Manufacturing Process Monitoring Software: An In-Depth Guide
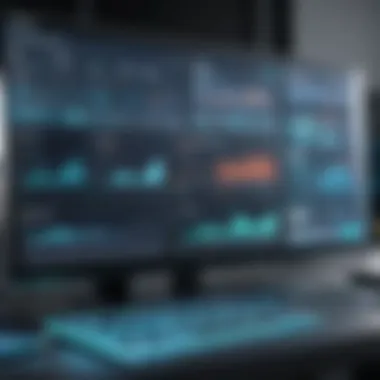
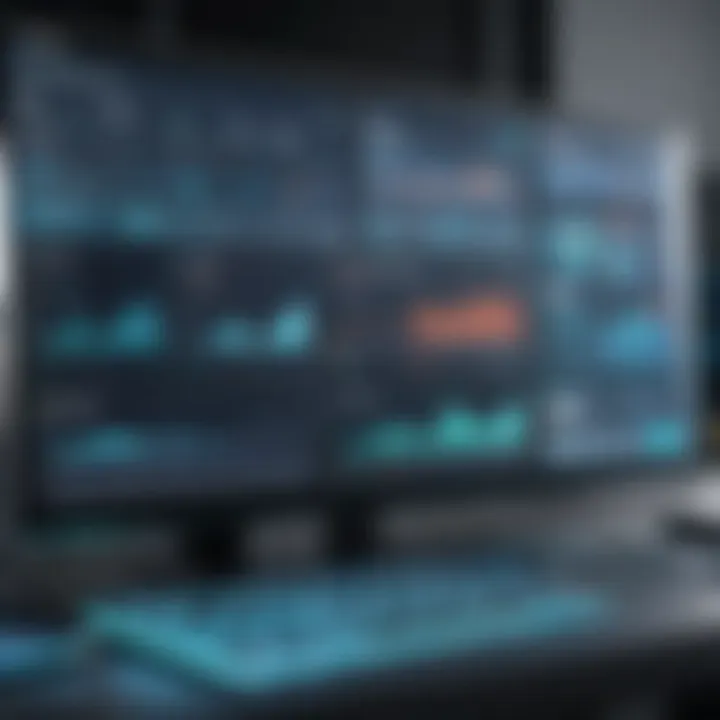
Intro
In the whirlwind of modern industry, the need for precision and efficiency has never been higher. Manufacturing process monitoring software stands at the forefront of this transformation, acting as a pivotal tool for organizations aiming to navigate the complex waters of production. At its core, this type of software is designed to track, analyze, and optimize manufacturing operations, ensuring that everything from raw material acquisition to final product delivery is executed seamlessly.
This article takes a comprehensive look at the functionalities and advantages of manufacturing process monitoring software. By breaking down the essential features, comparing various solutions, and exploring the implications of Industry 4.0, we hope to provide a clear path for manufacturing businesses to enhance their operations. Furthermore, we will delve into the specific applications of these tools across differing sectors, as well as discuss the integration capabilities that are essential in today's tech-driven environment.
With the ever-evolving landscape of manufacturing fueled by technology, understanding these software solutions is a critical step for decision-makers, IT professionals, and entrepreneurs who seek to harness the power of data for their operational needs. Let's explore this topic with a fine-toothed comb.
Understanding Manufacturing Process Monitoring Software
In the complex world of manufacturing, keeping a sharp eye on processes is not just a luxury—it's a necessity. Manufacturing process monitoring software plays a vital role in ensuring that production runs smoothly and efficiently. Without it, your operations might as well be a ship lost at sea, vulnerable to a storm of inefficiencies and errors. Understanding how this software functions, its benefits, and its overarching importance can help decision-makers, IT professionals, and entrepreneurs navigate the choppy waters of modern production environments with confidence.
The significance of manufacturing process monitoring software can be viewed through various lenses: operational efficiency, data quality control, and cost management among other aspects. When deployed effectively, such software collects and analyzes real-time data, enables swift decision-making, and minimizes downtime. It's like having a detailed map in a vast and unpredictable terrain where each data point is a marker guiding businesses toward their goals.
Definition and Purpose
Manufacturing process monitoring software can be defined as tools designed to observe, control, and optimize production processes. Its primary purpose is to provide a systematic way to track performance indicators, manage workflow, and facilitate communication between different parts of the manufacturing ecosystem. You might think of it as the nervous system of a factory—constantly gathering signals and providing feedback to ensure everything runs like a well-oiled machine.
When implemented, this software not only assists in day-to-day operations but also plays a crucial role in strategic planning. For instance, predictive analytics features can tap into historical data to forecast potential disruptions or identify areas for improvement. Whether it’s ensuring the right amount of materials is on hand or alerting operators to abnormal conditions, the purpose of this software is to remove the guesswork from manufacturing processes.
Historical Context
The evolution of manufacturing process monitoring software has been tied closely to advancements in technology and changing industry needs. From the early days of assembly lines, where simple mechanical gauges indicated production rates, to today’s sophisticated systems equipped with IoT integration, the journey reflects the shift towards smarter manufacturing.
Not many would realize that the seeds of such technology were sown back in the mid-20th century. Initially, manual inspections and rudimentary electronic systems were dominant. However, as globalization and competition intensified in the latter part of the century, the need for greater efficiency and quality assurance became paramount, prompting manufacturers to explore automated solutions.
By the turn of the 21st century, more interconnected systems emerged, and the advent of Industry 4.0 catalyzed a transformation that integrated advanced sensors, data analytics, and machine learning capabilities. Today’s monitoring software is not merely a watchful eye; it's a dynamic tool that adapts in real-time, making informed recommendations and adjustments, reflecting an awareness previously thought impossible in manufacturing processes.
Key Features of Monitoring Software
In the realm of manufacturing, the significance of monitoring software cannot be overstated. Key features of such software directly contribute to operational excellence, ensuring that processes run smoothly and efficiently. By understanding these features, businesses can better align their needs with the right tools for success.
Real-Time Data Collection
Real-time data collection stands out as a fundamental element of monitoring software. It captures critical metrics as they happen, which is crucial for making immediate adjustments. Rather than relying on periodic reports that might offer a distorted view due to delay, real-time data equips decision-makers with up-to-the-minute visibility of processes. This feature alone can reduce the risk of delays, production faults, and quality issues. Imagine a production line where a bottleneck is detected instantly, allowing for immediate intervention to alleviate the issue; this is the power of real-time data.
Moreover, real-time data collection enhances collaboration among different departments in a manufacturing setup. For instance, the production team can collaborate seamlessly with maintenance crews, as everyone stays updated about the machinery's operational status, thus avoiding unexpected downtime. Such coordination is invaluable for maintaining a steady flow of production, ultimately contributing to a more robust bottom line.
Data Visualization and Reporting
Data visualization and reporting are arguably the lifeblood of effective monitoring software. The significance of translating complex raw data into a visual format cannot be overlooked. Graphs, charts, and dashboards provide a straightforward way for users to identify trends, assess performance, and spot anomalies. For example, if a specific machine consistently shows a decline in efficiency visualized through a line graph over weeks, it becomes clear where attention is needed.
These tools not only simplify the analysis process but also enhance strategic planning. Management can make informed decisions by quickly interpreting visualized data. Automated reporting further adds to the efficiency, as users receive comprehensive reports without needing to sift through piles of numerical data.
"The ability to visualize data is like having a map on a complex journey. It doesn’t just show you the way; it highlights the obstacles and opportunities."
Alerts and Notifications
Alerts and notifications may often be underestimated, yet they are crucial for timely responses and proactive management. When a production system encounters irregularities—be it a temperature spike, a drop in output, or even a need for maintenance—instant alerts enable quick action. This timely communication is essential as delays could result in cascading issues down the production line.
Furthermore, these alerts can be customized based on the user's role and needs. A floor manager may want immediate notices about equipment errors, while an executive may prefer daily summaries of operational health. This flexibility ensures that key personnel are always in the loop, no matter their level.
In summary, key features such as real-time data collection, data visualization, and alerts are the backbone of any effective manufacturing monitoring software. They transform data into actionable insights, streamline communication, and facilitate better decision-making, paving the way for enhanced operational efficiency and quality control.
Benefits of Implementing Monitoring Software
In the fast-paced world of manufacturing, implementing monitoring software is a game changer. It's not just about having the latest technology; it's about transforming operations to be more efficient, reliable, and aligned with quality expectations. The integration of such software brings substantial rewards that stretch across the organization.
Improved Operational Efficiency
Operational efficiency is at the heart of every successful manufacturing business. Implementing monitoring software allows for a streamlined approach to production. It collects data from various stages of the manufacturing process, allowing managers to identify bottlenecks and areas for improvement with remarkable clarity. This swift access to insights enables the ability to make real-time decisions that can propel productivity.
Moreover, by automating routine data collection and analysis, companies can eliminate the tedious manual processes that often consume precious time and resources. For example, a factory utilizing monitoring software can observe a 20% reduction in downtime simply by adjusting maintenance schedules based on live performance data. This means workers can focus on value-adding tasks, rather than chasing after equipment failures or errors.
"A stitch in time saves nine." This old saying rings true in manufacturing as timely interventions can prevent larger issues from compounding down the line.
Enhanced Quality Control
Quality control is non-negotiable in manufacturing. A single defect can not only derail a batch of products but can also tarnish reputation and erode customer trust. Vintage quality assurance methods are giving way to sophisticated monitoring systems that scrutinize every aspect of the production line.
With monitoring software, manufacturers can track quality metrics continuously. For instance, intelligent cameras and sensors incorporated into the production line can measure product specifications and alert operators immediately if something deviates from the norm. This immediate feedback loop means quality issues can be addressed on the spot, rather than waiting for post-production testing. Such proactive measures enhance overall product quality and reduce rework costs significantly, creating a consistent experience for customers.
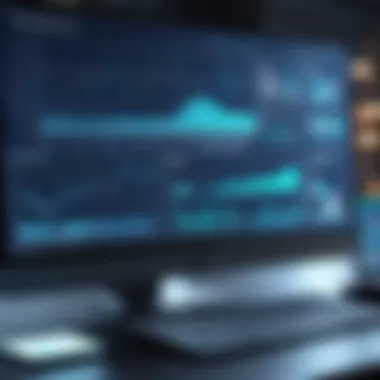
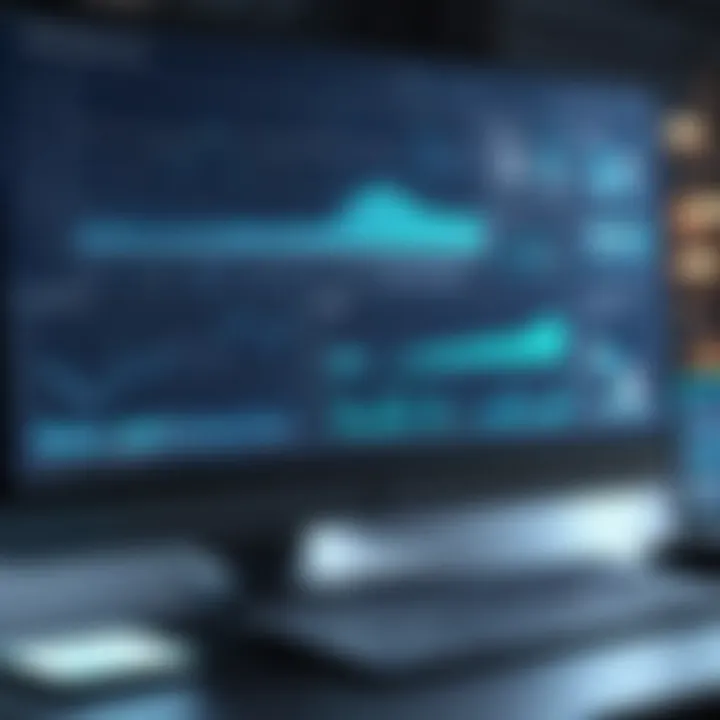
Cost Reduction and Waste Minimization
Businesses operate on slim margins, making cost management crucial. Monitoring software identifies inefficiencies that lead to excess spending. By closely analyzing the production process, businesses can uncover hidden costs linked to waste—whether it's material wastage, energy inefficiencies, or unnecessary labor.
For instance, a company may find that certain machinery consumes power inefficiently during off-peak hours. Recognizing this allows them to optimize usage patterns or upgrade to energy-efficient machines, leading not only to lower bills but also a reduced carbon footprint. Moreover, with waste minimization strategies rooted in data insights, manufacturers can often save thousands in raw material costs. The bottom line is that informed decisions based on monitored data help businesses streamline their spend, thus boosting profit margins.
This trifecta of benefits—operational efficiency, enhanced quality, and cost reduction—shows that monitoring software isn’t just an added layer; it’s a fundamental aspect of modern manufacturing that can propel a company towards success.
Types of Manufacturing Monitoring Software
Choosing the right manufacturing monitoring software is pivotal for organizations striving toward enhanced efficiency and productivity. Different types of software cater to specific operational needs, making it crucial to understand the options available. Each serves a unique function, whether it’s managing overall production processes, ensuring quality control, or integrating various business functions. This section will discuss three primary types of manufacturing monitoring software: Manufacturing Execution Systems (MES), Quality Management Systems (QMS), and Enterprise Resource Planning (ERP) Systems. Understanding these categories can help in making informed decisions that align with business objectives.
Manufacturing Execution Systems (MES)
Manufacturing Execution Systems, or MES, play a critical role on the shop floor. They bridge the gap between enterprise-level systems, like ERP, and the equipment on the production line. By providing real-time data and insights into every aspect of the manufacturing process, MES helps in overseeing operations effectively. It can track production metrics, manage scheduling, and even control inventory levels.
- Key Benefits of MES:
- Real-time monitoring enables quick decision-making.
- Streamlined processes lead to reduced lead times.
- Enhanced traceability aids in compliance with industry regulations.
Implementing MES can be a game changer, especially within industries that demand high levels of precision and regulatory adherence. Organizations are more often leaning on MES to gain an edge in productivity and reduce operational hiccups.
Quality Management Systems (QMS)
Quality Management Systems focus on ensuring that products meet certain quality standards. For manufacturers, maintaining a consistent level of quality control is vital to minimizing defects and maximizing customer satisfaction. A well-implemented QMS can help businesses document processes, manage audits, and conduct inspections to maintain high quality at every phase of production.
- Essential Features of QMS:
- Automation of quality procedures reduces human error.
- Integrated reporting provides insights for continuous improvement.
- Compliance management ensures adherence to industry standards such as ISO.
Adding a QMS into the manufacturing process means that control becomes systematic rather than reactive. This results in fewer recalls, a better reputation, and increased customer loyalty.
Enterprise Resource Planning (ERP) Systems
Enterprise Resource Planning (ERP) Systems are comprehensive solutions managing various business processes across an organization. For manufacturers, ERP systems integrate multiple functions, including finance, HR, production, and supply chain management, into a single cohesive system. This integration leads to improved information flow and operational transparency.
- Major Advantages of ERP in Manufacturing:
- Centralized data enhances reporting accuracy and consistency.
- Demand forecasting capabilities lead to better inventory management.
- Scalability allows organizations to grow without overhauling existing systems.
For decision-makers, ERP systems offer a holistic view of business health. By tracking key performance indicators across departments, they enable more strategic choices that align with corporate goals.
"Choosing the right type of software isn't just about technology; it's about aligning tools with your business strategy to achieve maximum operational efficiency."
Integration with Existing Systems
In the realm of manufacturing process monitoring, the ability to seamlessly integrate new software with pre-existing systems cannot be overstated. This integration is vital for ensuring that operations run smoothly and that data flows freely between various platforms. A well-planned integration strategy can significantly enhance the efficiency of production processes, facilitate better decision-making, and ultimately, lead to better business outcomes.
When a manufacturing firm considers adopting monitoring software, it encounters a patchwork of existing systems. These can range from outdated machinery to more sophisticated enterprise resource planning solutions. Therefore, addressing integration from the get-go is crucial. Failing to acknowledge integration possibilities can lead to siloed data, inconsistencies, and even disruptions in production.
Moreover, ensuring compatibility not just saves time and resources but lays a solid foundation for effective utilization of the new software. The benefits are multifold, leading to improved productivity, real-time data accessibility, and enhanced visibility across operations.
Compatibility Challenges
Integration is rarely smooth sailing; challenges are nearly always on the horizon. One of the most pronounced issues manufacturers face is compatibility with older systems. Many factories still rely on legacy systems that were not designed to communicate effectively with modern software solutions.
From my experience, compatibility issues often arise due to:
- Data Formats: Old systems might use non-standard data formats, making it hard for new software to read and interpret the data accurately.
- Communication Protocols: If the new monitoring software uses protocols that the existing equipment does not support, then those systems can’t share data.
- Hardware Limitations: Some older hardware may not have the capacity to integrate with advanced software, requiring upgrades or replacements that can be costly.
These challenges necessitate a careful evaluation of current infrastructure before implementing new monitoring solutions.
Integration Strategies
Navigating the integration maze can seem daunting, but there are practical strategies that firms can implement to ease the process. Here are a few approaches:
- Conducting a Thorough Assessment: Before integrating any new monitoring software, it's vital to analyze the existing systems thoroughly. Understand data flow, identify bottlenecks, and ascertain which parts can benefit from integration.
- Choosing Flexible Software: Opt for software known for its easy integration capabilities. Look for solutions that offer APIs and support standard communication protocols, as these features can pave the way for simpler integration.
- Investing in Middleware: Sometimes direct connections between old and new systems just are not feasible. In such cases, middleware can help bridge the gap allowing communication to flow between both systems.
- Working with Experienced Vendors: Collaborating with a vendor experienced in integration can save a lot of headaches. They usually have the expertise and tools necessary to facilitate smoother transitions.
- Pilot Testing: Before a full-blown implementation, conducting a pilot test can help identify potential issues in a controlled environment. This step is invaluable, as it allows for troubleshooting before the software is rolled out on a larger scale.
Being proactive about integration can result in a harmonious blend of systems, leading to optimized operations and a maximization of the software's capabilities.
Integrating new systems effectively can streamline data aggregation and enable informed decision-making, making it a pillar for successful operations.
Navigating the integration landscape of manufacturing process monitoring software may seem overwhelming at first, but with robust strategies in play, organizations can make successful transitions that yield fruitful results.
Challenges in Manufacturing Process Monitoring
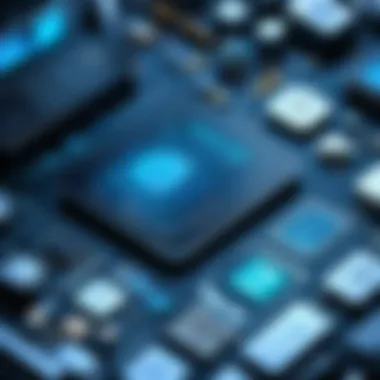
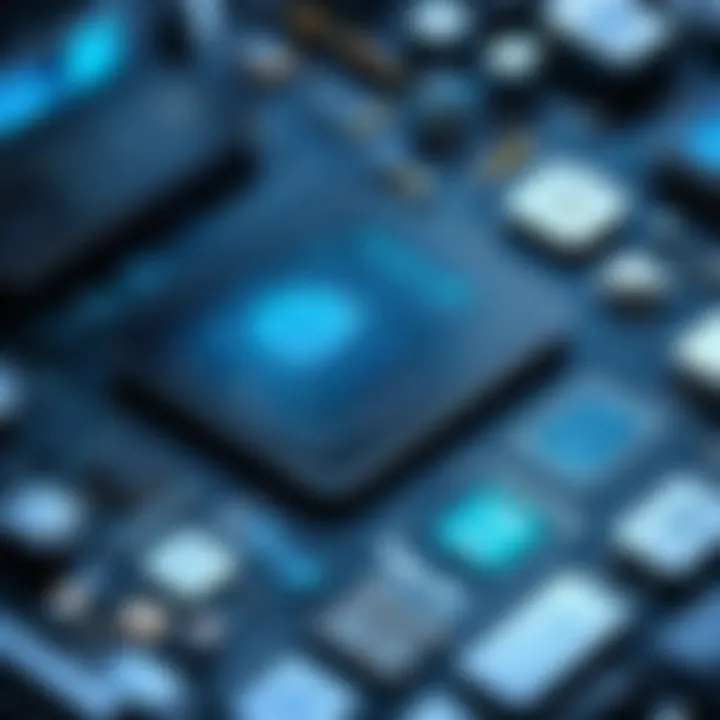
The manufacturing industry has embraced a plethora of technologies aimed at enhancing efficiency and quality. However, the integration of monitoring software presents numerous challenges that cannot be overlooked. Addressing these issues is pivotal for businesses seeking to harness the full potential of these systems. Understanding the hurdles can guide enterprises in establishing a robust framework that safeguards their investments and aligns with their operational strategies.
Data Security Concerns
In the age where data reigns supreme, security stands as a paramount concern for manufacturers. With the rise of interconnected systems, the threat landscape has expanded. Hackers may target sensitive operational data, intellectual property, and even customer information. For example, a breach in an automotive plant's monitoring system could potentially result in the theft of design blueprints or proprietary manufacturing processes.
To mitigate these risks, companies must adopt a multi-layered security approach. Implementing firewalls, encryption protocols, and securing access controls are just a few measures that can protect against potential breaches. Moreover, regular audits can help in identifying vulnerabilities before they become critical issues. In short, prioritizing data security not only protects valuable information but also bolsters trust and reliability within the manufacturing ecosystem.
User Adoption and Training
Despite having the best software, all that glitters isn’t gold if the users don’t know how to use it. User adoption and training emerge as critical components in the successful implementation of monitoring software. Resistance to change is a natural human reaction, especially when employees are accustomed to legacy systems. If not addressed, it can lead to underutilization of the software, ultimately diminishing its intended benefits.
To overcome this challenge, organizations should tailor training programs that cater to the varying tech-savviness of their workforce. Using a mix of hands-on sessions, tutorials, and continuous support can greatly enhance the onboarding process. Furthermore, adopting a change management strategy that includes employee feedback can pave the way for smoother transitions.
It’s also beneficial to highlight real-world applications of the software and encourage users to share their experiences. When employees see the tangible benefits in their daily tasks, they are more likely to embrace the software wholeheartedly.
Cost of Implementation
The financial investment associated with implementing monitoring software cannot be brushed aside. Companies often grapple with both the direct and indirect costs involved. From the initial licensing fees to the ongoing maintenance and necessary hardware upgrades, the expenses can pile up. Additionally, companies must factor in the costs of training staff to effectively use the new system.
Effective budget planning involves not only understanding these costs but also recognizing the potential return on investment (ROI). It’s crucial to weigh the costs against the anticipated improvements in efficiency and quality control. For instance, while a monitoring system may require a significant upfront investment, the subsequent reduction in waste and increase in operational efficiency can yield substantial savings over time.
To help navigate these financial intricacies, companies may consider phased implementation strategies. By gradually rolling out the software and measuring its impact, organizations can make adjustments along the way and better manage their budgets.
"In the world of manufacturing, understanding challenges ahead can mean the difference between success and struggles."
By thoroughly addressing these challenges, organizations can position themselves for a successful integration of manufacturing process monitoring software. Taking proactive steps to enhance data security, fostering user adoption, and strategically managing implementation costs will solidify their path towards operational excellence.
Role of Industry 4. in Monitoring Software
The advent of Industry 4.0 signified a transformative era in manufacturing that leverages advanced technologies to improve operational efficiencies. This section explores how Industry 4.0 shapes monitoring software, driving greater innovation and providing businesses with an opportunity to enhance their manufacturing processes.
Smart Manufacturing
At the core of Industry 4.0 is the concept of smart manufacturing, which encapsulates the use of interconnected systems to drive efficiency and flexibility. Smart factories integrate cyber-physical systems, cloud computing, and cognitive computing. This synergy enables real-time monitoring, predictive analytics, and adaptive responses to manufacturing challenges.
The importance of smart manufacturing is evident in its ability to:
- Reduce Downtime: With real-time data monitoring, manufacturers can swiftly identify and resolve issues before they escalate, ensuring that operations continue smoothly.
- Enhance Resource Management: Efficient use of resources is crucial. Smart manufacturing allows for precise tracking of materials and machinery, reducing waste and ensuring optimal output.
- Tailor Production: As customer demands shift, smart manufacturing facilitates the quick reconfiguration of production lines to meet new requirements without massive overhauls.
In sum, smart manufacturing instills agility into production processes, allowing manufacturers to respond promptly to changes in the market or operational challenges. The integration of these technologies into monitoring software not only boosts production but also enhances overall product quality.
Internet of Things (IoT) Integration
IoT integration is the backbone of Industry 4.0, connecting devices and systems that were previously isolated. In manufacturing, this translates to machines and sensors communicating seamlessly, providing a wealth of data for monitoring software to analyze.
The advantages of incorporating IoT into manufacturing monitoring systems are substantial. For one, the connectivity of devices allows for seamless data collection from various points across the production floor. This means that anything from temperature levels in a manufacturing plant to machinery performance can be tracked and analyzed. Here are some key benefits of IoT integration:
- Continuous Data Flow: IoT devices continuously feed data into monitoring systems, enabling businesses to make informed decisions based on current conditions rather than historical data.
- Predictive Maintenance: By examining trends from IoT data, companies can anticipate when machinery might fail and perform maintenance only as necessary, rather than on a rigid schedule.
- Enhanced Decision-Making: Data from IoT devices help in crafting strategies that align closely with real-time operational metrics, thus driving smarter decisions.
To sum it up, the integration of IoT enhances monitoring capabilities within manufacturing, positioning firms to take advantage of smart decision-making processes and paving the way towards a future where adaptability is paramount.
In the rapidly evolving landscape of manufacturing driven by Industry 4.0, embracing smart manufacturing and IoT integration is not just an option. It is a necessary shift for companies aiming to remain competitive.
Case Studies of Successful Implementations
In examining the landscape of manufacturing process monitoring software, the significance of practical case studies cannot be overstated. They offer tangible proof of the software’s effectiveness and benefits, serving as blueprints for potential adopters. These case studies spotlight real-world applications and showcase the myriad ways companies successfully harness these tools to enhance productivity, quality, and overall operations. When decision-makers approach software selection, these examples provide a much-needed reality check, illustrating not just the theoretical advantages but also the hurdles encountered and overcome during implementation.
By reflecting on the successes of diverse industries, businesses can glean insights into critical elements such as flexibility, automation, and user engagement, which in turn help to inform best practices in their journey toward optimized manufacturing processes.
Case Study in Automotive Manufacturing
The automotive industry serves as a prominent example of successful manufacturing process monitoring software implementation. A notable case is that of a major automotive manufacturer that faced declining efficiency and an uptick in defects. To address these challenges, they deployed a sophisticated monitoring software that integrated seamlessly with their existing Manufacturing Execution Systems (MES).
Key aspects of the implementation included:
- Real-time Performance Tracking: The software allowed for continuous monitoring of machine performance and production throughput. This feature identified bottlenecks in production swiftly, helping managers take corrective actions before small issues snowballed into larger problems.
- Enhanced Quality Control: By utilizing integrated quality control checks, the manufacturer significantly reduced defect rates. The system automated inspections at various stages of production, allowing for immediate feedback and minimizing waste.
- Employee Training and Adaptability: What stood out in this case was the emphasis on training the workforce to adapt to the new technology. Employees engaged with live data feeds to understand machine performance deeply, allowing them to react proactively rather than reactively.
Case Study in Electronics Production
In the electronics sector, another relevant example showcases how monitoring software revolutionized a leading company that produces intricate circuit boards. They decided to adopt a Quality Management System (QMS) alongside their monitoring software to ensure every step in their production process could be scrutinized and optimized.
Highlights from this case study include:
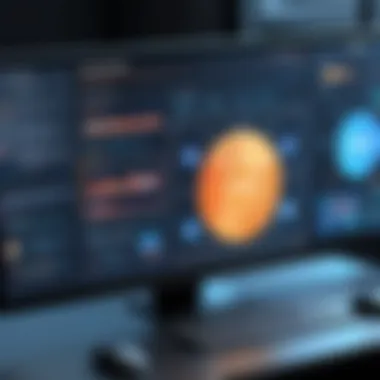
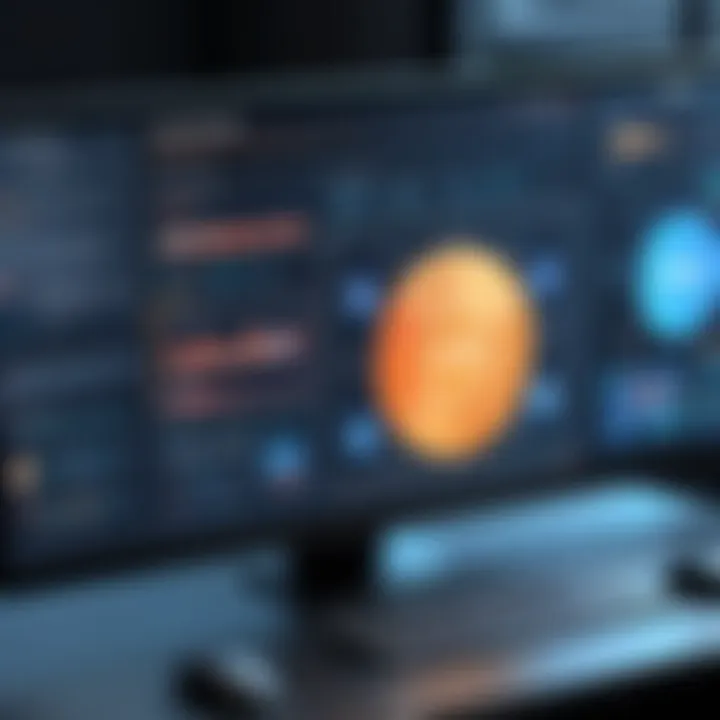
- Integration with IoT Devices: By integrating Internet of Things (IoT) devices, the company achieved real-time data collection from various production units. This laid the foundation for predictive analytics, allowing them to foresee equipment failures before they caused delays.
- Data Visualization and Reporting: The use of advanced data visualization tools transformed how the management team perceived production data. Key performance indicators (KPIs) were easy to interpret, fostering informed decision-making.
- User Engagement and Feedback Loops: Creating a culture of feedback was crucial. The company actively sought input from users regarding the new monitoring tools, which informed future updates and modifications, ultimately leading to high user satisfaction rates.
Both case studies underscore crucial considerations: the importance of alignment between technology and organizational goals, and the necessity for training to address user adaptation. Implementing manufacturing process monitoring software, backed by solid case studies, lays a roadmap for companies to follow for successful software adoption that directly improves processes and outcomes.
Choosing the Right Monitoring Software
Selecting suitable manufacturing process monitoring software is a pivotal decision that can have far-reaching implications for an organization. The manufacturing industry is rapidly evolving, and with the relentless pursuit of efficiency and precision, the software tools companies choose to implement are more vital than ever. It isn't just about picking a system; it's about ensuring that the solution aligns seamlessly with business objectives, existing workflows, and future growth plans. The right choices can bolster productivity and quality, while the wrong ones can lead to inconsistencies and failure to achieve organizational goals.
When assessing which monitoring software fits your needs, it's crucial to reflect on specific elements that can define success. Key considerations include functionality, compatibility with current systems, ease of use, and the ability to scale as demands change. Each organization will have distinct parameters based on their unique operations, and making the right decision can save time, money, and resources in the long haul.
Assessment Criteria
To pounce on the most suitable monitoring solutions, a thorough assessment of various criteria is necessary.
Here are specific elements that should be evaluated:
- Functionality & Features: Does the software provide real-time data analytics, alerts, and reporting capabilities? Information should be easy to access and analyze, providing actionable insights.
- Usability: Is the interface intuitive? If the users find it complicated, it will hinder productivity. Proper ease of use ensures that staff can adapt quickly without arduous training.
- Integration Capability: How well does it integrate with existing systems like ERP, MES, or QMS? Smooth integration can reduce downtime and contribute to seamless operations.
- Scalability: Will the software accommodate future growth? It’s vital to think about long-term requirements to avoid switching solutions again.
- Cost-effectiveness: Does the ROI justify the implementation costs and ongoing maintenance fees? Understanding both immediate and long-term financial implications is key.
Vendor Reputation and Support
Choosing a reputable vendor can significantly influence the successful implementation and ongoing operation of the software. The importance of vendor credibility cannot be understated. A well-established vendor often indicates reliability, extensive experience, and a dedication to customer service. You want a partner who will stand by you, especially when navigating tough challenges that may arise post-implementation.
Here are a few factors to consider:
- Track Record: Vendors with positive testimonials and proven success in similar industries generally inspire more confidence.
- Customer Support: What kind of support does the vendor offer? Support services should be readily available, with responsive customer service channels understanding of manufacturing challenges.
- Community and Resources: A supportive community can provide valuable insight and exchange of ideas. Look for vendors that engage in forums or have customer reference programs.
- Training and Resources: Quality training tools provided by the vendor are crucial for helping your team utilize the software fully. Training minimizes disruption when rolling out new software.
Brands like Siemens, Rockwell Automation, and SAP offer comprehensive support and are noted for their robust software solutions. However, the final choice should always relate to specific needs and context.
As companies navigate the vast landscape of manufacturing process monitoring software, they must tread carefully through the myriad offerings. By focusing on diligent assessment criteria coupled with a thorough understanding of vendor capabilities, businesses can position themselves for achieving not just operational efficiency but also sustainable growth.
"Investing in the right technology now can pave the way for innovations that enhance operational excellence and drive industry leadership."
Navigating through the process requires strategic thinking and clarity of purpose, but the dividends of such planning are substantial.
Future Trends in Manufacturing Process Monitoring
The landscape of manufacturing process monitoring is rapidly evolving, influenced by advancements in technology and shifting industry demands. Understanding future trends in this realm is vital for decision-makers aiming to stay competitive and efficient. As organizations seek to leverage emerging technologies, it's paramount to consider how these developments will impact operational efficiency, product quality, and ultimately, the bottom line.
Predictive Analytics
Predictive analytics is making waves in manufacturing process monitoring. It refers to the use of statistical algorithms and machine learning techniques to identify the likelihood of future outcomes based on historical data. By analyzing patterns, manufacturers can foresee equipment failures, predict maintenance needs, and optimize production schedules.
This capability greatly reduces downtime. Instead of adopting reactive maintenance strategies, organizations can plan maintenance when it is most convenient, thereby avoiding disruption in the manufacturing flow. Beyond just maintenance, predictive analytics can also forecast demand, enabling manufacturers to adjust inventory levels accordingly. Here are some ways predictive analytics can be integrated:
- Machine Health Monitoring: Sensors installed on machines can collect data that analytics can assess for wear and tear, allowing preemptive action before issues escalate.
- Quality Assurance: By analyzing past quality data, manufacturers can identify factors leading to defects, enabling them to take corrective actions early in the process.
Implementing predictive analytics does come with challenges, such as ensuring data integrity and the need for skilled personnel. However, the potential benefits make it a worthwhile consideration for forward-thinking manufacturers.
Augmented Reality Applications
Augmented reality (AR) is another innovative trend that is enhancing manufacturing process monitoring. It overlays digital information on the physical world, allowing workers to visualize and interact with data in real-time. This can significantly improve training, maintenance, and operational efficiency.
For example, technicians can use AR glasses to receive immediate visual guidance on machine repairs or operational procedures. Instead of fumbling through manuals, they can access step-by-step instructions projected directly onto the equipment they’re working on. The benefits of AR include:
- Enhanced Training: New employees can undergo immersive training without the risk of making costly mistakes on the production floor.
- Real-Time Decision Making: Access to data in context allows workers to make faster and more informed decisions.
"Augmented reality empowers workers with insights that were once trapped behind screens, transforming how they interact with machines."
Both predictive analytics and augmented reality signal a shift towards more data-driven and interactive manufacturing processes. As these trends become more commonplace, manufacturers who embrace them will likely see substantial improvements in production efficiency and effectiveness. Adapting to these future trends, while navigating their associated challenges, will position organizations for sustained competitive advantage in an increasingly sophisticated manufacturing landscape.
Culmination
In summing up the extensive details provided throughout this article, it’s essential to understand that the world of manufacturing process monitoring software is not just a technological advancement; it's a requisite for survival and success in today’s high-stakes environment. The integration of this software means businesses can awaken a sleeping giant of efficiency, leverage data like never before, and streamline processes that were once a tangled mess.
Summary of Insights
To grasp the full breadth of insights shared, let’s break it down:
- Enhanced Efficiency: Employing monitoring software can substantially amplify operational effectiveness, leading to faster production times and reduced downtime.
- Quality Control: A sophisticated suite of tools assists in maintaining consistently high standards, considerably lowering defect rates and customer complaints.
- Data Utilization: With real-time data collection and visualization, management can make more informed decisions swiftly, staying ahead of prospective issues before they escalate.
- Adaptability to Change: Software options available today are increasingly designed to integrate seamlessly with existing systems. The possibilities presented by the Internet of Things (IoT) and Industry 4.0 allow for unprecedented flexibility in manufacturing processes.
In addition, considerations surrounding cost reduction and waste minimization lay a sturdy foundation for implementing these tools. The challenge now lies in finding the right software that aligns with specific operational needs.
Final Thoughts on Software Selection
Selecting the right manufacturing process monitoring software is akin to finding the right key for a lock—without it, efficiency remains locked away. Here’s what decision-makers ought to ponder:
- Assessment Criteria: Evaluate the software against established criteria to ensure it meets your operational demands. This includes user-friendliness, support resources, and the ability to scale.
- Vendor Reputation: A vendor's history tells a story. Look for experience in your industry and check their support reliability. After all, a supportive provider can make or break your software experience.
- Long-Term Viability: Software isn’t just a short-term investment. Consider how the software will adapt as your manufacturing processes evolve.
So, as businesses inch forward into a future filled with intelligent systems and automated workflows, judiciously selecting the right monitoring software is vital. This bears the possibility not just for enhanced output, but for a more robust, informed, and competitive presence in the marketplace.