Exploring the Maximo Inventory System for Better Management
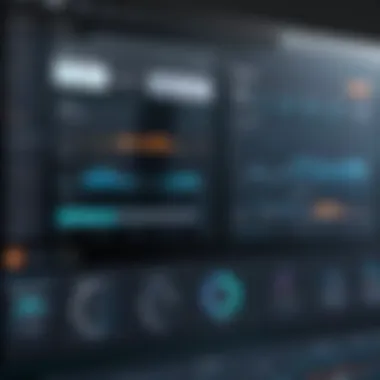
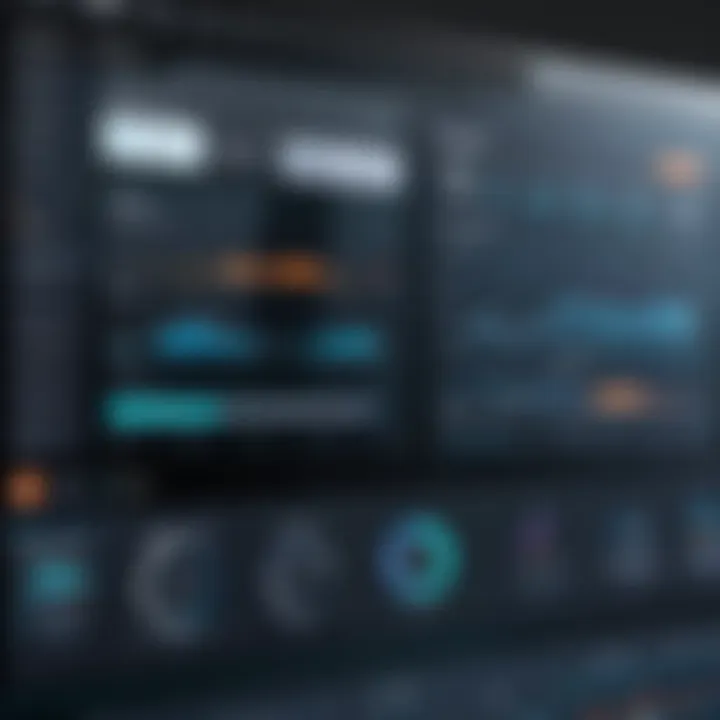
Intro
In an era where businesses are constantly striving to maximize efficiency, the management of inventory has emerged as a critical concern. The Maximo Inventory System stands out as a pivotal solution for organizations that aim to tackle this challenge head-on. This system not only simplifies asset management but also enhances overall operational effectiveness. Its multifaceted functionalities address various inventory tasks, enabling organizations to maintain control over their assets in a seamless manner.
Maximo is not just a tool but resembles a sophisticated framework that merges technological proficiency with practical applications. Its integration with other software platforms further enhances its functionality, making it adaptable to the varying requirements of different industries. As we delve deeper into this discussion, we will explore the key software features that make Maximo a sought-after solution, alongside the essential metrics for comparison that can guide decision-makers in assessing its value.
Key Software Features
Essential functionalities
The Maximo Inventory System comes packed with a myriad of features that cater to the intricate needs of inventory management. One fundamental aspect is its ability to provide real-time visibility into inventory levels. This is crucial for organizations that require precise tracking of assets, whether it be raw materials or finished goods.
Moreover, Maximo facilitates automated reordering processes. This prevents stockouts by notifying managers when inventory levels dip beyond predetermined thresholds.
Additionally, the system supports multiple locations. With Maximo, a company can easily manage inventory across various sites, which is particularly beneficial for larger organizations with widespread operations.
Advanced capabilities
Moving beyond the basics, Maximo’s advanced capabilities include sophisticated analytics and reporting tools. Businesses can analyze trends in inventory usage, providing insights that can drive purchasing decisions and inventory turnover rates. The built-in dashboards present this data in visual formats that are easy to interpret, which enables decision-makers to identify outliers and potential issues quickly.
Integration capabilities with other software systems raise the bar even higher. Organizations can connect Maximo with ERP systems, ensuring that all departments operate on aligned data. Thus, finance can have an accurate picture of inventory values and procurement can plan better based on real-time insights.
"In today’s competitive landscape, having a strong inventory management system like Maximo can be the difference between profit and loss for a business."
Comparison Metrics
Cost analysis
When evaluating an inventory system like Maximo, cost is a significant factor that cannot be overlooked. Pricing models may vary significantly based on the number of users, features selected, and deployment methods. Organizations should consider total cost of ownership, which encompasses not just the initial investment but also ongoing maintenance and support. Conducting a thorough cost-benefit analysis can provide invaluable insights into whether the system’s advantages outweigh its expenses.
Performance benchmarks
Performance is another crucial metric when assessing the efficiency of the Maximo System. Tracking key performance indicators, such as inventory turnover ratio, order fulfillment time, and accuracy in stock levels, can help organizations measure the system’s effectiveness. Comparing these benchmarks against industry standards can illustrate the value Maximo delivers relative to competitors and facilitate informed decision-making.
Prelude to Maximo Inventory System
The world of inventory management is intricate, like a well-crafted symphony where each component plays its part to perfection. Among the many tools available, the Maximo Inventory System stands out, serving as a central hub for businesses keen on honing their asset management strategies. Understanding this system is not just about learning software; it’s about grasping a foundational element that can drive efficiency and decision-making across various industries.
Definition and Purpose
When we peel back the layers of the Maximo Inventory System, we discover a robust platform designed to enhance the monitoring and tuning of inventories. At its core, it provides businesses with tools to track, manage, and streamline their assets effectively. The system is not merely a repository for data; it embodies the art of strategic resource management that aligns with an organization’s overall objectives. In a world where time is money, Maximo’s ability to cut through the clutter of inventory discrepancies can lead to significant financial savings.
History of Maximo Software
Maximo's journey began in the late 1980s when it was initially developed by Project Software & Development, later acquired by IBM in 2005. Over the decades, it has evolved from a basic application into a sophisticated solution that meets the complex demands of modern industries. The history of Maximo reflects broader technological advancements, integrating emerging trends such as cloud computing and mobile accessibility. This evolution hints at Maximo’s commitment to staying ahead of the curve and adapting as business needs shift.
Key Features Overview
The Maximo Inventory System is loaded with features that cater to diverse operational needs. Here are some of its standout capabilities:
- Real-Time Inventory Tracking: Offers up-to-date visibility of stock levels, reducing the chances of overstocking or running out of supplies.
- Automated Reordering: Configurable alerts ensure that reorders happen at optimal times, preventing delays in operations.
- Detailed Reporting: Customizable reports allow organizations to analyze trends and make informed decisions that propel business growth.
- Integrations: Connects seamlessly with existing ERP systems and other software solutions, enhancing operational fluidity.
As businesses grapple with increasingly complex inventory needs, mastering the Maximo Inventory System becomes a vital skill set for decision-makers. The intricacies of its frameworks can lead organizations to not just efficient but transformed inventory management practices.
Core Functionalities of Maximo
In understanding the Maximo Inventory System, one must delve into its core functionalities. These elements are the backbone of how organizations streamline asset management, facilitating both efficiency and clarity. With the right tools, businesses can not only track their inventory but also harness data insights that drive informed decisions. Below, we explore three pivotal functionalities: inventory management, asset tracking, and work order management.
Inventory Management
Managing inventory goes beyond keeping stock levels in check; it involves ensuring that all items are where they need to be when they need to be there. Maximo’s inventory management feature provides a structured approach to monitoring stock items. This system enables businesses to analyze consumption patterns, forecast needs, and maintain optimal stock levels without falling prey to overstocking or stockouts.
Benefits of Maximo’s Inventory Management:
- Real-time Data: Continuous monitoring of stock provides accurate and timely information, which is crucial for decision-making.
- Automated Reordering: The ability to set trigger points for reordering items prevents unnecessary delays in production or service delivery.
- Cost Control: By assessing usage and inventory levels, organizations can save costs associated with excess or obsolete stock.
As an example, a manufacturing company implemented Maximo’s inventory management system, which resulted in a 30% reduction in surplus materials, leading to significant savings.
Asset Tracking
Asset tracking is another cornerstone of Maximo’s capabilities. This feature allows organizations to locate, manage, and analyze all physical assets within their operations. By centralizing asset data, companies can easily monitor the lifecycle, maintenance schedules, and usage patterns of their assets.
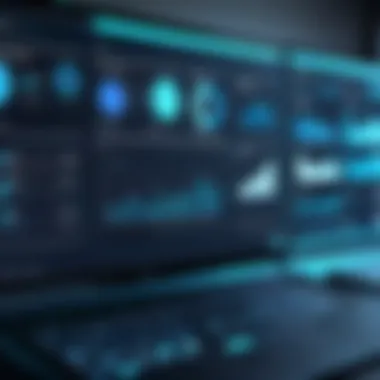

Key Considerations for Effective Asset Tracking:
- Barcoding and RFID: Utilizing technologies like barcoding and RFID enhances accuracy and speeds up the identification process.
- Lifecycle Management: Understanding the lifespan of assets contributes to better financial planning and resource allocation.
- Compliance and Reporting: Keeping track of assets aids in meeting regulatory requirements and generating insightful reports.
For instance, a healthcare facility tracked its medical devices through Maximo, ensuring that all equipment was operational and compliant with safety standards, which ultimately enhanced patient care.
Work Order Management
Work order management in Maximo ties together inventory and assets into a seamless workflow. This functionality is about more than just creating orders; it’s about orchestrating a series of actions to maintain and repair assets efficiently. Maximo empowers organizations to generate work orders automatically based on inventory levels or asset condition, thereby streamlining operations.
Advantages of Work Order Management:
- Improved Responsiveness: Quick generation and assignment of work orders reduce downtime and boost productivity.
- Enhanced Collaboration: Teams can easily access and share information related to tasks and priorities, fostering better teamwork.
- Performance Insights: With comprehensive reporting, stakeholders can identify trends, measure effectiveness, and make adjustments as needed.
A utility company adopted Maximo to manage its maintenance tasks, which improved its response times to equipment failures, ultimately leading to increased customer satisfaction.
In essence, the core functionalities of Maximo not only drive operational efficiency but also foster a culture of proactive management in organizations.
In summary, these features of Maximo, namely inventory management, asset tracking, and work order management, are integral for any business aiming to optimize their asset strategy and elevate performance amidst a competitive landscape.
Integration Capabilities
Integration capabilities of the Maximo Inventory System are pivotal for ensuring seamless operations across various organizational functions. By allowing communication between multiple software platforms, integration streamlines workflows and enhances data accuracy. This facilitates a unified view of inventory and assets, enabling decision-makers to respond swiftly to changing business needs.
This section will detail how Maximo interfaces with essential systems, harnessing the potential of integrated data to create substantial advantages for users. Let's explore the key facets of this topic, including integration with ERP systems, API connectivity, and third-party software integrations.
Integration with ERP Systems
The integration of Maximo with Enterprise Resource Planning (ERP) systems like SAP or Oracle significantly amplifies operational efficiency. By merging these powerful platforms, organizations can synchronize inventory with procurement, finance, and HR processes. When these systems link up, it fosters a holistic approach to managing assets.
For example, when a purchase order is generated in ERP, it can instantly reflect in Maximo, updating the inventory levels accordingly. Consequently, this mitigates the risk of overstocking or understocking, leading to better cash flow management and optimized resource allocation.
Considerations for ERP integration include:
- Selecting the right ERP partner that aligns with Maximo's capabilities
- Understanding data flow to avoid conflicts
- Training users on both systems to ensure smooth transitions
API Connectivity
API (Application Programming Interface) connectivity is at the heart of modern software ecosystems. With Maximo’s robust API framework, businesses can expand their toolsets, linking to diverse applications tailored to specific needs. This open pathway invites innovation—organizations can create custom applications that speak directly to Maximo, centralizing data management.
For instance, a logistics company could develop an app that pulls data from Maximo to craft real-time reports on inventory movements, thus revolutionizing how they track deliveries and stock levels.
Key benefits of utilizing API connectivity include:
- Enhanced agility in responding to market demands
- Customization options for varied business requirements
- The ability to scale operations with new functionalities over time
Third-party Software Integrations
The ability to integrate with third-party software is an indispensable feature of the Maximo Inventory System. Tools like Microsoft Power BI or Tableau can draw insights from Maximo’s data, empowering users to visualize trends and make informed decisions. This flexibility allows businesses to leverage their existing software ecosystem efficiently.
Unique examples of third-party integrations are:
- Connecting Maximo with a predictive maintenance solution to foresee equipment failures
- Integrating with an e-commerce platform for real-time inventory updates to enhance customer satisfaction
By bringing together various applications, organizations can create a synergistic environment that not only enhances productivity but also simplifies user experiences.
Integrating systems isn't just about connecting software; it’s about weaving a tighter fabric of information that ultimately shapes decision-making.
In summary, integration capabilities are a cornerstone of the Maximo Inventory System, enabling it to be more than just a standalone tool. Integrating with ERP systems, employing API connectivity, and collaborating with third-party software lay the groundwork for a responsive, data-driven organization.
Benefits of Using Maximo Inventory System
The Maximo Inventory System stands as a beacon for organizations eager to enhance their asset management dynamics. By utilizing this system, companies can unlock a myriad of benefits that hinge not just on lowering costs but on refining processes, boosting morale, and maintaining a competitive edge. It's not merely about managing inventory; it’s about understanding and responding swiftly to the ebb and flow of business needs, making every operational move count.
Enhanced Operational Efficiency
Operational efficiency isn't just a buzzword; it’s a lifeblood for enterprises aiming to thrive in today's fast-paced market. With the Maximo Inventory System, organizations can streamline workflows and minimize downtime. Here’s a closer look at how it works:
- Real-time visibility: Imagine having instant access to inventory levels, locations, and usage patterns. That’s what Maximo delivers, allowing teams to make swift, informed decisions that keep operations humming.
- Automation features: Manual processes can be a bottleneck. With Maximo, automating routine tasks lowers the risk of human error, ultimately leading to smoother operations.
- Synchronized departments: The seamless integration features mean that everyone from procurement to operations is on the same page. This cohesion eliminates miscommunication and fosters a culture of collaboration.
"The ability to see inventory in real time transforms how we respond to demand shifts. It takes the guesswork out!"
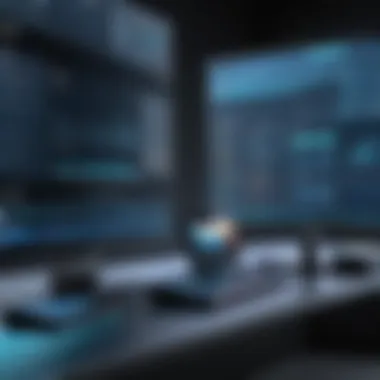
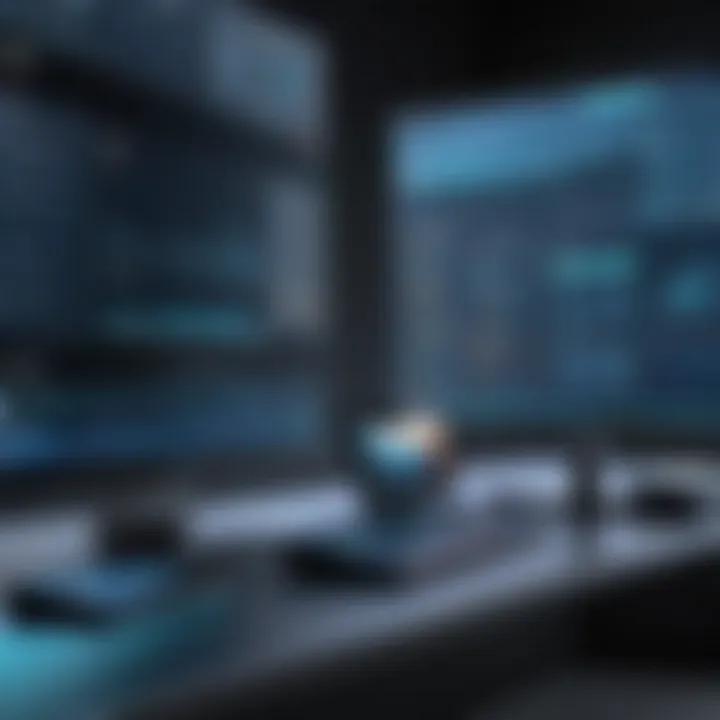
Cost Reduction Strategies
Cost control is not solely about slashing expenditures; it’s about making strategic choices that promote long-term savings. Maximo’s inventory management system contributes to cost reduction through several mechanisms:
- Decreased carrying costs: By optimizing inventory levels, businesses can reduce the expenses tied to overstock and storage. Maximo’s predictive analytics tools help in understanding demand cycles, thus enabling better stocking decisions.
- Fewer stockouts and overages: The risk of either running out of stock or having excess happens when there’s no clarity over inventory levels. Maximo minimizes this risk, aligning inventory closely to actual needs, and saving costs associated with last-minute orders or markdowns on surplus stock.
- Supplier management: Effective tracking and monitoring of supplier performance help organizations negotiate better terms, select the best partners, and implement bulk purchasing strategies when beneficial.
Improved Decision-making
A data-driven decision-making approach can substantially change the trajectory of a business. Maximo supports this by equipping users with the analytics necessary to make informed choices:
- Comprehensive reporting: The system generates reports that unveil trends and historical data, enabling leaders to anticipate future needs and tailor strategies to meet them.
- Dashboard functionality: With customizable dashboards, key performance indicators are just a glance away. Managers can pinpoint issues before they escalate, making proactive strategies a reality rather than a hope.
- Scenario modeling: Maximo allows users to simulate different scenarios and assess outcomes, creating a safe space for testing decisions before putting them into action.
Armed with these insights, organizations can navigate challenges with confidence, supporting a culture where informed decision-making reigns.
In sum, the Maximo Inventory System powers organizations to enhance operational efficiency, trim costs wisely, and make choices backed by solid data. As the marketplace continues to evolve, leveraging such systems becomes not just advantageous but essential for enduring success.
Challenges and Limitations
Understanding the challenges and limitations of the Maximo Inventory System is crucial for organizations aiming to optimize their asset management endeavors. In any implementation of such software, it is wise to anticipate potential hurdles. Recognizing these obstacles not only sets realistic expectations but also enhances the capability to navigate through them effectively.
Implementation Challenges
Implementing the Maximo Inventory System can often resemble assembling a complicated jigsaw puzzle—it demands careful planning and resource allocation. Organizations may face various implementation challenges, including:
- System Integration: Many businesses run multiple systems concurrently. Integrating Maximo with other software, whether it’s ERP platforms or specialized inventory tools, can be tricky. Mismatched data formats and compatibility issues can hinder fluid interoperability.
- Resource Allocation: A successful implementation requires the right amount of time and expertise. Teams may find themselves short-staffed or lacking the necessary skills. Training existing personnel is essential, but it’s also an investment that not all firms are prepared to make.
- Data Migration Difficulties: Transitioning from a legacy system to Maximo involves moving historical data, which poses the risk of data loss or corruption. Ensuring data integrity throughout this process is critical, yet challenging, as it often involves extensive validation efforts.
"Investing time upfront to strategize the implementation process will pay dividends in the long run."
User Adoption Issues
Even when a system is implemented successfully, gaining user adoption is another mountain to climb. Factors influencing user adoption of Maximo include:
- Resistance to Change: Employees often develop a comfort zone with existing processes. The introduction of a new system could face objections simply because change causes disruption in their day-to-day tasks.
- Training and Support: If users are not adequately trained on how to utilize Maximo effectively, this can lead to frustration and decreased productivity. Lack of ongoing support or resources can exacerbate this issue.
- Usability Problems: If the interface is not user-friendly, employees may struggle to engage with the system. The learning curve shouldn't feel like scaling a wall; rather, it should be more of a steady incline.
Maintenance and Support Concerns
Once Maximo is up and running, maintenance and support must remain a priority. Ongoing concerns include:
- System Upgrades: Regular updates are necessary to keep the software aligned with the latest technological advancements. However, these upgrades can cause temporary disruptions and may require additional training.
- Technical Support Availability: Reliable technical support is paramount. If issues arise, swift solutions are needed to minimize downtime. Relying solely on vendor support can sometimes lead to delays, making internal technical self-sufficiency a goal for many settings.
- Cost Management: Budgeting for the ongoing cost of maintenance, including software updates and support services, can pose a challenge. Organizations often underestimate these costs during the planning phase.
By keeping these challenges in mind, decision-makers and IT professionals can approach the Maximo Inventory System with a plan to mitigate potential issues, leading to smoother transitions and greater overall effectiveness.
Industry Applications of Maximo
The application of the Maximo Inventory System trends across various industries, demonstrating its adaptability and robust functionality tailored to diverse operational needs. This section elaborates on how different sectors harness the capabilities of Maximo to optimize their inventory systems, improve asset management, and bolster overall efficiency. Understanding these industry-specific implementations will provide valuable insights not just into Maximo's versatility but also into best practices that organizations can adopt for similar success.
Manufacturing Sector
In the manufacturing realm, the challenge is often to balance production schedules with efficient inventory management. Here's where the Maximo Inventory System shines by providing a framework for managing raw materials, work-in-progress, and finished goods. With its real-time tracking and reporting features, manufacturers can keep a close eye on stock levels, reducing the chances of overproduction or stockouts.
Key advantages in the manufacturing sector include:
- Streamlined Production Planning: Maximo allows manufacturers to align inventory levels with production demands, thereby avoiding bottlenecks.
- Predictive Maintenance: By integrating asset management, manufacturers can foresee when machinery requires servicing, preventing unexpected downtime and prolonging asset life.
- Enhanced Compliance: Regulatory requirements often dictate strict controls over inventory; Maximo helps organizations maintain these standards efficiently.
"A well-structured inventory system is the backbone of any flourishing manufacturing operation, and Maximo ensures that backbone is strong and sturdy."
Healthcare Industry
The healthcare industry faces unique inventory challenges—from managing medical supplies to pharmaceuticals, inefficiencies can have serious implications. The Maximo Inventory System is particularly well-suited for healthcare applications because it emphasizes visibility and control. Health organizations leverage Maximo to ensure that critical supplies are always on hand, thus safeguarding patient care.
In the context of healthcare, Maximo's capabilities encompass:
- Automatic Reorder Points: This feature allows healthcare providers to maintain optimum supply levels without manual effort, ensuring availability when needed.
- Expiration Tracking: Drugs and medical supplies often come with expiration dates, and Maximo helps to track these, reducing waste and ensuring patient safety.
- Audit Trail: This capability supports regulatory compliance, keeping detailed records for inspections and audits.
Utilities and Energy Management
Utilities and energy companies often contend with complex inventory requirements that must align with regulatory demands and the need for reliability. The Maximo Inventory System plays a crucial role in the efficient management of assets such as transformers, meters, and service trucks. By employing Maximo, these organizations enhance their operational capabilities significantly.
For utilities, the advantages of using Maximo include:
- Asset Lifecycle Management: Maximo tracks the entire lifecycle of utility assets, helping companies plan for replacements and upgrades strategically.
- Field Mobility: With mobile accessibility, field workers can access critical data and update inventory records in real-time, improving service efficiency and accuracy.
- Inventory Cost Management: Through insightful analytics, organizations can make informed decisions about stock levels, leading to significant cost savings.
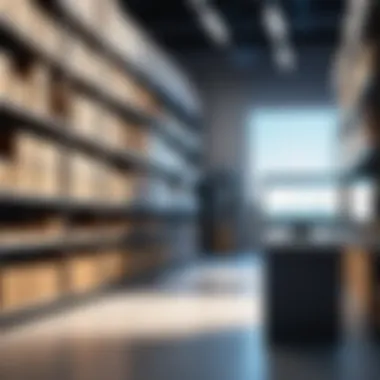
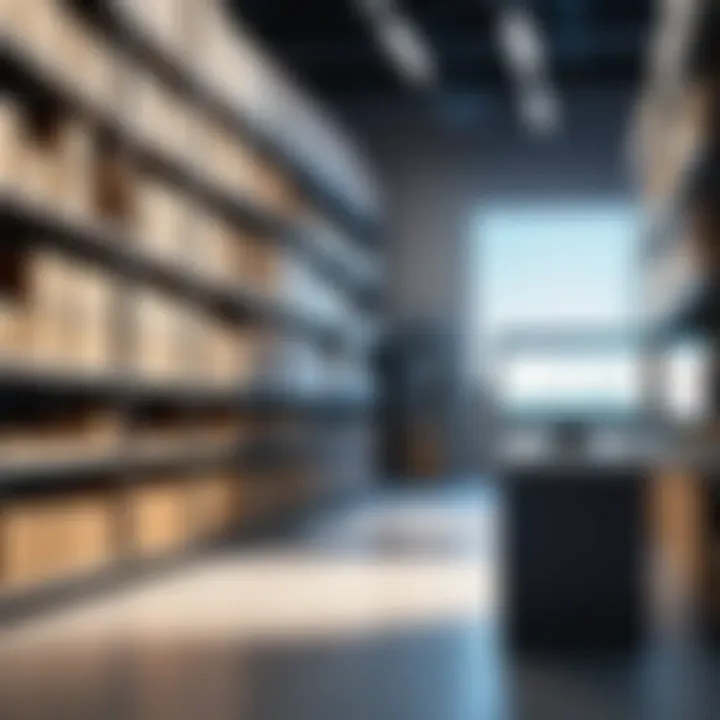
Through these industry applications, Maximo not only enhances operational efficiency but also fosters an environment where data-driven decisions can flourish. The tailored features underscore its importance, serving diverse sectors with unique demands, ultimately affirming that Maximo is a pivotal tool in modern inventory management.
Maximo Technology Stack
In the realm of asset management, the Maximo Inventory System hinges on a robust, adaptable technology stack. This stack marks the backbone, ensuring efficient workflows and seamless integrations, which are critical for today's business operations. By understanding the intricacies within this technology stack, organizations can leverage Maximo more effectively, enhancing their capabilities in monitoring and managing inventories.
Underlying Technology and Architecture
The architecture of Maximo is designed for flexibility and scalability. Built upon Java EE and IBM's middleware, this system is capable of running in both cloud and on-premise environments. This dual-approach provides organizations with the choice to align their infrastructure strategy with corporate policies, security requirements, or operational preferences. The service-oriented architecture (SOA) inherent in Maximo enables it to utilize web services to communicate with various applications, making integration across platforms smoother.
Additionally, Maximo's use of the IBM Db2 database for data storage offers outstanding performance and reliability. This backend structure ensures that users have access to essential data without the common bottlenecks that can plague less robust systems. As the data ecosystem evolves, Maximo’s architecture can easily integrate new technologies or adapt to changing workloads without a complete overhaul, exemplifying its long-term value for organizations.
Data Management Tools
Data management in Maximo is comprehensive and meticulously designed. From tracking inventories to analyzing asset lifecycles, the tools provided facilitate a holistic view of enterprise data. Utilizing predefined data metrics, users can monitor various aspects of inventory performance, identifying trends and patterns that drive informed decision-making.
The system incorporates data analytics that can be customized for specific requirements. This personalization is crucial for businesses in the competitive landscape, allowing them to extract insights pertinent to their operations. Moreover, Maximo can leverage data visualization tools, derived from its analytics capabilities, to present this information in engaging formats. For example, organizations can use dashboards that dynamically display performance metrics, making it easier for stakeholders to understand information at a glance.
User Interface and Experience
A central consideration in the design of Maximo is its user interface (UI). The UI is crafted to provide a simple and intuitive experience for both seasoned professionals and new users. This clarity is vital for minimizing the learning curve often associated with advanced software systems.
The interface is streamlined, featuring customizable dashboards that help individuals focus on the metrics that matter most to their functions. Changes to the layout can often be done with just a few clicks, accommodating user preferences easily. Furthermore, convivial mobile access enables staff to stay updated on the go, a significant benefit for teams working in dynamic environments.
With frequent updates, Maximo aims to enhance the user experience continually. Customers are encouraged to provide feedback, which informs future developments and UI enhancements. This responsiveness demonstrates a dedication to user satisfaction and operational effectiveness.
In summary, the technology stack of Maximo not only supports its core functionalities but also equips businesses with the tools needed to thrive in a data-driven ecosystem. As environments transform and technology advances, having a reliable, flexible solution like Maximo positions organizations for sustained success.
Future of Maximo Inventory System
The future of the Maximo Inventory System holds considerable promise as businesses continue to evolve in the face of rapid technological changes and global economic shifts. Understanding the direction in which this robust system is headed is crucial for decision-makers, especially those keen on leveraging the latest tools for optimizing inventory management, improving asset utilization, and achieving lean operational processes. This section will unwrap emerging trends, technological advancements, and predictions shaping the future of the Maximo Inventory System.
Emerging Trends in Inventory Management
Inventory management is not a one-size-fits-all affair. Instead, it is a dynamic field that constantly incorporates new methodologies and strategies. One particularly notable trend is the growing adoption of data analytics to facilitate predictive inventory management. Businesses are becoming more adept at analyzing historical data to forecast demand accurately, which helps in reducing excess stock and minimizing shortages.
- Real-time Inventory Tracking: Organizations are utilizing advanced technology to achieve real-time visibility into inventory levels across multiple locations. This capability enables swift and informed decision-making.
- Sustainability: There's an increasing focus on green practices within inventory management. Companies are examining their supply chains for carbon footprints and waste reduction, aligning their operations with sustainability goals.
- Artificial Intelligence: AI is beginning to play a pivotal role in automating routine inventory tasks, enabling teams to focus on strategic initiatives instead. The potential of AI in predicting market trends and behavioral analysis means smarter stock levels and reduced waste.
"The emergence of technology in inventory management is revolutionizing the way organizations handle stock, creating smarter and more efficient processes."
Technological Advancements
As technology marches forward, Maximo is also set to leverage significant advancements to enhance its capabilities further. One of the highlights of upcoming changes is the integration of machine learning algorithms. These algorithms can analyze vast sets of data to identify patterns and make intelligent predictions about inventory needs.
Moreover, the rise of the Internet of Things (IoT) cannot be overlooked. With devices connected in a network, organizations can monitor asset conditions and inventory levels through smart sensors. A timely update on inventory metrics or potential issues can make all the difference in maintenance and management plans.
- Blockchain Technology: As supply chain transparency becomes paramount, blockchain could be a game-changer. It holds the potential to provide immutable records of every transaction, improving traceability and accountability.
- Cloud Computing: The move to cloud-based inventory systems allows for easier access, better data security, and the ability to scale resources based on demand, offering organizations greater flexibility.
Predictions for Market Evolution
Looking ahead, the market for inventory management solutions, including Maximo, is expected to experience significant transformations. Analysts suggest sustained growth in this sector as businesses recognize the pivotal role of effective inventory management in ensuring operational success.
Some predictions include:
- Increased Investment: More companies are anticipated to invest in advanced inventory systems, prioritizing flexibility and scalability.
- Enhanced Customer Experience: As organizations strive for efficient inventory control, the result will often culminate in improved customer satisfaction due to better product availability and quicker shipping times.
- Rise in Remote Accessibility: With the ongoing trend toward remote work, solutions that offer full access capabilities from anywhere will likely dominate market offerings, ensuring teams can respond to inventory demands anytime, anywhere.
In summary, the horizon for the Maximo Inventory System is replete with innovations and opportunities. Each evolution comes not just as a mere upgrade but as a necessary adaptation to meet the ever-changing landscape of business needs and customer expectations.
End
In today's fast-paced business environment, the Maximo Inventory System emerges as a cornerstone for organizations aiming to enhance their asset management efficiency. Understanding this system's potential is crucial for decision-makers, IT professionals, and entrepreneurs who wish to harness its capabilities to drive operational success.
Summary of Key Points
The crux of leveraging the Maximo Inventory System involves several critical components:
- Operational Efficiency: By streamlining processes, Maximo allows companies to reduce overhead costs and increase their productivity.
- Integration Capabilities: Its ability to seamlessly interface with various ERP systems and third-party software ensures a cohesive operational framework.
- Data-Driven Insights: The system's analytics tools empower organizations to make informed decisions based on real-time data.
- Industry Applications: Its versatility across sectors such as manufacturing, healthcare, and utilities exemplifies its wide-reaching benefits.
In summation, the Maximo Inventory System not only enhances daily operations but also positions organizations for long-term success in a competitive landscape.
Final Thoughts on Maximo
The future of the Maximo Inventory System looks promising as technological advancements continue to evolve. Companies that adopt this system stand to gain a significant competitive edge. However, it is vital to be mindful of the challenges that may arise, such as user adoption and implementation hurdles. Addressing these considerations proactively can pave the way for a successful integration of Maximo into the fabric of an organization.
Embracing the Maximo Inventory System is not merely about efficiency gains; it is about fostering a culture of informed decision-making and adaptability. By treating the system as an ongoing investment rather than a one-time solution, businesses can unlock its true potential and navigate the complexities of modern inventory management with confidence.
"In the world of inventory management, the right tools can make all the difference. Embrace technology, adapt, and thrive."