Streamlining Construction Inventory Management Software
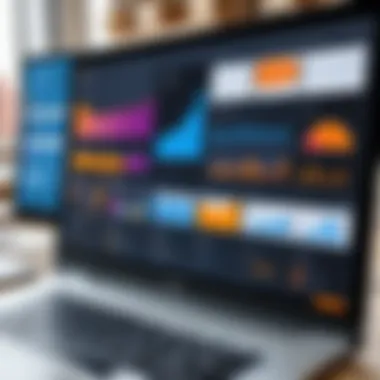
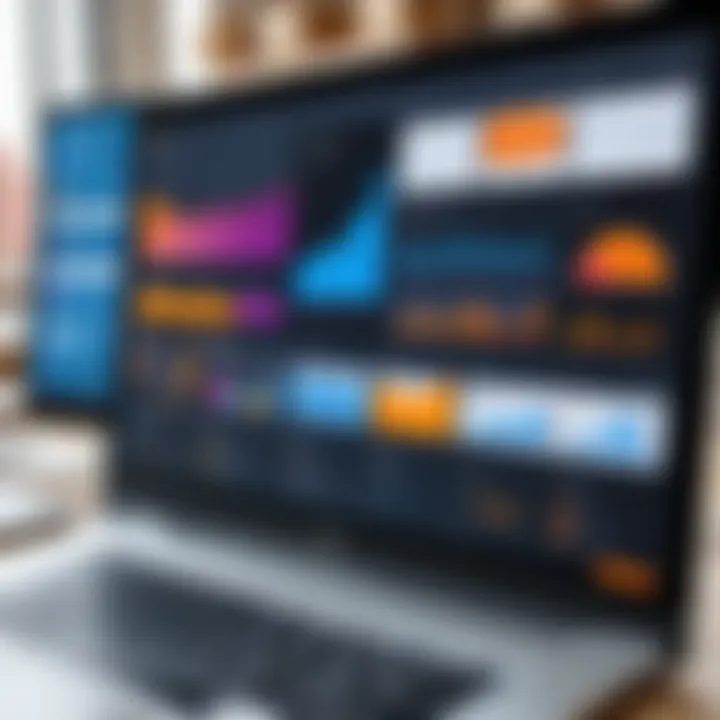
Intro
In the construction industry, managing inventory effectively is vital for operational success. Construction projects often involve numerous materials and equipment that need careful tracking. Without an efficient system in place, companies face challenges like excess costs, project delays, and suboptimal resource allocation. Inventory management software offers a strategic solution to these problems, providing tools that streamline processes and enhance productivity.
This software is specifically designed for the unique requirements of the construction sector. It caters to complexities such as fluctuating supply needs, diverse material types, and the necessity of maintaining accurate records for budgeting and accounting. Through this comprehensive overview, we will examine the primary features, benefits, and best practices associated with inventory management software tailored for the construction industry. By doing so, we aim to equip decision-makers with the insights needed to enhance their operational efficiency and ultimately, profitability.
Key Software Features
Essential functionalities
Effective inventory management software shares several essential functionalities that cater specifically to the needs of construction companies. These features often include:
- Real-time tracking of materials and equipment, ensuring users know what is available and what needs to be ordered.
- Automated stock alerts that notify teams when inventory levels are low, which helps prevent project delays due to material shortages.
- Barcode scanning capabilities for faster and more accurate data entry, reducing human error and enhancing accuracy.
- Integration with other construction software, such as project management and accounting tools, facilitates smooth data exchange across different functions.
- Reporting and analytics tools that provide insights on usage patterns, helping managers make informed decisions on future orders and budgets.
Advanced capabilities
Beyond the core features, many software solutions offer advanced capabilities that can significantly enhance a construction company's inventory management. These may include:
- Mobile access, allowing teams to track inventory on-site through smartphones and tablets, improving responsiveness.
- Forecasting tools that help predict future inventory needs based on project timelines and historical data.
- Vendor management features that improve communication with suppliers, streamlining the procurement process.
- Multi-location support, crucial for firms managing several projects in different locations with varying inventory needs.
Comparison Metrics
When evaluating different inventory management software, it is essential to use specific metrics to guide your decision. Here are critical considerations:
Cost analysis
Understanding the total cost of ownership is crucial. Look beyond initial purchase price. Consider:
- Subscription fees or one-time payment costs
- Implementation costs, including training and onboarding
- Ongoing maintenance and support fees
- Potential savings from improved efficiency
Performance benchmarks
To assess the value of software, performance benchmarks can provide essential insights. Key metrics might include:
- System uptime and reliability, affecting access to crucial data
- Speed of inventory updates, which impacts decision-making
- User satisfaction ratings to evaluate interface usability
- Return on investment realized from implementing the software
Investing in the right inventory management software can lead to significant improvements in both operational efficiency and bottom-line profitability for construction firms.
Prelude to Inventory Management in Construction
Inventory management is a critical component of the construction industry. It involves overseeing and controlling the ordering, storage, and use of materials. Effective inventory management ensures that the right materials are available at the right time, reducing delays and minimizing costs.
In the construction sector, where projects are often complex and timelines tight, the significance of inventory management cannot be overstated. It directly impacts the smooth execution of construction projects. A well-implemented inventory management system can lead to improved productivity and enhanced operational efficiency.
Key Elements of Inventory Management
Inventory management in construction includes various elements such as tracking usage, managing stock levels, and ensuring materials are delivered when needed. Accurate tracking helps project managers avoid over-ordering or under-ordering, which can disrupt workflows.
Moreover, it allows for optimal utilization of resources, reducing waste and ensuring that projects stay within budget. The benefits of a robust inventory management system include:
- Cost Savings: Reducing excess inventory can lead to significant cost savings.
- Time Efficiency: Streamlined processes save time during material procurement.
- Risk Mitigation: Minimizing the risk of project delays due to material shortages or mismanagement.
Considerations for Implementing Inventory Management
When considering the implementation of an inventory management software, construction firms must assess their specific needs. This includes evaluating the scalability of the software, integration capabilities with current tools, and the accessibility of real-time data. Training employees on the new system is also crucial to ensure its effectiveness.
To summarize, understanding the importance of inventory management in construction is essential for decision-makers. It is not merely an operational function, but a strategic element that influences overall project success.
Importance of Inventory Management in Construction Projects
Inventory management is crucial in construction projects. It impacts the efficiency and productivity of construction operations significantly. This importance is rooted in several key areas that drive project success.
First, managing inventory effectively ensures timely availability of materials. Construction projects rely on a variety of materials, from concrete to steel. Delays in material delivery can halt progress, leading to increased costs and ultimately affecting project timelines. By tracking inventory levels in real-time, project managers can anticipate needs and order supplies ahead of time, mitigating risks of delays.
Second, efficient inventory management also supports cost control. By maintaining an accurate inventory, companies can prevent over-ordering or stockouts. Over-ordering leads to excess materials that consume storage space and can lead to waste, while stockouts may require emergency orders that often come at a premium. This balance directly influences the project's bottom line.
Another aspect of significance is resource allocation. Construction projects are often complex, with many moving parts. A centralized inventory management system allows decision-makers to track which materials are available where. This knowledge enables smarter allocation of resources across different sites, improving overall operational efficiency.
Moreover, effective inventory management contributes to better financial planning. Accurate tracking of materials and their costs helps project managers to develop more precise budgets. Thus, stakeholders can make informed decisions about future projects.
Additionally, maintaining a consistent inventory system supports safety and compliance. Many regions have regulations governing the use of specific materials in construction. Keeping track of inventory ensures that all materials used comply with industry standards and safety regulations.
"An effective inventory management system is not just about materials. It’s about driving efficiencies and ensuring that projects run smoothly and profitably."
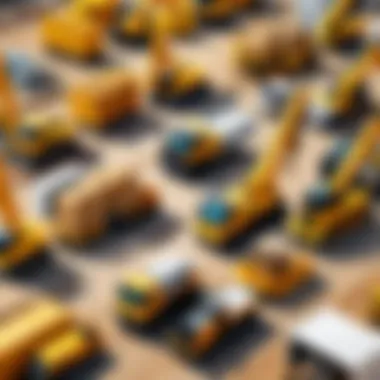
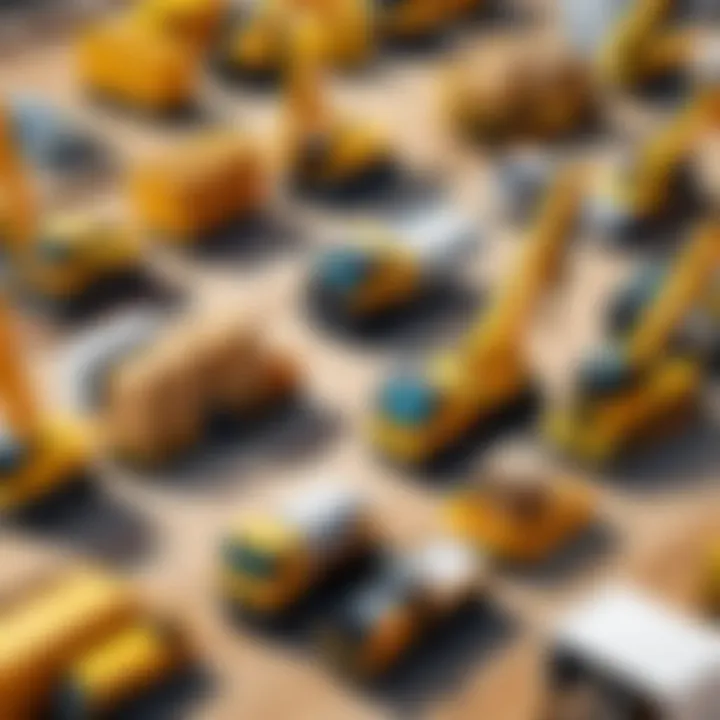
Incorporating robust inventory management practices leads to operational excellence, setting the stage for successful project completion.
Challenges of Inventory Management in the Construction Sector
Efficient inventory management is a cornerstone of success in the construction industry. However, it is also fraught with obstacles that businesses must navigate. Understanding these challenges can help construction firms develop strategies to mitigate risks, enhance inventory accuracy, and ultimately improve project outcomes.
The complexity of construction projects often means that inventory needs fluctuate significantly. This is exacerbated by external factors such as market demand, supplier reliability, and economic conditions. When construction companies cannot adapt to these dynamic elements, inefficiencies arise, leading to increased costs and delays. Therefore, addressing these difficulties is not just beneficial, but essential for the sustainability of operations.
Fluctuating Demand and Supply Chain Issues
In the construction sector, demand for materials can be highly volatile. Projects are influenced by seasonality, client preferences, and changing regulations. This volatility poses a unique challenge for inventory management teams. For example, an unexpected surge in demand for concrete may deplete supplies faster than anticipated, causing delays and frustrating project schedules.
Moreover, supply chain disruptions can lead to further complications. Factors such as transportation delays, natural disasters, or geopolitical issues can impact the availability of necessary materials. Given that construction often operates on tight deadlines, any disruption can be costly. Companies must therefore implement robust forecasting methods and maintain flexible supply chain relationships to respond effectively to these changes.
Site-Specific Inventory Needs
Every construction site has its own unique requirements, influenced by project size, location, and type of work. This specificity necessitates a tailored approach to inventory management. For instance, a residential construction project may require different materials than a commercial one, and the location can influence delivery times and logistics.
Maintaining an accurate inventory at multiple sites can become burdensome. Companies must strike a balance between having sufficient stock to avoid delays and preventing excess inventory, which ties up capital. Utilizing technology such as mobile inventory tracking can help site managers stay aware of stock levels and site-specific needs, allowing for better allocation and usage of resources.
Regulatory Compliance and Reporting
In recent years, the construction industry has faced increasing scrutiny regarding compliance with regulations. Governments impose strict guidelines on safety, environmental impact, and material standards. Failing to comply can lead to fines, project shutdowns, and reputational damage.
Proper inventory management plays a critical role in meeting these regulatory demands. Businesses must maintain accurate records of materials used, their sources, and their compliance with safety standards. Furthermore, reporting requirements are often complex, necessitating a systematic approach to documentation. This is where specialized software can become an asset. Automated systems can facilitate compliance by tracking inventories and generating reports that adhere to regulatory standards, enabling companies to focus on their core operations instead of administrative tasks.
"The construction industry faces unique challenges that directly impact inventory management. By understanding these issues, businesses can take proactive steps towards improving their processes."
In summary, the challenges faced in inventory management within the construction industry are significant and multifaceted. Addressing fluctuating demands, site-specific needs, and regulatory compliance is essential for operational efficiency and project effectiveness. Technologies that streamline these processes can provide a competitive edge to construction firms.
Key Features of Inventory Management Software
In the construction industry, selecting the right inventory management software is essential for efficient operations. This section will explore the key features that enhance inventory management practices. Each feature contributes distinctly towards solving challenges such as material wastage, project delays, and budget overruns. Understanding these features can help decision-makers choose the appropriate software that aligns with their operational needs.
Real-Time Inventory Tracking
The capability for real-time inventory tracking stands out as one of the most critical features of any inventory management software. In the construction sector, where timelines and budgets are often tight, having an up-to-the-minute view of inventory status is invaluable. This feature allows project managers to see current stock levels, reducing the risk of running out of essential materials or incurring excess costs from over-ordering.
With real-time tracking, any discrepancies between expected and actual inventory levels can be addressed swiftly. This helps in identifying potential theft or loss on site immediately, allowing for rapid response. Additionally, improved visibility into inventory movement enhances coordination between teams, as they can manage resources more effectively.
Data collected through real-time tracking can also feed into broader analytics, supporting long-term planning and purchasing decisions.
Integrated Supply Chain Management
An integrated approach to supply chain management is crucial for construction projects. Inventory management software that incorporates this feature facilitates better relationships with suppliers and subcontractors. Effective integration reduces delays in acquiring materials, ensuring that project timelines remain intact and reducing the chances of work stoppages.
The software should allow for seamless communication between all stakeholders, updating everyone involved about inventory levels and the status of orders. This minimizes misunderstandings and reinforces accountability. Moreover, some systems can automate reordering processes when stock levels fall below a predetermined threshold, which ensures that essential items are always available without manual intervention.
Overall, integrated supply chain management optimizes logistics, streamlines project workflow, and improves supplier collaboration, ultimately benefiting the bottom line.
Automated Reporting and Analytics
The provision for automated reporting and analytics is another essential feature that enhances inventory management in construction. Automated reports can provide insights into inventory usage patterns, helping decision-makers understand how materials are consumed across different projects. This understanding promotes more accurate forecasting and budget allocation.
Through analytics, it becomes easier to identify trends in supply costs, which can inform negotiations with suppliers or lead to strategic adjustments in purchasing decisions. Additionally, automated reporting saves time typically spent on manual data entry and analysis, which can be redirected towards more value-generating activities.
In essence, this feature supports strategic planning and risk management, allowing construction firms to base decisions on reliable data rather than guesses.
Key Insight: The integration of real-time tracking, supply chain management, and automated reporting creates a robust foundation for effective inventory control in construction.
By focusing on these key features, construction companies can enhance their inventory management processes significantly, leading to improved project outcomes and operational efficiency.
Top Inventory Management Software for Construction
In the construction sector, effective inventory management is key to maintaining operations. Having the right software can significantly enhance efficiency, minimize waste, and provide real-time insights. Construction projects often involve large numbers of materials that must be tracked at various sites. Hence, a robust inventory management software is vital. This ensures all stakeholders can access accurate data anytime, supporting informed decision-making and seamless operations.
Software A: Overview and Features
Software A is tailored for the construction industry, offering flexible solutions that cater to varying project needs. It features real-time inventory tracking, which allows project managers to monitor stock levels as materials are consumed. This functionality prevents over-ordering and stockouts. The software also includes a user-friendly dashboard that provides insights into current inventory status, enabling quick assessments.
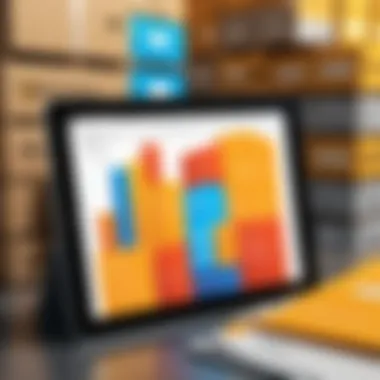
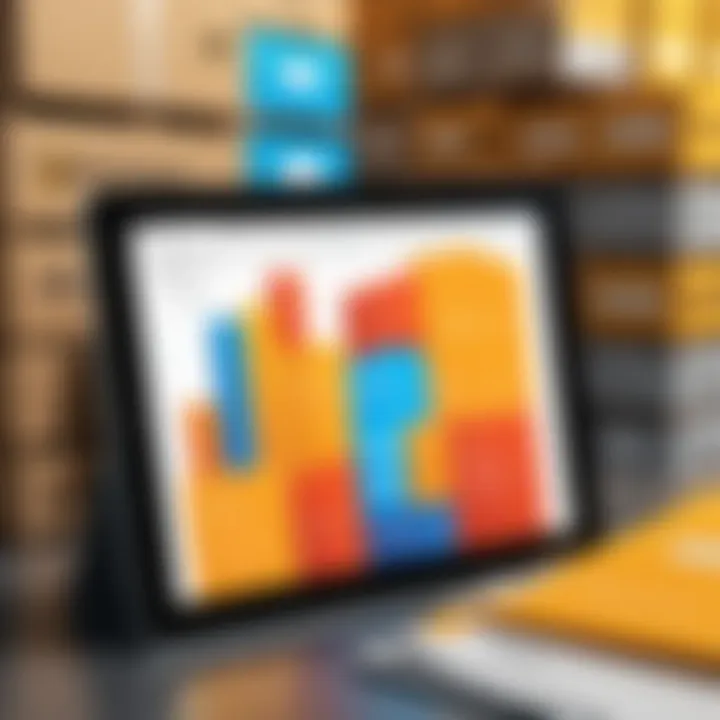
Moreover, it integrates with major suppliers for efficient restocking. The automated alerts about low stock levels further enhance management’s ability to maintain supply without interruptions. Compliance tracking is another essential feature, ensuring that inventory meets industry regulations at all times.
Software B: Overview and Features
Software B takes simplicity and efficiency to the next level. Designed with a focus on mobile accessibility, it allows field teams to update inventory data directly from job sites. This feature helps in maintaining accurate records without delays, minimizing errors associated with data entry.
In addition, it offers comprehensive reporting tools. Construction managers can generate reports that summarize inventory usage over specific periods. This information aids in analyzing trends and planning for future projects. Software B also ensures compatibility with other playforms, allowing for streamlined operations across different facets of construction management.
Software C: Overview and Features
Software C stands out with its advanced analytical tools. This software collects data on usage patterns and predicts future inventory needs based on historical data. Such predictive analytics enable construction firms to prepare for fluctuations in demand, leading to more strategic procurement practices.
In terms of features, Software C includes cloud-based storage that enhances accessibility from any location. This is particularly beneficial for remote construction sites where traditional access may be limited. Additionally, it offers multi-site inventory management, allowing companies operating in multiple locations to coordinate materials effectively across all sites.
By leveraging the right tools, decision-makers in the construction industry can transform inventory management into a strategic asset.
Overall, selecting the appropriate inventory management software depends on understanding project needs, company size, and integration capabilities. An informed choice will ultimately lead to enhanced operational efficiency and profitability.
Evaluating Inventory Management Software Options
In the construction industry, choosing the right inventory management software is critical. Effective evaluation can greatly enhance operational efficiency, reduce costs, and improve project timelines. When assessing software options, it is vital to focus on specific elements that fit the unique requirements of construction businesses. This process involves various aspects, from understanding the software's features to considering the costs associated with it.
A well-chosen inventory management system can streamline operations, minimize waste, and aid in compliance with regulatory requirements. Each construction project has its own complexities, and the right software can help navigate these challenges while maximizing resource utilization.
Key Selection Criteria
When evaluating inventory management software, it is essential to consider certain selection criteria. These criteria ensure that the chosen software aligns with the operational needs of the construction firm. Here are some important factors to focus on:
- Usability: The software should have an intuitive interface for easy adoption by users. A steep learning curve can lead to inefficiencies and resistance within workflows.
- Integration Capabilities: The software should seamlessly integrate with existing systems, such as accounting or project management tools. This allows for better data flow and reduces duplicated efforts.
- Scalability: Evaluate whether the software can grow with your business. Future needs may require additional functionalities or expanded user access.
- Customization Options: Look for software that allows customization to tailor it to specific project requirements and company processes.
- Security Features: Protecting sensitive data is vital. Ensure the software has robust security protocols to safeguard information.
These criteria serve as a foundation for making informed decisions about inventory management software options.
Cost Considerations
Cost is a significant factor when evaluating inventory management software. It is important to understand both the initial investment and the long-term expenses that may arise. Costs are not only limited to the software pricing but also include factors such as:
- Subscription Fees: Monthly or annual fees can vary greatly between software products. Assess the pricing model that best fits your budget.
- Training Costs: Consider any expenses associated with training staff on how to use the new software.
- Implementation Expenses: Include costs related to installing and integrating the software with existing systems.
- Maintenance and Support: Ongoing support may come at an additional cost. Ensure that this is factored into your evaluation.
- Potential ROI: While costs are important, it is equally critical to evaluate the potential return on investment. Look at how the software can improve productivity, reduce waste, and lead to savings in the long run.
Assessing these cost considerations alongside the selection criteria provides a more comprehensive view. This approach helps in choosing the right inventory management software that meets both operational needs and financial constraints.
Best Practices for Inventory Management in Construction
Effective inventory management is crucial for construction businesses aiming to minimize waste, reduce costs, and enhance overall productivity. By implementing best practices, companies can create a seamless workflow, ensuring that materials are available when needed without overstocking or running into shortages. This not only streamlines operations but also supports project timelines and budgets, critical factors in the construction sector.
Implementing best practices involves several strategic elements. Companies must establish clear processes for tracking inventory levels and managing the replenishment of materials. This includes defining roles and responsibilities, ensuring that team members understand their part in the inventory management cycle. Moreover, it is vital to integrate inventory management systems with other operational systems to allow for better data visibility.
Regular Audits and Replenishment Strategies
Regular audits are essential in inventory management as they help to reconcile physical stock with digital records. Audits can uncover discrepancies, prevent theft, and ensure that all materials on-site are accounted for. This process should be conducted periodically, depending on the size and scope of the project.
To complement audits, effective replenishment strategies must be developed. This means setting guidelines for reorder points and lead times. Identifying these factors prevents sudden shortages and keeps the project on track.
Key practices for regular audits and replenishment include:
- Establish a schedule for audits: Determine how often audits should take place. Depending on the volume of materials used, monthly or quarterly audits might be necessary.
- Utilize technology: Leverage mobile solutions or inventory management software that provides real-time updates and alerts for low stock levels.
- Train staff: Ensure that all relevant employees know how and when to conduct audits. They should also understand the importance of accurate reporting.
"Prior planning and consistent auditing can result in major efficiencies, leading to significant cost savings over time."
- Document findings: Create a systematic approach for documenting audit results to track trends and address recurring issues.
Utilizing Data and Analytics for Optimization
The use of data and analytics in inventory management leads to insightful decision-making. By analyzing historical data on material usage, companies can forecast demand more accurately and optimize their inventory levels accordingly. This proactive approach reduces waste and enhances operational efficiency.
Data analytics enables construction firms to:
- Identify patterns: Understanding usage trends allows for better planning, which leads to timely replenishments and reduced hold times for materials.
- Enhance supplier relationships: Analytics can reveal which suppliers have the best performance, leading to more strategic partnerships and negotiations.
- Improve project planning: By evaluating current and past project needs through data, firms can allocate resources more effectively for future projects.
A few strategies to leverage data analytics include:
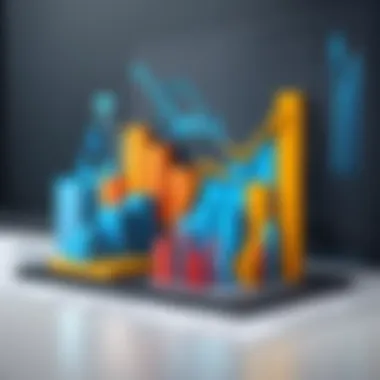
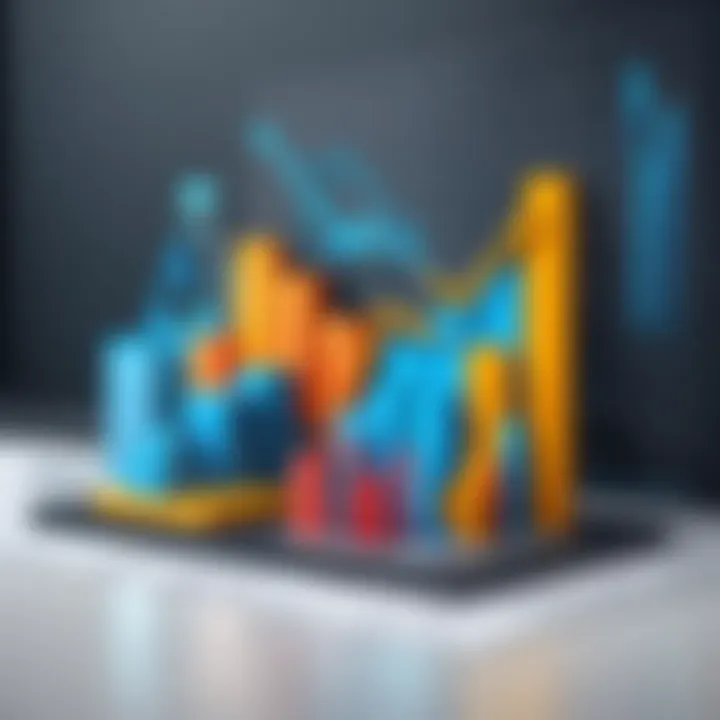
- Invest in analytics tools: Utilize software that offers robust analytical features to convert raw data into actionable insights.
- Collaborate Across Teams: Ensure all relevant departments have access to this data. Sales, procurement, and project management can benefit from shared insights.
- Establish KPIs: Define key performance indicators relevant to inventory management and consistently monitor them for ongoing improvement.
By following these best practices, construction companies can drastically improve their inventory management processes. This leads to more efficient operations, cost savings, and the successful delivery of projects.
The Role of Technology in Enhancing Inventory Management
In the construction industry, effective inventory management is crucial for maintaining project timelines and optimizing resource allocation. The implementation of technology is increasingly becoming a linchpin in achieving these objectives. Technology facilitates not only the tracking of materials but also enhances communication between stakeholders. Integrating various technological solutions can significantly reduce costs and improve efficiency.
Mobile Solutions for Construction Sites
Mobile solutions represent an evolution in inventory management. With construction sites often being on the move, having inventory management at one’s fingertips is invaluable. Mobile applications allow for real-time updates on stock levels, helping project managers make informed decisions quickly.
Moreover, these applications can streamline ordering processes. Workers can check availability or order supplies from any location. This reduces the downtime associated with searching for materials or waiting for deliveries. Most mobile solutions enable barcode scanning, which automates data entry, reduces human error, and speeds up the inventory process.
Key benefits of mobile solutions include:
- Accessibility: Users can access information from anywhere using smartphones or tablets.
- Efficiency: Immediate data updates reduce the chance of stock discrepancies.
- User-Friendly: Most mobile apps are designed for ease of use, minimizing training time for staff.
Integration with Other Management Systems
Integration with other management systems is another critical aspect enhancing inventory management. For construction firms, combining inventory management software with project management tools, accounting software, and supply chain applications is essential for holistic oversight.
When these systems are interconnected, data synchronization occurs. This means that when a material is used on-site, all related systems are automatically updated. Financial implications are also affected; invoices and expenses related to materials can be automatically tracked, leading to better cash flow management.
Furthermore, integrating systems enables:
- Improved Decision-Making: Access to combined data provides a clearer overview of operations.
- Reduced Manual Work: Decreases the need for repetitive data entry across various platforms.
- Enhanced Communication: Different departments can share relevant information seamlessly, leading to coordinated efforts across projects.
"Incorporating technology into inventory management is not merely an option anymore; it's an imperative to stay competitive in the construction industry."
The integration of advanced technologies, such as artificial intelligence and predictive analytics, can further optimize these processes. By analyzing trends and usage patterns, firms can forecast inventory needs with more accuracy. This reduces overstocking or stockouts, which are common pitfalls.
Future Trends in Inventory Management Software
The landscape of inventory management software within the construction industry is evolving rapidly. Change agents like technology and environmental concerns demand that construction firms adapt. Recognizing these trends is vital, as they highlight innovative opportunities to enhance efficiency, reduce costs, and maintain a competitive edge. Understanding future trends allows decision-makers to prepare their organizations for upcoming shifts. It encourages investment in relevant technologies, informing strategic moves that ensure sustainability and effectiveness in inventory management.
Artificial Intelligence and Automation
As we step into an era dominated by data, the incorporation of artificial intelligence (AI) and automation in inventory management software rises in prominence. AI algorithms analyze consumption patterns and predict future needs, which helps in decision-making. This predictive capability allows businesses to maintain optimal inventory levels, minimizing both excess and shortage. Automated ordering systems can track material levels and automatically place orders when thresholds are reached, reducing manual errors and saving time.
Additionally, machine learning models can learn from historical data. They can adjust forecasts based on various influencing factors such as project size, supplier lead times, or even local market trends. These insighs prepare firms to respond proactively to dynamic project requirements.
Overall, adopting AI and automation facilitates increased operational efficiency and enables resources to be allocated more strategically.
Sustainability and Eco-Friendly Solutions
The construction industry faces increasing scrutiny over its environmental impact. As a result, there is a growing demand for sustainability-focused inventory management solutions. Software that incorporates features promoting eco-friendliness can lead to more responsible usage of materials. Efficient inventory control reduces waste, aligning with organizational goals for greener practices.
Some inventory management platforms now include tools for assessing the sustainability of suppliers. Companies can evaluate vendor practices based on their environmental policies. This move empowers construction firms to select suppliers that prioritize sustainability, further enabling a circular economy approach in project execution.
Moreover, tracking energy consumption and material sourcing helps organizations reduce their carbon Footprint. Utilizing eco-friendly materials not only satisfies regulatory requirements but also enhances a company's reputation. The trend towards sustainability in inventory management is not just ethical; it also comes with potential cost savings and improved brand loyalty.
"Companies that incorporate sustainable practices are likely to see improved operational efficiency in the long run."
Ultimately, recognizing and adapting to these future trends lays the groundwork for savvy investment in technology. The construction sector stands to gain significantly by embracing innovation and sustainability, shaping the future of inventory management in the industry.
The End: Strategic Importance of Effective Inventory Management
Effective inventory management is crucial in the construction industry. Construction projects are often complex and involve numerous materials and equipment. Thus, maintaining a streamlined inventory system influences the project outcome significantly. When effective practices are applied, there are notable benefits.
Enhancing Operational Efficiency
Having the right materials at the right time reduces downtime. Delays due to lack of supplies can inflate costs and disrupt schedules. Efficient inventory management facilitates smooth logistics, ensuring resources are readily available when needed.
Cost Savings
By optimizing inventory levels, construction companies can reduce excess stock and avoid unnecessary purchases. This directly affects the bottom line by minimizing waste and enhancing profitability.
Improved Accuracy in Reporting
Using specialized inventory management software allows for better data collection and analysis. Accurate inventory counts lead to reliable project forecasts and more effective budgeting. When stakeholders have visibility into inventory status, decision-making becomes easier and more informed.
Considerations for Implementation
Investing in inventory management software must be approached thoughtfully. Companies should consider the following:
- Customization Needs: Different businesses have varied requirements. Selecting a solution that can adapt to unique processes is essential.
- Training: Staff must be trained to use the new software effectively. Without adequate training, the potential of the system may not be fully realized.
- Integration Capabilities: The software should integrate seamlessly with other systems in use, such as project management tools.
As the construction industry evolves, the focus on inventory management will only become more pronounced. Adopting strategic inventory management practices supports long-term success in construction projects. Therefore, decision-makers should prioritize evaluating and investing in the right software for their needs.
"A well-managed inventory is not just an asset; it is a competitive edge."