A Deep Dive into Katana Smart Manufacturing Software
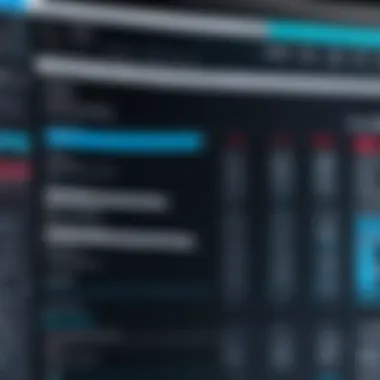
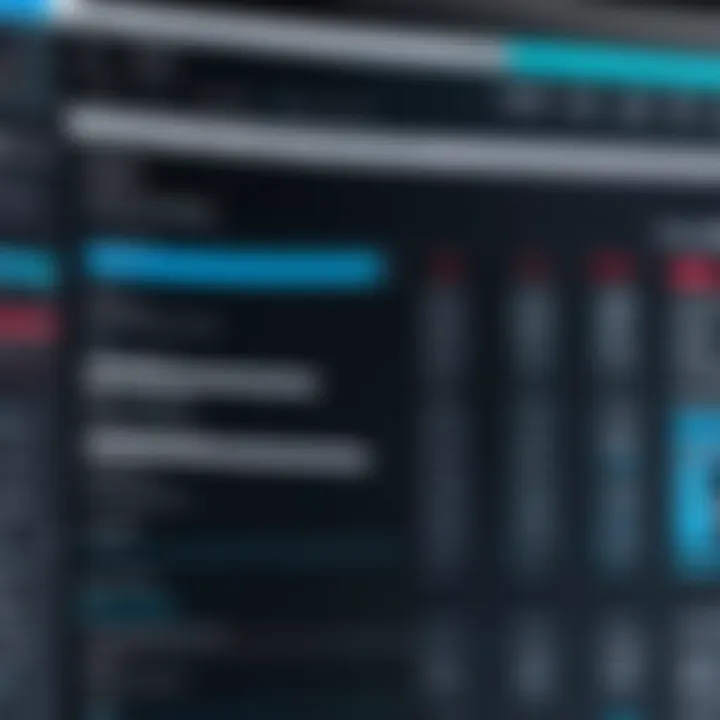
Intro
In the rapidly changing world of manufacturing, companies are on a quest for tools that can streamline their operations and enhance overall efficiency. Among these tools, Katana Smart Manufacturing Software has emerged as a significant player that promises to transform modern production processes. This discussion dives deep into how Katana can change the game for manufacturers, looking closely at what makes it tick, the benefits it offers, and how it stands against rival solutions in the market.
Katana is not just another software; it’s designed with a keen focus on integrating diverse manufacturing components into a seamless operation. As manufacturing environments grow more complex, the capacity to adapt and integrate is imperative. This article will guide industry professionals through a comprehensive overview of the software's key features and implications.
Key Software Features
When evaluating any software, especially in the manufacturing domain, one has to consider its foundational features and advanced capabilities.
Essential functionalities
At its core, Katana offers functionalities that address both the operational needs and strategic goals of a manufacturing business. Some essential features include:
- Real-time inventory management: This feature empowers users to keep a pulse on stock levels, enabling more informed decision-making and reducing the likelihood of overstocking or stock shortages.
- Production scheduling: Users can build complex schedules that accommodate shifting demands and resource availability. The ability to prioritize orders efficiently is crucial for manufacturers looking to enhance responsiveness.
- Order tracking: With Katana, managing orders from creation to fulfillment becomes transparent and straightforward. This not only improves customer satisfaction but also enhances internal accountability.
Advanced capabilities
Beyond the basics, Katana provides sophisticated functionalities designed to elevate manufacturing efficiency:
- Integrations with third-party tools: The software seamlessly connects with various platforms, ensuring that businesses can customize their tech stacks without facing compatibility issues. Whether it’s accounting software or e-commerce platforms, Katana can play nice.
- Data analytics: By harnessing real-time data, users can glean insights about their manufacturing processes, spotting bottlenecks or inefficiencies quickly. This empowers businesses to make data-driven decisions that ultimately enhance productivity.
- User-friendly interface: The dashboard is designed for ease of use, allowing team members at all levels to engage with the software effectively without a steep learning curve.
"Investing in the right software like Katana is not just about improving operations today, but about positioning for competitive advantage tomorrow."
Comparison Metrics
Understanding how Katana stacks up against competitors is essential for making informed decisions.
Cost analysis
In terms of pricing, the software provides various pricing tiers to cater to businesses of different sizes. A detailed analysis of the total cost of ownership, including subscription fees and potential integration costs, reveals valuable insights into financial commitments over time.
Performance benchmarks
In comparing performance benchmarks, Katana has demonstrated a significantly reduced lead time and improved accuracy in inventory management compared to many other solutions out there. Looking at case studies or user testimonials can help paint a clearer picture of its performance in real-world settings.
While gathering insights on software like Katana, one must consistently think critically about the specific needs of their operation. It's not a one-size-fits-all scenario. The alignment of Katana’s features with your operational requirements might just be the key to enhancing productivity and maintaining a competitive edge.
Prologue to Smart Manufacturing
In today's fast-paced industrial landscape, the term smart manufacturing has become increasingly relevant. It encompasses the use of advanced technologies to streamline production processes, optimize resource utilization, and enhance overall efficiency. Understanding smart manufacturing isn't just beneficial—it's essential for businesses seeking to maintain their edge in a competitive market. The integration of cutting-edge software solutions, such as Katana, allows manufacturers to harness real-time data and automate routine tasks, providing a pathway for transformation.
Smart manufacturing leverages various technologies such as the Internet of Things (IoT), cloud computing, and artificial intelligence. These tools enhance the visibility of operations and enable manufacturers to respond swiftly to market demands. It’s about creating a smarter factory where machines communicate seamlessly with humans. This synergy leads to better decision-making, optimized supply chains, and ultimately, higher profitability.
Defining Smart Manufacturing
At its core, smart manufacturing refers to the use of digital technologies to collect and analyze data across the production line. This data-driven approach facilitates informed decision-making, allowing companies to adapt their processes and strategies. The key components involve interconnected systems that can sense, collect, and transfer information in real-time.
For example, imagine a factory floor where sensors placed on machinery send alerts about equipment malfunctions before they lead to significant downtime. By having these insights at their fingertips, operators can address issues promptly, reducing delays and costs associated with repairs. Thus, smart manufacturing can dramatically improve operational resilience.
The Evolution of Manufacturing Technologies
Manufacturing has seen a monumental shift over the past few decades, evolving from traditional methods to automation and now to smart technologies. The journey began with mechanization and eventually transitioned to the first industrial revolution, which introduced steam power. Fast forward to the second industrial revolution, characterized by electrification and assembly lines, and we witness a transformation in efficiency and productivity.
Now, we find ourselves in the fourth industrial revolution, often referred to as Industry 4.0. This new era combines digital technologies with physical production processes. In this context:
- Automation has become more sophisticated, employing robotics and AI to reduce human intervention.
- Data analytics plays a crucial role, offering insights that enable smarter decision-making.
- IoT devices create a connected network of machines, allowing for a more streamlined flow of information.
As we probe into smart manufacturing's capabilities, it’s apparent that continuous evolution represents not just a trend, but a necessity for survival and growth in modern manufacturing. Business leaders must embrace these changes, ensuring they are not left behind as technology shapes the future of the industry.
"Staying on top of these trends is not just about technology adoption; it's about rethinking how we operate and innovate."
In summary, understanding smart manufacturing plays a pivotal role in navigating today’s manufacturing terrain. It’s a bridge connecting resources, processes, and market demands, ultimately guiding businesses toward sustained success.
Understanding Katana Software
Understanding Katana Software is crucial, as it provides insights into how this tool can transform manufacturing processes. In an age where efficiency and agility are kings, Katana stands out by seamlessly integrating core functionalities that cater to the unique needs of modern manufacturers. This understanding isn’t just about recognizing a software’s features but grasping its strategic implications for businesses.
The significance of Katana lies in its ability to tackle operational pain points and streamline workflows. Decision-makers and IT professionals alike need to appreciate the software's user-friendly design, which makes complex processes easier to manage. It is an invitation to rethink how inventory, production, and order management interconnect.
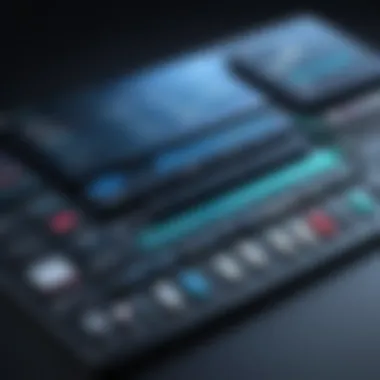
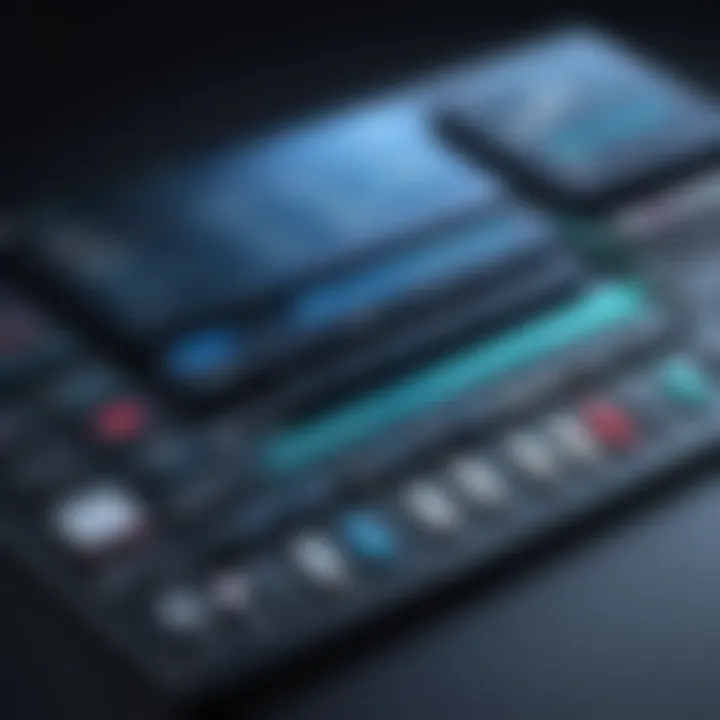
Overview of Katana Smart Manufacturing Software
Katana Smart Manufacturing Software is tailored to address the intricacies of manufacturing in today’s fast-paced environment. This platform connects various aspects of production, providing an integrated approach to manage resources effectively. With its cloud-based architecture, it ensures that teams have access to real-time data from anywhere. This is particularly crucial for companies that operate across multiple locations or have remote teams.
Key Features and Functionalities
The relevance of key features cannot be overstated. They stand as the backbone of Katana, supporting the cornerstone of efficiency and productivity in manufacturing operations.
Real-time Inventory Management
Real-time inventory management is one of Katana's standout features. It allows manufacturers to monitor their stock levels continuously, linking raw materials directly to production schedules. This feature enhances accuracy in stock tracking and reduces uncertainty.
A key characteristic of this functionality is its synchronization with sales channels, enabling automatic updates in inventory levels when orders are placed. It is a welcomed choice in the industry as it minimizes the risk of overstocking or stockouts, which can cripple operational flow.
A unique aspect of Katana’s real-time inventory management is its simplicity in implementation; users can quickly adapt to the system without extensive training. This ease of use is advantageous for small to mid-sized enterprises that often lack the resources for detailed onboarding processes. However, manufacturers must also be aware of the potential challenges, such as initial setup time and the need for continual data accuracy, as these issues can complicate the initial transition.
Production Scheduling
Production scheduling is another critical feature that elevates Katana above many of its competitors. This tool assists in allocating resources efficiently, scheduling tasks based on availability and priority. By facilitating clear timelines and resource assignments, Katana empowers businesses to streamline operations and meet tight deadlines.
What makes this aspect particularly popular is its visual layout, providing a comprehensive overview of the production process. This user-friendly feature allows managers to see at a glance where bottlenecks might occur, enabling proactive adjustments. However, the unique feature of customizable workflows may encounter resistance, since changing existing processes within a company requires buy-in across various departments.
Order Management
Order management within Katana offers a way to efficiently handle customer orders from inception to completion. This feature stands out because it connects customer requests directly to the production wheelhouse, facilitating a more fluid response to market demands.
A notable characteristic is the integration with e-commerce platforms, which keeps order information current and reduces data entry errors. This functionality positions Katana as a suitable choice for businesses aiming to enhance the customer experience through timely deliveries and consistent communication. However, the complexity of managing multiple sales channels can be a downside if not handled cautiously, as it may lead to confusion if orders are not Batched properly.
Integration and Compatibility
In the world of smart manufacturing, the integration and compatibility of software solutions like Katana play a crucial role in achieving operational harmony. Most businesses today rely on a patchwork of systems, and for many, seeing those systems work together seamlessly can spell the difference between success and struggle. Without integration, information resides in silos, preventing a holistic view of operations, which can lead to delays and increased costs.
When a manufacturing software can smoothly integrate with existing systems, it enhances the overall productivity of the organization. It streamlines communication and reduces the risk of error that arises from manual data entry. Compatibility with other platforms ensures that businesses can maintain the status quo of their operations while reaping the benefits of modern solutions without the overwhelming need to overhaul their entire system.
A few benefits to consider when discussing integration and compatibility include:
- Enhanced Data Flow: The smoother the data flow between existing ERP systems and Katana, the more real-time insights can be generated, which is vital for informed decision-making.
- Cost Savings: Integrating new software can eliminate the cost associated with duplicate systems and reduce the resource allocations needed for data management.
- Scalability: As businesses grow or pivot their strategies, integrated systems provide the flexibility to adapt without major disruptions.
Existing ERP Systems
When it comes to existing ERP systems, their role in manufacturing cannot be overstated. They serve as the backbone of operations, handling everything from supply chain management to accounting. For a system like Katana to be truly effective, it must be able to communicate with and complement these established ERPs. Given that many manufacturers might already have invested significant resources into their ERP systems, making the switch to a new software can sometimes feel like jumping through hoops.
Katana has a knack for integrating with widely-used ERP systems such as QuickBooks and Xero. This means that users can effectively monitor inventory levels, reduce discrepancies in financial reporting, and align orders with production schedules without the usual hassle. Integration allows data to flow freely, ensuring all teams are on the same page and can work collaboratively towards common goals.
E-commerce Platforms
In today’s digital marketplace, e-commerce platforms have become indispensable for businesses aiming to harness their online sales potential. Integrating Katana with e-commerce platforms like Shopify and WooCommerce allows manufacturers to streamline their order fulfillment process significantly. When orders can be processed, tracked, and fulfilled efficiently, customers are happier, ultimately leading to improved customer satisfaction rates.
By connecting Katana with e-commerce platforms, businesses can:
- Automate Order Processing: Orders received online can trigger automated workflows, ensuring production aligns with customer demands swiftly.
- Achieve Accurate Inventory Updates: With real-time updates, inventory levels are accurate across all sales channels, reducing the likelihood of overselling or stockouts.
- Enhance Data Analytics: E-commerce platforms come equipped with valuable sales insights, and pairing that data with Katana allows businesses to make data-driven decisions that can craft better marketing and operational strategies.
Integration and compatibility are more than just buzzwords in the world of smart manufacturing; they are critical enablers of efficiency, productivity, and customer satisfaction. As organizations move forward, leveraging these connections will likely be pivotal in shaping the landscape of modern manufacturing.
Benefits of Implementing Katana
The implementation of Katana Smart Manufacturing Software is not just a trend, but a substantial leap forward in how manufacturing processes can be optimized. Manufacturers who harness such tools gain not only operational insights but also a distinct competitive edge. The myriad of advantages that come with Katana extends across the board, influencing various facets of a business. Understanding these benefits can illuminate pathways to enhance productivity and customer satisfaction while cutting costs effectively.
Enhancing Operational Efficiency
When it comes to operational efficiency, Katana shines. The software’s real-time data tracking allows businesses to keep a finger on the pulse of production cycles, inventory levels, and order statuses. An example could be a small manufacturer who previously struggled with managing its stock effectively. By integrating Katana, they experienced a notable decline in missed deadlines and overproduction.
The visual dashboards and user-friendly interface help decision-makers spot inefficiencies in their workflow. Quick adjustments can be made based on current operational data. Being able to see the entirety of a process—and adjust it in real-time—makes all the difference. The emphasis is always on smarter, faster, and more precise operations, which ultimately leads to an unprecedented level of productivity.
Improving Customer Satisfaction
Customer satisfaction is a linchpin of long-term success in manufacturing. With Katana, businesses can ensure products are available when customers want them. By streamlining order and inventory management, the software allows a manufacturer to meet customer demands swiftly.
Imagine a small furniture maker who struggled to fulfill custom orders on time. By adopting Katana, they managed to improve their production scheduling, leading to quicker turnaround times. As a result, their clients were pleased—revamping the company's reputation and driving repeat business.
Regular communication with customers regarding orders is also facilitated. Status updates become seamless, which fosters trust and reliability. All in all, using Katana leads to happier customers, and happy customers can translate into increased sales and loyalty over time.
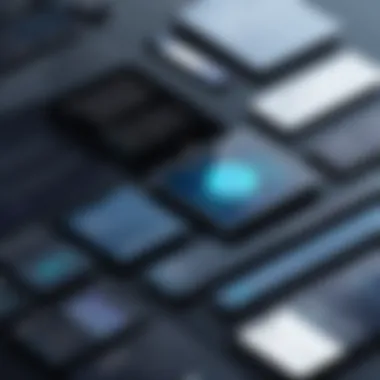
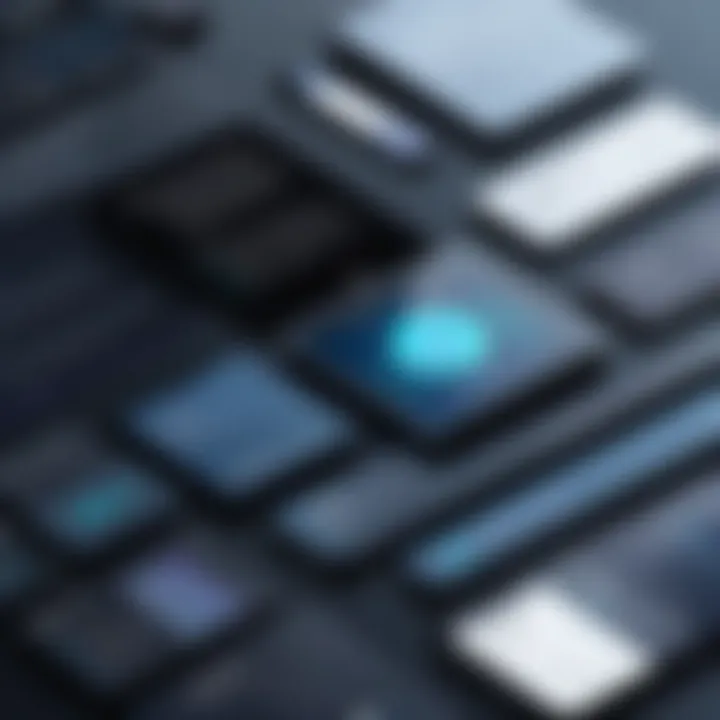
Cost Reduction Strategies
One of the most attractive aspects of implementing Katana is its potential for cost reduction. The software provides valuable insights into cost management. By identifying waste in processes and suggesting efficiencies, Katana plays a crucial role in trimming the fat off production costs.
A practical case is that of a small electronics firm. Prior to adopting Katana, they faced regular overstocking, which tied up funds unnecessarily. Post-implementation, they optimized their inventory levels substantially, which freed up cash flow and allowed for reinvestment in other areas. The software’s ability to analyze purchasing patterns also helps businesses negotiate better deals with suppliers, further contributing to cost savings.
"Technology used wisely can uncover not just savings, but also new avenues for growth."
In summary, the benefits of implementing Katana extend well beyond immediate operational improvements. By enhancing efficiency, boosting customer satisfaction, and pinching penny wisely, manufacturers can forge a future that not only keeps the wheels turning but accelerates growth in a competitive marketplace.
User Experience and Interface
When it comes to any software, particularly one involved in manufacturing processes, the User Experience (UX) and Interface (UI) are paramount. They can mean the difference between a seamless operational flow and a frustrating experience that hampers productivity. Katana Smart Manufacturing Software places significant emphasis on these aspects, understanding that a well-designed user interface not only reduces the length of time needed for training but also enhances overall user satisfaction.
Navigational Simplicity
Navigational simplicity is more than just aesthetic appeal; it serves as a lifeline for users who rely on the software to perform crucial tasks effectively. Katana smartly prioritizes intuitive navigation, ensuring that users can easily find their way around the platform without feeling lost in a maze of options. This is particularly important in environments where time is of the essence.
For example, rather than burying vital functionalities under layers of menus, Katana provides a clean layout with clearly labeled sections. A user can jump directly to inventory management or production schedules with just a click or two. This straightforward structure can be a game changer, especially for businesses trying to onboard new employees who may be unfamiliar with the software.
Benefits of navigational simplicity include the following:
- Speed: Users can quickly access the tools they need, saving precious time.
- Reduced Error Rates: A clear interface minimizes the chance of mistakes that often arise from confusion.
- User Retention: When employees find a system easy to navigate, they are more likely to engage with it consistently.
Customization Options
The modern work environment is anything but static; customization plays a critical role in adapting software to specific business needs. Katana recognizes this by offering a range of customization options that allow users to tailor their interface and workflows according to their unique operational demands.
Customization can manifest in various forms, from personalized dashboards to adjustable reporting parameters. For instance, a manufacturing firm dealing with different product lines might prefer a dashboard that highlights performance metrics for each line distinctly. By allowing users to modify their interface, Katana enhances the utility and relevance of its software.
Some key aspects of customization include:
- Visual Personalization: Users can adjust colors or layouts to create a familiar workspace, encouraging comfort and productivity.
- Functional Adaptability: Companies can modify workflows to fit their processes rather than forcing their processes into a one-size-fits-all mold.
- Scalability: As businesses grow, the ability to adapt and expand software functionalities becomes indispensable.
"A software that adapts to its users rather than the other way around is a sign of true innovation."
Challenges in Adoption
Adopting new technologies, particularly in the realm of smart manufacturing, comes with its fair share of hurdles. The introduction of Katana Smart Manufacturing Software epitomizes this struggle, as organizations strive to harness its full benefits while navigating the complexities that arise. Recognizing these challenges is vital for decision-makers because overcoming them not only improves operational efficiency but also enhances long-term strategic positioning in the market.
Resistance to Change
One of the most prominent hurdles to the successful implementation of Katana software is the resistance to change among staff and management. The manufacturing landscape has traditionally relied on well-established routines; any deviation from these practices might be met with skepticism. Here are a few key points to consider:
- Cultural Barriers: Companies often develop a culture resistant to new technologies. Employees may fear redundancy or feel overwhelmed by the prospect of learning a new system.
- Knowledge Gaps: Some workers may lack the necessary skills, making the idea of transitioning to an advanced platform like Katana daunting. Addressing these gaps through comprehensive training is essential yet can be resource-intensive.
- Misconceptions: There's a tendency to underestimate the capabilities of Katana, viewing it as an unnecessary tool rather than a potential game-changer that can streamline processes and yield greater productivity.
Cultivating an environment that embraces change is crucial. Organizations need to communicate the value of technology effectively, ensuring that both management and the workforce acknowledge the long-term benefits of adopting tools like Katana.
Integration Complexities
Another significant challenge lies in the integration complexities associated with implementing Katana with existing systems and processes. The manufacturing ecosystem often involves multiple software platforms that serve different purposes; tying them all together seamlessly can be tricky. Consider the following:
- Compatibility Issues: Integrating Katana with legacy systems may reveal compatibility issues. Older software might not support the latest technologies, necessitating costly upgrades or, in severe cases, complete overhauls.
- Data Migration: Transitioning existing data to the new platform can become a logistical nightmare. It's imperative to ensure that data from various sources is consolidated accurately to avoid discrepancies.
- Interdepartmental Coordination: The implementation process often requires collaboration between various departments like IT, production, and finance. If these groups do not effectively communicate and coordinate, it may lead to misunderstandings and a lack of cohesive strategy.
Navigating these challenges demands meticulous planning and a unified approach. Setting clear goals and involving key stakeholders from various departments early in the process can pave the way for a smoother adoption of Katana Smart Manufacturing Software.
Comparative Analysis with Competitors
In the rapidly evolving landscape of smart manufacturing, understanding how Katana software stacks up against its competitors is crucial for businesses looking to enhance their operational capabilities. The comparative analysis with competitors sheds light on the specific advantages that Katana offers, alongside any gaps it might have in relation to other solutions available in the market. Such a scrutiny not only informs purchasing decisions but also drives improvements in software features, ensuring that companies choose the most fitting tools for their needs.
Examining Alternative Software Solutions
When looking at the myriad of smart manufacturing software options, it’s helpful to consider a few key players in the field alongside Katana. Here are some examples of alternative software solutions available:
- Fishbowl: Focused heavily on inventory management, Fishbowl offers robust manufacturing and warehouse management features, though it may lack some flexibility in production scheduling compared to Katana.
- NetSuite: A cloud-based ERP system that provides comprehensive manufacturing capabilities, but can be more costly and complex to implement, making it less appealing for smaller businesses.
- Odoo: This open-source platform presents a unique offering with endless customization. However, its broad scope can lead to a steeper learning curve for users unfamiliar with such systems.
Each of these alternatives has its strengths—be it in scalability, integration, or cost-efficiency. However, the crux lies in whether they meet the specific demands of a business.
Identifying Unique Selling Points
Katana's unique selling points distinguish it in the crowded market of smart manufacturing software. Understanding these can aid decision-makers in determining its fit for their organization. Here are several of Katana's standout attributes:
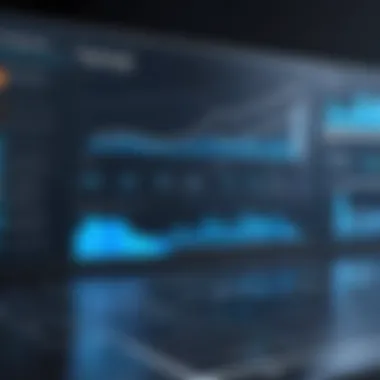
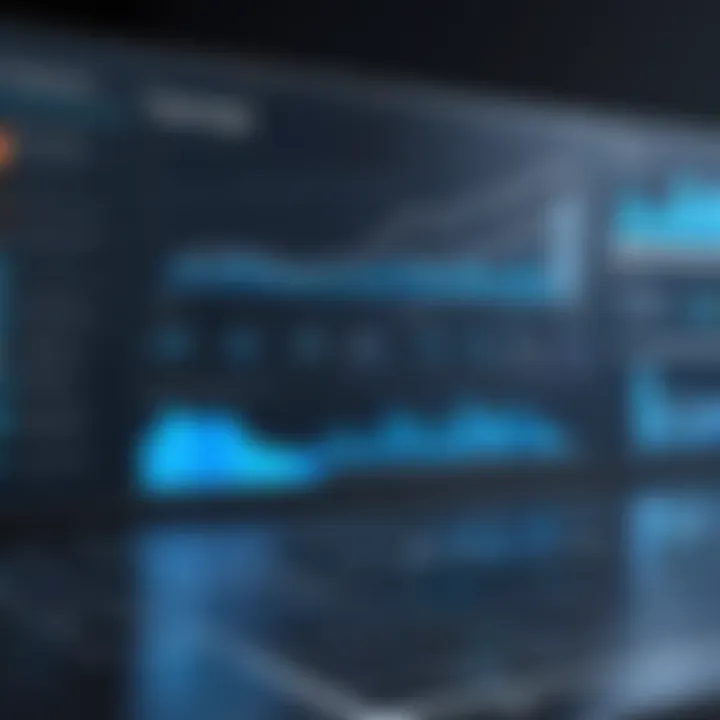
- Intuitive Interface: Users often note the simplicity and clarity of Katana’s layout. The design reduces the learning curve, enabling quicker onboarding for teams.
- Real-time Data Insights: Katana excels in delivering real-time inventory and production data. This immediacy allows businesses to respond swiftly to market changes and operational needs.
- Seamless Integrations: Whether linking with e-commerce platforms or existing ERP systems, Katana offers strong connectivity. This flexibility enables manufacturers to maintain data consistency across their operations, which is often a stumbling block in other tools.
"Selecting the right manufacturing software is about fitting it to how you operate, not just picking the most popular solution on the market."
In sum, while many software solutions claim to support manufacturing efficiency, Katana’s specific strengths make it an attractive option for businesses aiming to thrive in today’s competitive environment. Its user-friendly design combined with real-time capabilities positions it as a strong contender amongst the alternatives available.
Future Outlook for Katana
Looking toward the future of Katana Smart Manufacturing Software is like peering into a crystal ball. With rapid advancements in technology, understanding the trajectory of such software is essential for stakeholders and industry professionals. This forward-looking analysis will highlight not just the possibilities that lie ahead but also the growing significance of Katana in an increasingly competitive manufacturing landscape.
Emerging Trends in Manufacturing Software
The manufacturing world is changing at a breakneck pace, affecting how companies choose and implement software solutions. One such trend is the rise of cloud-based software. As more companies shift from traditional on-premise systems to cloud environments, Katana positions itself as a frontrunner, ensuring real-time accessibility and scalable solutions that are essential for modern-day operations.
As businesses increasingly rely on data-driven decision-making, AI and machine learning are becoming commonplace in manufacturing software. Katana’s potential to incorporate these technologies could revolutionize operational processes, impacting everything from inventory management to production efficiency. This shift toward smart automation means that users can expect tailored solutions that not only respond to data but can also predict outcomes.
Moreover, collaboration tools integrated within manufacturing software are gaining traction. As remote work continues to be a viable option for many businesses, having software that allows teams to work together seamlessly becomes crucial. Katana’s capacity to enhance collaboration and communication in real-time can be a game-changer, proving instrumental in driving project success.
Innovation and Updates to Anticipate
The road ahead for Katana is paved with potential updates that could significantly enhance its functionalities. Staying ahead requires commitment to innovation. Look for enhancements in user interface design; easier navigation and visuals can optimize user experiences and increase productivity. If Katana incorporates adaptive learning algorithms, it may learn from user habits, further simplifying processes and minimizing training times.
Expect also a higher degree of integration with other systems and tools. Businesses today use a slew of software. Katana can enhance its value by working smoothly with existing structures, creating a more cohesive operational atmosphere.
Lastly, as regulatory standards and sustainability concerns grow, Katana could release features aimed at compliance tracking and environmental impact assessments. Companies are increasingly held accountable for their production processes. By incorporating a suite that addresses these elements, Katana will not only keep users compliant; it will also support businesses committed to responsible manufacturing.
"The future is not something we enter. The future is something we create."
- Leonard I. Sweet
Case Studies
Case studies are not merely illustrative examples; they are invaluable narratives that bring to life the practical applications of Katana Smart Manufacturing Software. They lay bare the specific scenarios in which the software can thrive or falter. By deep diving into real-world experiences, decision makers can glean insights on optimization opportunities, financial implications, and the potential challenges associated with the adoption of this software. Not only do these case studies illuminate the capabilities of Katana, but they also serve as a source of motivation and guidance for businesses contemplating a shift towards smart manufacturing.
Successful Implementations
Successful implementations of Katana offer a glimpse into the transformative potential that effective smart manufacturing can impart on businesses. The experiences of companies that have adopted the software often echo a similar narrative: an increase in productivity, enhanced visibility in operations, and improved resource allocation.
For instance, a medium-sized furniture manufacturer in the United States leveraged Katana’s real-time inventory management to reduce excess stock levels by 30%. By switching from manual tracking methods to this intelligent system, they not only optimized their workflows but also significantly cut costs associated with storage and excess inventory. As the production runs became more predictable, the scheduling became less of a headache, leading to timely deliveries and satisfied customers.
- Key Highlights from Successful Implementations:
- Enhanced tracking of materials and finished goods.
- Increased communication between sales teams and production schedules.
- Ability to react quickly to market changes, much like a chameleon changing colors.
Lessons Learned from Challenges
As illuminating as the success stories are, the lessons gleaned from challenges during implementation help paint a fuller picture. Every pioneering journey carries its share of obstacles. Some businesses faced resistance from employees reluctant to embrace new technologies or restructured workflows. For example, a textile company adopting Katana encountered pushback from workers who preferred their legacy systems.
Understanding that change isn’t always well-received is critical. The leadership team in this case offered training sessions, demonstrating the software’s benefits firsthand. The result? A remarkable shift in attitudes. Employees went from doubters to advocates of the system, witnessing firsthand how it simplified their tasks and reduced burdens.
- Significant Takeaways from Overcoming Challenges:
- Investing in thorough training mitigates fear of the unknown.
- Addressing user concerns directly helps build trust in the new system.
- Continuous feedback loops promote a culture of improvement and adaptation.
In summation, the rich tapestry of case studies related to Katana Smart Manufacturing Software—highlighting normative successes and learning from missteps—provides a robust framework for understanding its applications in diverse industrial contexts. As organizations navigate their own paths to digital transformation, these stories form an essential toolkit for informed decision-making.
The End
The conclusion of this article serves as the capstone to the investigation of Katana Smart Manufacturing Software and its implications for the manufacturing sector. Recognizing the nuances of its integration capabilities, enhanced user experience, and the myriad challenges it presents is critical for decision-makers, IT professionals, and entrepreneurs alike. We have traversed through its key features and analyzed the advantages that Katana can bestow on an organization, from operational efficiencies to improved customer satisfaction.
Summarizing Key Takeaways
Several key insights emerged throughout our exploration of Katana's framework. These include:
- Real-time Insights: Katana facilitates immediate visibility into inventory and production status which accelerates decision-making processes.
- Customization Flexibility: The platform's adaptability allows businesses to tailor processes to their distinct needs, promoting seamless workflows.
- Integration with Various Platforms: Capabilities for smooth integration with existing ERP systems and e-commerce platforms create a cohesive technological landscape, simplifying operations.
- Cost-Efficiency: Implementing Katana's solutions has shown potential for lowering operational costs, contributing to healthier profit margins.
These takeaways underscore the importance of selecting a manufacturing software solution that aligns with organizational goals while addressing specific pain points.
Final Thoughts on Katana's Role in Modern Manufacturing
In closing, it is evident that Katana Smart Manufacturing Software represents more than just a tool; it is a catalyst for transformation within the manufacturing landscape. By harnessing its powerful capabilities, businesses not only enhance their productivity but also foster innovation and adaptability.
As manufacturing continues to evolve in a rapidly changing digital environment, Katana stands as a pivotal player capable of guiding organizations through the complexities of modern production needs.
"The future is not something we enter, the future is something we create." - Leonard I. Sweet
Embracing this innovation is not merely optional; it is essential for those wishing to remain competitive in today's fast-paced market. Consideration of Katana's role in your operational strategy could very well determine the trajectory of your business in the years to come.