Exploring Different Types of Quality Management Systems
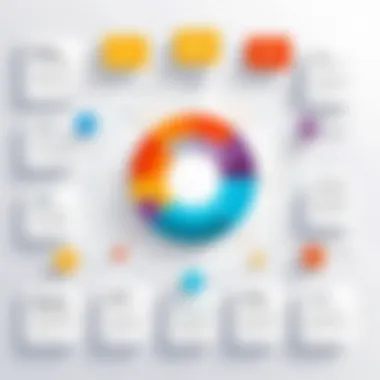
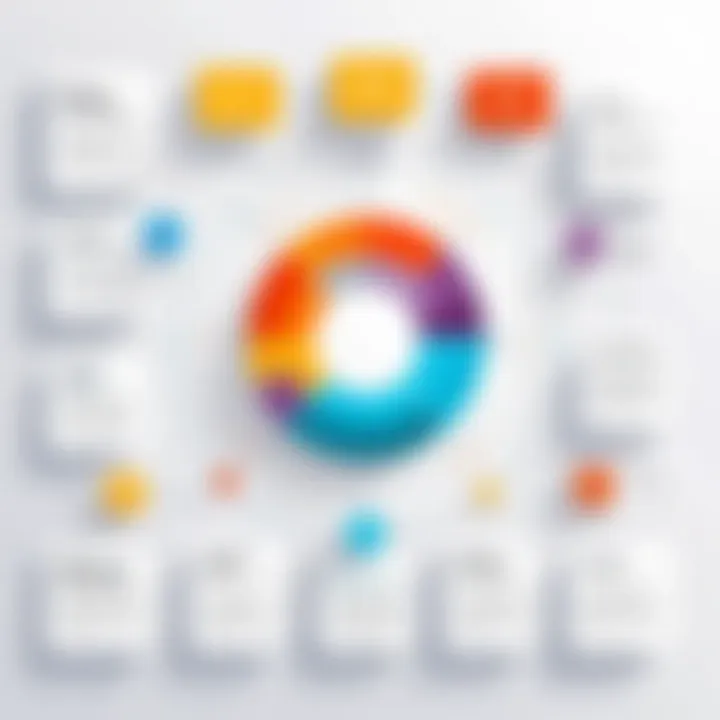
Intro
Equipped with the right insights, decision-makers, IT professionals, and entrepreneurs can make informed choices that bolster efficiency and enhance customer satisfaction.
Key Software Features
Adopting a quality management system often involves leveraging specialized software to facilitate processes, measure outcomes, and ensure compliance across the board. Understanding the key software features can help organizations identify the right solutions for their quality management needs.
Essential functionalities
- Document control: Systems often include features for managing documents, ensuring version control, and maintaining compliance with regulations.
- Non-conformance tracking: This functionality enables organizations to track deviations from standards, allowing for corrective actions to be implemented swiftly.
- Audit management: Effective systems come equipped with tools for planning, conducting, and managing audits, facilitating adherence to prescribed standards.
- Reporting and analytics: Reliable software provides in-depth analysis and reporting features, allowing stakeholders to derive insights from data and make data-driven decisions.
Advanced capabilities
- Integration with other systems: Modern quality management software often integrates seamlessly with existing enterprise resource planning (ERP) and other organizational software, fostering efficient workflows.
- Real-time monitoring: Advanced systems can track real-time data, providing insights that facilitate quick decision-making and responsiveness to changing conditions.
- Customizable workflows: Organizations can tailor workflows to fit their specific processes, making the system adaptable to diverse operational needs.
- Machine learning algorithms: Some cutting-edge solutions employ machine learning to predict trends, helping organizations proactively address potential quality issues before they escalate.
"Quality is not an act, it is a habit." - Aristotle
Comparison Metrics
When evaluating quality management systems, organizations must employ comparison metrics that provide a clear view of the potential benefits and drawbacks of each system. Two crucial metrics often utilized in this analysis are cost analysis and performance benchmarks.
Cost analysis
Cost is a significant factor when deciding on a quality management system. Here are key aspects to consider:
- Initial implementation costs: This involves software licensing fees, systems integration costs, and training expenses for employees.
- Ongoing maintenance costs: Organizations should factor in expenses related to software updates, support services, and user licenses.
- Return on investment (ROI): Analyzing potential savings from improved efficiencies and reduced errors can help justify the initial costs.
Performance benchmarks
When analyzing systems, organizations should also assess how well each performs in practical settings. Consider:
- Response time: How quickly can the system provide insights? Operational delays can be costly.
- User satisfaction: Gathering feedback from users can shed light on how effectively the system meets their needs and expectations.
- Compliance rates: Systems should be able to demonstrate a high degree of compliance with industry standards or regulations.
Understanding these metrics allows organizations to make a balanced decision that aligns with their operational goals and constraints. By diving into the specifics of each quality management system, businesses can tailor their approach to maximize efficiency and bolster customer satisfaction.
Understanding Quality Management Systems
Quality Management Systems (QMS) are crucial frameworks that organizations utilize to ensure their products and services meet customer expectations and regulatory requirements. These systems can lead to improved efficiency, reduced waste, and enhanced customer satisfaction, making them indispensable in todayâs competitive business landscape.
Definition and Purpose
At its core, a Quality Management System is a structure of processes, policies, and procedures that help an organization achieve its quality objectives. The primary purpose is to guide and standardize operations to achieve consistent quality outputs. By implementing a QMS, businesses can not only maintain quality but also identify areas for improvement.
Finding a clear definition can sometimes feel like chasing smoke; itâs elusive and often varies from one industry to another. However, generally speaking, a robust QMS integrates various management functions and empowers organizations to improve their performance continuously. This includes addressing customer needs, boosts operational efficiency, and ensures compliance with applicable standards.
Historical Context
The origins of Quality Management Systems can be traced back to the early 20th century. During this time, industrialists began seeking methods to systematize production processes. The Ford Motor Company, for instance, revolutionized manufacturing with its assembly line which aimed at minimizing waste. Fast forward a few decades, and we see the introduction of quality assessments by giants like W. Edwards Deming and Joseph Juran in the post-World War II era in Japan, as they helped rebuild the countryâs industrial capabilities. Their work laid the groundwork for modern quality management practices that adapt to changing market demands.
Quality systems matured throughout the latter half of the 20th century, culminating in the establishment of international standards such as ISO 9001. Organizations began to recognize the need for structured systems that not only promote quality but also enhance operational efficiency and customer loyalty.
Importance in Modern Business
In todayâs fast-paced business environment, the importance of understanding Quality Management Systems cannot be overstated. A well-implemented QMS contributes to:
- Consistency in Processes: Helps standardize operations which ensures that products and services are delivered at a certain quality level every time.
- Risk Management: By addressing various quality aspects, businesses can identify and mitigate risks that may affect product quality and customer satisfaction.
- Increased Customer Satisfaction: Satisfied customers are more likely to become repeat buyers. A reliable QMS helps businesses meet customer expectations and create a loyal client base.
- Regulatory Compliance: Many industries are governed by various regulations and standards. A QMS can assist companies in adhering to these requirements, helping to avoid legal issues.
"A quality system isn't just a badge to wear; itâs a commitment to excellence that permeates every corner of the organization."
As the business landscape continues to evolve, organizations that embrace Quality Management Systems will be better positioned to adapt and thrive. Theyâll transform their operations, maintain a competitive edge, and ultimately enhance their bottom line.
Total Quality Management
Total Quality Management (TQM) is vital in today's landscape of quality management systems. It emphasizes a culture centered on continuous improvement, with the goal of enhancing customer satisfaction. TQM isn't just a tool; it's a philosophy that permeates every aspect of an organization.
One of the most significant aspects of TQM is its holistic approach. It doesn't just focus on the output, but also on the processes that lead to quality products and services. This paradigm shift enriches the company culture and fosters teamwork since every member plays a role in maintaining quality. This leads to greater employee engagement because they feel their contributions matter, which in turn boosts morale.
Core Principles
TQM comprises several core principles that define its framework:
- Customer Focus: The customerâs needs shape the driving force behind all efforts. Listening and reacting to customers' feedback is essential.
- Total Employee Involvement: Each employee must be encouraged to participate, recognizing that they are crucial to meeting quality standards.
- Process-Centered Approach: Understanding and controlling the processes that lead to outcomes is fundamental.
- Integrated System: Every aspect of an organization must work together toward improvement and quality enhancement.
- Strategic and Systematic Approach: This underscores the necessity of aligning a companyâs goals with its processes.
- Continual Improvement: Pursuing improvement at all levels encourages organizations to stay ahead of the competition.
These principles serve as a foundation, guiding organizations in implementing TQM.
Implementation Strategies
Successful implementation of TQM requires careful planning and execution. Here are few strategies:
- Leadership Commitment: Senior leadership should be visibly dedicated to TQM principles.
- Training and Education: Provide training as needed to empower employees, ensuring they understand their roles in quality management.
- Establishing Quality Teams: Form cross-functional teams to encourage collaboration on quality initiatives.
- Data-Driven Decision Making: Use data to make informed choices, monitor progress, and adjust strategies as necessary.
- Recognizing Contributions: Acknowledge and reward contributions from individuals and teams to maintain momentum and engagement.
These strategies promote a TQM culture and facilitate smoother incorporation into an organization.
Case Studies
Case studies of TQM implementation provide tangible evidence of its effectiveness.
- Toyota: Recognized for its commitment to quality, Toyota uses TQM to enhance production processes and customer satisfaction. It focuses on continuous improvement through methodologies like Kaizen.
- Ford Motor Company: After facing intense competition in the 1980s, Ford embraced TQM to revamp its business strategies, focusing on employee involvement and customer feedback. As a result, they saw significant improvement in product quality.
- Mayo Clinic: This healthcare institution adopted TQM principles to enhance patient care and operational efficiency. Their success lies in the integration of patient feedback and staff involvement in quality initiatives.
These examples not only highlight the versatility of TQM across different sectors but also reveal how a commitment to quality can lead to remarkable improvements in efficiency and customer loyalty.
"Quality is not an act, it is a habit." - Aristotle
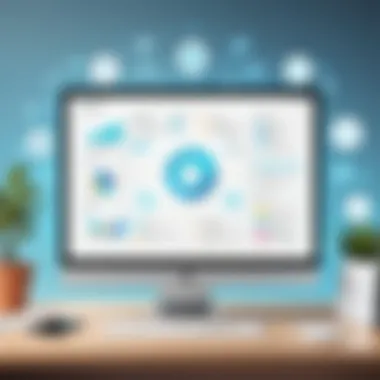
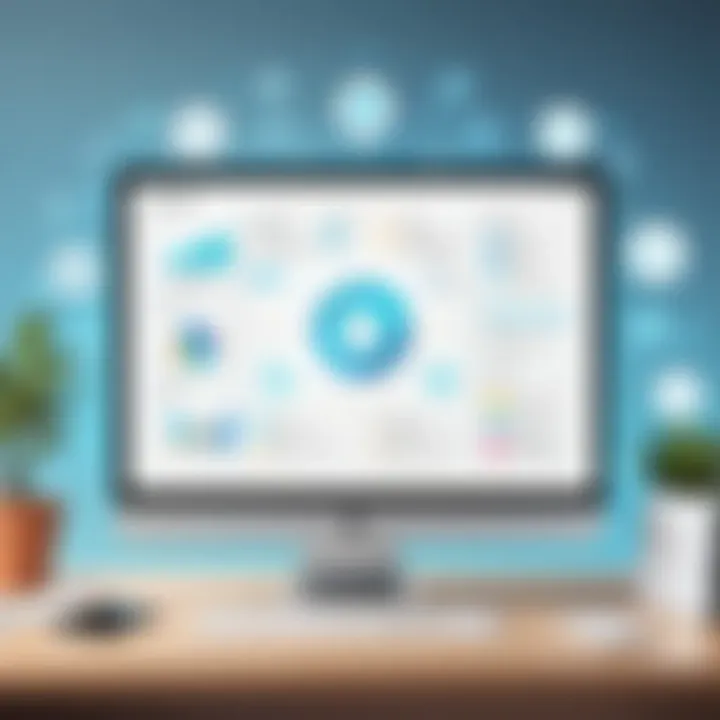
ISO Standard
ISO 9001 is a linchpin in the landscape of quality management systems, playing a pivotal role in guiding organizations toward enhancing customer satisfaction through effective quality management processes. Defined by the International Organization for Standardization, this standard provides a framework that outlines the requirements for a consistent quality management system. It's not just about box-ticking; itâs about embedding quality into every fiber of the enterpriseâs operational fabric.
Overview of ISO
ISO 9001 focuses on the principles of quality management that lead to consistent quality in products and services. At its core, it promotes the idea that meeting customer expectations and striving for continuous improvement are essential for every organization, regardless of size or industry. The standard is built on several fundamental principles, including:
- Customer Focus: Understanding and meeting customer needs is paramount.
- Leadership: A unified direction and purpose creates an environment conducive to achieving objectives.
- Engagement of People: Involving and empowering people at all levels fosters a culture of quality.
Benefits of Certification
Certifying to ISO 9001 yields numerous tangible benefits that resonate across organizational boundaries:
- Enhanced Customer Satisfaction: By systematically embedding quality into processes, organizations are more equipped to meet and exceed customer expectations.
- Improved Operational Efficiency: Streamlined processes often lead to reduced waste and lower operational costs.
- Global Recognition: ISO 9001 certification is recognized globally, providing a competitive edge in international markets.
- Operational Consistency: The standard helps ensure reliable and consistent products and services, minimizing variation that could compromise quality.
- Continuous Improvement: The framework encourages ongoing effort to refine and improve processes, sustaining long-term success.
"ISO 9001 isn't just a standard; it's a strategic tool for enhancing performance and stimulating growth."
Challenges in Compliance
While the advantages of adopting ISO 9001 are enticing, organizations must navigate some challenges to achieve and maintain compliance:
- Resource Allocation: Implementing the standard requires an investment of time and resources, which can strain smaller organizations.
- Resistance to Change: Employees' reluctance to adapt existing processes can slow down implementation efforts.
- Documentation and Record-Keeping: Maintaining the necessary documentation to demonstrate compliance can be a daunting task, particularly for those unfamiliar with formal quality management systems.
- Sustaining Engagement: Maintaining momentum post-certification can be tricky; organizations must keep the focus on continuous improvement to avoid stagnation.
Lean Quality Management
Lean Quality Management is a paradigm that emphasizes creating value while minimizing waste. Itâs particularly relevant in todayâs fast-paced business environment where efficiency can define competitive success. Businesses are increasingly turning to Lean principles as a means to elevate their quality management frameworks and achieve sustainable improvements.
Fundamental Concepts
The core idea behind Lean Quality Management revolves around understanding value from the customer's perspective. Here are some key elements that underpin this principle:
- Value Stream Mapping: This helps identify all the actions (both value-adding and non-value-adding) in a process, allowing organizations to streamline operations comprehensively.
- Waste Identification: Lean identifies seven types of wasteâoverproduction, waiting, transport, extra processing, inventory, motion, and defects. By targeting these areas, organizations can free up valuable resources.
- Continuous Improvement (Kaizen): This staged approach involves small, incremental changes which can lead to significant enhancements over time. Each employee plays a role, as everyoneâs input is crucial.
- Just-In-Time Production: This strategy aims to produce only what is needed when it is needed, thereby reducing inventory costs and inefficiencies.
Understanding these concepts equips organizations with a powerful toolkit aimed at enhancing product quality while reducing costs.
Tools and Techniques
Implementing Lean Quality Management involves a wide array of tools and techniques designed for precision and effectiveness. Some noteworthy tools include:
- 5S Methodology: This technique advocates for organizing workspaces systematically to improve efficiency. It stands for Sort, Set in order, Shine, Standardize, and Sustain. Each aspect pushes for tidiness and ease of access to necessary tools.
- Kanban: Often used in manufacturing, this visual system helps manage work by signaling when new tasks need to be initiated or completed, seamlessly integrating workflow into production.
- Root Cause Analysis (RCA): This method digs deep into issues to identify their root causes, preventing reoccurrences rather than merely treating symptoms.
- PDCA Cycle (Plan-Do-Check-Act): Itâs a cyclical approach for continuous improvement, facilitating project management from inception through completion with consistent feedback vectors to refine processes.
These tools, when applied effectively, can cause a ripple effect that transcends multiple levels of an organization, empowering teams to achieve higher standards of quality.
Real-World Applications
Lean Quality Management isnât just theory; itâs been actively applied across various sectors, yielding remarkable results.
- Manufacturing: Toyota is often highlighted for its groundbreaking Lean practices, famously embodied in its Toyota Production System, which has influenced countless organizations globally. Through meticulous evaluation and waste elimination, theyâve achieved extraordinary efficiencies while maintaining high product quality.
- Healthcare: The Virginia Mason Medical Center in Seattle adopted Lean principles to enhance patient care. By streamlining administrative processes and focusing on value from a patient standpoint, they reduced wait times and improved overall service delivery.
- Software Development: In the tech domain, companies frequently implement Lean methodologies to eliminate bottlenecks in product development cycles, leading to faster releases of high-quality software products.
By integrating Lean Quality Management with existing practices, organizations aren't merely optimizing for short-term goals but strategically positioning themselves for long-term success.
"The goal is to provide the best products and services possible while remaining aware of our impact on our work environment and customers."
This emphasis on sustainability highlights the need for quality in not just the end product but throughout the process. The Lean principles guide an organization not just toward efficiency, but also adaptabilityâa crucial trait in a rapidly evolving marketplace.
Six Sigma
Six Sigma is a powerful quality management methodology that aims to enhance organizational processes, reduce defects, and improve overall performance. This system plays a crucial role in various industries by promoting a culture of continuous improvement. Its fundamental focus lies in data-driven decision-making, ensuring that teams rely on solid evidence, rather than gut feelings, to drive changes. As competition becomes fiercer, Six Sigma stands out as a beacon for businesses aiming for operational excellence and customer satisfaction.
Principles of Six Sigma
At the heart of Six Sigma are several key principles that inform its philosophy and practices:
- Customer Focus: The ultimate goal of Six Sigma is to meet customer expectations. Understanding customer needs is critical in shaping process improvements.
- Data-Driven: Decisions are grounded in data analysis rather than assumptions. This precision helps to identify inefficiencies and target areas for improvement.
- Process Centricity: Six Sigma emphasizes viewing and optimizing processes rather than focusing on individual components. This ensures that the entire workflow is efficient and effective.
- Continuous Improvement: Organizations adopting Six Sigma commit to ongoing enhancements. Itâs about getting better every day, eliminating waste, and increasing quality.
"What gets measured gets managed."
This statement reflects the ethos of Six Sigma, emphasizing the importance of metrics in driving quality improvements.
DMAIC Methodology
The DMAIC framework is the backbone of the Six Sigma approach. It consists of five key phases:
- Define: Identify the problem, project goals, and customer requirements. Clear definitions set the stage for focused efforts.
- Measure: Gather relevant data to establish a baseline and evaluate the current performance against goals. Understanding where you stand is essential for progress.
- Analyze: Investigate the data to find root causes of defects or issues. This phase often utilizes various tools such as cause-and-effect diagrams and Pareto charts to visualize data.
- Improve: Develop solutions to improve the process and rectify any identified issues. Testing these improvements in real-world scenarios is critical.
- Control: Implement controls to maintain improvements and ensure that issues do not resurface. Ongoing monitoring is key to sustaining gains.
This structured approach allows organizations to methodically tackle problems and optimize their processes effectively.
Implementation in Various Industries
Six Sigma's flexibility makes it applicable across different sectors. Its principles and methodologies can be tailored to meet the specific needs of industries ranging from manufacturing to healthcare. Here are a few sectors where Six Sigma has demonstrated significant benefits:
- Manufacturing: The traditional domain for Six Sigma, where it started, focuses on reducing defects in products and enhancing operational efficiency.
- Healthcare: In this sector, Six Sigma helps in minimizing errors in patient care and streamlining processes, ultimately leading to better patient outcomes.
- Finance: Financial institutions use Six Sigma to enhance process consistency, eliminate errors in transactions, and improve customer satisfaction levels.
- IT and Software Development: Here, Six Sigma aids in identifying bugs in software and reducing cycle times for development and deployment processes.
Implementing Six Sigma can seem daunting, yet many organizations find that the dedication to quality yields high returns on investment in improved processes. Its enduring relevance points to its intrinsic value in navigating the complexities of modern business.
Quality Management Maturity Models
Quality Management Maturity Models are crucial for organizations striving to enhance their quality management systems. They serve as a roadmap, guiding businesses through various stages of quality development. Understanding these models is not just about improving processes but fostering a culture of continuous improvement.
Definition and Purpose
Quality Management Maturity Models are frameworks that help organizations assess their quality management processes against established benchmarks. The primary purpose is to provide a structured approach to evaluate where an organization stands in its quality management journey. These models highlight areas for improvement while offering a clear pathway to enhance quality practices.
This means organizations can identify gaps in their current practices and work to fill those gaps for better performance.
Common Frameworks
Several frameworks exist which outline the stages of maturation in quality management. Some common ones include:
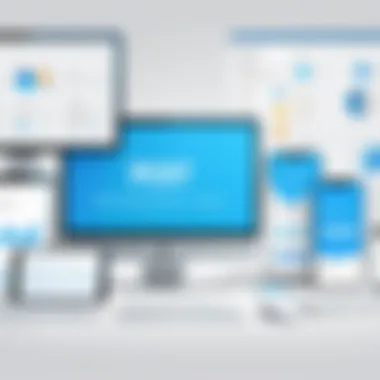
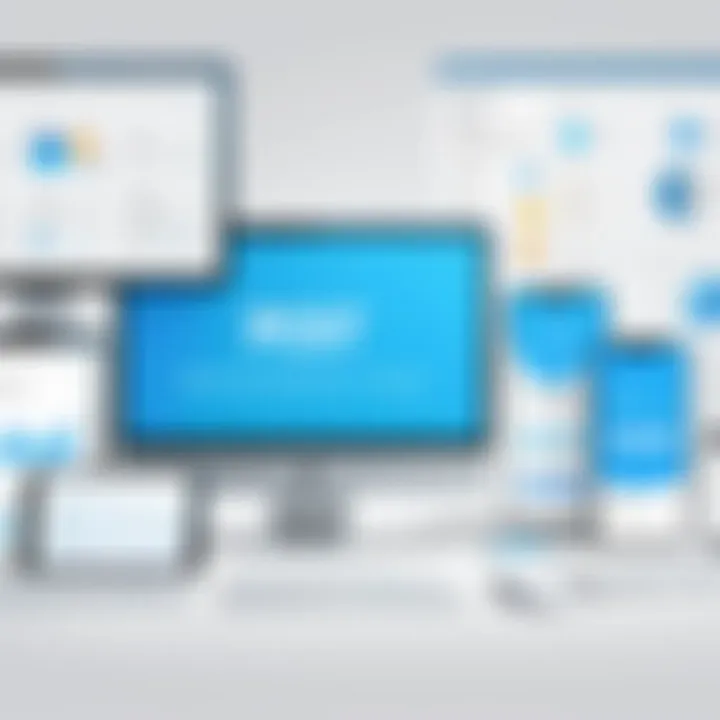
- Capability Maturity Model Integration (CMMI): This model is widely used in software development but applies to other sectors. It categorizes maturity into levels from initial to optimizing.
- Baldrige Excellence Framework: This model emphasizes performance excellence through key categories like leadership, strategy, and results. Organizations use this framework to assess overall performance.
- ISO 9001 Maturity Model: This is related to the ISO 9001 standard, focusing on continuous improvement and customer satisfaction as part of an organizationâs quality management system.
These frameworks are not one-size-fits-all. Depending on the industry, some might find one model more applicable than others.
For instance, while a tech company may lean towards CMMI for its detailed software processes, a manufacturing firm might find the Baldrige criteria more closely aligned with its operational goals.
Assessment Techniques
Assessing maturity can involve a variety of techniques, ensuring an organizationâs approach is tailored to its unique environment. Some common assessment methods include:
- Self-Assessment: Organizations often start here, using surveys and checklists to evaluate their current quality practices.
- Benchmarking: Comparing processes and outcomes to those of industry leaders can uncover useful insights for improvement.
- Third-Party Audits: Independent auditors can provide an objective perspective on an organizationâs quality maturity, offering detailed reports on performance.
- Focus Groups: Engaging employees across various levels can yield a wealth of input, revealing perceptions about the effectiveness of quality initiatives.
Effective assessment not only gauges where an organization is but also ignites discussion on where it wants to be. The goal isn't merely to check boxes but to inspire change.
In summary, Quality Management Maturity Models guide organizations on their journey toward improved quality practices. By defining maturity levels, utilizing established frameworks, and implementing assessment techniques, companies can pave a clearer path to operational excellence. This structured approach does not only promote efficiency but aligns quality management closely with overall business objectives.
Baldrige Performance Excellence Program
The Baldrige Performance Excellence Program is a beacon for organizations striving for exceptional performance. Established in the United States in 1987, this program aims to elevate the standards of quality and performance in companies across various sectors, including healthcare, education, and manufacturing. In todayâs fast-paced business environment, the importance of the Baldrige framework cannot be understated. It serves as a roadmap, guiding organizations toward excellence through a comprehensive set of criteria that focus on key areas such as strategic planning, customer service, and workforce engagement.
Overview of Baldrige Criteria
The Baldrige Criteria for Performance Excellence is divided into several categories, each targeting a crucial component of organizational success. These are:
- Leadership: Involves how leaders guide the organization and foster a culture of improvement.
- Strategy: Focuses on how the organization sets and deploys its strategic objectives.
- Customers: Examines how organizations engage with and learn from customers to drive satisfaction and loyalty.
- Measurement, Analysis, and Knowledge Management: Looks at how organizations assess their performance and manage information and knowledge.
- Workforce: Addresses how the organization manages its workforce to ensure engagement and development.
- Operations: Centers on how the organization designs its work processes for efficiency and effectiveness.
- Results: Involves the measurement of the organization's outcomes in various areas including financial, customer, and operational results.
Integrating these criteria helps organizations develop a comprehensive perspective on their operations, leading to continuous improvement and sustainability.
Impact on Organizational Performance
"Excellence is not a destination; it is a continuous journey that never ends."
The Baldrige Performance Excellence Program has a profound impact on organizational performance. Organizations that pursue Baldrige recognition typically experience increases in key metrics such as profitability and productivity. By adhering to the Baldrige framework, they are better equipped to improve efficiency and reduce waste, which in turn helps in cutting down costs. This is particularly significant in industries where margins are thin, and competitive advantages are essential for survival.
Moreover, the engagement of employees is markedly enhanced. When organizations actively involve their workforce in quality initiatives, it yields a culture of accountability and collaboration. Employees are more likely to feel valued and invested in the organizational goals.
Another notable impact is on customer satisfaction. Organizations applying the Baldrige criteria report higher levels of customer loyalty and repeat business. Understanding customer needs and providing tailored solutions can lead to strong relationships that are vital in todayâs complex market landscapes.
Quality Audit Systems
Quality audit systems stand out as crucial components in ensuring organizational excellence. They offer organizations a structured approach to evaluating and enhancing their quality management processes. Audits not only help in identifying deviations from set standards but also promote a culture of continual improvement. Having solid audit systems in place can lead to better compliance, informed decision-making, and ultimately boost customer satisfaction.
Audit Types and Purposes
Quality audits come in various shapes and sizes, each tailored to meet specific organizational needs. Here are some key types and their purposes:
- Internal Audits: These are conducted by the organization's own personnel. They focus on the effectiveness of the internal quality management systems and are essential for regular evaluations.
- External Audits: Carried out by independent parties, external audits verify compliance with standards like ISO 9001. They prompt organizations to maintain transparency and accountability.
- System Audits: These audits evaluate the overall management system, checking how different components work together to meet quality objectives.
- Process Audits: By examining specific processes, these audits assess whether practice aligns with prescribed procedures, helping pinpoint areas for improvement.
Each type serves a distinct purpose, aiding organizations in establishing baseline performance metrics, identifying weaknesses, and staying aligned with industry regulations.
Conducting Effective Audits
To conduct effective audits, there are several best practices worth adopting:
- Set Clear Objectives: Before the audit begins, clearly define what needs to be evaluated and the expected outcomes. Ensuring all team members understand the purpose will lead to a more focused process.
- Select Competent Auditors: Choosing the right people for the job is vital. Auditors need not just technical knowledge but also good interpersonal skills to foster open discussions during the audit.
- Utilize Audit Checklists: Employ checklists that outline all necessary criteria. This streamlines the assessment and enhances consistency across audits.
- Document Thoroughly: Keep thorough records of findings, discussions, and recommendations. This documentation not only provides a reference for future audits but also supports the audit's legitimacy.
- Encourage Participation: Engage all levels of staff during the audit, inviting input and feedback. A collaborative environment can unveil insights and foster acceptance of findings.
Feedback and Continuous Improvement
Feedback from audits is not merely a summary of results. It serves as a foundation for continuous improvement, allowing organizations to adjust and refine their processes. Hereâs how to harness feedback effectively:
- Review Outcomes Regularly: Regularly discussing audit results among team members keeps everyone aligned and encourages a proactive approach to problem-solving.
- Establish Action Plans: Develop specific plans to address identified issues. Assigning responsibilities ensures that everyone knows what they should do to enhance quality.
- Monitor Progress: After implementing changes, monitor progress to evaluate their effectiveness. If issues persist, revisit processes to identify underlying causes.
"Quality is not an act, it is a habit." This rings true, as only through continuous scrutiny and commitment can organizations build a culture of excellence.
Quality Data Management Systems
Effective quality management relies heavily on data. In this section, we explore the concept of Quality Data Management Systems, emphasizing their pivotal role in enhancing organizational performance. At its core, data management focuses on collecting, storing, and analyzing data to foster insights that drive continual improvement in products and services. For decision-makers and professionals alike, understanding these systems is crucial for maximizing quality control processes and ensuring consistency in output.
Quality Data Management Systems serve several critical functions, such as providing insights into operational efficiency and customer satisfaction. Proper management of quality data ensures that businesses not only comply with regulations but also proactively address potential issues before they escalate. Thus, this area cannot be ignored when designing or refining quality management strategies.
Role of Data in Quality Management
Data acts as the backbone of any quality management system. It provides the empirical evidence required to identify trends, track performance, and measure improvement over time. When utilized effectively, data allows organizations to make informed decisions rather than relying solely on intuition.
For instance, consider a manufacturing company that has been experiencing fluctuations in product quality. By collecting data on production processes, machine performance, and employee actions, they can pinpoint specific areas that contribute to the inconsistencies. This measurable approach enables them to implement data-driven solutions tailored to their specific challenges.
In short, the role of data in quality management cannot be overstated; it transforms subjective evaluations into objective, trackable metrics.
Tools for Data Analysis
Today, various tools exist to facilitate data analysis within quality management systems. Here are some notable tools:
- Statistical Analysis Software: Tools such as Minitab or SPSS streamline the process of performing complex statistical analyses, helping organizations decipher performance metrics.
- Business Intelligence Platforms: Software like Tableau or Power BI allows for the visualization of data in meaningful ways, enabling teams to follow trends and recognize patterns effortlessly.
- Quality Management Systems Software: Specific applications, such as Qualio or MasterControl, are designed exclusively for managing quality processes, including document control and compliance tracking.
These tools empower professionals to delve into the data, draw valuable conclusions, and enact necessary changes founded on factual understanding rather than guesswork.
Importance of Data Integrity
Data integrity refers to the accuracy and consistency of data throughout its lifecycle, and it is paramount in the realm of quality management systems. If the data is flawed, the decisions based on that data will inevitably lead to poor outcomes.
Data integrity can be compromised through various means, including human error, system malfunctions, and intentional tampering. Thus, organizations must implement stringent validation processes. Regular audits and cross-verification with source data can help maintain the integrity of the quality data.
"Quality data is the cornerstone of effective decision-making. Without it, organizations can easily veer off course, leading to inefficiencies and loss of customer trust."
Maintaining data integrity ensures compliance with standards and supports continuous improvement efforts. As organizations become increasingly data-driven, safeguarding the integrity of this data becomes vital to long-term success.
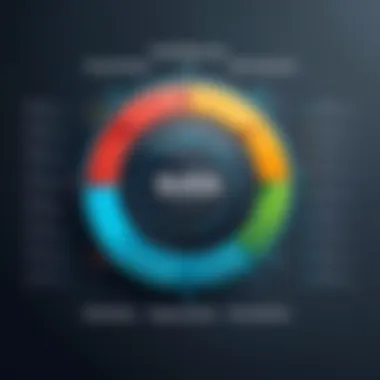
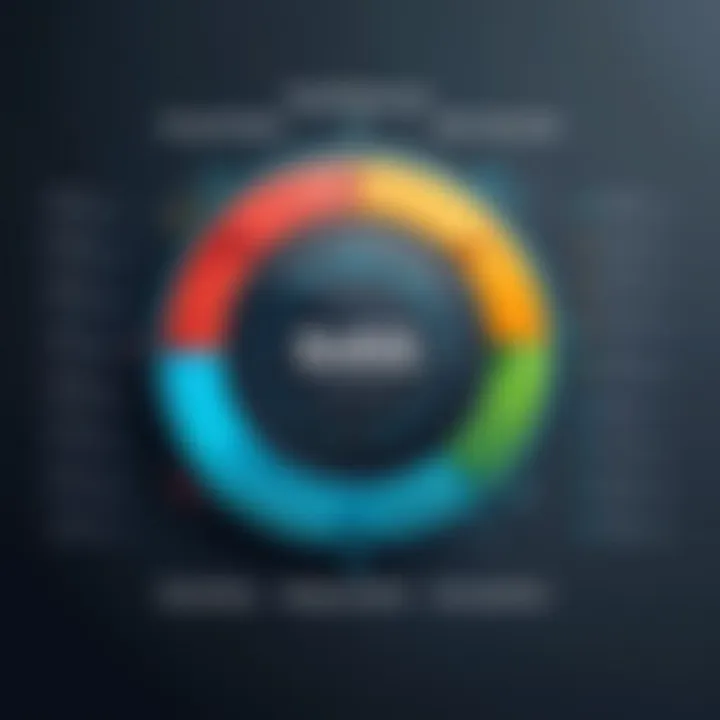
Technology in Quality Management Systems
Embracing technology in quality management systems is not just a trend; it has become a necessity for organizations aiming to thrive in todayâs fast-paced environment. With the complex demands of modern businesses, technology provides tools to streamline processes and improve the quality of products and services. This section will delve into the significance, benefits, and considerations of integrating technology in quality management.
Emerging Technologies Impacting Quality Management
A plethora of emerging technologies is making waves in the realm of quality management. These innovations shape how organizations monitor, control, and improve their processes.
- Internet of Things (IoT): IoT devices enable real-time monitoring of production lines, ensuring any deviations from quality standards are quickly identified. For example, a manufacturer can use sensors to track machinery performance and alert staff if a machine is operating outside its parameters.
- Cloud Computing: By leveraging cloud-based platforms, companies can store vast amounts of data securely and access it from anywhere. This approach facilitates collaboration across departments and even geographical locations.
- Blockchain: This technology ensures transparency and traceability in supply chains. For instance, if a food product is defective, blockchain can quickly pinpoint its source, allowing companies to react swiftly and effectively.
- Augmented Reality (AR): AR can train employees in complex tasks by overlaying instructions on top of their actual workplace, reducing errors and improving quality outcomes.
Incorporating these technologies into a quality management system not only boosts efficiency but also enhances customer satisfaction. A quality product delivered on time will keep customers coming back.
Role of Artificial Intelligence
Artificial Intelligence (AI) plays a transformative role in enhancing quality management systems. By processing vast datasets, AI makes sense of complex patterns, allowing organizations to predict potential quality issues before they arise.
- Predictive Analytics: AI can analyze historical data to predict trends and identify potential problems, enabling proactive management. For example, a quality management system using AI could anticipate a drop in product quality due to changing raw materials and recommend adjustments in the production process.
- Automated Quality Checks: AI-driven systems can automate the inspection processes, which not only speeds things up but also enhances accuracy. With machine learning techniques, these systems improve over time, learning from past inspections to become even better.
- Enhanced Decision-Making: Decision-makers can leverage AI tools to make informed choices. By presenting data in an easily digestible format, AI helps leaders grasp complex information at a glance.
- Personalization: In service industries, AI can help tailor experiences to individual preferences based on past interactions, leading to higher customer satisfaction.
As organizations adopt AI, they must also consider ethical implications and data privacy, ensuring that the benefits do not come at the cost of compromising customer trust.
Integrating technology into quality management systems not only boosts performance but also safeguards an organization's reputation and bottom line.
Future Trends in Quality Management
In today's rapidly changing business landscape, quality management is evolving at an unprecedented pace. This evolution is essential because it responds not only to market demands but also to technological advancements and shifting consumer expectations. Being attuned to these trends equips organizations with the knowledge and tools to remain competitive and innovative. As we discuss future trends in quality management, we will look closely at two pivotal areas: evolving standards and practices, and the effects of globalization.
Evolving Standards and Practices
Gone are the days when quality was just about adhering to established guidelines. Today's environment sees quality management systems adapting to newer methodologies. For instance, organizations are increasingly emphasizing agile quality management, which incorporates flexibility and continuous improvement into their processes. This adaptation allows companies to respond swiftly to changes without compromising quality.
With regulations tightening in many sectors, compliance is now a crucial part of quality systems. For instance, healthcare and manufacturing sectors must stay consistent with emerging international standards like ISO 31000. This standard focuses on risk management, helping organizations to preemptively manage potential quality setbacks.
Additionally, the rise of remote work is reshaping quality management practices. Teams spread across different locations must employ digital quality management systems that allow real-time data sharing and collaboration. Remote quality audits and online training programs are becoming more commonplace, showcasing how organizations are bending to technical solutions.
"In quality management, the only constant is change; staying ahead means embracing it."
Three key aspects to keep in mind about these evolving practices include:
- Integration of digital tools to enhance real-time monitoring of quality control.
- Cross-disciplinary approaches, combining insights from various fields to create holistic quality strategies.
- Sustainability practices now play a huge role, pushing organizations to incorporate environmental considerations into their quality management practices.
Globalization Effects
Globalization has a profound impact on quality management systems, presenting both opportunities and challenges for organizations worldwide. With businesses operating across borders, maintaining consistent quality across different regions has become essential. Quality management isn't just limited to one locale anymore; itâs about understanding multicultural and socio-economic contexts affecting standards everywhere.
One significant influence of globalization is the demand for uniformity in quality standards across markets. For instance, a product manufactured in one country must often meet the quality standards not only of its home market but also of international markets, like the European Union. This requirement calls for a deeper understanding of various frameworks that guide quality management on a global scale, including ISO 9001, which is recognized worldwide.
Moreover, globalization encourages collaborative quality approaches. Sharing best practices and learning from international peers can lead to better efficiency and innovation. Companies are beginning to realize that tapping into a global talent pool can bring fresh perspectives on quality issues. This can result in refined quality processes driven by diverse insights.
However, globalization also brings about challenges like communication barriers which can hinder effective quality control. Fluctuations in trade regulations and geopolitical tensions can disrupt supply chains and affect quality. Organizations must remain adaptable, preparing to navigate these complexities while ensuring quality is never compromised.
Challenges in Implementing Quality Management Systems
Implementing a quality management system (QMS) may seem straightforward, but it involves navigating through various challenges that can hinder its success. These challenges, if not addressed, can lead to inefficiencies, decreased employee morale, and ultimately a decline in customer satisfaction. Recognizing these hurdles is essential for decision-makers, IT professionals, and entrepreneurs aiming for operational excellence. Letâs delve into the specifics but keep in mind the benefits, considerations, and nuances of these challenges.
Organizational Resistance
A significant barrier to implementing quality management systems is organizational resistance. Often, employees might feel threatened by changes to their workflows and processes. This can stem from a lack of understanding regarding the changes or fear of increased scrutiny.
- Communication Breakdown: When leadership communicates inadequately or does not involve employees in the change process, it often leads to skepticism. Employees may feel left out and perceive the new system as something imposed upon them.
- Cultural Clashes: Each organization has its culture, and shifting this culture towards a more quality-focused approach can face pushback. For instance, if a company has a long history of informal processes, enforcing structured quality measures might seem disruptive.
To tackle organizational resistance, companies should prioritize effective communication on the reasons behind the change. Using training sessions can help ease fears, making employees feel included and valued. Furthermore, encouraging feedback allows employees to voice concerns and contribute to the decision-making process.
Resource Constraints
Another hurdle often encountered during the implementation of a QMS is resource constraints. Many organizations find themselves stretched thin, struggling to allocate the necessary time, manpower, and financial resources for such an initiative.
- Financial Investment: Quality initiatives can be costly, involving software systems, training programs, and potential restructuring. Budget constraints can lead organizations to cut corners, compromising the effectiveness of the system.
- Time Management: Employees already juggle numerous responsibilities. Adding the learning and adaptation of a new quality management system may feel like an insurmountable burden, leading to potential burnout and decreased efficiency.
Leaders must acknowledge these constraints and plan accordingly. Investing in a phased implementation approach may help alleviate some resource pressure. Allowing teams to adapt gradually rather than overwhelming them with change all at once can foster a more positive transition.
"Overcoming the barriers of resistance and resource limitations is vital. Thoughtful planning today aids in a more streamlined and effective quality management system tomorrow."
In summation, challenges like organizational resistance and resource constraints can significantly impact the successful implementation of quality management systems. Companies should take proactive steps to address these issues, reinforcing the importance of a quality-focus within their organizational culture. Understanding and navigating these challenges is essential for anyone looking to implement a robust QMS.
Epilogue
The conclusion of this article serves as a vital summation of the transformative landscape that quality management systems cultivate within organizations. Understanding the integral components of diverse quality management systemsâsuch as Total Quality Management, Lean, and the ISO standardsâequips decision-makers with the insight necessary to steer their enterprises toward success. By navigating through the distinct methodologies discussed, one gains a clearer picture of how quality systems not only enhance operational efficiencies but also bolster customer satisfaction, which is paramount in today's competitive market.
Quality management systems are designed to foster a culture that prioritizes excellence. When organizations adopt these systems, they don't just comply with standards but rather embrace ongoing improvement as a core value. This cultural shift has several remarkable benefits:
- Increased Efficiency: Streamlined processes minimize waste and reduce costs.
- Enhanced Customer Satisfaction: Products and services that meet or exceed customer expectations lead to loyalty and positive referrals.
- Greater Employee Involvement: Employees who understand their role in quality management are often more engaged and motivated.
However, the implementation of these systems requires careful consideration. Businesses must weigh the costs against the anticipated benefits and recognize that flexibility is critical to adapting these methodologies to their unique environments. Therefore, the conclusion ties back to the essence of a well-rounded quality management system; it is not solely about rigorous compliance but about cultivating a framework within which each part of the organization thrives together.
Summary of Key Points
Here are some key takeaways from our exploration of quality management systems:
- Definition and Purpose: Quality management systems aim to ensure that an organizationâs products and services consistently meet customer and regulatory requirements.
- Core Principles: Emphasizing continuous improvement, customer focus, and data-driven decision-making are central tenets across various systems.
- Frameworks: Each system, whether it's ISO 9001 or Lean, provides a unique framework that organizations can adopt according to their operational needs.
- Technology Integration: Modern tools and technology play a crucial role in supporting quality management systems, enhancing data integrity and process efficiency.
This distillation of information sheds light on the multi-faceted nature of quality management and its pivotal role in driving organizational success.
Final Thoughts on Quality Management Systems
Quality management systems are more than just a collection of best practices; they represent a strategic approach that positions organizations for sustainable growth and competitive advantage. Each system embodies principles that, when effectively harnessed, lead to transformative results across various sectors. As we look ahead, businesses need to remain attune to evolving quality standards while also embracing innovative tools to keep pace with changing demands.
In summary, implementing a robust quality management system can be the difference between mediocrity and excellence. As trends evolve, organizations should stay proactive, adopting a mindset geared towards quality that resonates deeply within their culture. The path isn't without challenges, particularly in aligning resources and combating resistance to change, but the rewards justify the effort.
In this ever-fluctuating business environment, having a strong foundation in quality management will undoubtedly pave the way for enduring success.