Mastering Inventory Management in Manufacturing
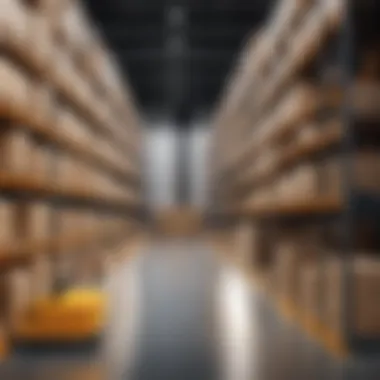
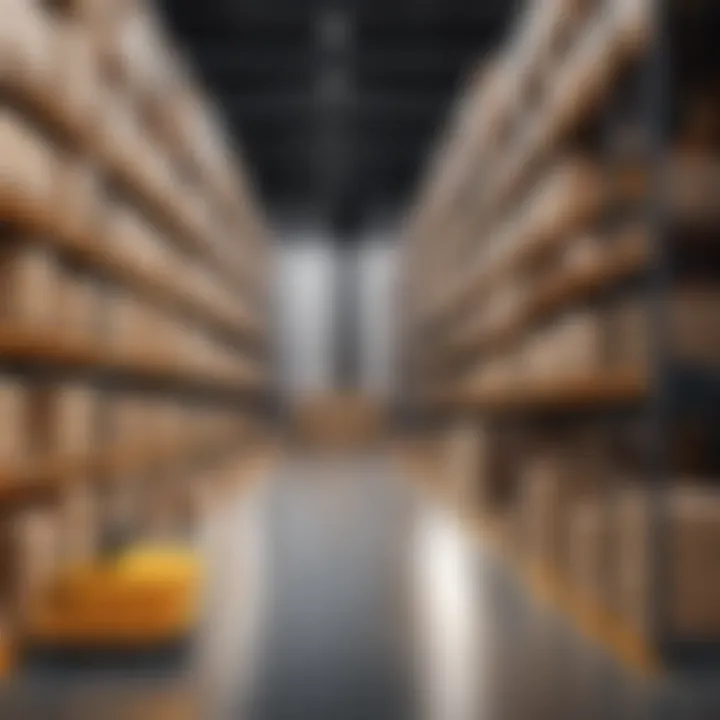
Intro
Managing inventory effectively in the manufacturing sector is critical for sustaining operations and maximizing profit margins. The challenges of aligning supply with demand while minimizing costs can be daunting. As market conditions shift, businesses must adapt their inventory management strategies to maintain a competitive edge.
This guide aims to unpack the complexities of inventory management, focusing on actionable strategies and tools rather than theoretical discussions. With the right approach, manufacturing firms can streamline processes, enhance efficiency, and ultimately drive cost reductions.
Key Software Features
The integration of software solutions into inventory management practices can greatly enhance overall effectiveness. The following sections outline essential functionalities and advanced capabilities that decision-makers should consider when evaluating inventory management systems.
Essential functionalities
- Real-time tracking: Monitoring stock levels in real-time is crucial. This allows businesses to respond quickly to fluctuating inventory needs.
- Automated reordering: Automated systems can streamline inventory replenishment, reducing the risk of stockouts.
- Reporting tools: Advanced reporting capabilities help in analyzing sales trends, inventory turnover, and identifying potential issues.
- Supplier collaboration: Maintaining a clear line of communication with suppliers can facilitate smoother operations and better responsiveness in managing supply levels.
Advanced capabilities
- Demand forecasting: Utilizing predictive analytics helps in anticipating customer needs and optimizing stock levels.
- Integration with ERP systems: A cohesive relationship with Enterprise Resource Planning systems enhances data accuracy and operational coordination.
- Cloud-based solutions: These allow for access to inventory data from anywhere, supporting remote decision-making and operational agility.
- Customizable dashboards: Tailoring dashboards based on specific business needs improves user experience and quickens data retrieval.
Effective inventory management is not just about storing products; it is about making informed decisions that propel the organization forward.
Comparison Metrics
When assessing inventory management solutions, several key metrics should be taken into account to ensure the selected system aligns with organizational goals.
Cost analysis
- Initial investment: Understand the upfront costs associated with software deployment.
- Operating expenses: Evaluate ongoing costs, including licensing, support, and training.
- Return on investment: Analyze the expected benefits, such as reduced waste and improved order fulfillment.
Performance benchmarks
- Inventory turnover ratio: A higher ratio indicates efficient inventory management.
- Stockout rates: Monitor how frequently products are out of stock to identify potential weaknesses in the supply chain.
- Carrying costs: Understand the total cost of holding inventory, including storage, insurance, and deterioration.
Foreword to Inventory Management in Manufacturing
Inventory management is a critical aspect of the manufacturing sector. It not only governs the flow of materials and products but also significantly influences operational efficiency, cost management, and overall business success. A well-organized inventory management system allows manufacturers to streamline processes, minimize waste, and meet customer demands promptly. As such, understanding the principles of effective inventory management is essential for decision-makers and entrepreneurs.
Definition of Inventory Management
Inventory management refers to the systematic control of ordering, storing, and using a company's inventory. This encompasses raw materials, work-in-progress items, and finished goods. Effective inventory management ensures that the right amount of inventory is available at the right time, preventing both stockouts and overstock situations. Accurate tracking and reporting are key components, and involve monitoring stock levels, orders, and sales data to maintain optimal inventory levels.
Importance of Inventory Management
Effective inventory management brings several benefits:
- Operational Efficiency: Efficient inventory practices align stock levels with production schedules, helping to streamline operations.
- Cost Reduction: By reducing carrying costs and minimizing waste, companies can improve their bottom line. Maintaining the right levels of inventory also helps in mitigating unnecessary financial strain.
- Enhanced Customer Satisfaction: Having the necessary stock on hand to meet customer demands directly impacts customer satisfaction. Timely fulfillment of orders establishes trust and loyalty among customers.
- Data-Driven Decision Making: Strong inventory control systems generate valuable data, which can inform procurement strategies and sales forecasts.
"Inventory management is essential to ensure that the components needed for production are always available, without excessive surplus."
In summary, the significance of inventory management in manufacturing cannot be overstated. It serves as the backbone of operations and contributes to the overall success of businesses in the sector. Proper knowledge and application of inventory management principles can lead to sustained growth and enhanced profitability.
Understanding Different Types of Inventory
Understanding different types of inventory is crucial for effective inventory management in manufacturing. It provides clarity regarding how to classify goods, enhancing accuracy in tracking and controlling stock levels. Each inventory type plays a distinct role in the supply chain, impacting production efficiency and costs. By categorizing inventory into raw materials, work-in-progress, and finished goods, manufacturers can better assess their operations and make informed decisions about resource allocation and scheduling.
Raw Materials Inventory
Raw materials inventory refers to the basic materials that are required for the manufacturing process. These are items that have not yet undergone any transformation or processing. Managing raw materials effectively is vital to ensuring smooth production flow and minimizing delays.
Manufacturers must keep careful track of the quantities of raw materials on hand. They need to consider lead times and reorder points to avoid production interruptions. For instance, if a factory produces furniture, the raw materials might include wood, screws, and varnish. Calculating how much raw material is needed for upcoming production runs can help in maintaining adequate stock levels.
- Benefits of managing raw materials inventory include:
- Reduced carrying costs through optimal stock levels.
- Less waste from expired or obsolete materials.
Work-in-Progress Inventory
Work-in-progress (WIP) inventory includes items that are in the process of being manufactured but are not yet complete. This category encompasses goods that require several steps to reach completion. Understanding WIP helps manufacturers identify bottlenecks and enhance production processes.
By tracking WIP levels, companies can analyze how long materials spend in production. This can inform adjustments in workflow and resource allocation. For instance, in a jewelry manufacturing plant, items might include partially assembled rings or necklaces. Regularly monitoring the status of these items aids in timely completion and meets customer demands.
- Key considerations for WIP inventory management:
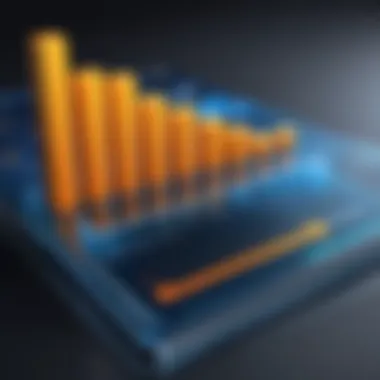
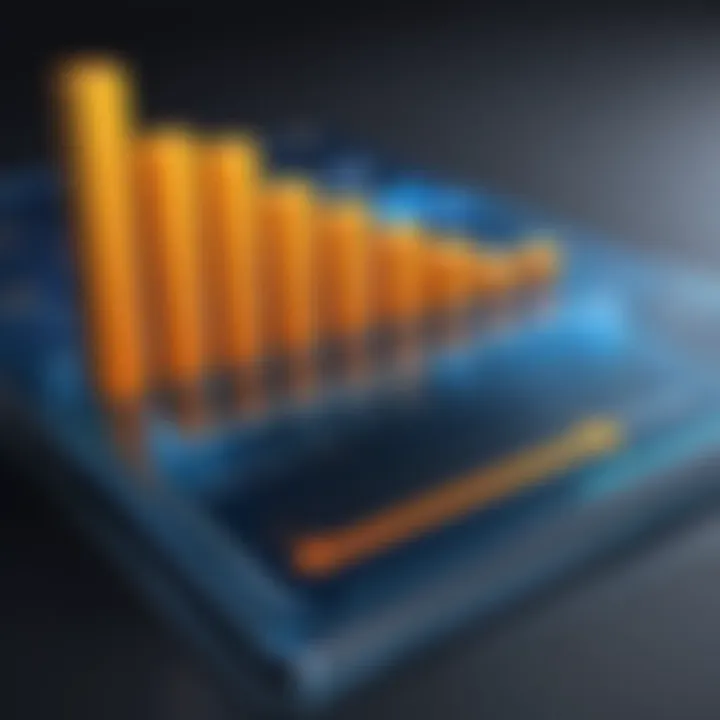
- Ensure balanced production schedules.
- Analyze cycle times and process efficiencies.
Finished Goods Inventory
Finished goods inventory consists of completed products that are ready for sale. This inventory type represents the final stage of the manufacturing process, where quality control and customer demand play important roles. Managing finished goods efficiently can optimize sales potential and support cash flow management.
Accurately assessing the level of finished goods inventory helps prevent stockouts or excess stock, which can lead to lost sales or increased holding costs. For example, a company that manufactures electronic devices must predict demand accurately to ensure they have enough products available during peak sales periods.
- Considerations when managing finished goods include:
- Regular audits to evaluate stock levels.
- Seasonal demand planning to adjust production and inventory.
Understanding the different types of inventory allows manufacturers to develop targeted strategies for inventory control, leading to greater overall efficiency and cost savings.
Inventory Management Methods
Effective inventory management is pivotal in maintaining operational agility and competitiveness in manufacturing. The methods applied to manage inventory directly relate to how resources are utilized, costs are controlled, and overall production goals are achieved. These methods not only influence inventory levels but also affect cash flow and customer satisfaction. Organizations benefit from understanding various techniques, which enable them to make data-driven decisions to optimize their inventory processes.
Just-In-Time (JIT) Inventory
Just-In-Time inventory is a strategy that aims to reduce stock levels while ensuring that the necessary materials are available for production when needed. The core idea is to synchronize demand with production and inventory levels. This method holds significant importance in minimizing waste and reducing holding costs.
With JIT, manufacturers aim to receive goods only as they are needed in the production process. This approach can lead to several benefits:
- Lower Inventory Costs: Holding less stock reduces storage and carrying costs.
- Reduced Waste: Fewer materials in stock mean less risk of obsolescence or spoilage.
- Increased Efficiency: Streamlined operations can improve production flows and accelerate turnaround times.
Implementing JIT requires precision in demand forecasting and robust supplier management to ensure that materials arrive at precise times. Regular communication with suppliers is vital for maintaining this delicate balance.
ABC Analysis
ABC Analysis is an inventory categorization technique based on the concept of managing items based on their importance. In this method, items are divided into three categories:
- A Items: These are high-value items that represent a small percentage of inventory but a significant portion of overall spend.
- B Items: Moderate-value items that are essential but less critical than 'A' items.
- C Items: Low-value items that form the bulk of the inventory but have less impact on total costs.
This analysis helps organizations focus their attention on the items that matter most. By understanding which items drive significant value, decision-makers can improve management and control in purchasing and stock rotation. Notably, aligning inventory practices with product importance enhances efficiency in managing resources.
First-In-First-Out (FIFO) vs Last-In-First-Out (LIFO)
FIFO and LIFO are inventory valuation methods that significantly impact financial statements and tax implications in manufacturing. The choice between the two involves understanding their operational suitability.
- FIFO (First-In-First-Out): This method entails selling or using the oldest inventory first. FIFO is widely used and preferred in industries where products have a limited shelf life, such as food and pharmaceuticals. It aligns nicely with the flow of goods in production and ensures that older stock moves before newer stock, minimizing waste.
- LIFO (Last-In-First-Out): In contrast, the LIFO method assumes that the most recently acquired items are sold first. This can lead to tax advantages in periods of rising prices since the newer, higher-priced stock is recorded as sold, reducing taxable income. However, it may not accurately reflect actual inventory flow for many manufacturers.
Choosing the appropriate method involves weighing the benefits against potential drawbacks, considering aspects like tax implications, financial reporting, and actual operational processes.
Understanding each of these inventory management methods allows manufacturing firms to tailor their strategy to suit their unique needs and operational realities.
Challenges in Inventory Management
Inventory management is a critical component in the manufacturing sector. However, it is not without its challenges. Understanding and addressing these challenges is vital for ensuring operational efficiency and maintaining cost-effectiveness. Two significant issues stand out in this area: demand forecasting and supplier reliability. Each of these elements poses unique considerations that can impact inventory levels, production schedules, and ultimately, profitability.
Demand Forecasting Issues
Demand forecasting is the process of estimating future customer demand for a product. It is crucial for effective inventory management. When forecasts are inaccurate, they can lead to either surplus stock or shortages. An overestimation can result in excess inventory, leading to increased holding costs. Conversely, underestimating demand may cause stockouts, leaving customers dissatisfied.
To improve forecasting accuracy, various techniques can be employed. These include historical sales analysis, market research, and even advanced statistical methods. Leveraging technology, such as predictive analytics software, can significantly enhance the accuracy of forecasts. However, despite the tools available, demand forecasting remains inherently uncertain due to factors like changing market dynamics, seasonal variations, and economic shifts.
Supplier Reliability
Another major challenge in inventory management is supplier reliability. Dependable suppliers are essential for maintaining a smooth production process. If suppliers fail to deliver materials on time or do not meet quality standards, it can lead to production delays. These delays may escalate costs and disrupt customer satisfaction.
Building strong relationships with suppliers can mitigate these risks. Communication is key. Regularly discussing expectations and performance can create a more collaborative environment. Additionally, diversifying Supplier Base can prevent reliance on a single source, buffering against potential disruptions. Having contingency plans also helps. This can include identifying alternative suppliers or maintaining buffer stock to manage unexpected delays.
Addressing challenges in inventory management requires diligence and strategic thinking.
"An effective strategy is not just about minimizing challenges but also leveraging them for greater operational insights."
By honing in on demand forecasting and supplier reliability, businesses can enhance their inventory management processes, ultimately leading to improved efficiency and reduced costs.
Inventory Control Techniques
Inventory control techniques are essential for effective management in manufacturing. These methods aim to maintain optimal inventory levels while minimizing costs. Proper implementation of these techniques can lead to improved efficiency and reduced waste. For decision-makers, understanding these control techniques is crucial for achieving supply chain excellence.
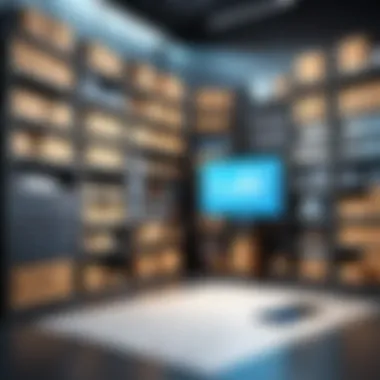
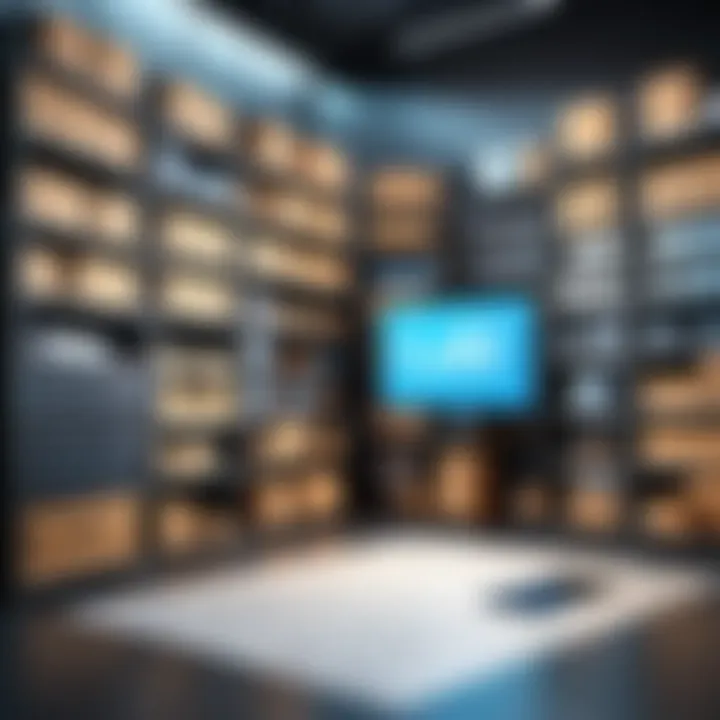
Stock Audits
Stock audits are systematic evaluations of inventory. They help organizations verify the accuracy of inventory records. Regular audits ensure that the physical stock aligns with the recorded stock in the inventory management system. This alignment is vital for identifying discrepancies that could arise from theft, loss, or clerical errors.
Conducting stock audits can also help in assessing the condition of products. Items that are damaged or expired can be removed from inventory, thus improving overall inventory quality. Furthermore, stock audits can inform purchasing decisions. By understanding inventory turnover, businesses can adjust their ordering processes.
Some best practices for conducting stock audits include:
- Scheduling audits during slower business periods
- Using technology to streamline the process
- Ensuring that staff involved are well-trained
"A well-organized stock audit can uncover potentially costly errors."
Cycle Counting
Cycle counting is an alternate method to complete inventory counts. It involves counting a subset of inventory in a specific location on a specific day. Cycle counts are performed regularly throughout the year, which can be more efficient than annual audits. This method allows businesses to continuously monitor inventory levels and maintain accuracy.
Cycle counting provides a few distinct advantages:
- Timely Identification of Issues: Problems with inventory can be discovered and addressed promptly, minimizing potential impact.
- Reduced Disruption: Unlike full-scale audits, cycle counting can be integrated into normal operations without causing significant disruption.
- Improved Accuracy Over Time: Frequent counting leads to enhanced accuracy in inventory records, fostering trust in data among stakeholders.
To implement cycle counting effectively, organizations should focus on:
- Developing a systematic approach to select items for counting.
- Training staff on procedures to ensure consistency.
- Regularly reviewing and adjusting the process for continuous improvement.
Inventory control techniques, such as stock audits and cycle counting, are foundational practices. They help maintain accurate records and ensure the efficiency of manufacturing operations.
Utilizing Technology in Inventory Management
Technology plays a crucial role in modern inventory management. As manufacturing operations grow in complexity and scale, the integration of advanced technological solutions is essential. It provides a framework that improves precision, efficiency, and responsiveness. Businesses can leverage technological tools to streamline processes, reduce human error, and ultimately enhance profitability.
One of the primary benefits of utilizing technology is the real-time visibility it offers. With digital tools, inventory levels can be monitored continuously. This enables manufacturers to respond quickly to supply chain fluctuations and demand changes. Keeping inventory information updated minimizes the risk of overstocking or stockouts, both of which can lead to substantial losses.
Moreover, technology aids in data management, providing insights that guide decision-making. By analyzing historical data, manufacturers can predict trends and optimize their inventory strategies. This supports more strategic purchasing and production planning, helping to align resources with market demand.
"Incorporating technology into inventory management is not merely a choice but a necessity in today's competitive environment."
Inventory Management Software
Inventory management software automates and manages stock levels, helps track product movements, and facilitates ordering processes. Programs like Oracle NetSuite and Fishbowl are designed to cater to diverse business size and industry needs.
Key benefits include:
- Accuracy: Digital records reduce human errors associated with manual tracking.
- Efficiency: Automation of repetitive tasks allows staff to focus on critical areas, enhancing productivity.
- Informed Decision-Making: The software provides detailed reports and analytics, informing better procurement and sales strategies.
Choosing the right inventory management software is vital. Considerations include ease of use, scalability, customer support, and integration capabilities with other systems. Organizations must ensure that the solution aligns with their specific operational requirements to fully capitalize on advantages.
Automation Tools
Automation tools further enhance the inventory management process. The primary goal of automation is to eliminate repetitive tasks and minimize the time spent on manual processes.
Various types of automation tools are available, including:
- Barcode Scanners: These devices expedite tracking and managing inventory by simplifying data entry.
- Automated Reordering Systems: These systems automatically generate purchase orders when stock levels fall below a pre-set threshold.
- Robotic Process Automation (RPA): RPA can handle inventory management tasks across multiple platforms, improving speed and accuracy.
While implementing automation tools, organizations should keep in mind the initial investment and training requirements. These factors can significantly influence the success of integration in existing processes. Successful adoption leads to enhanced performance, allowing businesses to thrive in a competitive environment.
Metrics for Inventory Performance
Metrics for inventory performance are essential tools that help organizations evaluate their efficiency in managing stock. These metrics enable businesses to gain insights into their inventory management capabilities and identify areas for improvement. By relying on quantitative measures, companies can make informed decisions that lead to better operational outcomes. This section will focus on two critical metrics: the Inventory Turnover Ratio and Days Sales of Inventory (DSI).
Inventory Turnover Ratio
The Inventory Turnover Ratio is a key metric that assesses how efficiently a company converts its inventory into sales. It is calculated by dividing the cost of goods sold (COGS) by the average inventory during a given period.
A higher turnover ratio indicates robust sales and effective inventory management, while a lower ratio may suggest overstocking or weak sales performance.
Understanding this ratio is crucial. Here are several benefits of monitoring the Inventory Turnover Ratio:
- Optimizes Stock Levels: Regular analysis helps to maintain optimal inventory levels, which reduces holding costs.
- Enhances Cash Flow: By improving turnover, companies can free up cash, making it available for other operational needs.
- Drives Strategic Decisions: With clear data on inventory performance, businesses can make more strategic choices regarding purchasing, pricing, and promotions.
Days Sales of Inventory (DSI)
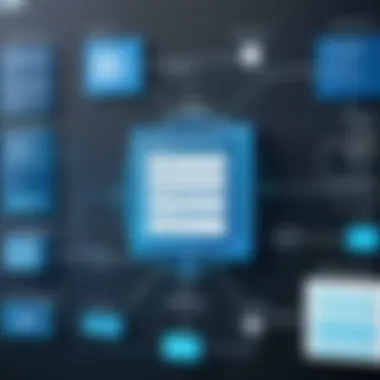
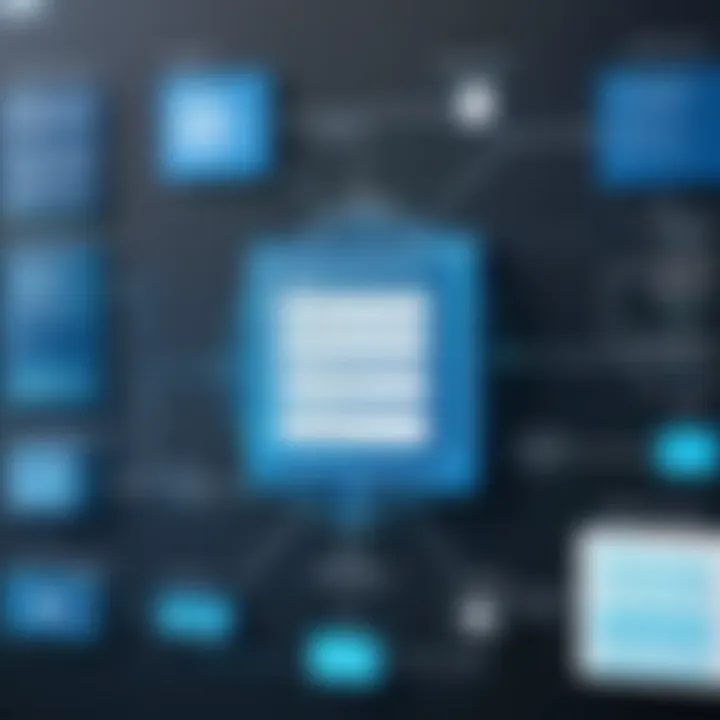
Days Sales of Inventory is another important metric that indicates how long it takes for inventory to be sold. DSI is calculated by dividing the average inventory by daily sales. This gives businesses a timeframe, in days, for selling their stock.
A lower DSI figure means a company is selling inventory quickly, which can be favorable. Conversely, a high DSI may suggest slow-moving inventory and potential cash flow issues.
The significance of DSI includes:
- Identifying Slow-Moving Items: Understanding which products are not selling can help in making decisions on markdowns or discontinuations.
- Adjusting Purchasing Strategies: Companies can better align their buying habits with actual sales trajectories, thus avoiding excess inventory.
- Supporting Cash Flow Management: By keeping DSI at an optimal level, businesses can ensure better cash flow throughout their operations.
Best Practices for Effective Inventory Management
Effective inventory management is pivotal in the manufacturing sector. It directly influences operational efficiency, cost management, and customer satisfaction. Aligning best practices with organizational goals is key to navigating today's complex supply chains. This section highlights two essential practices that can substantially improve inventory management processes: regular reconciling of records and supplier collaboration.
Regular Reconciling of Inventory Records
Reconciliation of inventory records is a vital aspect of maintaining accurate stock levels. Regular checks help to ensure that what is recorded in the system matches the actual physical inventory. This practice mitigates discrepancies that can arise due to various factors such as human error, theft, or data input mistakes. Regular reconciliation provides several benefits:
- Accuracy Improvement: Frequent updates reduce the likelihood of stockouts or overstock situations.
- Enhanced Decision-Making: Accurate data enables better forecasting and planning. Decision-makers can combine real data with market trends to make informed choices about inventory levels.
- Cost Savings: Identifying discrepancies in a timely manner helps prevent excess spending on stock that is not required.
To implement regular reconciling, organizations should establish a routine schedule for audits. This could be monthly, bi-weekly, or even weekly, depending on the volume of transactions. Employing inventory management software can also enhance this process by automating updates and notifications for discrepancies.
Supplier Collaboration
Collaboration with suppliers is another keystone of effective inventory management. Strong partnerships with suppliers lead to timely deliveries and minimize disruptions. When manufacturers and suppliers communicate regularly, they can address issues proactively, such as predicting inventory shortages or unexpected demand spikes. Here are a few considerations for successful supplier collaboration:
- Open Communication: Maintain clear lines of communication with suppliers. This helps build trust and encourages them to provide crucial information regarding lead times and potential delays.
- Joint Forecasting: Engaging suppliers in the forecasting process can create a more accurate picture of market demand, enabling both parties to prepare adequately.
- Flexible Agreements: Establish flexible contracts that allow for adjustments based on shifting circumstances. This provides both manufacturers and suppliers with the agility to adapt to changes in demand.
Frequent audits and open supplier communication are crucial for maintaining inventory accuracy and responsiveness.
The Future of Inventory Management
Understanding the future of inventory management is crucial for businesses aiming to maintain a competitive edge. Rapid technological advancements and shifting market dynamics are transforming how manufacturers handle their inventory. With the increasing complexity of supply chains and consumer expectations, organizations must adapt and innovate.
Among the main elements to consider for the future are automation and artificial intelligence. These technologies promise efficiency and accuracy, reducing human error in inventory tracking and forecasting. As these tools become more integrated, they will allow businesses to respond quickly to market changes and optimize stock levels. Additionally, sustainability is gaining prominence. Consumers and regulators alike demand eco-friendly practices, pressuring companies to rethink their resource management.
The future of inventory management will rely not only on advanced technology but also on strategic thinking and adaptability. Companies that embrace these changes can expect reduced costs, improved customer satisfaction, and sustainable growth.
Trends in Automation and AI
Automation and AI stand at the forefront of transforming inventory management. With tools like robotics, businesses are able to streamline warehouse operations, enhancing speed and reducing overhead. Automated systems can facilitate real-time inventory tracking, significantly improving order accuracy and fulfillment speed.
AI adds another layer of sophistication by enabling predictive analytics. Through machine learning algorithms, companies can analyze historical data and forecast demand with remarkable precision. This allows for smarter decision-making when it comes to purchasing and stock management.
- Key benefits of automation and AI include:
- Increased efficiency in inventory handling
- Enhanced forecasting capabilities
- Reduction of human error in stock counts
- Cost savings through optimized labor utilization
Furthermore, automation can assist in minimizing holding costs. Automated systems often incorporate alerts and notifications when stock levels fall below a threshold, ensuring timely reordering and preventing stockouts. Consequently, manufacturers can maintain a smooth production flow, meeting consumer demands without interruption.
Sustainability Considerations
Sustainability is increasingly becoming a vital consideration in inventory management practices. As regulatory frameworks tighten globally, manufacturers face growing pressure to minimize their environmental footprints. Effective inventory management plays a significant role in enhancing sustainability efforts.
Adopting sustainable practices can involve:
- Optimizing stock levels to reduce excess inventory, which often leads to waste.
- Implementing eco-friendly packaging solutions to decrease plastic waste.
- Choosing suppliers that prioritize sustainable practices throughout their supply chains.
Moreover, integrating sustainability into inventory practices can have financial benefits. Sustainable inventory management helps reduce waste and can lead to cost savings over time. As consumers increasingly favor brands that demonstrate a commitment to sustainability, businesses can enhance their market positioning by promoting such initiatives.
In summary, the future of inventory management is shaped by advances in automation and AI, alongside a crucial need for sustainability. Companies that invest in these areas not only prepare themselves for upcoming challenges but also position themselves as leaders in a rapidly evolving marketplace.
Ending
In the manufacturing sector, effective inventory management is not just a process but a pivotal part of operational success. Managing inventory well ensures that production runs smoothly, costs are kept in check, and customer demand is met without delay. This article summarizes key strategies that promote efficient inventory management practices. It emphasizes how these practices lead to overall business improvement and sustainability.
Summary of Key Strategies
The strategies outlined throughout the article provide a roadmap for businesses aiming to optimize their inventory management processes:
- Adopting Automation Technologies: Embracing technology to streamline inventory processes can significantly reduce human error and increase efficiency.
- Implementing JIT Inventory: Just-In-Time methods minimize holding costs and waste, aligning production schedules more closely with actual demand.
- Conducting Regular Stock Audits: Frequent inventory counts catch discrepancies early and enhance accuracy in stock records.
- Supplier Collaboration: Building strong relationships with suppliers can lead to better reliability and flexibility in inventory management.
- Tracking Inventory Performance Metrics: Utilizing metrics like Inventory Turnover Ratio and Days Sales of Inventory provides insight into inventory effectiveness and informs decision-making.
Call to Action for Effective Management
Businesses must actively engage in improving their inventory systems to stay competitive. The steps that can be taken include:
- Assess Current Practices: Review existing inventory management processes to identify weaknesses and potential improvements.
- Invest in Technology: Leverage advanced inventory management software and automation tools designed to enhance tracking and reporting capabilities.
- Train Staff: Ensure that employees are well-trained about new systems and processes to maximize efficiency and reduce resistance to change.
- Monitor Trends: Stay abreast of new trends in inventory management, such as the use of AI and sustainable practices, to remain ahead in the market.
By embracing these strategies, companies can create a more resilient inventory management system that drives efficiency and cost reduction, ultimately leading to enhanced profitability and customer satisfaction.