Enhancing Fleet Efficiency with Predictive Maintenance
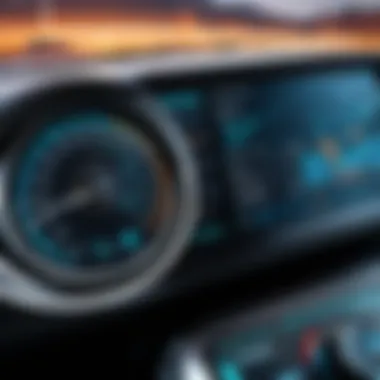
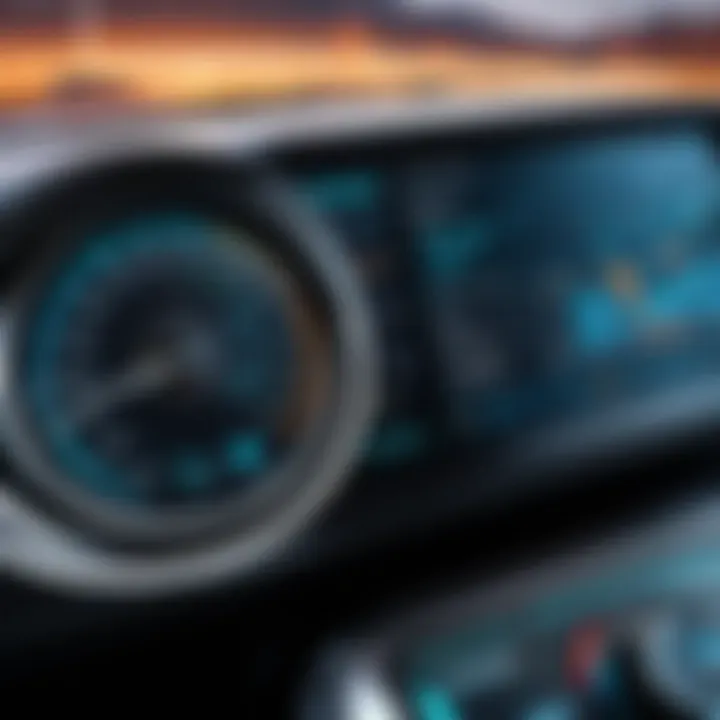
Intro
In today's fast-paced transportation landscape, the demand for efficient fleet management is higher than ever. Businesses are increasingly recognizing that maximizing the lifespan of their vehicles not only saves money but also enhances service reliability. This has led to a growing interest in predictive maintenance, a strategic approach that leverages advanced technologies and data-driven insights.
Predictive maintenance involves analyzing equipment conditions through various sensors and monitoring systems to anticipate failures before they occur. With this approach, companies can shift from a reactive maintenance strategy, where issues are addressed only after they arise, to a proactive one. The intersection of predictive maintenance and fleet management paves the way for significant operational efficiencies, allowing organizations to improve their bottom line while ensuring vehicles are always ready to hit the road.
This article will delve into the crucial elements of integrating predictive maintenance into fleet management. We will explore how data analytics, machine learning, and IoT technologies can transform operations, along with highlighting the potential benefits and challenges. By the end of this piece, decision-makers in transportation will have a thorough understanding of crafting a strategy that optimizes fleet operationsâan essential component in todayâs competitive market.
Key Software Features
When it comes to integrating predictive maintenance into fleet management, choosing the right software solutions is paramount. Effective tools enhance operational insights and provide real-time data that can be utilized to make informed decisions. Hereâs a closer look at the essential and advanced software features that can drive successful integration.
Essential functionalities
- Real-Time Monitoring: The ability to monitor vehicle conditions in real-time helps in recognizing patterns that may indicate potential failures. This involves tracking metrics such as engine temperature and brake performance.
- Data Analytics: Sophisticated analytics tools sift through large volumes of data collected from various sensors to identify important trends. This kind of analysis enables fleet managers to prioritize vehicle maintenance schedules effectively.
- Alert and Notification Systems: Software that provides alerts for needed maintenance based on predictive analytics can avoid unexpected breakdowns. Immediate notifications can help get vehicles back in service quickly.
Advanced capabilities
- Machine Learning: Incorporating machine learning algorithms can improve the predictive accuracy of maintenance needs. These systems learn from historical data to predict future maintenance proactively.
- Integration with Other Systems: Advanced software should seamlessly integrate with existing fleet management systems to provide a comprehensive view of operations. This ensures efficient collaboration across various departments.
- Mobile Accessibility: With mobile access to fleet data, managers can make quick decisions while on the go, ensuring that any issues are addressed swiftly even when they are away from their desks.
"Incorporating predictive maintenance software can lead to reduced downtime and lower repair costs while enhancing overall fleet operation efficiency."
As more organizations recognize the importance of predictive maintenance, the software landscape continues to evolve. It's imperative for fleet managers to embrace these advancements to maintain a competitive edge and optimize their resources.
Prologue to Predictive Maintenance and Fleet Management
In todayâs fast-paced world, efficiency is a buzzword that echoes through every industry, especially in fleet management. This sector, pivotal for transportation and logistics, grapples with constant pressure to optimize operations, minimize costs and maintain high service levels. But how does one achieve this delicate balance? Enter predictive maintenance, a game-changer that stitches together data, technology, and analytical insights tailored for fleet management.
Predictive maintenance leverages data analysis to foresee potential equipment failures before they occur, allowing fleet managers to schedule maintenance at just the right moment. This approach not only lengthens asset life but also reduces unexpected downtimeâa critical concern in any fleet operation. By integrating predictive maintenance into fleet management, companies harness the power of data, emerging technologies, and advanced methodologies to enhance operational efficiency.
Defining Predictive Maintenance
Predictive maintenance is an intellectually sound concept that seeks to predict when maintenance should be performed. This methodology relies heavily on statistical models and data collected from various sources, primarily sensors and operational history. Instead of adhering to a fixed schedule or reacting post-failure (which can often be too late), predictive maintenance anticipates mechanical issues.
To put it simply, think of it as going to the doctor for a health check rather than waiting until you're struck down by an ailment. So why is this aspect crucial for fleet management? Well, the consequences of unexpected equipment failure can lead to costly downtimes, delayed deliveries, and, quite frankly, unpleasent customer experiences. By employing predictive maintenance, businesses can take proactive steps to address potential issuesâkeeping their wheels turning and customers satisfied.
Overview of Fleet Management
The realm of fleet management encompasses a broad range of activities including logistics, dispatching, and, of course, maintenance. Managing a fleet effectively involves the coordination of vehicles, drivers, and routes to achieve optimal productivity. This goes beyond just keeping track of vehicles; it encompasses monitoring performance metrics, understanding fuel consumption patterns, and ensuring compliance with regulatory standards.
For fleet managers, every aspect counts. A small hiccup can cascade into significant financial implications. Therefore, itâs not just about managing vehicles; itâs about managing a comprehensive ecosystem. The key components of fleet management include:
- Asset tracking: Using GPS and telematics to monitor vehicle location and status.
- Driver management: Ensuring compliance with safety regulations and managing driver performance.
- Fuel management: Monitoring usage effectively to control costs.
- Maintenance scheduling: Planning repairs and inspections to reduce downtime.
The Relationship Between Predictive Maintenance and Fleet Management
When you look closely, the relationship between predictive maintenance and fleet management is not just a simple overlap of functions; it's a strategic alignment. Predictive maintenance acts as a radical improvement for fleet management. It transforms traditional maintenance strategies into more intelligent, data-driven processes.
Through continual analysis of vehicle performance data, fleet managers can pinpoint patterns that indicate the wear and tear of parts, leading to timely interventions. This not only reduces costs associated with emergency repairs but also enhances overall fleet reliability. When maintenance is performed preventively, fleets are less likely to face the unexpected, thereby fostering a smoother operational rhythm.
To summarize, integrating predictive maintenance into fleet management creates a symbiotic relationship: enhancing decision-making, improving efficiency, and saving costs. As fleet challenges evolve, embracing predictive strategies is no longer optional but imperative for those aiming to stay ahead of the curve.
The Role of Data in Predictive Maintenance
In the realm of predictive maintenance, data acts like the lifeblood of the system. The increasing sophistication of fleet management relies on the effective use of data to predict equipment failures before they occur. This proactive approach not only saves money but also enhances vehicle reliability and extends asset life. Therefore, understanding the role of data is paramount for any fleet operator hoping to harness the full potential of predictive maintenance.
Types of Data Used
Sensor Data
One of the cornerstones of predictive maintenance is sensor data. This information is directly collected from the vehiclesâ sensors, measuring various parameters such as engine temperature, oil pressure, and tire pressure. The key characteristic of sensor data is its real-time relevance, providing immediate insights into vehicle performance.
The benefit of using sensor data lies in its ability to identify potential issues as they occur. For instance, if an engine temperature exceeds the normal range, it can trigger alerts that set maintenance actions in motion before a complete failure happens. This feature makes sensor data a popular choice among fleet managers aiming for a preventive stance in maintenance strategies. However, the drawback might involve the initial investment in sophisticated sensors and the technology to process this data.
Historical Maintenance Records
Next up, we have historical maintenance records. This traditional data source offers a retrospective view into a vehicle's performance, capturing past repairs, service intervals, and component replacements. The key characteristic of these records is their ability to reveal patterns or trends in failures over time.
Historical maintenance data is beneficial because it can guide decision-making on preventive actions. For example, if a certain vehicle model consistently shows a pattern of requiring brake replacements after a specific mileage, this information can inform future maintenance schedules. The unique feature here is its reliance on anecdotal evidence coupled with compiled statistics, yet, it may have a disadvantage due to the changing conditions in vehicles or operational environments which could alter previous trends if not re-evaluated regularly.
Operational Metrics
Finally, operational metrics reflect the day-to-day performance of fleet operations. These metrics involve data like fuel efficiency, average speed, route tracking, and driver behavior. The key characteristic is the broad perspective of vehicle usage, which can influence maintenance needs.
Operational metrics are a beneficial choice because they help in understanding how different factors affect the longevity of the fleet. For instance, aggressive driving can lead to more frequent tire wear, thus tweaking driving behavior could prolong tire life. The unique feature of operational metrics lies in their capacity for real-time analysis. However, they require constant monitoring and can sometimes lead to information overload if not managed properly.
Data Collection Techniques
To leverage the aforementioned types of data effectively, utilizing robust data collection techniques is vital. From IoT devices capturing sensor readings to manual recording from maintenance logs, diverse methods exist.
By employing these data collection strategies, fleet management can innovate their predictive maintenance approaches, leading to better resource allocation and ultimately, enhanced fleet efficiency.
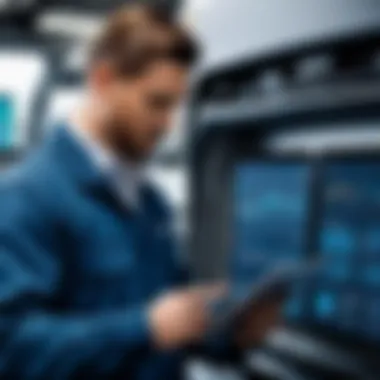
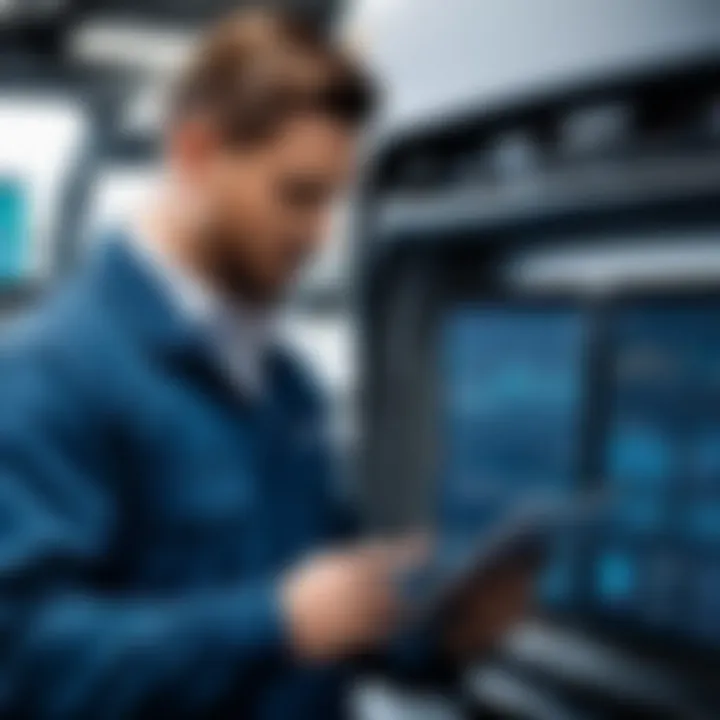
"Data is the new oil; itâs valuable, but if unrefined, it cannot really be used."
In summary, the focus on data use in predictive maintenance signifies an evolution in fleet management practices. Fleet operators who harness the potential of sensor data, historical records, and operational metrics will likely find themselves at a distinct advantage in a competitive landscape.
Technologies Driving Predictive Maintenance
In the realm of predictive maintenance, the role of technology cannot be overstated. Numerous innovations are advancing the way businesses manage their fleets. From machine learning algorithms to the Internet of Things (IoT), these technologies are instrumental in predicting malfunctions before they occur, thereby streamlining operations and creating efficiencies that were previously unimaginable. Letâs delve deeper into the specifics of these technologies.
Machine Learning and AI
Machine learning and artificial intelligence (AI) are at the forefront of predictive maintenance. They enable systems to analyze vast amounts of data, recognize patterns, and make informed predictions about potential equipment failures.
For instance, a fleet management company can utilize algorithms that continually learn from new dataâsuch as wear and tear patternsâfrom its vehicles. This means that the more data the systems collect, the more precise their insights become.
Some key benefits include:
- Early Detection: Identifying issues before they escalate can save time and money.
- Data-Driven Decisions: Instead of relying on gut feelings, fleet managers can make choices based on hard data.
- Customized Maintenance Plans: Through data analysis, companies can create tailored maintenance schedules for each vehicle, enhancing overall fleet health.
The integration of these technologies allows for a proactive approach rather than a reactive one, fundamentally changing fleet operations.
IoT and Sensors
The Internet of Things (IoT) brings an entirely new layer of capability to predictive maintenance. By incorporating sensors in vehicles and equipment, real-time monitoring becomes a reality.
Consider this: sensors can track various parameters like engine temperature, oil pressure, and tire pressure. When these metrics exceed normal thresholds, alerts can be triggered. This real-time data collection offers a continuous feed that can significantly improve decision-making.
Benefits of IoT implementation include:
- Real-Time Insights: Information is processed continuously, allowing for immediate action when needed.
- Reduced Downtime: By addressing issues as they arise, fleet managers can prevent delays and maintain productivity.
- Cost Efficiency: Improved monitoring reduces unnecessary maintenance costs and extends vehicle lifespans.
Ultimately, the fusion of IoT and predictive maintenance creates a dynamic environment that emphasizes immediacy.
Cloud Computing and Data Storage
An integral part of leveraging predictive maintenance is cloud computing. It provides the infrastructure that allows vast amounts of data to be stored and processed efficiently.
Cloud platforms enable fleet managers to access analytical tools and maintain a centralized database where real-time data from all vehicles can be collected. This centralization simplifies data sharing across teams and enhances collaboration.
Some considerations when thinking about cloud computing for predictive maintenance are:
- Scalability: As fleet operations expand, cloud solutions can effortlessly adjust to increased data loads.
- Remote Access: Fleet management teams can access information from anywhere, facilitating quicker decision-making.
- Data Security: Leading cloud providers implement robust security protocols, ensuring that sensitive information remains protected.
The interplay of cloud computing with data management underscores the systematic approach needed for effective predictive maintenance.
Implementing Predictive Maintenance in Fleet Operations
Implementing predictive maintenance in fleet operations is not just a buzzword; itâs a game changer. The integration of this approach into daily practices can significantly bolster overall efficiency while minimizing costs and downtime. By leveraging data analytics and advanced technologies, businesses can navigate the complexities of fleet management with greater ease.
When companies embrace predictive maintenance, they're not merely reactive. Instead of waiting for something to break down, these fleets can proactively anticipate issues, leading to a smoother run. The operational benefits can be numerous:
- Cost savings: Identifying potential failures before they result in costly repairs.
- Enhanced safety: Reducing incidents caused by equipment failure.
- Improved compliance: Staying ahead of regulatory requirements through consistent monitoring.
However, successful implementation hinges on several factors unique to each organization's needs and infrastructure.
Assessing Operational Needs
Before diving into tools or technologies, a thorough assessment of operational needs is crucial. This involves analyzing current fleet performance, understanding service requirements, and identifying critical components that warrant monitoring.
Considerations might include:
- Type and Age of Equipment: Older vehicles may need different strategies compared to newer models.
- Usage Patterns: Understanding how often vehicles are used can inform decisions on maintenance frequencies.
- Environmental Factors: Fleets operating in harsh conditions may experience wear and tear differently.
- Operational Goals: Align the predictive maintenance approach with broader business objectives, whether itâs reducing costs, enhancing service delivery, or improving fleet longevity.
By understanding these elements, organizations can tailor their predictive maintenance strategies to directly address specific challenges and leverage opportunities for efficiency.
Selecting the Right Tools and Software Solutions
The market is flooded with tools and software designed for predictive maintenance, but not every solution will fit every fleet. Itâs imperative to explore options that align seamlessly with both operational needs and technological landscape.
Key factors to evaluate include:
- Integration Capabilities: Ensure that the software can interface smoothly with existing systems, such as GPS tracking and inventory management software.
- User-Friendliness: A tool should be accessible for all team members, not just IT professionals.
- Scalability: As operations grow, the solution should adapt without major overhauls.
- Cost-effectiveness: Look for solutions that offer substantial return on investment, not just the lowest initial price.
Some notable choices in the field could include solutions like Uptake, which provides machine learning insights, or IBM Maximo, renowned for its asset management capabilities. The right choice will not only simplify data analysis but also effectively support predictive maintenance goals.
Training Staff and Stakeholders
Even the best tools are only as effective as the people using them. Hence, investing in training for staff and stakeholders is paramount to realizing the full potential of a predictive maintenance program.
Several aspects should be covered:
- System Navigation: Ensure staff know how to efficiently use the selected tools.
- Data Interpretation: Training on how to analyze and act upon the data provided is just as important as data collection.
- Change Management: Facilitate conversations around how predictive maintenance will affect current workflows, addressing any resistance.
Regular refresher courses and open lines of communication can foster a culture where team members feel confident in utilizing predictive maintenance technologies, ultimately leading to a more efficient fleet operation.
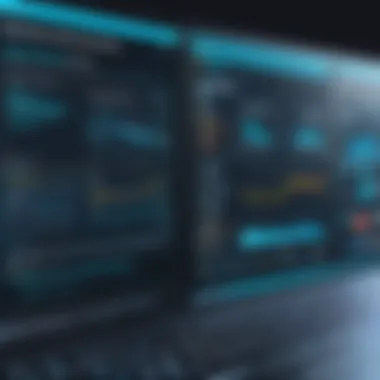

"Predictive maintenance isn't just about the technology; it's about cultivating a mindset that anticipates needs and drives improvement."
Challenges in Predictive Maintenance Implementation
Predictive maintenance has the potential to revolutionize fleet management. However, integrating it into existing systems is not a walk in the park. It presents various challenges that companies must navigate to fully harness the benefits. Understanding these hurdles is crucial for decision-makers, as it shapes the strategies they adopt for implementation.
Data Management Issues
Data is the lifeblood of predictive maintenance. Ensuring it flows seamlessly can be a real tightrope walk. Fleet managers must grapple with the sheer volume of data generated from various sources, such as sensors and operational metrics. Poor data management can lead to incorrect analytics, resulting in faulty predictions. Making sense of this data involves robust data management systems.
Several considerations come into play here:
- Data Quality: Inaccurate or incomplete data can skew results. Regular audits on data quality are non-negotiable.
- Integration: Data silos can hinder the ability to gather insights effectively. Consolidating data from different sources into a unified system is vital for success.
- Real-time Access: Fleet operations demand immediate insights. Without the ability for real-time monitoring, even the best predictive maintenance strategies might fall short.
In short, if the data isnât managed well, the whole predictive maintenance strategy could go south rapidly.
Resistance to Change Among Staff
No one likes change. Itâs like trying to teach an old dog new tricks. Employees, especially those who have been in their roles for a long time, might resist the transition towards predictive maintenance. This can stem from various factors:
- Fear of the Unknown: Staff may worry that adopting new technologies could threaten their jobs.
- Lack of Training: If workers donât feel equipped to use new tools and processes, they might hesitate to embrace them.
- Cultural Barriers: Some teams have a deeply ingrained way of doing things. Shifting this mindset might be more challenging than expected.
To overcome these challenges, itâs essential to foster a culture that promotes continuous learning. Engaging staff in training programs can help mitigate their fears and showcase the advantages of predictive maintenanceâleading them to jump on the bandwagon willingly.
Cost Implications
Implementing predictive maintenance doesnât come for free. It requires a financial outlay that some companies may not be ready or willing to make. Cost implications can be a double-edged sword. Initially, there can be heavy investments in technology and training. These may include but are not limited to:
- Software licenses for predictive analytics platforms
- Hardware installations, like IoT sensors
- Training and upskilling existing staff
However, while the upfront costs might seem daunting, itâs crucial to look at the long-term return on investment. Efficient predictive maintenance can significantly reduce costs over time:
- Decreasing unexpected downtimes leads to less lost revenue.
- Optimizing maintenance schedules can result in lower repair costs and better asset longevity.
Ending
Facing these challenges head-on is essential for any fleet manager looking to implement predictive maintenance effectively. Recognizing data management issues, addressing staff resistance, and considering cost implications will prepare businesses for tackling what lies ahead.
"Understanding and preparing for potential challenges can make all the difference in a successful predictive maintenance implementation."
By tackling these hurdles, companies can unlock the full potential of predictive maintenance, driving efficiency and operational success in fleet management.
Measuring the Impact of Predictive Maintenance
Measuring the impact of predictive maintenance takes center stage in our discussion around fleet management and efficiency. Itâs crucial not just for understanding how maintenance practices influence performance but also for justifying the investment in these technologies. Fleet managers need a clear view of the improvements and savings to gauge if the predictive strategies are worth their salt. With this clarity, decision-makers can allocate resources more effectively and refine their maintenance plans over time.
An effective assessment measures three primary areas that can radically transform fleet operations: maintenance costs, downtime reduction, and asset longevity. Understanding these metrics gives fleet managers insight into their operations' health, aligning maintenance strategies with business goals.
Key Performance Indicators
Maintenance Costs
Maintenance costs provide one of the clearest indicators of efficiency in fleet operations. In practice, a company that embraces predictive maintenance can expect to see a reduction in both scheduled and unscheduled maintenance expenditures. The relationship here is pretty straightforward; by predicting failures before they occur, fleets can avoid those costly breakdowns when operations are most vulnerable.
What sets this aspect apart is the potential for smart budgeting. Predictive maintenance systems analyze data that can indicate when a piece of equipment is at risk of failure, allowing companies to intervene in a timely manner. This predictive insight helps organizations avoid unexpected expenses, making it a popular choice among fleet managers.
Advantages include:
- Significant reduction in repair costs.
- More predictable budgeting processes.
- Better cash flow management due to fewer emergency repairs.
One should also consider some disadvantages, such as the initial implementation costs and the requirement for training staff on these systems to optimize their effect.
Downtime Reduction
Downtime reduction speaks directly to operational efficiency. Minimizing the amount of time vehicles spend out of action directly translates to increased productivity and revenue generation. Predictive maintenance allows fleet operators to anticipate and plan for repairs during non-peak times, thus ensuring that their assets are available and operational when they are most needed.
A key trait of downtime reduction is time efficiency. By strategically scheduling maintenance, fleets can avoid costly emergency repairs that usually occur during critical business hours. This aspect makes it a beneficial practice that resonates well in this article about efficiency improvements.
Advantages include:
- Enhanced service delivery due to increased vehicle availability.
- Improved customer satisfaction from timely deliveries.
- Optimal utilization of resources.
On the flip side, complexities around scheduling can arise. Stratifying maintenance schedules without disrupting operations is delicate but necessary for gaining the downtime advantage.
Asset Longevity
Asset longevity stands as a testament to the efficacy of predictive maintenance. By maintaining equipment properly and catching issues early, businesses can extend the life span of their vehicles. This is an ongoing benefit, resulting in lower long-term capital expenditures and better value over time.
The prominent feature of asset longevity is sustainability. Regular maintenance practices keep vehicles running efficiently, significantly reducing the need for replacements and thus having a less detrimental impact on the environment. This is why sustainability has emerged as a popular consideration for modern fleets today.
Advantages include:
- Reduced frequency of purchasing new assets.
- Better resale values due to maintained conditions.
- Lesser environmental impact, aligning with green initiatives.
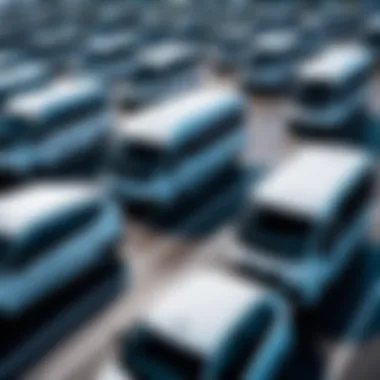
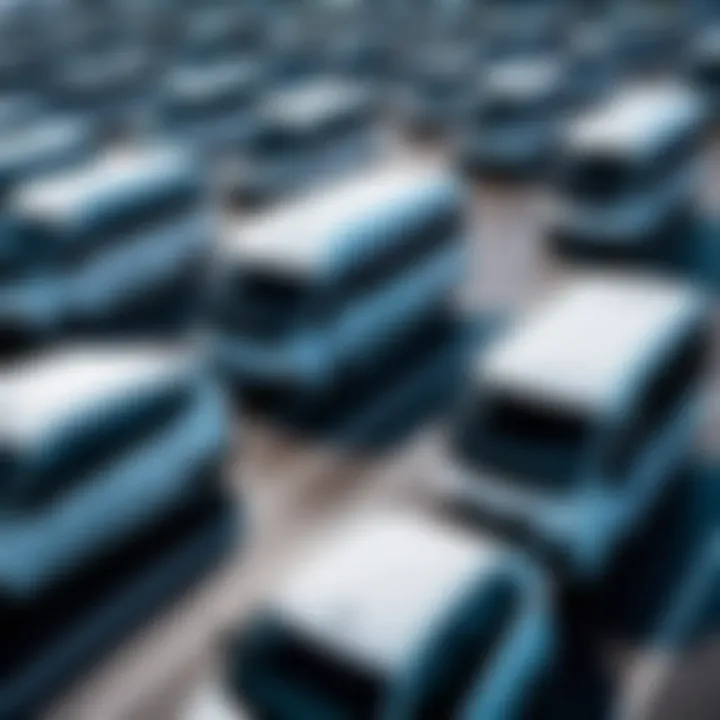
Conversely, again, investment and commitment are necessary to see its benefits. Itâs not just about maintaining but also about monitoring regularly and adjusting maintenance practices when necessary to foster longevity.
Case Studies and Examples
To further appreciate these metrics, looking at real-world applications brings clarity. Companies that have integrated predictive maintenance methodologies showcase significant improvements in their operations. One notable example is Company X, which reported a 30% decrease in maintenance costs over a two-year period after implementing a predictive strategy.
Through case studies like these, the significant benefits of measuring and analyzing predictive maintenance can no longer be overlooked. By examining these examples closely, one can draw parallels and inspire similar shifts in their own fleet operations.
Best Practices for Predictive Maintenance in Fleet Management
Predictive maintenance is a game changer in fleet management, offering a pathway to enhanced operational efficiency and sustainability. The practices that best align themselves with this strategy can yield myriad benefits. Implementing these best practices is essential, not just to avoid unexpected breakdowns but also to align maintenance schedules with real-world conditions. Whatâs more, these measures can help optimize costs, improve equipment lifespan, and significantly boost fleet dependability.
Developing a Maintenance Schedule
Creating a robust maintenance schedule is arguably the first step in the predictive maintenance journey. Itâs crucial to tailor the maintenance timetable according to vehicle use, operational environment, and specific manufacturer guidelines. Here are key considerations:
- Utilize Data Analytics: Leverage historical data from vehiclesâ performance records. By analyzing trends, you can pinpoint the optimal maintenance intervals.
- Flexibility is Key: Situations change; therefore, your schedule should be able to adapt without heavy friction. Regularly revisiting the schedule allows for necessary adjustments that reflect current operating conditions.
- Team Input: Engaging your operational staff in schedule development can surface insights that data alone might overlook. They can provide on-the-ground knowledge that shapes realistic maintenance windows.
Continuous Monitoring and Adjustment
Maintenance does not end once the schedule is set; itâs a dynamic process. Continuous monitoring facilitates timely adjustments based on operational realities. This can involve a few strategies:
- Real-time Data Collection: Implementing IoT sensors on vehicles not only paves the road for real-time data but also enhances decision-making accuracy regarding maintenance needs.
- Feedback Loops: Establishing mechanisms to obtain ongoing feedback from drivers and maintenance crews can inform necessary changes. For instance, if a driver notes unusual sounds or performance, prompt investigation and adjustment can prevent more severe issues.
"Adapt or be left behind." â A motto that resonates within the realm of predictive maintenance.
Engaging with Suppliers and Partners
Building solid partnerships with suppliers and service providers is another essential practice. Collaborating closely offers various advantages:
- Shared Expertise: Suppliers often have insights on best practices related to the parts and equipment they provide. Their ability to guide you can lead to more effective and efficient maintenance.
- Cost Negotiation: When you develop long-term relationships, you can negotiate better prices or exclusive deals, saving your operations fondly-maintained dollars.
- Access to Innovations: Staying connected with partners can keep you up to speed on the latest technologies and methods, which can be beneficial for staying ahead in the fast-evolving world of fleet management.
By integrating these best practices into operational workflows, fleet management teams can navigate towards a more efficient future, ensuring not just the longevity of equipment but also the overall success of the operations.
The Future of Predictive Maintenance in Fleet Management
Predictive maintenance is no longer a flashy buzzword; itâs evolving into a mandatory facet of fleet management. As the technology advances, its integration into routine operations is set to reshape how businesses think about maintenance, efficiency, and overall costs. The future of predictive maintenance in fleet management revolves around adaptability, precision, and sustainability.
Emerging Trends and Technologies
As we step into a future where data reigns supreme, several trends are emerging within predictive maintenance that decision-makers must keep a sharp eye on. The embedding of Artificial Intelligence (AI) and machine learning into maintenance schedules provides unprecedented precision. These technologies analyze patterns and predict failures before they occur, potentially saving companies substantial costs in repairs and downtime.
Furthermore, IoT devices are becoming pivotal. With sensors integrated into every vehicle, real-time data collection allows fleet managers to anticipate mechanical issues before they escalate. Imagine a scenario where a sensor detects an abnormal temperature in the engine. It transmits this information to the fleet manager's dashboard, triggering an alert for inspection. This becomes critical for modern fleets, facilitating not just maintenance but also seamless operations across distances.
Hereâs a snapshot of some notable technologies paving the way:
- Advanced data analytics: Tools that can sift through vast amounts of operational data to highlight trends.
- Blockchain technology: Enhancing data security and integrity in maintenance records, ensuring reliability.
- Predictive modeling platforms: Providing simulations based on historical data to forecast maintenance needs.
"In the realm of fleet management, being proactive is about predicting problems rather than just solving them after they arise."
As the integration of these technologies deepens, fleet operators will find their operations more streamlined and their strategies more data-driven.
Sustainability Considerations
In recent years, sustainability has become a hot-button issue across industries, and fleet management is no exception. Predictive maintenance can play a significant role in fostering sustainable practices. For one, by minimizing unnecessary repairs and ensuring vehicles run efficiently, companies can significantly reduce their emissions. A vehicle that is functioning optimally uses less fuel and thus has a smaller carbon footprint.
Moreover, embracing sustainability often goes hand-in-hand with cost savings. For instance, effective predictive maintenance can extend the lifespan of fleet vehicles, meaning companies wonât be required to replace their fleet as frequently. This reduction in turnover not only conserves resources but also curbs waste generation associated with vehicle disposal processes.
Some strategies to consider:
- Optimizing fuel consumption: Using predictive analytics to fine-tune vehicle routes, thus lowering fuel usage.
- Regular upgrades of technologies: Making sure that vehicles are fitted with energy-efficient components.
- Training employees: Encouraging responsible driving techniques which contribute to sustainability.
Implementing these strategies can help cultivate a culture that prioritizes environmental responsibility while maintaining operational excellence.
As decision-makers reflect on the implications of predictive maintenance, the narrative surrounding its future will undoubtedly be interwoven with sustainability efforts, technological advancements, and a commitment to fostering efficiency across the board.
Epilogue
As we wrap up our exploration of predictive maintenance within the realm of fleet management, it becomes_clear that the integration of such strategies can serve as a substantial game-changer for organizations looking to enhance their operational efficiency. The crux of the matter lies not just in understanding predictive maintenance, but in recognizing its transformative impacts on the daily workings of fleet operations.
Through this journey, we have highlighted several vital elementsâfrom the crucial role data plays, the technologies that facilitate effective predictive maintenance, to the pragmatic approaches needed for implementation. The potential to preemptively address maintenance issues reduces downtime and enhances vehicle reliability, all of which brings with it significant cost savings and operational fluidity.
Recap of Key Points
- Data Utilization: The effective use of dataâranging from sensor inputs to historical recordsâis essential for successful decision-making. The data not only aids in identifying potential breakdowns but also in forecasting maintenance needs before they evolve into more severe issues.
- Embracing Technology: Innovations like machine learning, IoT devices, and cloud computing are not mere buzzwords; they are pivotal in creating a proactive maintenance environment. These tools help businesses to monitor the condition of their fleet in real-time.
- Best Practices Adoption: The importance of developing a well-thought-out maintenance schedule and engaging relevant stakeholders cannot be overstated. Continuous feedback loops should be established for ongoing improvement and adaptation of the predictive strategies in place.
- Overcoming Barriers: We have also touched upon the potential bumps on the road. From data management issues to staff resistance, itâs clear that successful implementation requires not just technology, but change management strategies that involve communication, training, and unwavering commitment from leadership.
Final Thoughts and Recommendations
In the long run, the effectiveness of integrating predictive maintenance boils down to the commitment of fleet management professionals to embrace change and flexibility. Itâs about fostering a culture of continuous improvement where data-driven insights are valued and utilized.
As organizations strive to optimize their fleet operations, considering the following recommendations might prove invaluable:
- Invest in Training: Equip your staff with the knowledge and tools they need to effectively utilize predictive maintenance technologies.
- Regularly Review Your Systems: Evaluate your predictive maintenance framework and adjust based on unforeseen challenges or new advancements in technology.
- Foster Collaboration: Establish open communication lines between suppliers, stakeholders, and internal teams to share insights and best practices.
- Stay Informed: Keep an eye on emerging trends in predictive maintenance to ensure your strategies remain relevant in a rapidly-evolving landscape.
In summary, integrating predictive maintenance is not just a smart choice; itâs a necessary evolution in fleet management. As industries continue to grow more competitive, those who adopt these strategies will not only survive but thrive in the future.
"The road ahead requires attention, foresight, and adaptability; predictive maintenance offers the tools to navigate it effectively."
By taking a step back to reflect on these foundational aspects, organizations can harness predictive maintenance to rebuild and reinforce the backbone of their fleet management operations.