contributes to creating a robust environment where quality becomes part of the organizational culture.
Measuring Effectiveness of Quality Management Systems
The assessment of a quality management system's effectiveness is crucial for any organization striving for continuous improvement. Understanding how to measure effectiveness provides insights into operational performance and product quality. Furthermore, it helps in identifying strengths and weaknesses across processes. This section elucidates the various means through which effectiveness can be gauged, highlighting performance metrics, feedback mechanisms, and continuous improvement processes.
Performance Metrics
Performance metrics serve as the foundation for understanding how well a quality management system is functioning. These metrics are quantifiable measures used to evaluate an organization’s success in achieving specific objectives. A few key performance indicators (KPIs) are:
- Defect Rates: This metric measures the number of defects relative to the total number of products produced. Lower defect rates indicate a more effective quality system.
- Customer Satisfaction Scores: This gauge reflects client perceptions and can reveal the success of product quality or service delivery.
- Process Efficiency: Efficiency metrics assess how well resources are utilized in the production process. High efficiency often correlates with a well-functioning quality management system.
To measure these metrics accurately, organizations must implement data collection systems that capture relevant data consistently and analyze them for decision-making.
Feedback Mechanisms
Feedback mechanisms are vital in assessing the transaction quality between an organization and stakeholders. They enable actionable insights through various channels, such as customer surveys, employee suggestions, and quality audits. Here are several critical aspects:
- Surveys and Questionnaires: Regular feedback from customers about products or services assists in identifying potential areas of improvement.
- Employee Input: Gathering insights from employees about processes can unveil inefficiencies and innovative solutions to enhance quality management.
- Performance Reviews: Regular audits conducted internally or externally help ensure compliance and reveal areas needing improvement.
These feedback loops allow businesses to adapt quickly to changing customer needs and operational challenges, ensuring the management system remains relevant and effective.
Continuous Improvement Processes
Continuous improvement is a core principle of quality management. This concept embodies the idea that processes and systems can consistently be enhanced to achieve better performance and outcomes. It involves systematic actions to refine practices and products through:
- Plan-Do-Check-Act (PDCA) Cycle: This iterative process fosters ongoing evaluation and adjustment, leading to measurable improvements.
- Root Cause Analysis: Identifying underlying causes of defects or failures ensures that solutions address the problems at their source rather than merely treating symptoms.
- Employee Training and Development: Investing in skills development ensures that staff members are equipped to implement improvements effectively.
Ultimately, effective quality management systems incorporate performance metrics, feedback mechanisms, and continuous improvement processes to optimize their operations. These elements create a robust framework for ensuring that quality objectives are met, and businesses remain competitive in an evolving marketplace.
"The path to excellence is a continuous journey of improvement that is founded on the basis of measurement and feedback."
To delve deeper into quality management, visit resources like Wikipedia or Britannica.
The importance of measuring effectiveness lies not just in numbers but in fostering a culture of quality and accountability within the organization.
Industry-Specific Applications
The significance of industry-specific applications within quality management systems cannot be overstated. Each sector faces unique challenges and demands that require tailored solutions. Understanding these specifics allows organizations to implement systems that not only comply with general standards but also address particular operational needs. This focused approach results in enhanced efficiency and quality, creating a robust framework for sustained growth and improvement.
Manufacturing Sector
In the manufacturing sector, quality management systems play a critical role in ensuring product consistency and minimizing defects. The traditional manufacturing landscape relies on rigorous processes and stringent quality controls. Implementing a quality management system helps in defining the production process, monitoring output, and identifying areas for improvement.
Benefits of applying quality management systems in manufacturing include:
- Improved Product Quality: Ensures that every product meets the required specifications.
- Operational Efficiency: Streamlines processes, reducing waste and operational costs.
- Regulatory Compliance: Assists in adhering to industry regulations and standards such as ISO 9001.
Healthcare Industry
Quality management systems in the healthcare industry are vital for maintaining patient safety and ensuring the quality of care. By applying these systems, healthcare facilities can implement standardized protocols that safeguard against errors. Systems like Total Quality Management help in fostering a culture of continuous improvement.
Key considerations for the healthcare sector include:
- Patient-Centered Care: Enhances patient experiences and outcomes through standardized procedures.
- Risk Management: Identifies potential risks in healthcare delivery and establishes mitigation strategies.
- Compliance with Standards: Facilitates adherence to healthcare regulations and accreditation requirements.
Service Industry
In the service industry, quality management systems focus on delivering consistent customer experiences. Services are often intangible, making quality more challenging to measure than in manufacturing. However, implementing a solid framework allows businesses to track performance and satisfaction levels.
The following elements are crucial in service sector applications:
- Customer Feedback: Establishes mechanisms for gathering and analyzing customer input for improvements.
- Employee Training: Ensures staff are equipped to deliver quality service consistently.
- Process Standardization: Streamlines service delivery processes to enhance efficiency.
"Quality management systems are not merely tools; they are frameworks that drive organizational excellence across different industries."
By recognizing the specific needs of different sectors, organizations can better position themselves for success in the increasingly competitive market. Understanding how these systems can be tailored to fit unique operational landscapes fosters a culture of quality that permeates every level of an organization.
Challenges in Quality Management
Quality management systems are integral to achieving organizational success. However, they are not without challenges. This section discusses the complexities involved in adopting and sustaining these systems. Understanding these challenges is critical for decision-makers, IT professionals, and entrepreneurs. Encountering obstacles can derail the quality initiatives if not addressed properly. Fostering a robustness in quality management requires cognizance of these challenges. Well-informed stakeholders are better equipped to implement effective strategies for overcoming them.
Common Obstacles in Adoption
Quality management systems often face several hurdles during adoption. Some common obstacles include:
- Resistance to Change: Employees may be reluctant to alter existing processes. Familiarity with current practices can lead to pushback against new methods. This resistance can stymie the implementation of a quality management system.
- Inadequate Training: Effective utilization of a quality management system requires thorough training. Insufficient training can lead to misunderstandings, misuse, and ultimately a failure to leverage the system's potential.
- Resource Constraints: Organizations frequently encounter resource limitations. This includes financial resources, time, or personnel. Lack of adequate resources can impede the successful adoption of quality management systems.
- Poor Communication: A breakdown in communication can hinder the adoption process. Transparency and proper dissemination of information are necessary for all levels of the organization. Without this, misalignments often occur, leading to confusion and failure.
- Misalignment with Company Goals: If the quality management system does not align with a company's strategic objectives, it may struggle for support. Ensuring that the system supports overall business goals is essential for its success.
Limitations of Existing Systems
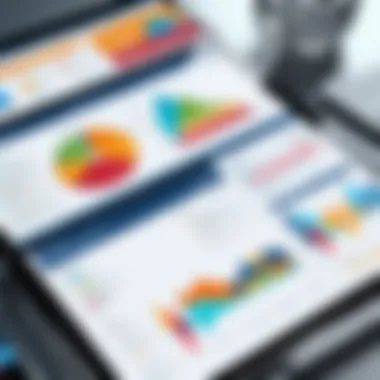
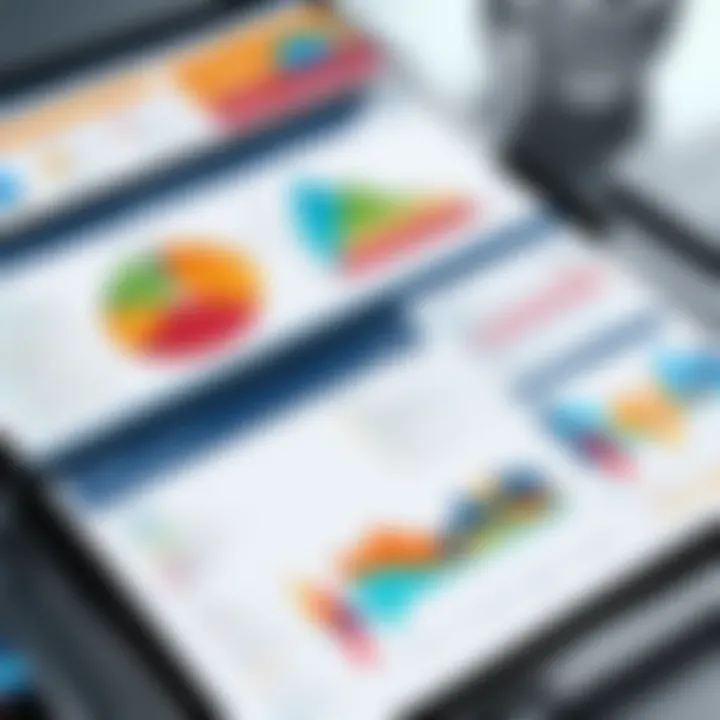
While quality management systems promise enhanced effectiveness, they often have inherent limitations. Some notable limitations include:
- Rigidity: Many existing systems can be too rigid. A lack of flexibility can prevent adaptation to changing market demands or customer needs. Organizations may find themselves stuck in outdated processes, unable to evolve.
- Complexity: Some systems are overly complex and difficult to navigate. This complexity can lead to user frustration and decreased engagement. If users struggle to effectively utilize the system, it will not be maximized to its full potential.
- Integration Challenges: Integrating a quality management system with other business systems can be difficult. Lack of compatibility may lead to gaps in processes and data, undermining the system's efficacy.
- Data Overload: Quality management systems often generate significant data. Without proper data management strategies, organizations can become overwhelmed. This overload can obscure meaningful insights and complicate decision-making processes.
Acknowledging these challenges helps organizations improve their quality management strategies. By addressing obstacles head-on, companies can unlock the full potential of their systems.
Each of these aspects has serious implications for an organization's ability to maintain high standards of quality. Decision-makers must recognize these challenges and strategize accordingly.
Future Trends in Quality Management
Quality management systems constantly evolve. Staying informed about future trends is vital for businesses aiming to maintain high standards and remain competitive. Understanding these trends allows decision-makers to anticipate changes, adapt processes, and leverage emerging technologies for improved efficiency and effectiveness.
Technological Advancements
Technology plays a significant role in shaping quality management practices. Automation tools are taking center stage. These tools streamline processes, reduce human error, and enhance data collection. For instance, software like Minitab and Qualityze facilitates statistical analysis, ensuring that products meet required standards.
Moreover, cloud technology brings flexibility. It allows organizations to access their quality management systems from anywhere. This is particularly important for organizations with multiple locations. By using cloud-based systems, teams can collaborate more effectively and ensure consistent quality across the board.
Mobile applications also streamline quality management. Employees can submit reports or access quality metrics in real-time, leading to faster decision-making. This immediacy is crucial for maintaining quality in fast-paced industries.
Shift Towards Data-Driven Decision Making
The current trend towards data-driven decision-making cannot be overemphasized. Organizations are increasingly relying on data analytics to inform their quality management strategies. Leveraging data helps businesses identify trends, address issues, and validate their approaches to maintaining quality standards.
Utilizing business intelligence tools, like Microsoft Power BI or Tableau, allows companies to interpret large datasets more effectively. These insights lead to informed decisions based on actual performance rather than assumptions.
By adopting data-driven practices, businesses can:
- Improve product consistency through better understanding of production variables.
- Identify areas for improvement quickly, enhancing responsiveness.
- Make informed strategic decisions, aligning quality goals with overall business objectives.
"Data-driven approaches are changing the landscape of quality management. Organizations can now predict quality issues before they arise, reducing waste and improving customer satisfaction."
Case Studies of Successful Implementation
Case studies are essential in understanding the tangible benefits of Quality Management Systems (QMS). They provide real-life examples that can demonstrate the effectiveness of various QMS strategies in different industries. Analyzing these cases offers valuable insights that can guide decision-makers in their pursuit of operational excellence. Successful implementations showcase how a structured approach to quality can lead to improved processes, enhanced customer satisfaction, and greater overall efficiency.
Analysis of an Automotive Manufacturer
Consider the example of Toyota, a leader in the automotive industry known for its commitment to quality. The company's implementation of the Toyota Production System (TPS) is a prime case study in effective quality management. The TPS emphasizes lean manufacturing principles, which focus on eliminating waste without sacrificing productivity.
Key elements of this QMS include:
- Just-in-Time Production: This approach minimizes inventory costs and enhances responsiveness to market demands.
- Continuous Improvement (Kaizen): Toyota encourages every employee to look for ways to improve processes incrementally. This philosophy has led to significant advancements in operational efficiency.
- Standardized Work Processes: By documenting processes, Toyota ensures consistency and quality across all production lines.
The results of these practices have been remarkable. Toyota has enjoyed a high level of customer satisfaction. Its vehicles often rank highly in reliability, largely due to its focus on quality management. The success of the TPS illustrates the importance of tailoring QMS to the specific needs and nuances of the automotive sector, making it a reference point for others in the industry.
Evaluation of a Healthcare Provider
In contrast, the implementation of QMS in the healthcare sector can be illustrated through the case of Cleveland Clinic, an institution renowned for its commitment to quality patient care. The clinic developed its quality management approach by focusing on evidence-based practices, robust training programs, and comprehensive feedback systems.
Key components of Cleveland Clinic’s quality management system include:
- Patient-Centered Care: The clinic focuses on understanding and prioritizing the needs and preferences of patients while delivering services.
- Quality Metrics: Cleveland Clinic employs various performance indicators to monitor and evaluate the quality of care provided. This allows for real-time adjustments to services and treatments.
- Staff Training: Investments in training ensure that staff members are well-equipped with the skills necessary for delivering high-quality care.
As a result of these practices, Cleveland Clinic has reported improvements in patient outcomes and satisfaction rates. Their experience underscores the significance of a tailored quality management approach in healthcare settings, where the stakes are particularly high.
Case studies such as those of Toyota and Cleveland Clinic illustrate not just the implementation of QMS but also highlight the diversity in application across different industries. They reveal the potential challenges and successes that come with striving for quality, offering a roadmap for organizations aiming to enhance their own quality management strategies.
Epilogue and Next Steps
In any comprehensive exploration of quality management systems, the concluding section serves a crucial role. It allows readers to consolidate their understanding while providing actionable insights that can influence decision-making processes.
The importance of a conclusion cannot be understated. It ties together the various threads of the discussion, reaffirming the key points made throughout the article. By summarizing what has been discussed, professionals can better remember the essential elements of quality management. Additionally, it highlights the practical applications of the knowledge gained, rendering it more relatable to real-world scenarios.
Summary of Key Insights
Effective quality management systems are not merely regulatory requirements; they represent a strategic approach for organizations looking to improve efficiency and product quality. Some key insights include:
- The foundational principles of quality management, which stress customer satisfaction and continual improvement.
- Different frameworks, such as ISO 9001 and Total Quality Management, offer varying levels of flexibility and structure, catering to diverse industry needs.
- The role of technological advancements in streamlining quality processes enhances performance measurement.
These insights will form the backbone of decision-making in selecting the right system for a given business context.
Recommendations for Businesses
Organizations seeking to implement or improve their quality management systems should consider the following recommendations:
- Align Quality Goals with Business Objectives: Ensure that the quality management objectives are tailored to fit within the broader mission of the organization.
- Invest in Training and Development: Regular training for employees on quality principles will foster a culture of quality awareness.
- Embrace Continuous Improvement: Create a learning environment where feedback is valued, and processes are regularly reviewed for efficiency enhancements.
By adhering to these principles, businesses can cultivate systems that not only meet but exceed quality expectations.
Resources for Further Learning
For those looking to deepen their understanding of quality management systems, the following resources are helpful:
- Wikipedia: For an overview of various quality management standards and their evolution. Wikipedia on Quality Management
- Britannica: Offers detailed articles on the historical development of quality management frameworks. Britannica on Quality Management
- Reddit: The community often discusses real experiences regarding quality management implementation in various sectors. Reddit on Quality Management
By engaging with these resources, professionals can stay updated on the latest trends and best practices in quality management.