Efficient Tool Inventory Management in Construction
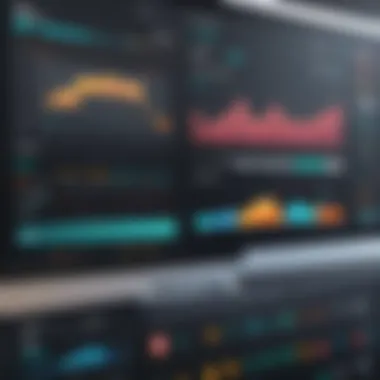
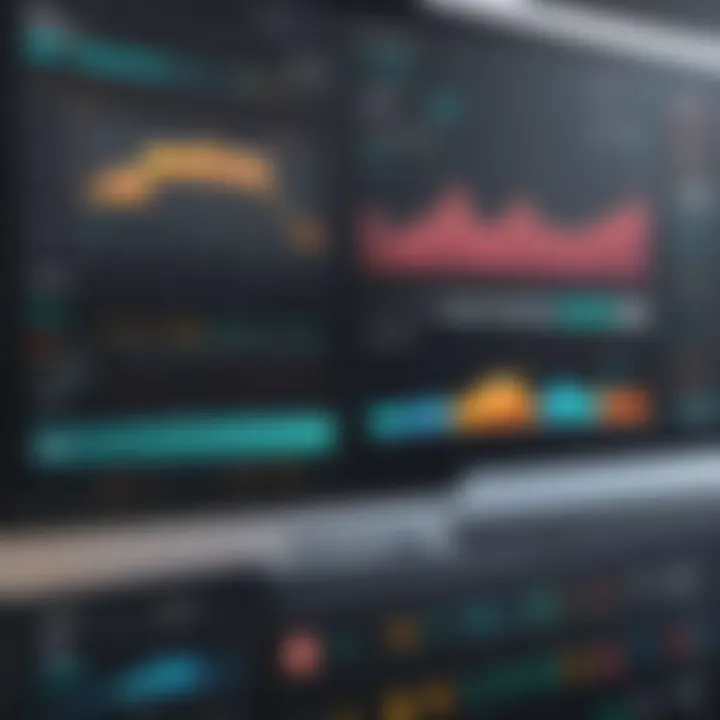
Intro
In the bustling world of construction, effectively managing a tool inventory goes beyond mere organization; it’s a linchpin for both productivity and cost management. Tools are the heart and soul of any construction site—their availability and optimal usage directly impact timelines and budgets. When tools vanish into the abyss of mismanagement or become dysfunctional due to neglect, projects can face significant delays or even financial overruns.
Considering these stakes, it’s essential for construction companies to adopt a pragmatic approach to tool inventory management. This not only helps in cutting down confusion and loss but also elevates the overall efficiency of operations.
By integrating robust systems and technologies, firms can ensure that their tools reside not just in designated spaces, but are utilized correctly and effectively. In the sections that follow, we will dissect various elements that compose an efficient tool inventory management system, explore software features, and provide concrete metrics for making an informed decision.
Ultimately, the goal is to empower decision-makers with the insights necessary to refine operational practices and bolster productivity in their projects.
Understanding Tool Inventory Management
In the world of construction, tools are the lifeblood of any project. Whether it's a hammer, a power drill, or sophisticated machinery, these instruments are necessary not just for task execution, but for ensuring projects are completed on time and within budget. Understanding tool inventory management, therefore, becomes essential for anyone involved in construction management. A refined approach in this area can significantly impact operational efficiency, minimize costs, and enhance overall productivity.
Definition and Importance
Tool inventory management refers to the systematic process of tracking, controlling, and maintaining construction tools and equipment. It's not just about knowing which tools are on hand; it's about understanding how frequently they are used, where they are located, and when they require maintenance. The importance of effective tool inventory management cannot be overstated:
- Cost Control: Missing or broken tools lead to unexpected replacement costs and project delays. A well-organized inventory helps avoid such expenses by ensuring proper tracking and maintenance.
- Increased Productivity: When workers know exactly where to find the tools they need, less time is wasted in searching or waiting. This expedited access allows for smoother daily operations.
- Minimizes Risks: Proper inventory management prevents safety hazards that arise from using defective or poorly maintained tools, fostering a safer work environment.
- Improving Accountability: When each tool has a designated custodian or usage log, accountability is inherent in the process, which cultivates a culture of responsibility among team members.
"Effective tool inventory management is not merely an operational task; it's a strategic advantage that can lead to significant savings and enhanced performance in construction projects."
Key Components of Tool Inventory Management
For an effective tool inventory management system to work, several key components must be taken into account. These components create a comprehensive framework that allows for seamless inventory control. Here are some fundamental aspects:
- User-Friendly Categorization: Tools should be categorized based on type, project, or usage frequency. This categorization facilitates easy identification and access.
- Real-Time Tracking: Implementing tracking systems, like barcode or RFID technology, allows managers to keep a live check on inventory levels and tool locations.
- Regular Audits: Conducting periodic audits is vital. It verifies inventory accuracy, informs future purchasing decisions, and identifies any potential theft or loss.
- Scheduled Maintenance: Keeping track of each tool’s maintenance schedule ensures that they are always in peak condition, reducing the likelihood of surprises when they are needed most.
By comprehensively understanding the specifics of tool inventory management, construction professionals can create more streamlined, efficient processes that ultimately enhance the success of their projects.
Challenges in Managing Construction Tools
Tool management in construction settings is not merely an operational necessity; it represents a labyrinth of challenges that can significantly undermine productivity and profitability. Understanding these hurdles helps firms design tailored strategies that can help mitigate risks and optimize processes. By acknowledging the common difficulties that arise in this domain, operators can implement more effective systems. Here, we will explore several crucial challenges that can impede the actualization of efficient tool inventory management.
High Costs of Tool Loss
One of the most pressing issues plaguing construction firms is the financial drain caused by tool loss. Tools don’t just vanish into thin air; they often end up stolen or misplaced on job sites. Once lost, the immediate impact is felt in the project's budget, but the ripple effects often extend far beyond that. Consider the costs associated with replacing specialized tools or those that are essential for certain projects; these aren't just pocket change. The procurement delays can cause project timelines to stretch, adding unexpected overhead.
Furthermore, the cumulative effect of tool losses can create a culture of negligence among the workforce. When employees see that tools are lost routinely, their own vigilance may drop as they think, "Why bother? Tools will just disappear anyway." This mindset can erode accountability and, in turn, lead to more losses. A robust tracking and management system can greatly diminish these losses; knowing the whereabouts of a tool at all times can provide a sense of security that encourages ownership among workers.
Maintenance and Downtime Issues
Regular maintenance is another critical aspect that faces either neglect or insufficient attention in tool management. Tools, much like patients in a clinic, require regular check-ups to function at their best. If maintenance schedules are overlooked, the implications can be dire. Inoperative tools can halt progress on job sites, causing a domino effect of delays that might tie up resources and soak up budget allocations.
To address these maintenance gaps, firms need to shift toward preventive maintenance schedules. This means creating a routine that encompasses both regular inspections of tools and the performance metrics that accompany them. Keeping records of maintenance allows for analyzing patterns that may reveal particular tools requiring more consistent care. Remember, an ounce of prevention is worth a pound of cure. This proactive approach will not only reduce tool-related downtime but also ensure that operations run like a well-oiled machine.
Worker Accountability and Responsibility
Accountability is often a tricky beast in the realm of construction tools. Without clear ownership, tools tend to suffer the fate of neglect. Workers may not care as much about tools that they do not feel are their responsibility. This discrepancy can lead to a lax attitude towards the management of tools. A careless focus on tools can lead to not just loss but also misuse.
To mitigate this issue, it is essential to instill a culture of responsibility among employees. Standardizing practices, including check-in/check-out procedures, can create a sense of attachment to the tools being used. If workers are required to account for tools, they may be less likely to leave them lying around or fail to report damages. Adding training elements that include a component on tool care and management can also bridge the gaps between employee awareness and actual practices.
"A tool not cared for is like a ship without a captain—lost and aimless."
Overall, by actively fostering worker accountability, businesses can create a more disciplined approach to tool management that nurtures respect and care for the equipment in use.
Implementing an Effective Inventory System
When it comes to tool inventory management, having a systematic approach isn’t just a nice-to-have; it’s a necessity. The construction industry is notorious for its complexities, and a well-thought-out inventory system can mean the difference between seamless operations and chaotic mishaps. Implementing an effective inventory system can streamline processes, enhance accountability, and ultimately lead to cost savings. Understanding this aspect is crucial for decision-makers and entrepreneurs who aim to maximize resource utilization and reduce waste.
Assessing Current Inventory Practices
Before diving headfirst into any new systems or technologies, it’s vital to take a step back and assess your current inventory practices. This phase is almost like doing a health check on your operations.
- Inventory Accuracy: Start by evaluating how accurate your current inventory records are. Are the tools listed in your inventory actually on hand? A few misplaced items can skew your workload.
- Tracking Methods: Analyze the methods currently in use to track tools. Are you using a manual log? A spreadsheet? Both methods can be prone to human error and can’t quite keep up with larger operations.
- Usage Rates: Look into how often each tool is used. Tools that sit around unused for weeks might not warrant keeping on-site.
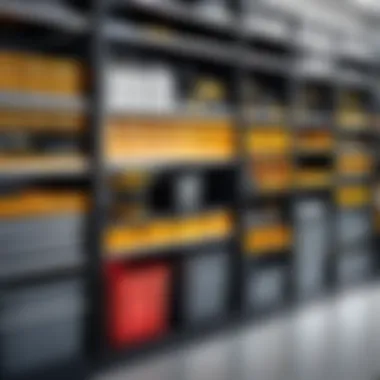

Doing this groundwork allows for a clearer picture of what’s working and what’s falling flat. This way, you demystify problem areas that need immediate attention, setting the stage for optimization work.
Setting Goals for Optimization
Once the current practices are assessed, it is time to set specific, actionable goals for optimizing the inventory systems. Without clear objectives, any efforts may feel like tossing spaghetti at the wall to see what sticks. Instead, establish concrete goals.
- Reduction in Costs: Aim for a clear number on how much you want to save annually by cutting tool losses or reducing downtime.
- Improved Utilization Rates: Tools should be used more efficiently. Think about how to maximize utilization rates. Remember, an underused tool is simply an expense waiting to happen.
- Enhanced Accountability: Establish accountability measures. This can include requiring sign-out sheets whenever a tool is borrowed, ensuring everyone knows what’s expected of them.
Setting these goals not only provides direction but also helps in measuring success down the line. As you implement changes, you can check back and see if those goals are being met, further refining the processes as needed.
"Effective inventory management is like a well-tuned engine: every component must work together seamlessly to drive performance and productivity."
By focusing on assessing current practices and setting solid goals, construction businesses lay a strong foundation for effective tool inventory management, ensuring that tools are where they should be when they are needed most.
Tools and Technologies for Inventory Management
Efficient tool inventory management relies heavily on the effective application of various tools and technologies. As the construction industry evolves, leveraging advancements in technology has become paramount for ensuring that tools are monitored, maintained, and accounted for in real-time. The integration of these technologies serves not just to streamline processes but also to enhance decision-making capabilities.
With the right systems in place, construction firms can minimize costs, reduce losses, and optimize resource allocation. Now, let’s delve into specific technologies that are reshaping how tools are managed in construction.
Inventory Management Software
When it comes to managing construction tools, software solutions play a key role. Specialized inventory management software is designed to provide a comprehensive overview of tool inventory, helping businesses track usage, maintenance schedules, and inventory levels with precision. For instance, systems like ToolWatch or EagleView allow for customized functionality based on the specific needs of the operation.
The benefits of inventory management software include:
- Real-Time Updates: Users can easily access and edit tool statuses, ensuring up-to-date information is always available.
- Data Analysis: Analytical tools embedded in the software help in identifying trends, allowing for data-driven decisions.
- User Collaboration: Multiple team members can access the platform, which enhances teamwork and accountability.
Incorporating such software not only automates mundane tasks but also provides a safety net against human error, which can be a costly mistake in the fast-paced construction environment.
Mobile Applications for Real-Time Tracking
The rise of mobile applications has transformed the way contractors and project managers keep track of tools and equipment. Utilizing mobile applications for inventory management allows for numerous advantages. Workers often have access to their tools precisely where their job takes them. A well-designed app can help users check out or return tools effectively.
Key features of mobile applications include:
- GPS Tracking: Knowing the exact location of each tool not only prevents loss but also aids in quickly relocating items on large job sites.
- Notifications and Alerts: Users can set reminders for tool maintenance, ensuring that equipment is always in its best condition.
- User-Friendly Interface: Most mobile apps are designed with a straightforward user experience, which reduces training time for employees—this is especially useful for workers who aren’t tech-savvy.
With real-time tracking at their fingertips, personnel can spend less time searching for tools and more time doing their jobs.
Barcode and RFID Technologies
Lastly, barcode and RFID technologies have brought an additional layer of efficiency in tool inventory management. Barcode systems simplify the tracking process as they allow for quick scanning, eliminating the need for extensive data entry. Similarly, RFID tags enable users to manage tools over larger areas without requiring a direct line of sight, thus providing a seamless tracking experience.
Benefits of utilizing these technologies include:
- Speed in Inventory Checks: A quick scan can allow teams to conduct audits in a fraction of the time that traditional methods would require, freeing up valuable labor hours.
- Reduced Errors: Automated scanning reduces the chances of human error, increasing the accuracy of inventory records.
- Durability: RFID tags are robust, which makes them suitable for the harsh environments often found on construction sites.
These technologies support dynamic construction environments by streamlining the tracking process, ensuring that tools are not just physically accounted for, but also systematically integrated into the inventory system.
"Adopting these technologies is crucial not only for tracking tools but also for ensuring that every dollar spent on equipment remains valuable and accounted for."
In closing, integrating advanced tools and technologies into your tool inventory management processes fundamentally alters the way construction operations are conducted. It clears the fog that often accompanies manual tracking and allocates more time to productive work. As tools and technologies continue to evolve, adapting to these changes is crucial for staying ahead in the competitive construction landscape.
Standardizing Tool Management Processes
Establishing a solid foundation for tool management is crucial in any construction enterprise. Standardizing tool management processes helps in reducing confusion, improving efficiency, and providing transparency. When everyone understands the procedures and expectations for tool handling, the likelihood of mistakes diminishes significantly. In this context, consistency in practices means that resources are not only accounted for but also easily accessible when needed.
Effective tool management standards encompass various elements, but the benefits tend to slice down to three main areas: operational efficiency, cost reduction, and enhanced accountability. In addition, using standardized protocols assists in training new employees, as they have a clear framework to follow from day one.
"Consistency breeds trust and reliability in any operation."
Creating a Tool Check-Out/Check-In Policy
A robust check-out/check-in policy is paramount. This policy serves as the backbone for monitoring tool usage across the board. Employees should clearly understand how to check out tools and how to check them back in after use. Such a structured approach helps minimize tool loss. The policy can include details about who is authorized to check out tools, how long tools can be borrowed, and the penalties for not returning them on time.
To create an effective policy, consider including the following:
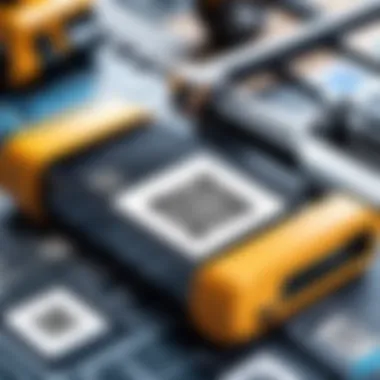
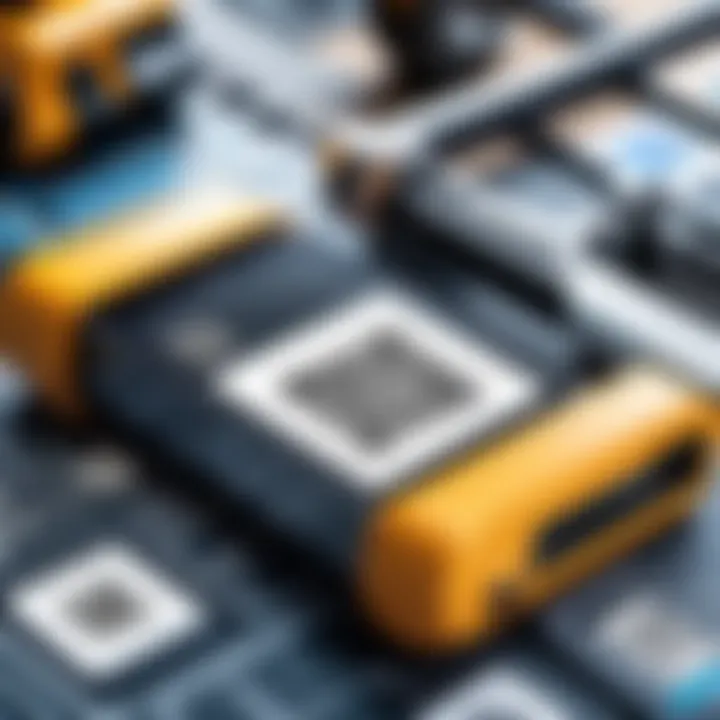
- Identification requirements: Employees could be required to present an ID before checking out tools.
- Time limits: Set a maximum borrowing duration to ensure tools are returned in a timely manner.
- Condition assessment: Require that tools be inspected for damage before and after use, creating a clear visual record.
Conducting Regular Audits
Audits play an essential role in maintaining the integrity of tool inventory management. Regular audits help keep track of current inventory levels and identify discrepancies between actual and reported tool counts. By implementing systematic audits—be they weekly, monthly, or quarterly—business can pinpoint not just losses but also overuse or under-utilization of tools.
Points to consider during audits include:
- Frequency: Determine how often audits should happen based on the size and usage of tools.
- Documentation: Use records during auditing to verify data, noting any missing or extra items.
- Involvement: Include personnel from varying departments in the audits for broader oversight and accountability.
Establishing a dedicated process for audits can go a long way in reassuring stakeholders that tools are being properly managed.
Implementing Preventive Maintenance Schedules
A preventive maintenance schedule is another key aspect of standardizing tool management. This program ensures that tools are regularly serviced, minimizing downtimes caused by mechanical failures. Failing to maintain tools can lead to increased costs over time as more significant repairs—and potentially replacements—might become necessary.
When formulating preventive maintenance schedules, keep these factors in mind:
- Usage frequency: Tools that see more action will require more frequent maintenance checks.
- Detailed log: Maintain records of maintenance performed, highlighting upcoming scheduled check-ups.
- Training staff: Ensure team members are trained to recognize the signs of tool malfunctions, prompting preventative measures quickly.
By incorporating these maintenance practices, businesses can greatly enhance the longevity of their tools, thus ensuring optimal performance throughout their lifespan.
Following these systematic processes in tool management, construction businesses can significantly improve expenses and operational workflow, allowing projects to finish on time and within budget.
Implementing these strategies helps businesses stay ahead in the industry, paving the way for smoother operations and thereby maximizing efficiency in tool management.
Training and Engaging Employees
When it comes to managing tool inventory in construction, the role of employees can’t be overlooked. They are the backbone of any operational strategy. Training and engaging employees in tool management ensures that everyone is on the same page, which is crucial for efficiency. If staff understand the importance of tools in their daily tasks and how to manage them properly, it can lead to fewer losses and better maintenance practices.
Importance of Employee Training Programs
An effective employee training program is an investment that pays dividends over time. By providing thorough training, companies equip their workers with the knowledge they need to take care of tools and equipment. This training should cover several areas:
- Basic Tool Usage: Understanding how to use tools correctly reduces wear and tear, hence lowering replacement costs.
- Inventory Systems: Familiarizing employees with whatever inventory management software is in place allows for smoother operations.
- Maintenance Protocols: Training on regular maintenance ensures tools are kept in optimal conditions, ultimately improving productivity.
Moreover, when employees are well-trained, they tend to feel more empowered and confident in their work. This leads to reduced accidents and better accountability. However, it’s important that training is not a one-and-done affair. Regular refresher courses should be scheduled to keep everyone updated on best practices and any new tools.
Fostering a Culture of Responsibility
Creating a culture of responsibility within the workforce makes a significant impact on how tools are managed. When employees feel accountable for the tools they use, they are more likely to handle them with care. Here are some strategies to foster this culture:
- Clear Expectations: Communicate the importance of tool management within the organization. Ensure that employees understand their obligations related to tool care and access.
- Incentives: Consider implementing incentive programs that reward employees who demonstrate exceptional care for tools. Recognition can be a powerful motivator.
- Open Communication: Encourage employees to voice any concerns regarding tools or inventory processes. A system where feedback is valued leads to improvements in how tools are managed.
Ultimately, employees should perceive themselves as guardians of equipment that significantly contributes to their work. Engaged employees who take responsibility for their tools will not only enhance the overall efficiency of operations but also reduce costs related to loss and damage. This proactive approach can transform inventory management from a mundane routine into an integral part of fostering workplace success.
"An engaged workforce is the secret sauce to reducing costs and improving tool management."
By focusing on training and fostering a responsible culture, companies can pave the way for an efficient and effective tool inventory management system, aligning everyone in achieving organizational goals.
Evaluating the Effectiveness of Inventory Management
Assessing how well an inventory management system operates is vital for construction businesses aiming to keep their projects on track and budgets in check. This evaluation goes beyond simply counting tools; it’s about understanding how effectively these tools are used, how often they're serviced, and how much they cost the company in terms of both time and money. An effective tool inventory management system enables construction firms to refine their processes, eliminating waste and minimizing delays.
By measuring performance, businesses can better align their inventory management practices with their operational goals. Key areas of focus include:
- Resource Optimization: Are you making the most of the tools and equipment at your disposal? Evaluating usage can pinpoint underutilized assets, leading to better allocation and ultimately cost savings.
- Cost Management: By analyzing expenditures related to tool maintenance, loss, or replacement, it's possible to identify patterns that may suggest better procurement processes.
- Operational Efficiency: Regularly evaluation helps to identify bottlenecks in workflows that stem from inadequate tool availability. This leads to prompt action in addressing these delays.
"Evaluating the effectiveness of an inventory system is like checking the pulse of your operations. Without this, you might be just a step away from a serious inefficiency."
In the rapidly changing landscape of construction, staying ahead requires constant monitoring and adjustment. The need for proactive assessment has never been more apparent.
Key Performance Indicators (KPIs)
Key Performance Indicators serve as the backbone of assessing tool inventory management effectiveness. When you look into how well your inventory management is doing, these KPIs can give you the numbers you need. Here are some noteworthy KPIs tied directly to inventory management:
- Inventory Turnover Ratio: This indicates how often inventory is sold and replaced over a specific period. A higher ratio suggests effective inventory management.
- Average Tool Cost: Monitoring this number over time can help highlight any unexpected expenditures due to damages or replacements.
- Tool Utilization Rate: Perhaps one of the most telling KPIs; this signifies how frequently tools are used compared to their availability. If tools sit idle while projects are delayed, it speaks volumes.
- Maintenance Frequency: Tracking this metric can reveal if your preventive or corrective measure is effective in reducing downtime and prolonging tool life.
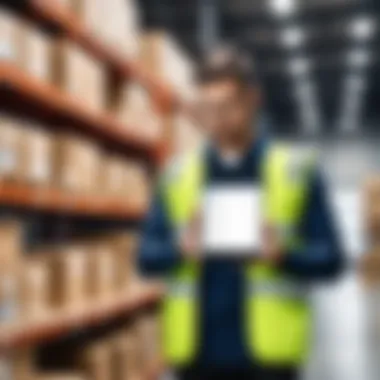
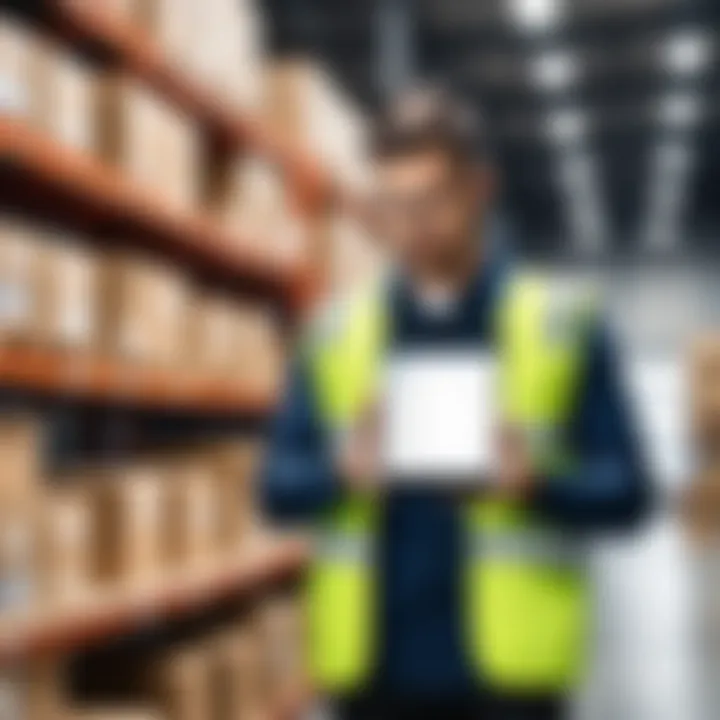
Establishing clear and measurable KPIs ensures that teams are not only grounded in solid data but are also able to pivot to more effective strategies based on those insights.
Feedback Mechanisms for Continuous Improvement
A strong feedback loop is crucial for ongoing success in tool inventory management. Listening to employees who work directly with the equipment can unearth concerns and suggestions that might otherwise fly under the radar.
Establishing a system where workers can provide input on inventory issues can yield various advantages:
- Identifying Pain Points: Workers may notice inefficiencies or problematic tools that aren’t as visible to managers. Frequent feedback allows for quick adaptations.
- Encouraging Ownership: When employees feel their voices matter, they’re more likely to take care of tools and maintain inventory correctly, fostering a sense of responsibility.
- Iterative Improvement: Feedback mechanisms create pathways for continuous improvement. Whether it’s through regular surveys, informal discussions, or dedicated feedback sessions, gathering insights helps drive better decision-making.
Incorporating these feedback avenues can't be neglected. They ensure that the inventory system remains agile and responsive, keeping pace with changing project requirements and workforce capabilities.
Case Studies in Effective Tool Management
Understanding how different entities tackle the challenges of tool inventory management provides invaluable insights for other businesses. Whether it’s through innovative approaches or simply refining existing processes, the lessons gleaned from diverse organizations can help streamline operations and bolster productivity. The case studies showcase both small businesses and large-scale operations, each embodying unique strategies while operating within the same goal of effective tool management.
Examining specific examples in effective tool management allows stakeholders to critically analyze what worked, what didn’t, and why. The benefits of leveraging these case studies include the chance to:
- Innovate based on proven practices
- Avoid common pitfalls encountered by others
- Adapt successful strategies to fit different operational scales
The insights from these case studies carry weight because they reflect real-world solutions, grounded and boosted by tangible outcomes.
"Success leaves clues. The best way to foresee your future is to understand the past."
Small Business Innovations
In the realm of small businesses, innovation often arises out of necessity due to limited resources. One artfully crafted example is a local landscaping company that grappled with tool loss every season. This company developed an in-house tracking system that relied on simple spreadsheets combined with a checklist-style checkout process.
They encouraged each employee to sign off on tool usage before heading out to a job. To add a layer of accountability, they incorporated brief training sessions highlighting the cost of tools and the importance of returning them. In doing so, this company not only cut down tool loss by an impressive 40% within a year, but also fostered a culture of personal investment in company resources.
Key components of this innovative approach include:
- Direct employee involvement: Employees felt empowered, knowing their actions directly impacted operational efficiency.
- Cost awareness training: By bridging the gap between employees and the cost of tools, this strategy cultivated respect for company property.
- Simplicity and accessibility: The use of readily available tools like spreadsheets minimized barriers to effective management.
Larger Scale Operations and Their Strategies
On the opposite end of the spectrum, larger operations can afford more elaborate strategies, often employing sophisticated technology to track and manage tools. Take, for instance, a national construction firm that dealt with multiple job sites and mountains of inventory. This firm introduced a robust inventory management software that integrated with RFID technology for real-time tracking of tools.
This approach afforded them several advantages:
- Scalability: As the firm expanded, the system effortlessly adapted to increasing tools and requirements.
- Real-time data access: Being able to see which tools are in use at any moment allowed for swift reallocations and minimized downtime.
- Enhanced analytics: The software provided insights and trends over time, guiding future purchases, tool usage training, and preventive maintenance schedules.
Among the challenges faced, the firm had to overcome initial resistance from employees wary of new technology. By incorporating thorough training sessions that highlighted the advantages of the new system, employee buy-in soared.
Lessons learned from both small and large operations affirm that effective tool management, whether through innovation or technology, hinges on creating an engaging culture of accountability and responsibility.
Future Trends in Tool Inventory Management
In the ever-evolving landscape of construction, keeping pace with technological advancements and societal shifts is crucial for optimal management of tool inventories. Recognizing the significance of future trends in tool inventory management not only marks a path forward but also highlights opportunities to streamline operations and enhance efficiency. Decision-makers and professionals at all levels will find that understanding these trends equips them better to tackle upcoming challenges while maximizing resource utilization.
Adoption of AI and Automation
Artificial Intelligence is rapidly transforming various sectors, and tool inventory management is no exception. By incorporating AI-driven solutions, businesses can foresee potential inefficiencies and counteract them proactively. For instance, AI can analyze usage patterns to predict when tools need maintenance or when to replace them, mitigating downtime and prolonging asset life.
Automated systems can also streamline the check-out and check-in processes for tools, minimizing human error and improving overall accountability. With AI's predictive capabilities, companies can optimize their stock levels, ensuring that tools are available when needed without over-purchasing.
The benefits of adopting AI and automation are manifold:
- Efficiency Gains: Automated data entry reduces labor costs and the chance for mistakes.
- Real-time Tracking: Monitor tools' locations and conditions to keep everything in check.
- Data-Driven Insights: Elevate decision-making by relying on solid analytics instead of gut feelings.
"AI and automation are not just trends; they are the backbone of tomorrow's competitive advantage in tool inventory management."
Sustainability and Eco-Friendly Practices
Sustainability is no longer merely a buzzword; it’s becoming a foundational aspect of business practice. An eco-friendly approach to tool inventory management encompasses not just the tools themselves, but the methodologies employed in their acquisition and maintenance. Companies are increasingly seeking ways to lessen their environmental impact, whether through sustainable purchasing practices or proper disposal methods.
Eco-friendly practices can lead to several substantial advantages:
- Cost Savings: Sustainable tools often consume less energy, leading to lower operational costs over time.
- Brand Image: Companies adopting green practices develop a reputation as environmentally conscious, attracting like-minded clients and partners.
- Regulatory Compliance: With growing environmental regulations, staying ahead of the curve can help companies avoid penalties and fines.
Integrating such practices into inventory management might involve:
- Selecting Energy-Efficient Tools: Prioritize sourcing tools that use less power.
- Implementing Recycling Programs: Establish processes for recycling older or unused tools instead of discarding them.
- Training Staff on Green Practices: Ensure that all employees are familiar with the company's sustainability goals and how to achieve them through responsible tool management.
As this trend becomes woven into the fabric of operational strategies, tools not only serve their primary functions but also contribute positively to the planet, aligning with broader societal shifts towards responsibility and stewardship.