PLM Quality Management: Elevate Standards in Product Lifecycle
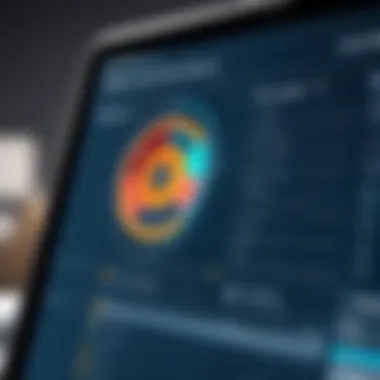
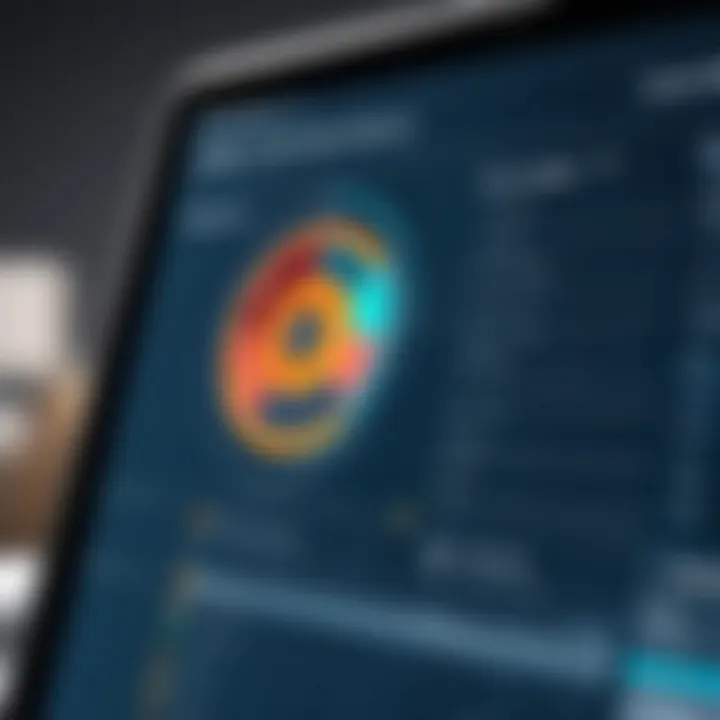
Intro
In recent years, the landscape of Product Lifecycle Management (PLM) has seen a notable transformation, largely driven by advances in technology and globalization. Quality management is an integral component of this evolution, becoming a foremost element that shapes product development strategies. Understanding the dynamics between PLM and quality management is essential for organizations striving to enhance product efficacy and meet regulatory requirements.
Quality management involves systematic processes that define, measure, and improve product quality throughout its lifecycle. It ensures that every stage, from inception to delivery, meets established standards and requirements. This impact permeates through all departments, influencing production, marketing, and even customer satisfaction. The ability to integrate quality management within PLM frameworks is what allows organizations to foster continuous improvement and embrace a culture of excellence.
As we delve into this article, we will explore key software features, comparison metrics, and best practices. We will examine how modern quality management systems can elevate PLM standards and provide organizations with the tools necessary to excel in a competitive market. This discourse aims to furnish decision-makers, IT professionals, and entrepreneurs with actionable insights that can drive their strategic initiatives.
Understanding how quality management can be implemented effectively within PLM systems will not only benefit organizational performance but also enhance product quality in ways that satisfy both regulatory mandates and consumer expectations. This synthesis of knowledge is crucial for any entity aiming to sustain a leading edge in product development and service delivery.
"Quality management is not an act; it's a habit that must be incorporated into every process."
As we progress through the article, we will illuminate how the confluence of quality management and PLM can become a catalyst for growth and innovation.
Prolusion to PLM Quality Management
In today’s competitive landscape, the integration of Quality Management within Product Lifecycle Management (PLM) is crucial. As organizations strive to develop products more efficiently while maintaining high standards, the intersection of quality and lifecycle management becomes a focal point. Effective management of quality ensures that products not only meet customer expectations but also conform to regulatory standards. This article delves into PLM Quality Management and highlights various frameworks, methodologies, and tools that contribute to enhancing product quality.
Understanding Product Lifecycle Management
Product Lifecycle Management involves the process of managing a product from its inception to its discontinuation. This approach encompasses several stages, including concept development, design, manufacturing, and retirement. Understanding each stage is vital, as it allows businesses to identify potential quality issues early in the process.
Integrating quality management into PLM means establishing control measures at each phase. It ensures that quality standards are not treated as an afterthought. Instead, they are embedded into the product's development right from the start. This proactive approach minimizes risks and enhances customer satisfaction.
The Role of Quality Management in PLM
Quality management plays a critical role in reinforcing the objectives of PLM. It ensures that products are compliant with specified requirements. In this context, quality management is not solely about defect control; it encompasses planning, assurance, and improvement strategies.
For decision-makers, quality management in PLM provides several key benefits:
- Consistency: Establishing uniform processes helps maintain consistent product quality.
- Risk Reduction: By identifying quality issues early, organizations can mitigate risks that may arise during product development.
- Compliance: Adhering to industry standards and regulations is facilitated through effective quality management processes.
- Customer Satisfaction: High-quality products lead to increased customer trust and loyalty, impacting the bottom line positively.
In summary, PLM Quality Management elevates standards significantly. It serves as a tool that drives efficiency, ensures compliance, and ultimately leads to improved product quality. Understanding its importance not only aids in better product development but also aligns quality objectives with the overall strategy of the organization.
The Fundamentals of Quality Management
Quality management serves as the backbone of effective product lifecycle management (PLM). It is not merely about ensuring a product meets specifications but encompasses a holistic approach that impacts everything from design to customer satisfaction. In today's market, where competition is so fierce, businesses need to adopt a robust quality management framework to remain relevant.
Implementing quality management principles offers several distinct benefits. Firstly, it fosters consistency across processes, ensuring that every output maintains a certain standard. This is crucial in industries where product failure can have significant repercussions. Furthermore, a strong quality management system (QMS) can lead to improved operational efficiency. By identifying and eliminating waste, organizations can reduce costs and enhance profitability.
Moreover, integrating established quality principles leads to a proactive approach to problem-solving. Rather than reacting to defects post-production, organizations equipped with a solid QMS can anticipate issues and implement corrective actions beforehand. This shift not only optimizes the product quality but also builds trust with stakeholders and customers.
Quality Management Principles
Quality management is built on several core principles that guide organizations in their quest to meet and exceed client expectations. These principles include:
- Customer Focus: Understanding and meeting customer needs should be prioritized. All processes must align with delivering value to customers.
- Leadership: Strong leadership is essential in creating a unified direction and fostering an environment conducive to quality.
- Engagement of People: Involving all stakeholders, from management to end-users, encourages accountability and enhances quality consciousness.
- Process Approach: Quality management should focus on processes as activities that transform inputs into outputs, facilitating efficiency and predictability.
- Continual Improvement: A commitment to ongoing improvement is essential. This might include regular assessments and the adoption of new best practices.
These principles are not isolated but are interconnected, creating a systemic framework that contributes to effective quality management.
Key Quality Management Standards
Adhering to established quality management standards is crucial for organizations striving for excellence in PLM. Notably, the International Organization for Standardization has articulated various standards that organizations can adopt in their quality management practices. Prominent among these are:
- ISO 9001: This is one of the most recognized standards globally, focusing on the effectiveness of a quality management system. It emphasizes meeting customer requirements and ensuring a culture of continual improvement.
- ISO 13485: This pertains specifically to the medical device industry, highlighting the need for organizations to demonstrate their ability to provide medical devices that consistently meet regulatory and customer expectations.
- Total Quality Management (TQM): This philosophy integrates all members of an organization in enhancing processes, products, services, and the culture in which they work.
Implementing these standards not only fuels quality improvement efforts but also aids in compliance with regulatory requirements, ultimately enhancing credibility and market competitiveness.
Integration of Quality Management in PLM
The integration of quality management into Product Lifecycle Management (PLM) is crucial. It ensures that quality control processes are not only implemented but are also aligned with the overall product strategy. In today's competitive market, businesses must deliver high-quality products consistently while minimizing costs. Quality management becomes a lynchpin in achieving this objective. This integration influences various dimensions of product development, from concept to market launch and beyond.
Quality management establishes structured methodologies and standards that guide organizations. By embedding these practices within the PLM framework, companies can proactively address quality-related challenges. This approach fosters a culture of quality within the organization, leading to more effective decision-making and efficient processes. Moreover, it aligns objectives across departments, ensuring that everyone is moving toward the same end goals.
Aligning Quality Objectives with PLM Strategy
Aligning quality objectives with the PLM strategy allows organizations to establish clear performance indicators that reflect both quality standards and business goals. This alignment is not just about setting high quality benchmarks but also ensuring everyone understands the role they play in achieving these targets. It promotes accountability across teams and enhances collaboration.
To effectively align these objectives, organizations should:
- Define specific quality metrics that tie directly to PLM objectives.
- Ensure all stakeholders are aware of these metrics and their significance.
- Regularly review and update quality objectives to reflect changes in market trends and technology.
This strategic alignment provides a framework for continuous assessment. When quality objectives are integrated into the primary business strategy, it becomes easier to identify areas for improvement. Additionally, it fosters resource allocation that enhances product quality.
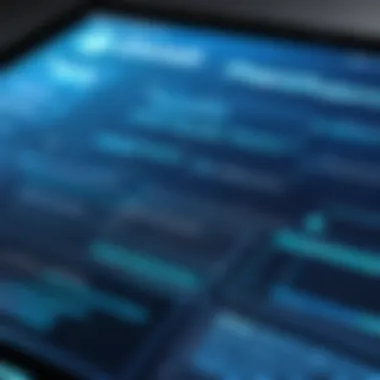
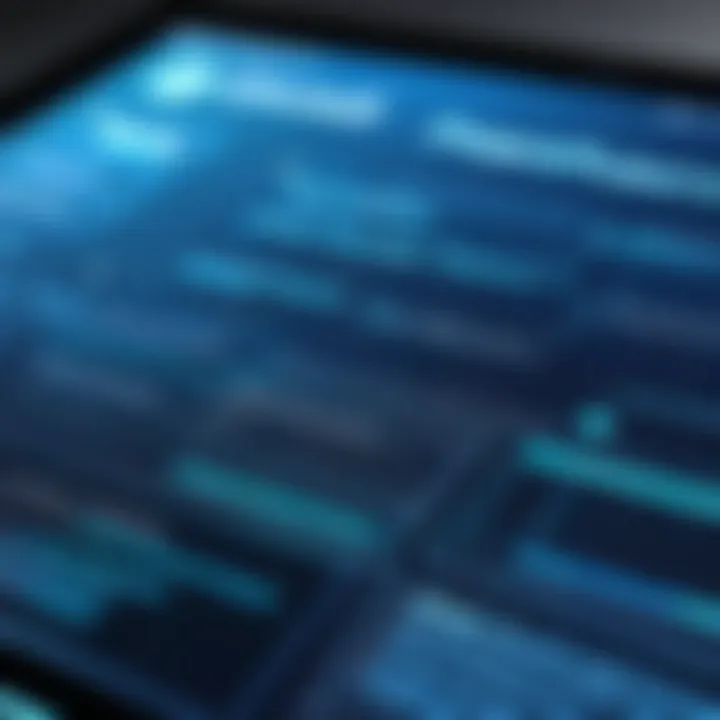
Frameworks for Quality Integration in PLM
There are various frameworks that facilitate the integration of quality management within PLM systems. Each framework emphasizes different aspects of quality but shares the common goal of enhancing product integrity throughout its lifecycle.
Some notable frameworks include:
- Total Quality Management (TQM): TQM focuses on long-term success through customer satisfaction. Implementing TQM within PLM ensures that every phase of product development is scrutinized for quality.
- Lean Manufacturing: This framework emphasizes waste reduction while improving product quality. Integrating lean principles within PLM helps organizations streamline operations and enhance efficiency without sacrificing quality.
- Six Sigma: This data-driven approach focuses on reducing defects and ensuring consistency. By embedding Six Sigma practices into PLM, organizations can make informed decisions based on statistical analysis.
These frameworks offer structured guidelines that can be adapted to various organizational needs. By choosing the most appropriate framework, companies can strengthen their quality management systems and achieve higher levels of excellence in their PLM processes.
In summary, the integration of quality management in PLM is a strategic necessity for organizations aiming for sustainable success. It enhances product excellence, fosters collaboration across teams, and prepares businesses for future challenges.
Quality Control Techniques in PLM
Quality control techniques play a crucial role in Product Lifecycle Management (PLM) by ensuring that products meet specific standards of quality throughout their development and execution. Implementing effective quality control practices can prevent issues, increase customer satisfaction, and ultimately enhance productivity. Organizations committed to maintaining quality recognize these techniques as foundational tools that align with their strategic goals. As products evolve, the complexities surrounding them also increase, making the integration of robust quality control a necessary pursuit.
Adoption of quality control techniques has specific benefits that address both operational and strategic layers. They assist in identifying defects early, thus reducing rework and saving costs. These techniques also foster a culture of continuous improvement by engaging teams in quality discussions and encouraging them to propose enhancements. Furthermore, they provide stakeholders with key insights into product performance, which informs decision-making processes.
Statistical Process Control in PLM
Statistical Process Control (SPC) is one of the most widely used quality control techniques in PLM. It involves using statistical methods to monitor and control a process to ensure it operates at its full potential. The essence of SPC lies in its ability to detect variations in the production process, allowing organizations to separate common causes from special causes of variation. This differentiation enables businesses to determine whether variations are normal or indicative of underlying issues that need attention.
The implementation of Statstical Process Control includes several specific elements:
- Data Collection: Gather relevant data from various stages of the product lifecycle.
- Control Charts: Utilize control charts to visualize and analyze variability in processes.
- Process Analysis: Analyze the data to identify trends or patterns that may signal quality problems.
- Corrective Actions: Implement corrective actions to address identified issues promptly.
Organizations employing SPC benefit from a proactive approach to quality. They can react to changes in real-time, reducing the risk of escalating defects. Moreover, through consistent monitoring, companies can optimize their production processes, thereby improving overall efficiency and reducing costs over time.
Standard Operating Procedures for Quality Assurance
Standard Operating Procedures (SOPs) provide an essential framework of documented processes that organizations use for quality assurance in PLM. These procedures serve to create consistency in operations, detailing every step necessary to achieve product quality objectives. SOPs also encompass training requirements, safety protocols, and compliance benchmarks, ensuring that all team members are aligned.
Key components of effective SOPs include:
- Clarity: Procedures should be written in simple, clear language that facilitates understanding.
- Accessibility: Make SOPs easily accessible to all relevant personnel, ensuring they can reference them as needed.
- Regular Reviews: Schedule regular reviews to ensure they remain relevant and up-to-date with current practices and regulations.
By utilizing SOPs, companies can ensure that each operational step adheres to predetermined quality standards. This adherence minimizes errors, promotes accountability, and enhances compliance with regulatory requirements.
"Quality is not an act, it is a habit."
Ultimately, the adoption of quality control techniques such as SPC and SOPs is a strategic necessity for companies engaged in PLM. They not only streamline processes but also enhance product integrity, providing a structured approach to maintaining high standards. Organizations equipped with these tools are better positioned to navigate the complexities of product development while achieving their quality objectives.
Technological Advancements in Quality Management
Technological advancements in quality management are vital for improving processes in Product Lifecycle Management (PLM). These advancements transform how organizations approach quality, providing new tools and methodologies that enhance product standards. As firms strive for excellence, understanding these technologies is essential.
Role of Software Solutions in Quality Management
Software solutions play a crucial role in modern quality management systems. They provide platforms for documentation, process mapping, and compliance tracking. With tools like SAP Quality Management or Siemens Teamcenter, organizations can automate inspections and quality checks, effectively minimizing human error.
Key benefits include:
- Improved Accuracy: Automation reduces the risk of mistakes.
- Real-Time Monitoring: Organizations can monitor quality standards constantly and make timely adjustments.
- Data Analytics: Software solutions analyze data trends, providing insights into quality issues. This helps in predicting potential problems.
- Integration: Many software solutions integrate well with existing PLM systems, preserving data integrity and ensuring a smooth workflow.
With these tools, decision-makers can prioritize quality management tasks based on data-driven evidence rather than assumptions or intuition.
Emerging Technologies Enhancing Quality in PLM
Several emerging technologies are set to redefine quality management in PLM. Machine learning, Internet of Things (IoT), and advanced analytics are transforming existing models.
- Machine Learning: Through machine learning algorithms, systems can learn from previous data, identifying patterns that lead to quality failures. This predictive capability allows organizations to implement preventive measures.
- Internet of Things (IoT): IoT devices can monitor products in real time during the manufacturing process. Sensors can track various parameters like temperature, humidity, or vibration. This data is used to adjust processes as needed and ensures that quality standards meet regulatory requirements.
- Blockchain: In terms of traceability, blockchain technology provides a secure and tamper-proof ledger. This feature is beneficial for industries where tracking the product journey is critical for quality assurance.
"Technological advancements reshape the future of quality management, embedding intelligence in processes to assure standards."
Combining these technologies provides organizations with a comprehensive view of their product quality. The integration of smart systems optimizes workflows and enhances communication across departments.
In the fast-evolving landscape of PLM, understanding and adopting these technological advancements can make a substantial difference in achieving consistent quality standards. By leveraging software solutions and emerging technologies, companies can elevate their quality management systems and consequently, their overall success.
Metrics and KPIs for Quality in PLM
In the context of Product Lifecycle Management (PLM), metrics and Key Performance Indicators (KPIs) serve as essential tools for measuring and enhancing quality. By defining and analyzing specific quality metrics, organizations can gain insights into their processes and identify areas for improvement. This understanding allows them to align their goals with broader business objectives, ensuring that quality remains a focal point throughout the product lifecycle.
Establishing robust metrics aids decision-makers in tracking product performance and compliance with regulatory standards. Metrics can encompass various dimensions of quality, such as defect rates, customer satisfaction scores, and adherence to standards. A focus on these measurements not only drives internal improvements but also enhances customer trust and satisfaction.
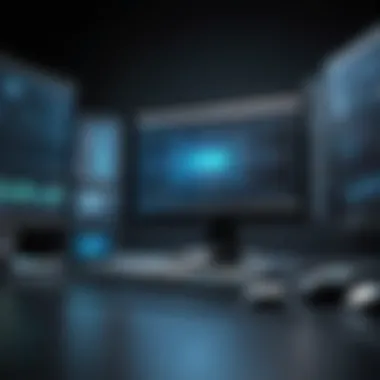
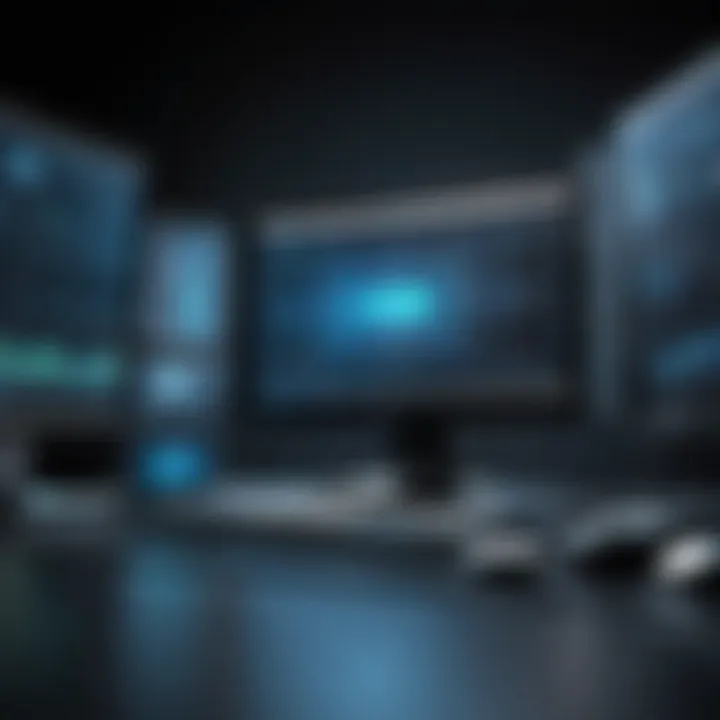
Defining Quality Metrics in PLM Systems
Quality metrics in PLM systems are quantifiable measures used to evaluate various aspects of a product's lifecycle from conception to delivery. Defining these metrics is critical as they guide organizations in their quality assurance efforts. Common quality metrics include:
- Defect Density: The number of defects per unit of product, providing insight into production quality.
- Return Rate: The percentage of products returned by customers, highlighting potential issues in design or production.
- Cycle Time: The time taken from idea inception to product launch, indicating efficiency in product development.
- First Pass Yield: The percentage of products manufactured correctly without rework.
Each of these metrics informs organizations about specific performance areas that may require attention. The presence of clear quality metrics helps in establishing accountability, fostering a proactive approach to quality management. When stakeholders can monitor these metrics effectively, it leads to informed decision-making that enhances overall product quality.
Evaluating Performance through KPIs
KPIs function as strategic tools that help organizations measure their effectiveness in achieving quality objectives. These indicators provide critical feedback on the interplay between quality efforts and organizational goals. Examples of relevant KPIs in PLM include:
- Customer Satisfaction Index: Gauges how well products meet customer expectations, reflecting the effectiveness of quality initiatives.
- Quality Improvement Rate: Measures the percentage decrease in defects over time, indicating the success of quality enhancement strategies.
- Regulatory Compliance Rate: Tracks adherence to industry regulations, which is crucial in maintaining quality standards and avoiding penalties.
By consistently monitoring these KPIs, organizations can evaluate their performance and make necessary adjustments to their quality management processes. This ongoing evaluation not only promotes a culture of continuous improvement but also aligns quality management strategies with broader business objectives.
Metrics and KPIs are not just numbers; they represent the quality journey that organizations undertake. By leveraging these tools effectively, businesses can elevate their standards in PLM, ensuring lasting impacts on product excellence.
Continuous Improvement and Quality Management
Continuous improvement is essential in the realm of quality management within Product Lifecycle Management (PLM). It refers to ongoing efforts to enhance products, services, or processes through incremental improvements. The significance of this topic cannot be overstated. In today's rapidly evolving market, organizations must be agile and adaptable. Continuous improvement ensures that quality remains a priority throughout every stage of the product lifecycle. It fosters a culture where innovation thrives and where teams are encouraged to identify areas for enhancement. This process not only increases efficiency but also elevates the overall quality of the products.
Implementing Continuous Improvement Models
Organizations can utilize various models to implement continuous improvement successfully. Among the most recognized are Lean, Six Sigma, and the PDCA (Plan-Do-Check-Act) cycle. Each model offers distinct approaches to identifying waste and variation, contributing to overall quality control.
- Lean focuses on maximizing value by eliminating waste. This principle applies to processes, materials, and time, leading to smoother workflows.
- Six Sigma centers on reducing defects and variability by using data-driven methodologies. It relies heavily on statistical analysis to pinpoint and eliminate sources of errors.
- PDCA Cycle is a straightforward framework for systematic improvement. Organizations can plan changes, implement them, check the results, and act on what they learn to foster ongoing enhancement.
Implementing these models requires a commitment from all levels of management. Staff training and engagement are central to the success of continuous improvement initiatives. Thorough understanding and application lead to a more quality-centric culture.
The Importance of Feedback Loops
Feedback loops are vital components of continuous improvement strategies. They allow organizations to collect data regarding the effectiveness of quality measures. Through consistent feedback, businesses can make informed decisions about necessary changes.
- Real-time data helps identify issues as they arise,
- Customer feedback provides insight into product performance and user satisfaction,
- Internal audits can serve as checks to ensure compliance with quality standards.
A robust feedback system enables quick corrective actions and minimizes the risk of recurring issues. This leads to enhanced product quality and customer satisfaction over time.
"Continuous improvement is better than delayed perfection." - Mark Twain
Feedback should not only focus on failures but also celebrate successes. This balanced perspective encourages teams to remain engaged in the improvement process. When employees see the importance of their contributions and the effects on quality, they are more likely to remain motivated and proactive. Hence, feedback loops serve as a guiding framework for sustaining quality initiatives in PLM.
Regulatory Compliance and Quality Management
Regulatory compliance is an integral aspect of quality management in Product Lifecycle Management (PLM). As organizations navigate the complexities of product development, they must adhere to a myriad of regulations that govern safety, quality, environmental impact, and data protection. These regulations vary by industry and region, making the landscape particularly challenging for global operations.
Ignoring regulatory requirements can lead to severe repercussions, including financial penalties, product recalls, and irreparable damage to a company’s reputation. Elevating standards in PLM through compliance not only mitigates risks but also enhances product quality and fosters customer trust. Companies that prioritize compliance cultivate a culture of accountability and continuous improvement, essential for long-term success.
Understanding Regulatory Requirements in PLM
In the realm of PLM, understanding regulatory requirements is not just about meeting standards; it's about integrating those requirements into the core processes of product development. Organizations must stay abreast of local and international regulations relevant to their products.
Some essential areas to consider include:
- Safety Standards: Ensuring products meet safety regulations is vital. For example, the FDA mandates stringent standards for medical devices, demanding thorough testing and documentation.
- Environmental Regulations: Compliance with environmental laws is increasingly important. Regulations like RoHS or REACH dictate what materials can be used in production.
- Data Protection: With regulations like GDPR, companies must protect consumer data throughout the product lifecycle.
Failing to comprehend these requirements can lead to compliance gaps, risking legal action and damaging consumer trust.
Smart Compliance Solutions
As organizations strive to enhance their compliance efforts, smart compliance solutions are emerging as essential tools in the PLM framework. These solutions leverage technology to streamline compliance processes, reduce human error, and facilitate real-time monitoring.
Some key features of smart compliance solutions include:
- Automated Documentation: Keeping accurate records is crucial. Automated systems can maintain up-to-date documentation that is easily accessible for audits.
- Real-Time Alerts: Advanced systems can provide alerts for compliance updates or potential breaches, allowing for swift corrective action.
- Integration with PLM: Smart compliance solutions can be integrated seamlessly with existing PLM systems, ensuring that compliance is maintained across all stages of the product lifecycle.
"Investing in compliance technologies not only raises the standards of product quality but also positions a company as a responsible player in the market."
Challenges in PLM Quality Management
In the realm of Product Lifecycle Management (PLM), quality management is often not a straightforward task. Numerous challenges can complicate the implementation and maintenance of effective quality management systems. Understanding these challenges is vital for organizations aiming to optimize their PLM practices.
A significant obstacle arises from the dynamic nature of product development. As products evolve, requirements may shift, leading to confusion and misalignment between quality standards and actual practices. This misalignment can result in unforeseen defects or compliance issues.
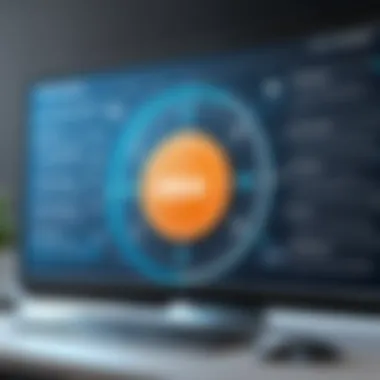
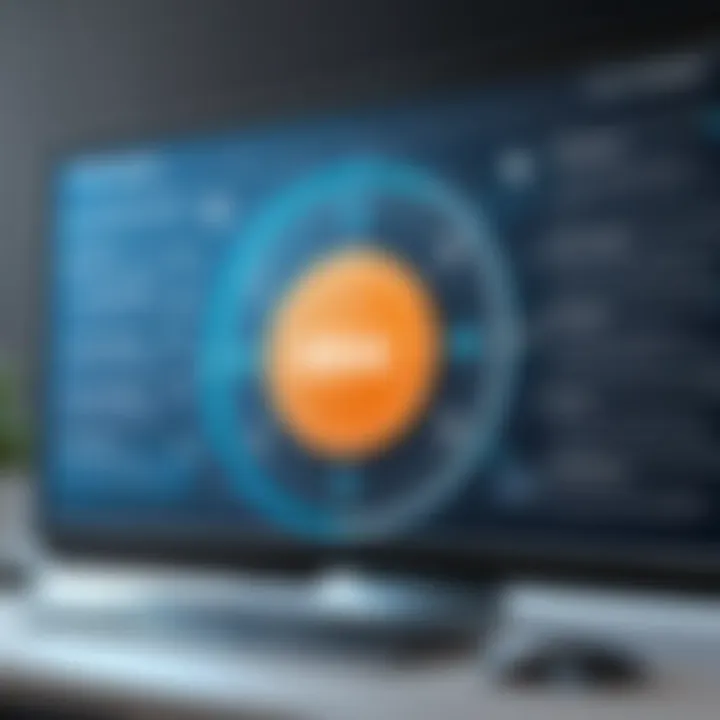
Furthermore, siloed departments can hinder the flow of information necessary for quality assurance. When different teams do not communicate effectively, critical quality data can remain isolated. This isolation prevents a cohesive strategy for quality management and can lead to repeated mistakes.
There is also the challenge of regulatory compliance. Organizations must navigate a complex landscape of regulations that can vary significantly across markets. Keeping track of these requirements and ensuring that all products meet them is a daunting task.
Moreover, the lack of adequate technological tools to monitor and analyze quality can severely limit an organization’s ability to implement effective quality management practices. Many businesses still rely on outdated systems that do not integrate well with modern PLM solutions.
Lastly, organizational culture plays a pivotal role in quality implementation. If there is resistance to change or insufficient training, employees may struggle to grasp the importance of quality management principles. These gaps can result in a lack of ownership over quality outcomes, ultimately impacting product success.
"Quality management in PLM is not just the responsibility of one department; it should be a collective endeavor that permeates the entire organization."
Common Obstacles in Quality Implementation
Several common obstacles can impede the effective implementation of quality management systems within PLM:
- Inadequate Training: Without proper training on quality management processes and tools, employees may lack the skills necessary for effective implementation.
- Lack of Clear Communication: Miscommunication across departments can lead to discrepancies in quality standards and practices.
- Resource Limitations: Organizations may face constraints in personnel, time, and budget, hindering their ability to focus on quality initiatives.
- Resistance to Change: Employees may be reluctant to adopt new quality management protocols, especially if they are accustomed to existing processes.
- Inconsistent Application of Standards: Different teams may apply quality standards inconsistently, leading to variability in product quality.
Strategies for Overcoming Quality Challenges
To address the challenges of PLM quality management, organizations can implement several strategies:
- Invest in Training Programs: Providing comprehensive training can empower employees, equipping them with the necessary skills and knowledge to contribute effectively to quality management.
- Enhance Cross-Departmental Collaboration: Establishing regular meetings between departments can ensure that quality objectives are aligned and that communication is clear.
- Utilize Advanced Technology Solutions: Implementing modern software tools that integrate well with PLM can facilitate better data management and improve quality oversight.
- Cultivate a Quality-Driven Culture: Encouraging a company-wide commitment to quality can foster a sense of ownership and accountability among employees.
- Regularly Review and Update Quality Standards: Continuous evaluation of quality standards ensures that they remain relevant and effective in a changing business landscape.
Case Studies: Successful PLM Quality Management
Case studies are critical in exploring real-world applications of PLM quality management. They provide tangible examples of how organizations have successfully integrated quality management within their product lifecycle processes. By examining these cases, decision-makers can gain valuable insights into effective strategies and potential pitfalls. It is in these narratives that lessons are learned, helping others to avoid missteps and to emulate successful practices that have proven effective in various industries.
Industry-Leading Examples of Quality Integration
Highlighting industry leaders gives an important perspective on best practices in PLM quality management. Companies like Apple and Toyota serve as prime examples. These organizations have harnessed quality management principles to streamline their product development, ensuring high standards without compromising innovation.
For instance, Apple consistently integrates quality assurance into every stage of its product lifecycle. Their rigid quality control checks are present from design through manufacturing to distribution. This results in products that meet customer expectations and regulatory compliance effectively. Moreover, their focus on data analytics allows Apple to identify quality issues before they escalate, minimizing risks and improving customer satisfaction.
Toyota, on the other hand, exemplifies the principles of lean manufacturing and continuous improvement through its Toyota Production System (TPS). They emphasize quality at every stage of production, encouraging employees to stop production to address quality concerns. This proactive approach has led to significant reductions in waste and improved product quality.
Lessons Learned from Quality Management Failures
While successful case studies offer rich insights, examining failures can be just as illuminating. Many organizations have faced challenges when implementing quality management systems, leading to costly mistakes that highlight the importance of learning from experience.
One notable case is Boeing's 737 MAX crisis. The issues related to quality oversight in design and testing processes raised significant concerns, which ultimately affected the safety of their aircraft. This situation underscores the necessity for robust quality management practices that include regular reviews, compliance checks, and a strong commitment to safety standards.
Another example is Volkswagen's emissions scandal, which revealed flaws in quality management and ethical considerations. The failure to uphold quality management principles not only damaged the company's reputation but also had severe financial implications. This case serves as a stark reminder that cutting corners in quality management can have lasting repercussions.
Future Trends in PLM Quality Management
Future trends in PLM quality management are vital to understand the evolving landscape of product lifecycle procedures. As industries change, it’s essential to stay updated with new practices. Businesses best flatter their market position if they recognize these trends early. This section discusses the significant shifts that could redefine quality management in PLM.
The Impact of AI on Quality Assurance Practices
Artificial Intelligence (AI) is at the forefront of innovation in quality management. Integrating AI into PLM systems allows organizations to automate routine tasks. This increases efficiency and helps reduce human error. AI can analyze vast amounts of data quickly. This capability enables organizations to uncover patterns that may not be obvious through traditional methods.
For instance, AI-driven tools can predict potential defects before they happen. This proactive approach significantly enhances quality assurance efforts. Additionally, machine learning algorithms can help in continuously optimizing processes based on real-time feedback. Here are some specific benefits of using AI in quality assurance:
- Discerning Trends: AI helps identify recurring issues during the production cycle.
- Enhanced Decision-Making: Data-driven decisions enhance quality outcomes.
- Increased Efficiency: Automated quality checks allows for faster processes.
In summary, AI transforms quality assurance from being reactive to proactive, which is critical for maintaining high standards in PLM.
Anticipating Changes in Industry Standards
The dynamic nature of industries necessitates that organizations remain adaptive to changes in regulations and standards. This adaptability fosters a culture of continuous improvement. Monitoring industry trends is crucial for anticipating forthcoming standards. Staying compliant with new regulations not only protects the organization but also builds customer trust.
Emerging regulations often relate to environmental sustainability and ethical sourcing. These factors will become more integrated into quality management systems. Companies must ensure their quality management practices reflect these values. Considerations for adapting to changes in industry standards include:
- Regulatory Tracking: Employing systems that monitor regulatory updates can help in preparing for changes ahead of time.
- Stakeholder Engagement: Involving a wide range of stakeholders ensures diverse perspectives are considered when adapting to changes.
- Proactive Training: Regular training for employees on new standards improves compliance and work quality.
Finale: The Path Forward for PLM Quality Management
The integration of quality management within Product Lifecycle Management (PLM) is not just a recent trend, but a substantial shift in how organizations approach product development. This article emphasizes that quality management is integral for businesses seeking to achieve operational excellence and continuous improvement. As we wrap up, it is essential to recognize the role of quality as a driver in the PLM landscape.
Organizations must acknowledge that the journey of enhancing product quality begins with understanding the current state of their quality management practices. By synthesizing insights from the preceding sections, decision-makers can identify gaps and opportunities for enhancement. This coherent approach allows for the establishment of a solid foundation that supports ongoing improvements.
Synthesizing Quality Management Insights
Quality management insights gained throughout this article provide a roadmap for organizational change. Recognizing the relationship between quality management and PLM efficiency is crucial. Businesses can fortify their strategies by leveraging established principles and emerging technologies. Quality management frameworks can serve as guides to navigate the complexities of product lifecycles.
Moreover, implementing metrics and key performance indicators offers a mechanism to track progress and ensure that quality objectives align well with strategic goals. Integrating feedback loops is vital as it helps to address sizeable concerns swiftly, giving organizations agility in responding to developmental challenges.
Final Thoughts on Quality's Role in PLM
Quality management is no longer an afterthought but a core component of successful PLM. The importance of quality in product lifecycle cannot be overstated. It fosteres trust with consumers, ensures compliance with regulatory standards, and enhances brand reputation. In an era where competition is fierce, focusing on quality might truly set a business apart.
Organizations must also prepare to adapt to the ever-changing landscape of standards and regulations by embracing the latest technologies and methods. Encouraging a culture of quality from every team member will lead to not just improvements in products, but also in processes and overall organizational efficiency.