Maximizing Efficiency with OEE Metrics
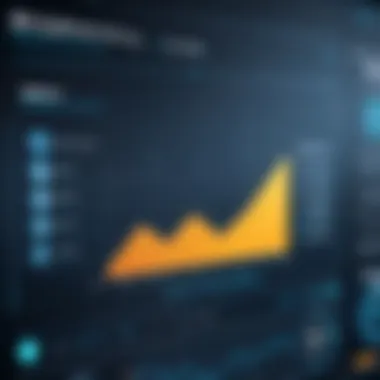
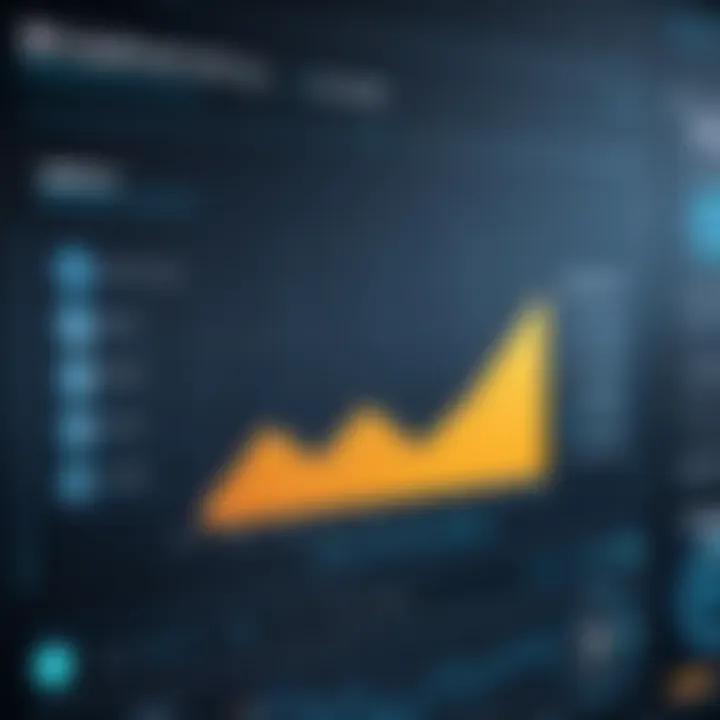
Intro
In the quest for operational excellence, industries around the globe are finding themselves leaning heavily on Overall Equipment Efficiency, commonly shortened to OEE. This metric pulsates at the heart of manufacturing performance, telling a story that can lead to enhanced productivity and reduced waste. For decision-makers and IT professionals, understanding OEE isn't just a box to tick; it’s the cornerstone of informed strategies that can propel organizations ahead of their competition.
OEE is often regarded as a compass for gauging the effectiveness of equipment and systems in a manufacturing environment. It provides a robust framework by breaking down efficiency into three core components: availability, performance, and quality. Each of these elements plays a crucial role in painting a comprehensive picture of how well machines operate and how that impacts the overall output.
This article serves as a deep dive into OEE metrics, from the nuts and bolts of calculation methodologies to practical tips for improvement and real-world applications across various industries. We aim to equip professionals with not just the how-to but also the why behind these metrics, creating a narrative that informs better decision-making in the realm of manufacturing performance.
As we embark on this exploration, keep in mind that the insights gained could make a significant difference in how manufacturing processes are perceived and implemented.
"A metric isn't just a number; it's a reflection of your operational soul."
Understanding these metrics and their intricacies could very well be the game changer that many industries are seeking.
Key Software Features
In today’s tech-driven world, software solutions designed to track and optimize OEE are more than just helpful tools; they’re essential for running efficient operations. A good OEE software platform should encompass a variety of features that contribute directly to defining, calculating, and improving this metric.
Essential functionalities
- Real-time data tracking: The ability to capture production data as it happens is pivotal. It allows manufacturers to respond to issues before they snowball into larger problems.
- Dashboard analytics: A well-designed dashboard can visualize complex data, making it easier for teams to identify trends, anomalies, and areas in need of attention.
- Alerts and notifications: Setting up alerts for when OEE drops below a target threshold can help in quickly addressing issues, thus preventing loss of productivity.
Advanced capabilities
As organizations mature in their OEE journey, they may look to more advanced functionalities, such as:
- Predictive analytics: Utilizing machine learning algorithms to forecast potential downtime or performance dips based on historical data. This proactive approach can save both time and money.
- Integration with existing systems: Ensuring compatibility with manufacturing execution systems (MES) and enterprise resource planning (ERP) solutions can streamline data flow and provide a holistic view of the production environment.
- Custom reporting: Tailored reports can help decision-makers gain insights that are specifically relevant to their operational goals.
Focusing on these software features enables companies to leverage OEE effectively, driving toward higher efficiencies and a more profitable base to operate from. As we turn our attention to metrics that compare and contextualize performance, we’ll see how deeper insights can inform strategic choices.
Foreword to OEE Industrial
When diving into the realm of industrial efficiency, a few metrics stand out as crucial, but none quite as pivotal as Overall Equipment Efficiency, or OEE. It’s not just a fancy acronym tossed around in boardroom meetings; it's the backbone of productivity strategies across various industries. Understanding OEE isn’t just a matter of calculations; it provides a lens through which decision-makers can assess their operations, improving yield and effectiveness.
Defining OEE
At its core, OEE is a measure that combines three essential elements: Availability, Performance, and Quality. Availability refers to the time a piece of equipment is actually running compared to the total time it’s scheduled to run. You can think of it as the difference between when the machine should be humming to life and when it’s actually doing its job.
Performance measures how quickly a machine operates versus its full potential during the production time. If a machine is capable of producing 100 widgets an hour but only churns out 80, that discrepancy tells a story about lost efficiency that OEE aims to clarify.
Lastly, Quality considers the percentage of products that meet quality standards out of all products produced. If defects pile up, ideally, OEE nudges us to focus on quality improvements alongside availability and performance. By understanding these components, industries can pinpoint inefficiencies and create targeted strategies for enhancements.
Importance of OEE in Industries
OEE isn’t just a buzzword; its significance stretches across different sectors, acting as a leading indicator of overall productivity. Here are some key perks that come with mastering OEE:
- Enhanced Productivity: With a clear metric like OEE, teams can set benchmarks, track progress, and fine-tune machines to maximize output without the guesswork.
- Waste Reduction: OEE highlights bottlenecks and downtime, enabling managers to address issues right in their tracks, substantially cutting waste.
- Informed Decision Making: Using OEE data allows for real-time adjustments to processes. teams can decide whether to replace equipment or provide further training based on solid evidence rather than instinct.
"The beauty of OEE lies in its simplicity; it takes complex manufacturing dynamics and breaks them into manageable, actionable insights."
Moreover, in an era where competitiveness is cutthroat, an efficient operation can set an industrial player apart from others. By keeping a close eye on OEE, industries not only aim for operational excellence but also pave the way for long-term sustainability. In essence, understanding OEE isn't just beneficial; it's vital.
Components of OEE
Understanding the components of OEE is pivotal for anyone looking to enhance operational effectiveness. When broken down, OEE consists of three core pillars: Availability, Performance, and Quality. Each of these components plays a significant role in shaping overall equipment efficacy and thereby influences the productivity of manufacturing operations. By paying close attention to these facets, businesses can glean insights into where inefficiencies lie and how best to tackle them. A thorough grasp of each component becomes indispensable for driving continual improvement and making informed decisions.
Availability
Understanding planned vs. unplanned downtime
In the realm of Availability, distinguishing between planned and unplanned downtime is crucial. Planned downtime relates to scheduled maintenance or machinery upgrades, allowing for a preemptive approach to performance. In contrast, unplanned downtime emerges unexpectedly, often resulting from equipment failures or other unforeseen issues. Recognizing this dichotomy helps organizations strategize effectively. For instance, while planned downtime can be accounted for and optimized, unplanned downtime often necessitates swift problem-solving measures to mitigate losses.
The key characteristic of knowing the difference is that it enables better forecasting and resource allocation. Companies can devise maintenance schedules that maximize machine uptime while simultaneously preparing for contingencies. However, a downside here lies in the potential complacency toward equipment health, as some may overlook the need for regular checks just because of a robust maintenance plan.
Factors affecting availability
Availability is further influenced by numerous elements such as equipment reliability, maintenance practices, and operator skill levels. If a machine frequently breaks down due to outdated components, its availability suffers, pushing OEE metrics downwards.
This highlights one of the fundamental reasons why focusing on availability is beneficial for this article. A thorough understanding of these factors offers a roadmap for improving OEE. It's also a unique opportunity for leaders to assess whether the right resources are being allocated toward overcoming shortcomings in equipment performance. However, the challenge here is determining how to measure these factors effectively, which can vary significantly across different settings.
Performance
Cycle time vs. ideal cycle time
The distinction between actual cycle time and ideal cycle time serves as a focal point in this context. Ideal cycle time represents the best possible performance under perfect conditions, while actual cycle time reflects real-world operational performance. Understanding this difference allows factories to pinpoint inefficiencies in their processes. The emphasis here lies in recognizing how much extra time is being spent on producing a single unit compared to the ideal scenario.
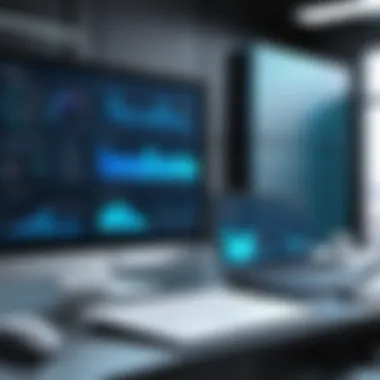
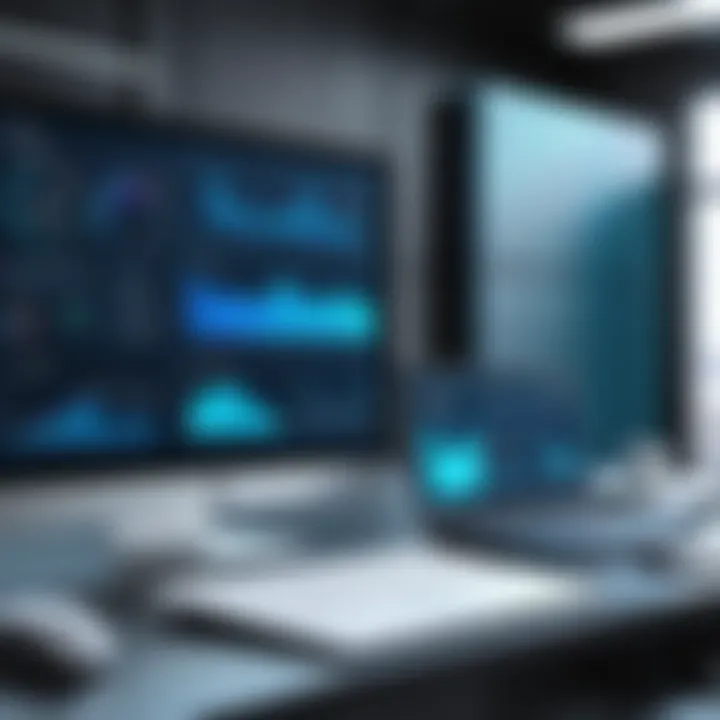
This comparison can spark discussions on the necessity of streamlining processes or adopting new technologies. However, focusing too heavily on ideal cycle time can lead to unrealistic expectations, which might negatively affect employee morale.
Identifying performance losses
Identifying performance losses becomes essential for optimizing plant output. Here, one assesses the gaps between expected and actual performance. This process involves scrutinizing machinery and operator interactions, as well as material flow. Common performance losses, such as slow cycles or minor stoppages, can add up and diminish overall productivity.
Highlighting these losses is a beneficial endeavor for this article since it emphasizes the importance of ongoing evaluation and fine-tuning. By openly discussing how to identify these issues, companies can cultivate an environment where continual improvement isn’t just a goal but a regular practice. On the flip side, not recognizing these losses may lead to stagnant performance metrics, diminishing overall OEE closer to the floor.
Quality
Defining quality metrics
When it comes to Quality, defining pertinent quality metrics is key. Quality metrics serve as benchmarks for assessing the worthiness of products produced. They help in determining if the finished goods meet certain standards before they reach the consumer. Good quality practices will ensure that a smaller percentage of defective items are produced, which directly benefits OEE scores.
This topic is crucial for the article as it links quality directly to efficiency. Having well-defined quality metrics enables firms to adopt proactive measures that can avert defects before they happen. Yet, there's a caveat; focusing excessively on quality can sometimes stifle creativity and slow down innovative processes, if not managed prudently.
Impact of defects on OEE
The impact of defects on OEE cannot be overstated. Each defect produced represents not just a lost unit, but also contributes to wasted time, labor, and materials. This inefficiency can create a ripple effect throughout the entire production process. Recognizing the weight of these defects fosters a culture where quality is prioritized alongside speed and cost.
The unique advantage of discussing this aspect is that it highlights the interconnected nature of production metrics. When firms commit to quality improvement, they inherently bolster their OEE, illustrating a clear path to significant gains in operational performance. It's important, however, to balance quality initiatives with production timelines, as excessive quality checks can sometimes hinder throughput.
"The road to success is dotted with many tempting parking spaces." Understanding OEE components helps navigate these challenges while steering clear of unnecessary stops.
Calculating OEE
Calculating Overall Equipment Efficiency (OEE) is more than a mere exercise in numbers; it’s a powerful tool for industries determined to straighten their operations. The value of OEE revolves around transforming raw data into actionable insights. This process allows businesses to pinpoint weaknesses, uncover opportunities, and bolster profitability.
Understanding the calculation also sheds light on its components – Availability, Performance, and Quality. Focusing on these elements shows just how interlinked different facets of productivity are. The real benefit here is that it empowers decision-makers to take informed action, ideally improving the overall operational efficiency down the line. Let’s break it down into more digestible parts.
Basic OEE Formula
OEE is calculated using a rather straightforward formula:
[ OEE = Availability \times Performance \times Quality ]\
Each of these components is expressed as a percentage. This simplicity is appealing. Yet, it masks the intricate interplay of those essential factors.
- Availability reflects how much of the scheduled time your equipment is actually up and running. It factors in planned and unplanned downtimes.
- Performance measures how fast your machinery runs during the time it is available compared to its potential speed.
- Quality represents the percentage of produced goods that meet quality standards versus the total produced.
Understanding how to apply this formula allows for quick assessments of productivity, leading towards areas for improvement.
Advanced Calculations
Advanced calculations of OEE can reveal insights that go deeper than what's found in the basic formula. Let's dive into two crucial aspects: incorporating additional metrics and real-time data consideration.
Incorporating additional metrics
When we talk about incorporating additional metrics, it means broadening the scope beyond the usual Availability, Performance, and Quality. You might consider things like Overall Yield, which includes scrap and rework rates, or machine utilization metrics that assess equipment flexibility.
The key characteristic of this approach is its demand for nuance. Industries adopting this strategy can effectively drill down into issues that may otherwise fly under the radar. For example, when machine utilization is high but OEE is low, it may signal inefficiencies in the production process needing attention.
However, there are some drawbacks. More metrics can lead to information overload, potentially confusing rather than clarifying. So, businesses need to strike a balance, factoring in relevance to their specific contexts while avoiding unnecessary complexity.
Real-time data consideration
Next, let's talk about real-time data consideration. It’s the name of the game in modern production environments. Capturing data as it happens enables immediate feedback, quick identification of problems, and, ideally, swift corrective actions.
The key characteristic here again circles back to timeliness. When decision-makers have access to real-time data, they can not only react but anticipate issues before they turn into bigger headaches.
However, this approach comes with unique hurdles, such as the need for investments in technology and training staff to make the best use of these tools. While the potential for enhanced OEE is enticing, one must consider whether the organization is equipped to handle these changes, both technically and culturally.
Modern industries that neglect real-time data risk falling behind their competitors who grasp this opportunity.
In summary, calculating OEE doesn’t end with the straightforward formula; it opens avenues for more profound understanding and innovation in operational efficiency. Whether it's through integrating additional metrics or leveraging real-time data, embracing these advanced calculations allows organizations to enhance their productivity and ultimately their bottom line.
Challenges in OEE Implementation
The implementation of Overall Equipment Efficiency (OEE) measures isn't a walk in the park. While the metrics are impactful, organizations face numerous hurdles that can bottleneck progress and skew results. Addressing these challenges is vital for industries that aim to leverage OEE but find themselves caught in the quagmire of operational inefficiency. This section will explore two primary challenges: Data Collection Issues and Cultural Resistance, both significant barriers to achieving optimal OEE outcomes.
Data Collection Issues
One of the core tenets of effective OEE analysis rests on accurate and comprehensive data collection. However, capturing the right data is akin to looking for a needle in a haystack. Numerous manufacturing processes produce a plethora of data, often leaving decision-makers drowning in irrelevant information.
To effectively gauge OEE, specific data points related to availability, performance, and quality need to be captured with precision. Here are some frequent data collection issues:
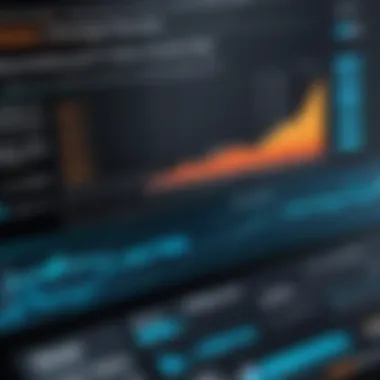
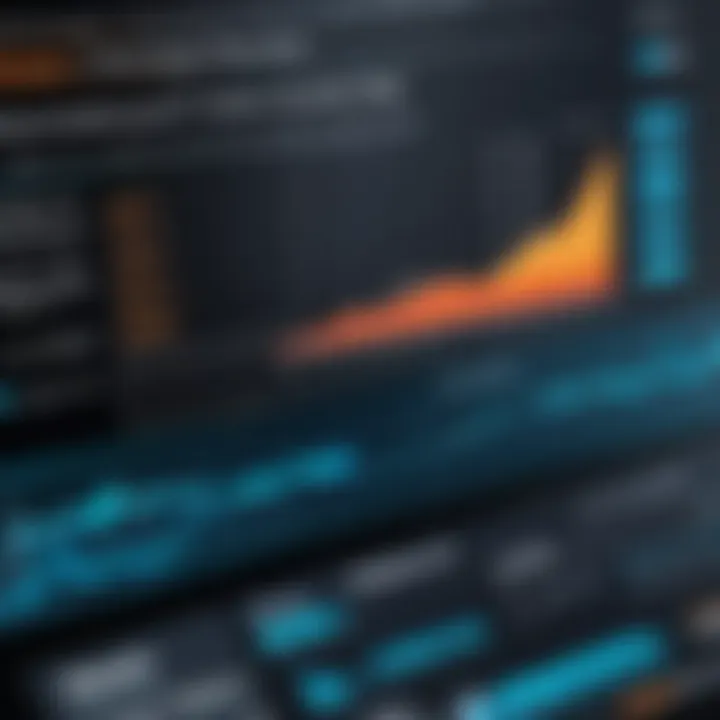
- Inconsistent Input: Gathering data often involves multiple sources which may not align, leading to discrepancies.
- Outdated Technology: Many industries still lean on legacy systems that cannot collect or process data in real-time, causing delays in analysis.
- Limited Training: Employees tasked with data collection may not fully understand OEE concepts, leading to misreporting or negligence in tracking key metrics.
These factors can dilute the reliability of OEE calculations. If the data is faulty, the conclusions drawn are just as weak. Getting a handle on these issues might involve investing in modern data collection tools or upskilling staff to ensure consistency in how OEE is reported and utilized.
Cultural Resistance
Even when the technical elements of OEE are in place, organizations often encounter cultural resistance that can hinder effective implementation. Employees and management alike may view OEE as a mere set of numbers rather than a roadmap for improvement.
Change is often met with skepticism, especially in environments steeped in tradition. Factors that contribute to this resistance include:
- Fear of Accountability: Workers might worry that OEE metrics will be used to scrutinize their performance unfairly.
- Comfort with Status Quo: Long-standing practices are hard to shake off. The fear of the unknown can paralyze initiatives that could otherwise lead to enhancements.
- Lack of Leadership Support: If upper management isn’t on board and vocal about the initiative, it’s unlikely that employees will rally behind OEE efforts.
To mitigate this resistance, fostering a culture that values transparency and open communication is key. > "When people understand how OEE metrics can benefit not just the company but also their daily tasks, they become more inclined to embrace changes."
Transmitting this enthusiasm from the top down can pave the way to smoother implementations, ensuring OEE metrics are viewed as allies rather than adversaries in the quest for efficiency. By addressing both data collection hurdles and cultural pushbacks, organizations can move closer to realizing the full benefits of OEE, ultimately solidifying process optimization as a key aspect of their operational strategy.
Best Practices to Improve OEE
Understanding how to effectively improve Overall Equipment Efficiency (OEE) involves more than just crunching numbers; it requires a multifaceted approach that seeks to eliminate inefficiencies at every turn. Improving OEE isn't just a matter of tweaking operations but rather an ongoing commitment to excellence that permeates through all levels of an organization. By adopting best practices, businesses can increase productivity, maximize production profits and ultimately create a more responsive and cost-effective operation.
Regular Equipment Maintenance
One of the cornerstones of improving OEE is regular equipment maintenance. Think of industrial machinery as the heart of any operation; if it stutters or halts, the entire system suffers. Implementing a rigorous maintenance schedule not only prevents unexpected breakdowns but also enhances the reliability of equipment, which plays directly into the availability component of OEE.
Regular maintenance can take various forms, including:
- Preventive Maintenance: Scheduling routine inspections and replacements helps to keep machinery running smoothly. For example, changing oil on a consistent schedule can prevent major engine issues down the line.
- Predictive Maintenance: Utilizing data analytics and sensors to predict when a machine is likely to fail allows for targeted interventions before an issue occurs. This method is becoming increasingly popular in modern factories.
- Corrective Maintenance: Addressing equipment issues as they arise ensures that minimal downtime occurs. Having a plan in place to quickly solve problems can keep operations ticking along.
In essence, investing in maintenance not only improves the overall functionality of equipment but also fosters a culture of trust within the team. Workers can feel secure knowing that their tools are reliable, which can lead to less stress and higher output.
Employee Training Programs
The importance of an educated workforce cannot be overstated when it comes to OEE. Well-trained employees who understand the nuances of both their roles and the machinery they operate are invaluable assets. Training programs should focus on providing workers with both theoretical knowledge and practical skills to maximize efficiency. It’s about arming them with tools that lead to not just understanding, but also innovation and self-sufficiency.
Key elements of effective employee training programs include:
- Onboarding: New hires should receive comprehensive training covering not only their specific roles but also an overview of how their work impacts OEE.
- Cross-Training: Employees trained in multiple areas can fill in for each other, increasing flexibility and minimizing downtime.
- Continuous Learning: Encouraging ongoing development through workshops and seminars keeps staff engaged and up to date with the latest industry trends.
Well-rounded training enables employees to spot inefficiencies that may not be immediately obvious to management, creating an environment where everyone is pulling toward the same goal: higher OEE.
Regular equipment maintenance and employee training are essential pillars for improving Overall Equipment Efficiency. Without them, achieving high OEE scores can be a steep uphill battle.
By focusing on these best practices, organizations can not only enhance their metrics but also foster an internal culture focused on continuous improvement and operational excellence.
Technological Advances Influencing OEE
In today’s fast-paced industrial landscape, technological advancements play a pivotal role in how industries leverage Overall Equipment Efficiency (OEE). These innovations not only streamline processes but also facilitate the collection and analysis of data, enhancing decision-making at every turn. The integration of cutting-edge technology leads to improved visibility into operations, which is essential for identifying inefficiencies and optimizing performance. With the onset of trends like Industry 4.0 and the application of data analytics, understanding these influences on OEE can lead businesses to new heights.
Industry 4. and Smart Factories
Industry 4.0 represents the fourth industrial revolution, characterized by the interconnectivity of machines and systems through the Internet of Things (IoT). In smart factories, equipment is equipped with sensors that gather real-time data about performance, availability, and quality metrics. This data, in turn, is transmitted for analysis, enabling manufacturers to pinpoint inefficiencies promptly.
Key Elements:
- Automation: Automating repetitive tasks not only reduces error rates but also helps maintain a consistent quality level, a major factor influencing OEE.
- Real-Time Monitoring: With data flowing from machines continuously, companies can monitor their processes in real time, spotting issues before they escalate into costly downtimes.
- Predictive Maintenance: Utilizing machine learning algorithms allows businesses to predict equipment failures before they occur, ensuring minimal disruptions to production workflows.
By integrating these elements, industries are capable of achieving a higher OEE by minimizing planned and unplanned downtimes. Even small improvements in this metric can lead to significant financial gains over time.
Data Analytics Applications
The application of sophisticated data analytics tools has transformed how organizations interpret the data collected via modern machinery. These tools allow for deeper insights into performance metrics, enabling informed decision-making. For instance, advanced algorithms can identify patterns and correlations in operational data that may not be immediately obvious.
Benefits of Data Analytics:
- Enhanced Decision Making: Access to accurate data fosters a culture of data-driven decision-making, which is key for continuous improvement.
- Actionable Insights: Analytics can highlight specific areas of production that require attention, granting teams the ability to efficiently allocate resources.
- Benchmarking Performance: Historical data analysis helps companies establish benchmarks for performance, providing context for assessing efficiency over time.
"Merging technology with OEE strategies creates pathways to unprecedented efficiency and sustainability in operations."
As industries harness these technologies, the potential for improved performance becomes boundless, turning OEE from a mere concept into a dynamic metric that drives success.
Case Studies of OEE Optimization
In the realm of industrial efficiency, OEE optimization stands at the forefront. The ability to gauge how effectively a manufacturing operation utilizes its resources provides invaluable insight. Case studies illustrating OEE success not only showcase practical implementations but also highlight potential benefits. Through these real-world examples, decision-makers gain a deeper understanding of the multifaceted aspects of OEE and its direct impact on operational performance. Let's delve into notable case studies from different sectors to illustrate these points more effectively.
Manufacturing Sector
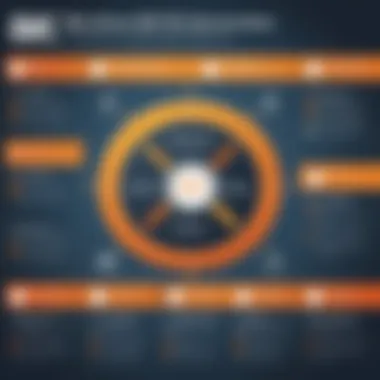
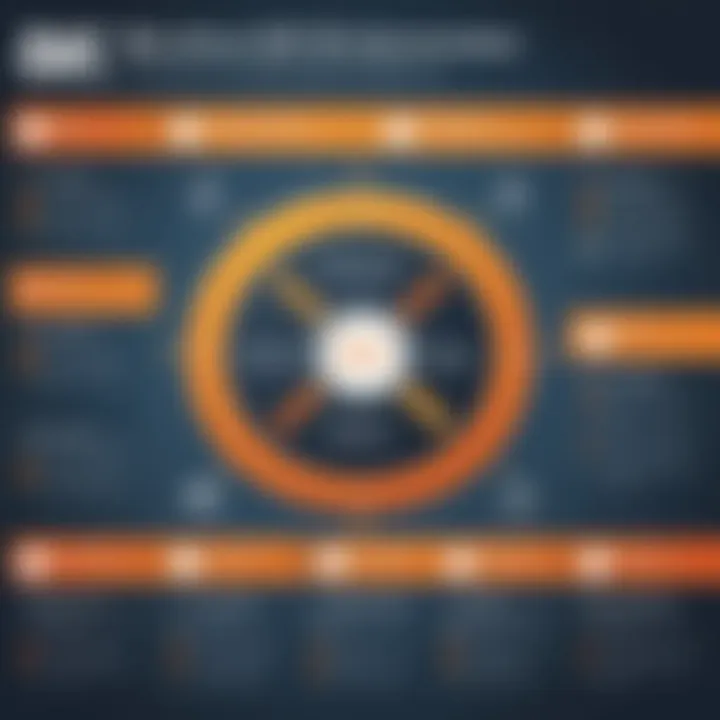
In the manufacturing field, OEE serves as a fundamental pillar. For instance, consider a prominent automotive manufacturer that faced significant downtimes, resulting in barely acceptable OEE scores. The leadership realized the need for a systematic approach. They initiated a comprehensive assessment of their processes.
After identifying the root causes of downtime, which included some equipment failures and operator inefficiency, they implemented a regular preventive maintenance schedule. Furthermore, they invested in training programs aimed at upskilling employees in precise operations. As a result, their OEE surged from a dismal 65% to an impressive 85% within a year. This translated to not only enhanced production but also substantial cost savings.
"By understanding where our losses were coming from, we optimized our workflow and addressed key pain points. The results exceeded our expectations." - Production Manager
This case illustrates how focusing on OEE in the manufacturing sector can yield marked improvements, benefiting overall productivity and profitability.
Food Processing Industry
Food processing also significantly leverages OEE metrics. A well-known snack food manufacturer, for instance, struggled with product quality issues leading to high scrap rates. As they examined their OEE data, they noted low scores partially attributed to product rejections due to manufacturing flaws.
To remedy this, they conducted thorough routine inspections and instituted new quality control protocols during production. They also collaborated directly with suppliers to ensure better quality raw materials, which played a pivotal role in reducing defects. After implementing these changes, their OEE improved from approximately 70% to above 90%. This not only enhanced production volume but also cultivated customer satisfaction through consistent product quality.
This highlights how integral OEE optimization is, not just for efficiency but for maintaining high standards of production in industries like food processing.
By examining these case studies, it becomes evident that optimizing OEE is not merely about math; it’s about creating a culture of continuous improvement. As industries evolve, the adaptability shown in these examples will be crucial for sustained success.
Comparing OEE with Other Metrics
When discussing the efficiency of industrial operations, Overall Equipment Efficiency (OEE) often takes center stage. However, it's essential to put OEE in context, particularly by comparing it to other performance metrics. This comparison helps in understanding its unique advantages and limitations, thereby allowing decision-makers and professionals to apply the right tools to measure and enhance productivity effectively.
OEE vs. First Pass Yield
First Pass Yield (FPY) is an important metric in the manufacturing sector. It measures the percentage of products manufactured correctly the first time without rework. Whereas OEE focuses on machine efficiency considering availability, performance, and quality, FPY zeroes in on the quality aspect alone.
- Benefits of FPY: This metric helps pinpoint quality issues early in the production process. It answers the question of whether a process is capable of generating products that meet specifications without the need for corrections or additional resources.
- Considerations: While FPY is invaluable for spotting problems quickly, it does not account for machine downtime or performance inefficiencies. For instance, a machine may produce high-quality output but not operate at optimal speed or may also suffer from frequent breakdowns.
In summary, while OEE provides a holistic view of both quality and machine effectiveness, FPY narrows the focus. Sticking to either one alone can lead to blind spots in production oversight. When used together, they can provide a more nuanced picture of operational health, potentially steering efforts for improvement in the right direction.
OEE vs. Scrap Rate
Another important metric to consider alongside OEE is the Scrap Rate (SR), which measures the percentage of materials that are discarded during the manufacturing process. A lower scrap rate typically indicates better quality control and material efficiency. However, its relationship with OEE is intricate.
- Benefits of Monitoring Scrap Rate: Keeping an eye on scrap rates enables companies to identify wastage and cost-saving opportunities. High scrap rates signal underlying issues in processes or inputs, urging companies to investigate further.
- Considerations: However, scrap rate does not tell the full story. It doesn’t incorporate how effectively production time is utilized or how many products were produced in relation to downtime. A machine could have a low scrap rate but still operate with significant inefficiencies or idling time, leading to a false sense of security regarding overall productivity.
Thus, while the scrap rate is a crucial metric to track, its insights are most powerful when integrated with OEE. Together, they paint a fuller picture of operational performance, allowing leaders to make informed decisions regarding production strategies.
The combination of OEE with metrics like FPY and Scrap Rate can yield valuable insights, pinpointing areas for improvement that might remain hidden when metrics are viewed in isolation.
Future of OEE in Industrial Settings
The realm of Overall Equipment Efficiency (OEE) is ever-evolving, shaped by advancements in technology and shifting industry needs. As we stride into a future increasingly characterized by sophistication and data-driven decisions, understanding the trajectory of OEE becomes paramount. Key aspects include how OEE intersects with industry trends, the benefits that follow its integration, and considerations that decision-makers must weigh.
Emerging Trends
Modern industries are witnessing a surge in innovative trends that significantly impact OEE. These trends aren't just passing fads; they represent fundamental shifts in how businesses operate.
- IoT Integration: The Internet of Things (IoT) connects machines and systems, providing real-time data. This constant flow of information helps in monitoring equipment health and tracking downtime, which contributes to better availability.
- Predictive Maintenance: Instead of waiting for breakdowns, businesses are utilizing predictive analytics to foresee when equipment might fail. This approach not only boosts availability but also reduces unnecessary maintenance costs.
- Lean Manufacturing: Lean principles, focusing on waste reduction, are becoming more intertwined with OEE metrics. By continuously analyzing workflows, companies can streamline operations, enhance quality, and ultimately raise their OEE scores.
- Collaborative Robots: Often referred to as cobots, collaborative robots are designed to work alongside humans. Their integration leads to increased efficiency in assembly lines while also accommodating labor shortages.
These trends showcase a decisive shift towards leveraging technology to maximize efficiency. As companies adopt these innovations, they will likely see an upward tick in their OEE scores.
Impact of Automation and AI
Automation and artificial intelligence (AI) play a monumental role in shaping the future of OEE. Their influence can't be understated, as they present avenues for remarkable efficiency improvements.
The following points illustrate their impact:
- Enhanced Data Analysis: AI tools can analyze vast datasets at speeds and accuracies that far exceed human capabilities. This allows firms to identify inefficiencies quickly and adjust processes in real time.
- Automated Reporting: Traditional reporting can consume substantial time and resources. AI streamlines this process, providing stakeholders with immediate access to OEE data, which helps in faster decision-making.
- Smart Decision Making: Machine learning algorithms can interpret trends and suggest action plans based on predictive data analytics.
- Resource Optimization: Automation reduces manual errors, enabling machines to achieve consistent performance levels. This stability in production directly correlates to quality improvements and minimized scrap rate.
The role of AI and automation in enhancing OEE metrics represents a frontier of operational excellence that every industry should consider adopting.
In summary, the future of OEE in industrial settings will be intricately woven with these advances. Companies that start embracing these trends and technologies today are likely to not just improve their OEE but also position themselves as leaders in efficiency and productivity.
Culmination
In wrapping up our exploration of Overall Equipment Efficiency (OEE) within industrial metrics, it’s essential to emphasize the profound impact that this metric has on enhancing production outcomes. The significance of OEE can't be overstated, as it serves as a lens through which industries can scrutinize their operational efficacy. By understanding and applying OEE, manufacturers stand to gain not just measurable improvements, but also insights that lead to more informed decision-making.
Summarizing Key Points
When considering OEE, a few crucial elements emerge:
- Components of OEE: Availability, performance, and quality are the pillars of this metric. Each component sheds light on different aspects of production effectiveness.
- Calculating OEE: Understanding both the basic and advanced calculations helps organizations pinpoint areas needing attention. It paves the way for realizing potential gains from seemingly minor adjustments.
- Challenges in Implementation: Recognizing data collection challenges and cultural resistance enables companies to strategize effectively for smoother implementation.
- Future Trends: With Industry 4.0 ushering in technological advancements, keeping an eye on emerging trends ensures that industries remain agile and adaptive.
"By leveraging OEE and embracing its broader applications, businesses often unlock pathways to unprecedented levels of efficiency and productivity."
Final Thoughts on OEE Application
As we navigate our way through an evolving industrial landscape, the application of OEE metrics becomes increasingly vital. The continuous quest for improvement drives industries to integrate OEE with innovative technologies such as AI and real-time data analytics. The interplay of these elements often leads to not just enhanced efficiency, but also a stronger competitive edge in the market.
Moreover, fostering a culture that prioritizes OEE awareness among employees cultivates a proactive approach towards operational challenges. It's not simply about crunching numbers but about weaving OEE into the very fabric of the organizational mindset. As industries propel towards future advancements, maintaining a sharp focus on OEE could be their golden ticket to sustained success.