A Complete Guide to Estimating Construction Jobs
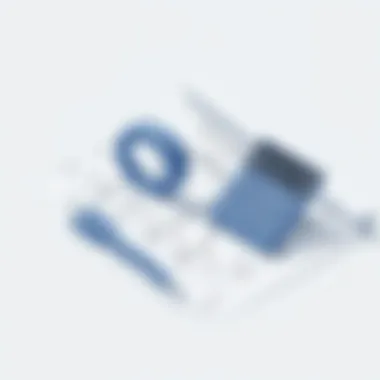
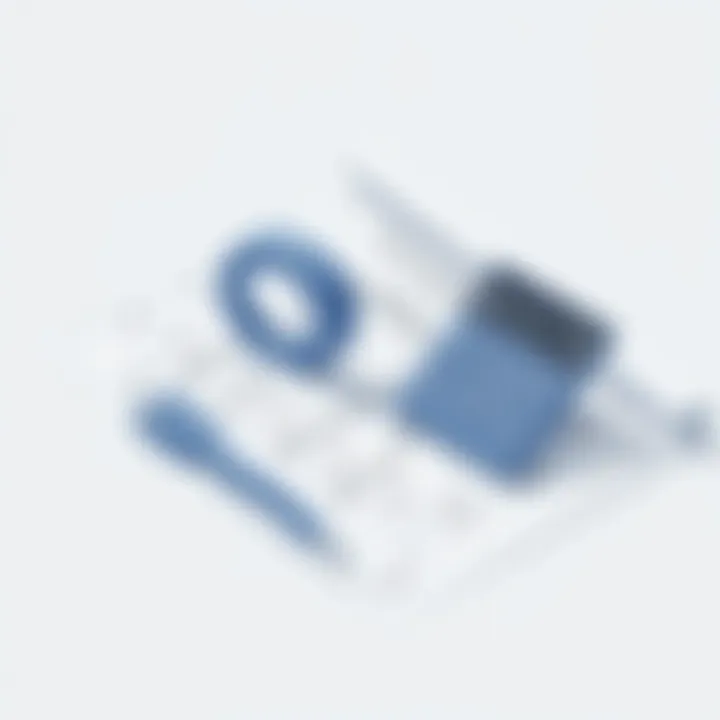
Intro
Estimating construction jobs is a practice that requires both skill and insight. Whether you're in the early planning stages of a new build or assessing ongoing project costs, the estimation phase is crucial. Missteps in this area can lead to budget overruns, project delays, and even strained relationships between contractors and clients. It's essential to understand the methodologies, tools, and techniques that can lead to accurate job costing. In this article, we will break down the layers of construction estimation, diving into the nuances that turn vague numbers into precise forecasts.
Understanding how to estimate effectively is not just about filling in numbers on a spreadsheet. It's like piecing together a puzzle where every piece represents a different aspect of the project — labor, materials, overhead, and potential risks. Each job is unique, entailing a delicate balancing act of scoping requirements, aligning resources, and forecasting inevitable uncertainties.
In this guide, we will first explore the key software features that make these calculations simpler and more efficient. Then we will delve into comparison metrics that can help differentiate between various tools and approaches. This exploratory journey aims to arm professionals with knowledge, thereby enhancing financial forecasts and streamlining project management. Ultimately, a well-grounded estimate sets the foundation for a successful construction job and ensures all parties involved remain on the same page.
Understanding Construction Estimation
Estimating construction jobs is a fundamental part of any successful building project. This section will lay the groundwork for grasping what construction estimation truly encompasses, and why it holds immense significance in the realm of construction management. An understanding of this process not only helps in accurate budgeting but also influences scheduling, resource allocation and ultimately, the success of construction projects.
Definition of Construction Estimation
Construction estimation refers to the systematic process of predicting the costs associated with a construction project. It goes beyond just crunching numbers; it involves a careful analysis of various factors such as materials, labor, equipment, and overhead costs. Think of it as putting together a jigsaw puzzle where each piece represents a cost element that fits together to form a complete financial picture of the project.
In essence, construction estimation can be categorized into different types, with preliminary, detailed, and bid estimates being the most recognized forms. Each serves a unique purpose and is utilized at different stages of a construction project. A preliminary estimate might be quite rough, setting the stage for feasibility, while a detailed estimate dives deep into all elements, giving a precise picture to work with.
Importance of Accurate Estimation
An accurate estimate is not just a mere number drawn from thin air; it is the cornerstone of budgeting and planning. In construction, every cent counts, and an erroneous estimate can lead to financial pitfalls that could have been avoided.
"A budget is more than a collection of numbers. It's an expression of our values and priorities." – Anonymous
Let’s peel back the layers on why precise estimation is crucial:
- Financial Stability: Predicting costs accurately ensures that funds are allocated appropriately, offsetting the risk of budget overruns that can cripple a project.
- Time Efficiency: A well-thought-out estimation plan can streamline processes and help in avoiding costly delays down the line.
- Resource Management: Knowing what you need, when you need it, helps in sourcing materials and labor effectively, preventing wastage.
- Stakeholder Trust: A reputable estimate builds confidence among investors, clients, and contractors alike. When they see a thorough assessment, they feel more secure about the project's financial footing.
Types of Construction Estimates
The significance of understanding the various types of construction estimates cannot be overstated. Different situations call for different estimation methods, and knowing when to deploy each type could spell the difference between a project's success and its untimely demise. Accurate estimations not only guide project planning but also influence bidding strategies, impacting the overall financial health of a construction business. Thus, it's crucial for professionals in the field to grasp the nuances of these estimating types.
Preliminary Estimates
Preliminary estimates serve as the first brushstroke on the canvas of a construction project. Generally created during the feasibility phase, these estimates provide a rough, high-level overview of the anticipated costs. The primary purpose here is to decide whether going ahead with a project makes financial sense. Unlike detailed estimates, these rely heavily on historical data, rough dimensions, and unit costs that are broadly accepted.
Some key points to consider:
- Purpose: Helps in determining project viability and securing initial funding.
- Data Source: Draws from previous project costs, industry standards, and commodity prices.
- Flexibility: Can quickly be adjusted if initial assumptions change.
The accuracy may be likened to reading the tea leaves; while it's not precise, it gives enough insight to either proceed or halt further investment in planning and scoping.
Detailed Estimates
When the rubber meets the road, detailed estimates come into play. These are utilized when a project is well-defined, and each line item needs scrutiny. They provide a granular view of what exactly is involved in the project, from materials to labor costs to equipment needs. With detailed estimates, there's an expectation that every last penny is accounted for, minimizing the risk of unexpected expenses cropping up later.
Important elements of detailed estimates include:
- Thorough Breakdown: Lists all components like subcontractor expenses, labor hours, and detailed material quantities.
- Methodologies: Incorporates various techniques, including quantity takeoffs and price evaluations.
- Precision: Aimed at delivering an accurate forecast, thereby aiding in bid formulation.
In many ways, a detailed estimate is that meticulous homework which, while time-consuming, pays dividends in confidence throughout the project lifecycle.
Bid Estimates
Bid estimates are pivotal for any contractor hoping to secure work on a project. Crafted with intention, they represent a contractor’s formal proposal to the project owner outlining how much the project will cost and how long it will take to complete. These estimates are typically based on detailed estimates but are tailored specifically to meet the requirements set forth in bid documents.
Several factors shape bid estimates:
- Competitiveness: Pricing must be in line with both market rates and competitor offerings.
- Adjustments: May involve negotiations or revisions after reviewing other bids.
- Inclusion of Risks: It often allows for a profit margin that considers potential uncertainties and project-related risks.
"When the stakes are high, knowing how to craft a competitive bid estimate can make or break your chances in the construction arena."
In summary, recognizing the distinct types of construction estimates is critical for a comprehensive approach to project financials. By using preliminary, detailed, and bid estimates strategically, construction professionals can enhance their decision-making process, improve profitability, and reduce the likelihood of budget-related pitfalls.
Key Components of Estimation
Understanding the key components of estimation is essential for anyone involved in construction budgeting. The accuracy of a project estimate hinges on several elements that, when properly considered, can lead to substantial cost savings and fewer surprises down the road. Misjudging any one of these components can alter project viability, timelines, and even relationships. Here, we will delve into three fundamental components: labor costs, material costs, and overhead and profit margins.
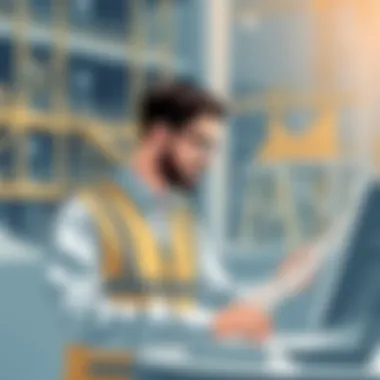
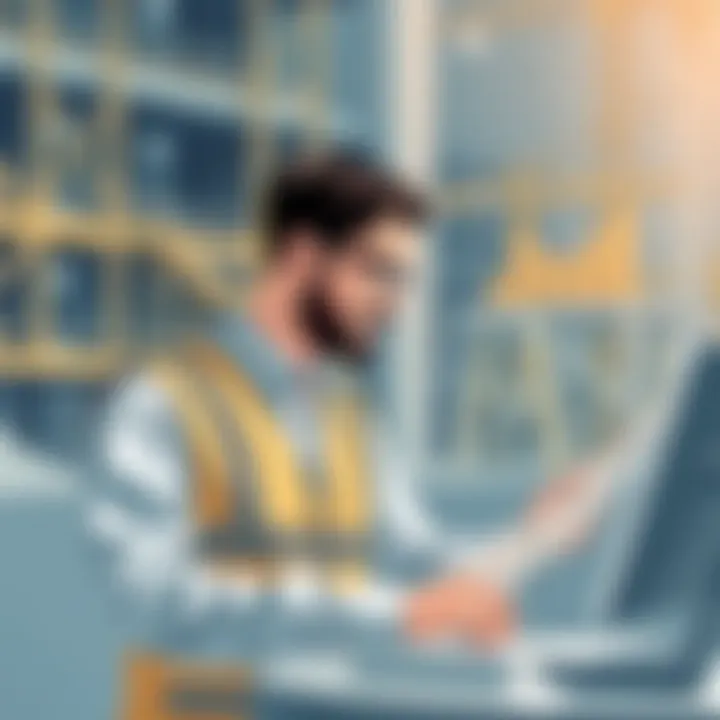
Labor Costs
Labor costs often represent a significant portion of the total construction budget. It encompasses not only the wages of the skilled workforce but also benefits, overtime pay, and even the administrative expenses associated with hiring staff. An accurate assessment of labor costs takes into account:
- Skill Level: Different trades come at different prices. For instance, electricians usually command higher wages than general laborers due to the specialized skills required.
- Geographical Variability: Labor rates can vary wildly from one region to another. If you’re working in a bustling metropolis, expect to pay more than if you're in a quiet town.
- Project Duration: A lengthy project might require reevaluating the labor rates as workers might seek higher compensation for extended commitments.
It's not just about the numbers but correctly estimating the human element and project dynamics. Factors like labor availability and local collective agreements can also influence these costs heavily.
Material Costs
Material costs are one of the primary variables in construction project budgeting. They are directly connected to the quality and quantity of the materials being utilized. To manage these costs effectively, consider:
- Quality Vs. Price: Sometimes, a more expensive material can save costs in the long run. For example, investing in high-quality insulation can reduce energy bills significantly.
- Supplier Relationships: Establishing solid ties with reliable suppliers isn't just good practice; it can lead to better pricing and priority during material shortages. You want to make sure you're not left empty-handed when the deadline looms.
- Market Trends: Keeping an eye on material price fluctuations can help you time purchases better. You wouldn't want to buy during a price hike if a dip is on the horizon.
Sometimes, it’s valuable to conduct periodic reviews of material estimations to adapt to ever-changing market conditions.
Overhead and Profit Margins
Overhead and profit margins are often the lesser-discussed elements of estimation, yet they significantly impact the overall financial health of a construction project. Overhead refers to all indirect costs necessary to keep a business running, excluding the actual project costs. These include:
- Admin Salaries: It’s crucial to account for the cost of your administrative staff, without whom the project wouldn’t succeed.
- Facility Costs: If your office is in a co-working space or you rent a site shed, these expenses should be factored in.
Profit margins, the markup on your costs, represent the profit earned for taking the business risk. While standard margins might hover around 10-20%, they can differ based on project type and industry standards. Be cautious, setting margins too high could deter potential clients, while setting them too low can squeeze your bottom line.
Remember: A well-thought-out estimation that includes accurate calculations of labor, materials, overhead, and profit can be the difference between a project that is profitable or one that results in unanticipated losses.
In summary, focusing on these core components can significantly enhance project outcomes. Each element must be assessed meticulously to ensure a comprehensive and realistic estimate. Ignoring any detail can result in wider repercussions, which can lead to project delays or cost overruns.
Methods for Estimating Costs
In construction, efficiency and effectiveness often hinge on the precision of cost estimation. Understanding various methods of estimating costs is crucial for professionals who aim to keep projects within budget, ensure client satisfaction, and maintain profitability. Each method offers distinct advantages and potential drawbacks depending on the scope and complexity of the project. Through this discussion, we will explore three primary estimating methods: Top-Down Estimation, Bottom-Up Estimation, and Parametric Estimation. These approaches not only cater to different project needs but also enhance the decision-making process by aligning estimations with real-world applications.
Top-Down Estimation
Top-down estimation is akin to drawing the big picture first; it involves establishing a project cost estimate based on overall project metrics. In this approach, costs are assessed from a macro perspective and then broken down into segments. Generally, this method is beneficial during the initial phases of a project when detailed information about components may not yet be available.
Some key points to note:
- Speed: This method allows for quick assessments. When time constraints are tight, it can be a lifesaver.
- Simplicity: It requires minimal detailed information, making it accessible for early-stage planning.
- Risk of Inaccuracy: If not checked against historical data or detailed estimates, the calculations can be less reliable for complex projects.
In practice, many project managers utilize top-down estimation when preparing initial budgets or during feasibility studies. By leveraging insights from previous projects, they allocate percentages to various project categories, such as labor or materials. Yet, it is vital to refine these estimates as more detailed plans develop.
Bottom-Up Estimation
In contrast to the top-down approach, bottom-up estimation starts at the granular level. This method involves creating detailed unit costs for individual project elements before summing them up to get the total project cost. It’s thorough, and as a result, it usually yields a more accurate overall estimate.
Here's why it is favored by many:
- Accuracy: Given its detailed nature, this method often leads to more precise cost projections.
- Transparency: Each component is accounted for, reducing the chance for hidden costs to arise unexpectedly down the line.
- Time-consuming: However, this method can be labor-intensive and lengthy, as it requires comprehensive data collection and analysis.
Implementing bottom-up estimation can be a daunting task, especially for larger projects, but once established, it often acts as a strong foundation for managing resources effectively. Construction managers frequently compile lists of materials and associated labor needs to calculate the precise costs involved.
Parametric Estimation
Parametric estimation is somewhat of a blend between top-down and bottom-up approaches. It relies on statistical relationships between historical data and project variables—like square footage or specific project types—to derive estimated costs. It's like using a formula that correlates costs to the quantity or dimensions of work to be done.
There are significant advantages:
- Scalability: This method can quickly adjust to varying project sizes based on the applied parameters.
- Data-Driven: Using historical data lends credibility, provided the data is relevant and current.
- Flexibility: It allows for adaptations as project specifications change.
However, relying heavily on parameters requires extensive historical data to be effective. If the relevant data isn't available, inaccuracies may permeate the estimation process. For instance, if a contractor is estimating a building's cost, inputting square footage and historical data on similar projects can provide a reasonably accurate estimate, but a lack of relevant data could lead off the mark.
Tools and Software for Estimation
When it comes to estimating construction jobs, the right tools and software can make all the difference. These resources serve not just as digital conveniences but as vital cogs in the estimation machine, streamlining processes, enhancing accuracy, and ultimately saving time and money.
The construction industry navigates a maze of variables every day. From fluctuating material costs to labor availability, the complexity can be overwhelming. Here’s where the right tools come in handy. They not only help to collect pertinent data but also allow for a clear presentation of estimates, making it easier for decision-makers or stakeholders to understand.
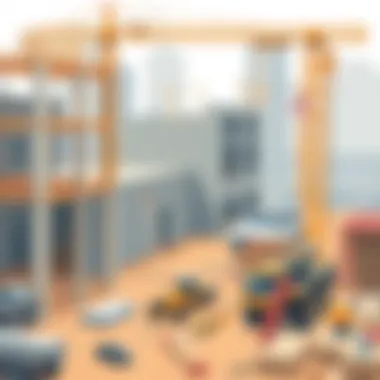
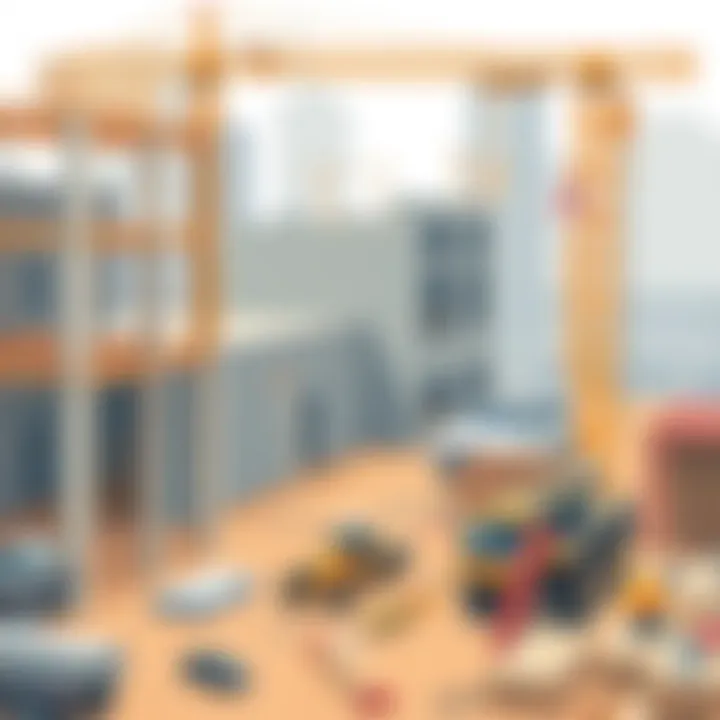
Benefits of Using Tools and Software For Estimation:
- Accuracy: Advanced tools can ensure that every detail is measured and accounted for, reducing human error.
- Efficiency: Automated calculations and data processing can speed up the estimation process, allowing projects to kick off sooner.
- Data Management: Modern software can store historical data, facilitating informed decisions based on past projects.
- Collaboration: Cloud-based solutions allow multiple stakeholders to access and contribute to estimates from anywhere, enhancing communication.
- Customization: Many tools cater to specific project needs, offering flexibility that traditional methods lack.
In short, these tools are essential, akin to a sturdy foundation in a building. A firm estimate relies on solid data and reliable software support.
Traditional Estimation Tools
Despite the surge of modern technology, traditional estimation tools remain relevant in the construction industry. Methods such as the trusty pencil-and-paper approach, templates, or even spreadsheets like Microsoft Excel are still favored by many professionals for their straightforwardness.
Why Stick with Traditional Tools?
- Simplicity: Some may argue that traditional tools eliminate the learning curve associated with software. For those not tech-savvy, a notebook can seem much less daunting.
- Cost-Effective: For smaller contractors or projects, investing in complex software may not be feasible. Traditional methods usually come with little to no financial commitment.
- Tactile Experience: There’s something inherently satisfying about writing down numbers and calculations by hand. It can foster a deeper connection to the data.
These tools, while low-tech, also allow professionals to customize their own systems without limitations imposed by software. However, one must also be aware of the drawbacks, such as increased chances for errors and lack of scalability.
Modern Software Solutions
As the world evolves, so does the technology used in construction. Modern software solutions offer powerful capabilities that can transform the estimation process. From comprehensive software packages like ProEst to cloud-based options like PlanSwift,
Advantages of Modern Software:
- Speed: Automated features enable rapid calculations, accelerating project timelines significantly.
- Integration: Many software solutions can integrate with other digital tools for project management, making it easier to track all phases of construction in one platform.
- Reporting: Modern software can generate detailed reports that provide insights into budgets, resources, and timelines.
- Data Visualization: Graphs and charts created by these tools can provide a clearer understanding of project metrics for clients or stakeholders.
With tools steadily becoming more robust and user-friendly, it’s clear that they are not just a passing trend but an essential aspect of contemporary construction estimation.
Cost Databases
Cost databases serve as a repository of information about material and labor costs, providing a valuable reference point for estimators. They compile vast amounts of data, drawing from various sectors of the industry, which means you aren’t left guesstimating in the dark.
Key Features of Cost Databases:
- Standardization: They provide a baseline for costs, making it easier to compare quotes from different suppliers or labor sources.
- Updates: Many cost databases are regularly updated to reflect the latest market trends, ensuring that estimators are working with relevant figures.
- Accessibility: Digital databases allow for instant access to information, saving time that would otherwise be spent tracking down costs manually.
- Enhanced Decision Making: Data drawn from historical trends empowers estimators to make informed forecasts for future projects.
One notable example of such a database is RSMeans, which is widely utilized in the industry. These databases not only enhance accuracy but also serve as crucial components in the estimation toolkit.
"Utilizing cost databases in conjunction with modern estimation software leads to improved accuracy and more reliable project forecasting."
Factors Affecting Construction Costs
Estimating construction costs effectively is not just a science; it’s also an art, one molded by various external and internal factors. Understanding these factors is crucial because they can mean the difference between a project coming in under budget or spiraling into financial chaos. With the construction landscape always changing, familiarizing oneself with the myriad of elements that influence costs can greatly enhance accuracy in job estimation. Doing so provides a competitive edge in a field where miscalculations can lead to substantial losses.
Economic Conditions
When it comes to construction, the economic climate plays a pivotal role. Fluctuations in the economy can directly influence material costs, labor rates, and the availability of resources. For instance, during a robust economic period, there’s often a surge in construction activity. This leads to increased demand for manpower and materials, which, in turn, drives up costs. Conversely, in a recession, projects may be scaled back or put on hold entirely, leading to a glut of labor and often reduced material prices.
Understanding the economic pulse allows estimators to predict trends over time, helping to fine-tune budgets accordingly.
Moreover, government policies and regulations can shift based on economic conditions, impacting everything from building codes to environmental regulations. Navigating through these can require additional considerations that must be accounted for during the estimation process.
Material Availability
Material costs can be unpredictable and are heavily reliant on global supply chains. When materials are in high demand, prices can surge dramatically. For instance, the recent surge in steel prices was almost completely due to supply chain disruptions caused by global events; unexpected shortages can wreak havoc on budgets. Estimators need to keep a close eye on market trends and stock levels to anticipate shifts in pricing.
Additionally, local availability plays a critical role. Regions that have easier access to specific materials might find better pricing compared to those that rely on imports. Factors such as local production capabilities, transportation costs, and even political stability can impact availability and costs.
- Be proactive: Estimators should:
- Keep updated with industry supply newsletters.
- Regularly consult with suppliers to gauge the future costs of materials.
- Consider alternative materials that might offer cost savings without compromising quality.
Labor Market Trends
Labor can often be the most intricate piece of the cost puzzle. The labor market is influenced by multiple factors, including demographic shifts, education and skill levels, and even local economic conditions. As the construction industry continues to evolve, finding skilled labor has become increasingly tougher. When demand outpaces supply, it translates to higher wage rates, which, in effect, elevates overall costs.
It’s important to consider not just the cost of labor, but also the quality. Hiring inexperienced workers can seem cost-efficient at first glance but may lead to mistakes that could cost a company much more in the long run.
- Key considerations for estimators:
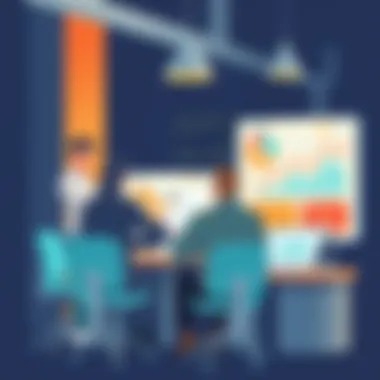
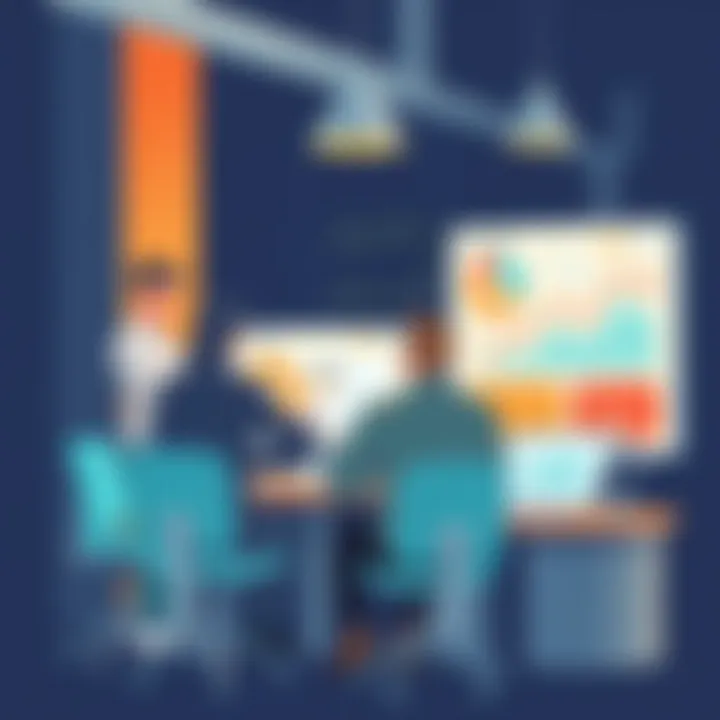
- Monitor trends in vocational training institutions and apprenticeship programs.
- Understand the demographic trends in your area, as population growth indicates a potential surge in labor demand.
- Utilize strategic workforce planning to manage contingencies related to labor shortages.
Understanding the multifaceted factors affecting construction costs is not merely a technical necessity; it’s a vital part of strategic project management. By considering the economic landscape, keeping tabs on material availability, and staying aware of labor market trends, professionals can craft more reliable estimates, thereby safeguarding their projects from unforeseen financial pitfalls.
Risk Management in Estimation
In the world of construction, where the stakes are high, understanding and implementing risk management in estimation can be the difference between a successful project and a financial disaster. Risk management is not just a buzzword; it’s an essential strategy that encompasses identifying, analyzing, and responding to potential risks associated with construction costs. When done correctly, it can lead to not only better budgeting but also to improved overall project efficiency.
Identifying Risks
The first step in effective risk management is recognizing the risks that might crop up throughout the construction process. This goes beyond just the obvious hurdles like weather delays or labor disputes. Risk can arise from:
- Supply chain issues: If a supplier unexpectedly goes out of business or can’t deliver materials on time, the whole project can come to a halt.
- Regulatory changes: New laws or regulations can add additional layers of cost that were not initially budgeted.
- Design changes: Whenever stakeholders make last-minute changes to designs, it can throw off estimated costs and timelines significantly.
- Economic fluctuations: A sudden spike in material prices or a downturn in the economy could impact the project's financial viability.
"Identifying risks early can significantly minimize their impact down the line."
Employing techniques like SWOT analysis (Strengths, Weaknesses, Opportunities, Threats) or brainstorming sessions with team members can help in pinpointing these risks effectively.
Mitigating Risk Factors
Once you've identified the risks, it's time to strategize on how to tackle them. Mitigating these factors involves developing systematic approaches to either eliminate or reduce the likelihood of these risks affecting the project. Some useful strategies include:
- Diversifying suppliers: By not relying on a single source for materials, you cushion yourself against potential disruptions.
- Regular communication: Keeping the lines open with all stakeholders can help in shortcutting the rumor mill and getting ahead of potential problems.
- Building in flexibility: Whenever feasible, plan for variable costs and timelines. For instance, allocating some budget for unexpected expenses.
- Risk transfer: Sometimes the best way to deal with risk is to simply pass it on. This might involve purchasing insurance or employing subcontractors who can take on certain project risks.
Mitigation plans should be reviewed and updated at regular intervals to match the evolving nature of the project.
Contingency Planning
Despite your best efforts, risks may still materialize. That’s where contingency planning comes into play. This involves preparing for the unexpected and having a plan B in place to ensure that the project stays on track. Effective contingency planning includes:
- Setting aside contingency funds: Depending on the project's size, having a reserve of around 5-15% of the total budget is advisable.
- Defining trigger points: Establish criteria for when to activate your contingency plan, so everyone knows when to pivot.
- Documenting processes: Having clear documentation of what steps to take in case of specific risks arising can streamline decision-making.
- Training the team: Preparing your team to be adaptable can go a long way. This might mean conducting regular training sessions or simulations to ensure they're ready for anything.
Best Practices for Estimating
When dealing with construction jobs, precision in estimating can mean the difference between profit and loss. Employing best practices in this area not only streamlines processes but also enhances project success rates. Here are vital practices that can improve the accuracy and reliability of your estimates:
Continuous Learning and Adaptation
In a field as dynamic as construction, continuous learning is crucial. The environment is ever-changing, influenced by new materials, regulations, and technologies. Professionals in the industry should engage in ongoing education, whether through formal workshops or self-study. Regular training allows estimators to stay on top of the latest trends, tools, and methodologies.
Additionally, adaptation based on previous project outcomes is equally significant. Learning from past mistakes—and successes—helps refine future estimates. For instance, if a certain material consistently exceeds budget projections, consider researching alternatives or adjusting your unit costs accordingly. Continuous learning is not just a phase, it's a strategic mindset.
Utilizing Historical Data
One surefire way to increase accuracy in estimates is by reviewing historical data from previous projects. By analyzing how costs unfolded in the past, estimators can identify patterns that may not be immediately apparent. Historical performance records serve as benchmarks, offering real-life insights into labor costs, material usage, and project timelines.
Moreover, utilizing databases like those from the Associated General Contractors of America can provide a wealth of useful figures. When you put this information to work, you gain a much clearer picture of potential costs, reducing the likelihood of any shockers down the line. But remember, while history does provide guidance, it should not be the only factor. Context is crucial, as each project has inherent variables that previous projects may not have faced.
"If you don’t know where you’re going, any road will take you there." - Lewis Caroll
Collaboration and Communication
Estimation isn’t a solo endeavor; effective collaboration is key. Engaging various stakeholders—from project managers to subcontractors—can result in more comprehensive estimates. Each participant brings unique insights that can help fill in knowledge gaps. Poor communication can lead to inaccuracies that can spiral into costly oversights.
Implementing regular check-ins and discussing projections openly can foster an environment conducive to accurate and timely estimates. Leverage tools and platforms that facilitate communication across teams, ensuring everyone is aligned on project goals and expectations. Ultimately, enhancing communication streamlines the estimation process while also enhancing the overall quality of project planning.
In summary, best practices in estimating construction jobs revolve around embracing learning, utilizing historical data, and ensuring lines of communication are always open. Following these practices can significantly boost accuracy, leading to more successful project completion.
Closure
When it comes to estimating construction jobs, the importance of thorough analysis can’t be overstated. This article dives into various aspects of construction estimation, shedding light on its significance in project management and financial planning. Accurate estimating forms the bedrock of successful construction projects, allowing for on-budget delivery and resource management. It’s not just about crunching numbers; it’s about strategic foresight that anticipates challenges and prepares for them. Without proper estimation, projects can spiral out of control, leading to financial loss and project delays.
Recap of Key Points
- Understanding Construction Estimation: It encompasses the assessment of costs, time, and resources.
- Types of Estimates: Various estimates serve different purposes, ensuring that stakeholders have the right information.
- Key Components: Recognizing labor, material costs, and profit margins is crucial for making informed decisions.
- Estimation Methods: Utilizing methodologies like top-down or bottom-up gives a clearer picture.
- Tools and Software: The right tools enhance accuracy and efficiency in the estimation process.
- Factors Affecting Costs: Economic conditions and market trends should constantly be monitored.
- Risk Management: Identifying and planning for risks is key to successful project outcomes.
- Best Practices: Continuous learning and effective collaboration are pillars of robust estimation practices.
Encouragement for Best Practices
To navigate the complexities of construction estimation, embracing best practices can provide substantial benefits.
- Stay Informed: The construction industry is ever-evolving. Engaging in continuous learning can help professionals keep up with trends and shifts in the market.
- Utilize Historical Data: Past projects can provide invaluable insights into potential costs and challenges for new undertakings. Leverage data to make informed projections.
- Foster Collaboration: Open communication between team members ensures that knowledge and expertise are shared, creating a more accurate estimation process.
"Investment in knowledge pays the best interest."
This timeless wisdom applies to construction estimation, for those who are willing to adapt and learn find themselves better positioned for success.