Choosing the Best CMMS: Key Features and Options
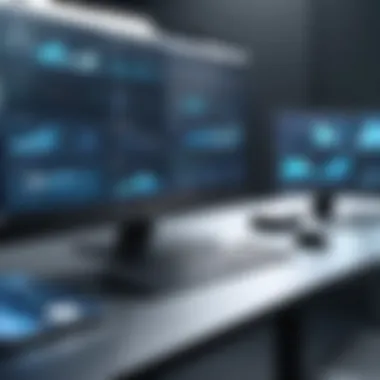
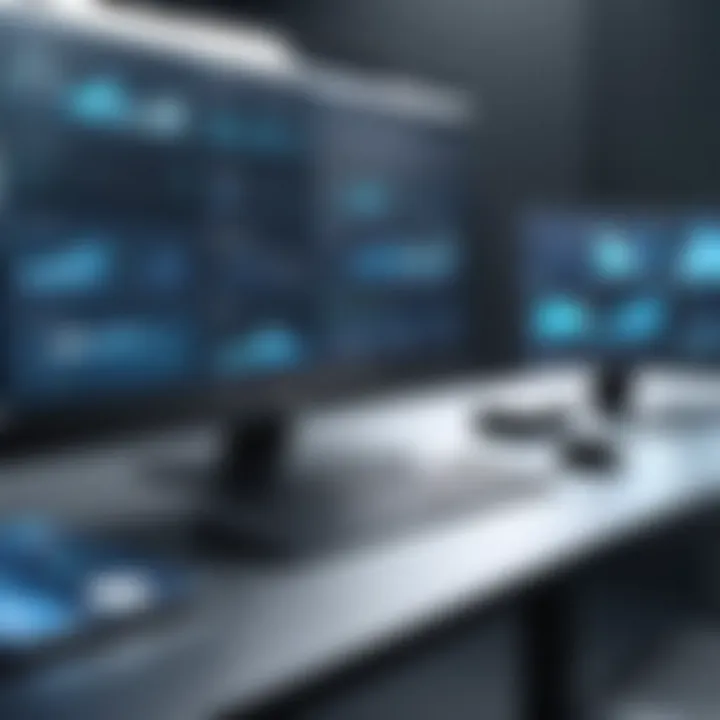
Intro
In today's fast-paced business environment, selecting the right Computerized Maintenance Management System (CMMS) can feel like trying to find a needle in a haystack. For organizations striving to enhance their maintenance processes, understanding what makes an ideal CMMS is key. This guide aims to illuminate the path towards making an informed choice, diving deep into critical software features, comprehensive metrics for comparison, and the nuanced requirements specific to various industries.
Choosing a CMMS isn't just about picking a piece of software; it’s about aligning a system that meets your unique operational needs while also propelling your organization toward its long-term goals. Whether you are a decision-maker in an established industrial service firm or a tech-savvy entrepreneur venturing into maintenance management, grasping what to look for is essential.
In the sections that follow, we will break down the fundamental characteristics of CMMS, explore advanced capabilities, and identify vital comparison metrics. The breadth of information provided will not only help clarify the features you may already be aware of but will also introduce you to lesser-known functionalities that can significantly impact your maintenance management approach.
By the end, you'll be equipped with the knowledge to sift through the myriad of options on the market, enabling you to choose a CMMS that doesn't just tick boxes but truly resonates with the heart of your organization's operational strategy.
Prelims to CMMS Systems
The landscape of maintenance management is changing rapidly, and at the heart of this evolution lies the Computerized Maintenance Management System (CMMS). Understanding CMMS is not merely an exercise in technology; it’s about recognizing the pivotal role it plays in modern organizations. With machines and equipment becoming increasingly complex, maintaining them effectively requires more than traditional methods. A CMMS facilitates not only the smooth operation of assets but also drives efficiency across various functions within an organization. It’s a blend of technology and management practices that can mean the difference between operational success and costly inefficiencies.
Definition and Purpose of CMMS
A Computerized Maintenance Management System is software that helps organizations streamline their maintenance operations. At its core, a CMMS collects, tracks, and organizes information about an organization’s assets and maintenance activities. The main purpose? To ensure that equipment remains in good running condition while prolonging its lifespan, minimizing downtime, and reducing maintenance costs.
But what exactly does a CMMS do?
- Asset Tracking: It keeps a detailed register of all assets and their specific maintenance needs.
- Work Order Management: Users can create, track, and close work orders efficiently.
- Preventive Maintenance Scheduling: The system automatically schedules maintenance tasks before issues arise, which fosters proactive management.
- Data Analytics: A CMMS provides valuable insights through reporting and data analysis, allowing decision-makers to make informed choices about maintenance priorities.
This sophisticated tool thus assists organizations in transitioning from a reactive maintenance strategy to a preventive one, promoting a culture of foresight and responsiveness.
The Role of CMMS in Maintenance Management
In the ever-evolving world of business, maintenance management is far from static. A CMMS stands as a cornerstone, underscoring its role in effective maintenance planning. By automating routine tasks, it not only saves time but also allocates resources more effectively, enabling teams to focus on critical operational needs.
When maintenance teams utilize a CMMS, several benefits arise:
- Improved Communication: The system facilitates better communication among team members by centralizing all maintenance data, making it accessible to everyone involved.
- Increased Accountability: With work orders logged, there is a clear record of who is responsible for what, making accountability seamless.
- Cost Reduction: Minimizing unforeseen failures reduces repair costs significantly, making maintenance budgets easier to manage.
- Regulatory Compliance: Many industries face strict regulations, and a CMMS aids in maintaining compliance by ensuring that maintenance schedules are followed and documented.
This synergy between technology and practice can transform maintenance management from a back-office function to a strategic asset within any organization. Thus, understanding how and why to implement a CMMS is crucial for any decision-maker looking to enhance operational efficiency.
"Adopting a CMMS isn't just about managing tasks; it’s about reshaping how an organization views maintenance as a strategic function."
From these perspectives, organizations can appreciate the comprehensive benefits that a well-implemented CMMS can offer. It’s not just a software solution; it’s a means to foster a culture of proactive maintenance that supports long-term organizational growth.
Key Features of an Effective CMMS
As organizations seek to enhance their maintenance management practices, understanding the key features of an effective CMMS becomes pivotal. This section focuses on core functionalities that not only streamline processes but also drive substantive improvements in efficiency, compliance, and overall asset performance. An effective CMMS should act as the backbone of maintenance operations, making it easier for teams to maintain their assets while optimizing resource allocation and minimizing downtime.
Asset Management Functions
Effective asset management serves as the cornerstone of a robust CMMS. By providing a clear overview of all assets, organizations can develop informed maintenance strategies. An effective asset management function enables users to track the complete lifecycle of each asset, from acquisition to retirement. This functionality encourages better decision-making about when to replace or upgrade equipment.
Moreover, asset management in a CMMS enhances compliance with industry standards. By logging maintenance history and supporting automated reporting features, the system can help organizations adhere to regulations, which is increasingly necessary across various sectors.
Work Order Management
Work order management represents a lifeline within a CMMS, as it mediates the day-to-day operations of maintenance teams. This section breaks down three critical aspects:
Creating Work Orders
Creating work orders is essential for organizing maintenance tasks efficiently. This feature helps to capture all necessary details about the requested work, including priority levels, detailed descriptions, and assigned personnel. By standardizing how work orders are created, organizations can reduce confusion and ensure clarity in expectations. A notable characteristic is the ability to attach documents, images, or even maintenance history data, which can provide technicians with a comprehensive view before they arrive on-site.
Unique to creating work orders is the flexibility in templates that can be tailored according to different needs, thus making it easier for teams to use the system. The benefit here is twofold: standardization across the board leads to greater accountability and improved scheduling of tasks.
Assigning Tasks
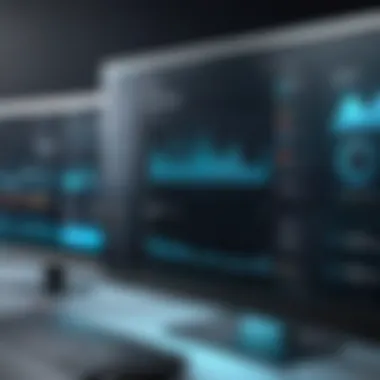
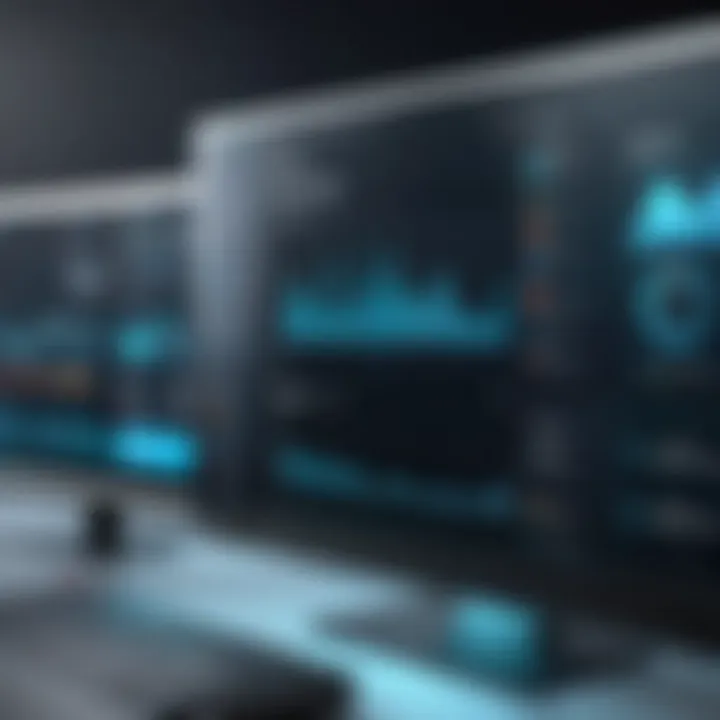
The assignment of tasks within a CMMS is crucial in ensuring that the right people tackle the right jobs. This feature allows managers to allocate work orders based on technician skills, availability, and workload. By efficiently assigning tasks, organizations can drastically cut down on response times and enhance team productivity. An important aspect of task assignment is that it provides a clear line of responsibility that can improve accountability and track performance.
However, one must consider the potential downside; if the task assignment process is overly rigid, it may not allow for flexibility in personnel management. Thus, a smart balance must be struck here.
Tracking Progress
Tracking progress serves as a vital part of the work order management process. This feature allows users to monitor job status in real time, updating on completion as well as any issues encountered along the way. By constantly tracking the progress of work orders, organizations can maintain transparency and provide updates to stakeholders promptly.
What sets tracking progress apart is the generation of reports and insights from the data collected. These analyses can reveal trends in maintenance efficiency, pinpoint recurring issues, and highlight areas that need improvement. The downside, though, is that it requires a cultural shift within the organization to embrace continuous monitoring and improvement strategies.
Preventive and Predictive Maintenance
Preventive and predictive maintenance strategies are not just buzzwords but essential features of a well-rounded CMMS. Preventive maintenance focuses on scheduled maintenance activities to ward off failures before they occur. This aspect reduces the odds of unexpected equipment breakdowns and expensive repairs.
On the other hand, predictive maintenance leverages data analytics and sensors to assess equipment health in real time, allowing organizations to plan maintenance before a potential failure occurs. By integrating both preventive and predictive maintenance, CMMS users can transition from a reactive to a proactive maintenance approach.
Considerations for Selecting a CMMS
When it comes to choosing the right Computerized Maintenance Management System (CMMS), the decision isn't just a walk in the park. It requires careful thought and consideration of various facets that can significantly impact your organization's maintenance processes. By understanding what to look for, decision-makers can avoid pitfalls and ultimately select a tool that aligns perfectly with their operational needs.
Understanding Your Organization's Needs
Before diving into the sea of options available, it’s crucial to take a step back and truly understand your organization's current and future needs. Each business is unique; one-size-fits-all solutions just won’t cut it if you want to optimize your operations.
Start with an assessment of your existing workflows. Consider what maintenance challenges your team faces, and identify gaps in your current processes. For example, does your team struggle with excessive downtime or recurrent equipment failures? Do you find it difficult to track and manage your assets effectively? All of these questions help you gauge the specific functionalities you need from a CMMS.
Moreover, it’s important to think about scalability. As your organization grows, so should your CMMS capabilities. If you envision expansion in the near future, ensure the selected system has the flexibility to accommodate additional devices, users, and processes. Mapping out your requirements now can save you time, hassle, and expenses down the line. Once you have a clear picture of your organizational demands, you’ll be in a stronger position to pick the CMMS that best fulfills those needs.
Budget Constraints and Cost Analysis
Of course, any discussion about selecting a CMMS inevitably leads to the dollars and cents. While it’s tempting to focus solely on upfront costs, a comprehensive cost analysis should factor in both short-term expenditures and long-term savings.
Here's a breakdown of important aspects to consider:
- Initial Investment: What is the price tag of the software? Make sure to factor in not just the purchase price, but also installation and setup costs.
- Ongoing Costs: Are there subscription fees? Licensing fees? Maintenance costs? These can vary widely and can sneak up on you.
- Training Costs: Will your staff need training? Ensure you have budget for that, as effective training is key for user engagement and system utilization.
- Return on Investment (ROI): Consider how the CMMS will save you money over time. Will it reduce downtime? Improve efficiency? The ROI can be a powerful deciding factor, helping you to justify the costs to stakeholders.
By analyzing all these factors, you’re better equipped to wield your budget wisely. Remember, the cheapest option isn’t always the best option. Sometimes spending a bit more upfront can yield substantial savings in the long run.
User Interface and Ease of Use
A CMMS can be packed to the brim with features, but if its user interface looks like it’s from the Stone Age, you might find your team rallying against it. The user experience is paramount. Employees should feel comfortable navigating their new tool, otherwise, you may face resistance or underutilization, which leads to wasted investment.
When evaluating different systems, take the following into account:
- Intuitive Design: Is the system easy to navigate? Are the key functions readily accessible? A cluttered interface can deter users, making it vital for you to find something that feels user-friendly.
- Customization Options: Does the software allow for tailored dashboards and reports? Being able to adapt the interface to suit specific roles and preferences can significantly enhance user experience.
- Mobile Accessibility: In today’s fast-paced work environments, having mobile capabilities isn’t merely a luxury; it's a necessity. Ensure that your CMMS is accessible on mobile devices, allowing maintenance teams to access crucial information on-the-go.
Ultimately, a sleek and easy-to-use interface can boost productivity by ensuring your staff spends less time figuring out how to use the system, and more time getting their jobs done right.
In essence, selecting a CMMS isn’t just about technology; it's about understanding what will work best for your organization and its people.
By considering these factors carefully, you can make a well-rounded decision that not only meets your current needs but also aligns with your long-term goals. Choosing the right CMMS means much more than purchasing software; it means setting the stage for a more efficient maintenance process.
Leading CMMS Solutions in the Market
In the realm of maintenance management, the selection of a suitable Computerized Maintenance Management System (CMMS) serves as a pivotal foundation upon which efficient operations are built. This section delves into leading CMMS solutions in the market, highlighting their unique offerings and relevance in today's ever-changing industrial landscape. Understanding these solutions is crucial for decision-makers, as each option can significantly influence how maintenance tasks are executed and managed.
Overview of Market Leaders
The market is filled with various CMMS platforms, each boasting its own strengths. Industry leaders have emerged, not only because of their technological capabilities but also their commitment to innovation and user satisfaction. Some of these prominent players include Fiix, Hippo CMMS, and Asset Essentials. These platforms distinguish themselves through robust functionality, flexibility, and customer support.
Time and again, feedback from professionals in various sectors emphasizes the need for reliable solutions that cater to both large and small organizations. As such, market leaders tend to focus on continuous enhancements, ensuring their software evolves to meet the fluid demands of maintenance management. One critical aspect is the integration capabilities these systems offer, allowing them to work seamlessly with other operational software.
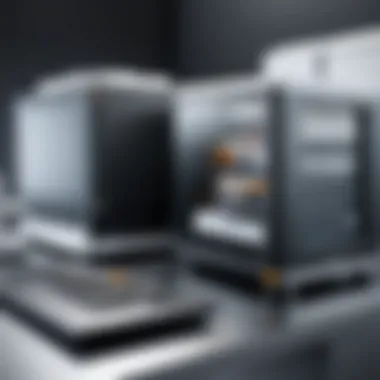
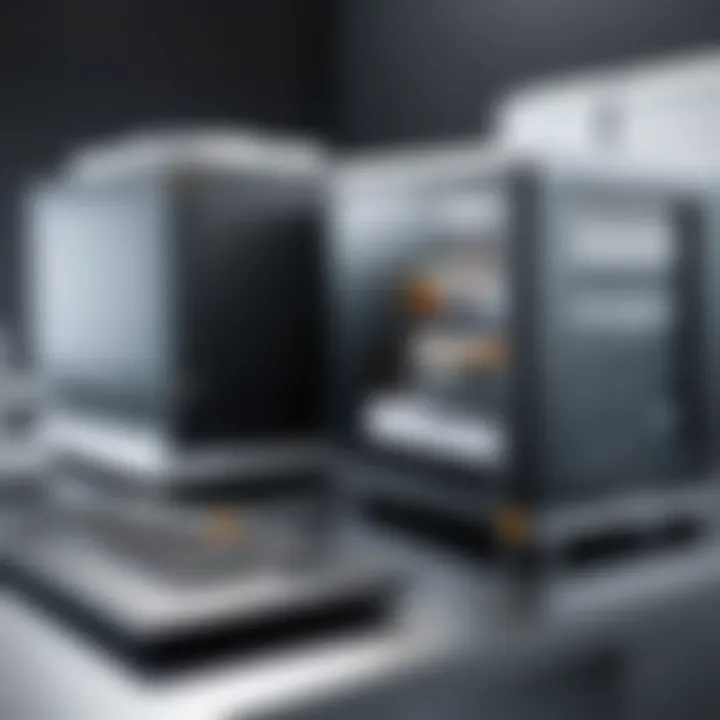
Comparative Analysis of Top CMMS Tools
When it comes to selecting the right CMMS, a comparative analysis helps in discerning the appropriate choice based on organizational needs. Below, we discuss three CMMS tools that stand out in the marketplace:
System A Overview: Fiix
Fiix is often heralded for its user-friendly interface and flexibility. It allows users to manage work orders effectively and conduct preventive maintenance easily. The key characteristic of Fiix is its cloud-based accessibility, which means that users can manage their maintenance processes from virtually anywhere. This beneficial feature allows for real-time updates and collaboration across teams. However, my experience shows that more advanced features might come with a steeper learning curve, which some users find cumbersome, especially when first transitioning.
- Unique Feature: The mobile application helps technicians access information on-the-go, boosting productivity on the ground.
System B Overview: Hippo CMMS
Hippo CMMS carries a reputation for excellent support and comprehensive asset management functions. Its straightforward operations make it a popular choice, particularly among smaller businesses aiming for simplicity without sacrificing functionality. Its user-friendly dashboard makes navigating tasks a breeze, attracting many users looking for an easy-to-adopt solution. One downside is the limited customizability some users experience, which can be problematic for companies with unique maintenance needs.
- Unique Feature: Robust reporting capabilities allow organizations to track performance metrics effectively, supporting informed decision-making.
System Overview: Asset Essentials
Asset Essentials shines with its focus on work order management and scheduling. This system is particularly appealing to companies needing in-depth scheduling and tracking solutions, making it a beneficial choice for industries with complex maintenance requirements. Users appreciate the detailed analytics that come with it, offering insights into operational efficiency. On the flip side, the sheer volume of features available can be overwhelming for new users, possibly leading to a steeper initial adjustment phase.
- Unique Feature: The integration of mobile technologies enhances ease of use by enabling technicians to perform inspections and log data straight from their devices.
Through this comparative analysis of leading CMMS tools, decision-makers can gauge their unique offerings and identify which system may align best with their operational needs. Each platform has its merits and subtle intricacies, making it essential for organizations to evaluate their specific requirements before making an investment.
Evaluating CMMS Vendor Support
When it comes to picking a Computerized Maintenance Management System, gauging the vendor support is nothing short of pivotal. A strong vendor support system ensures that organizations can smoothly navigate the challenges that come with implementing and utilizing a CMMS. You might think you’re buying just software, but what you’re really investing in is the vital backbone of your maintenance management hustles. Without proper vendor support, even the best system can turn into a burden rather than a benefit.
Importance of Customer Support
Customer support acts as the lifeline of a CMMS solution. Imagine you’re in the middle of a production run, and a critical module of your CMMS hiccups. If you don’t have effective customer service in your corner, what do you do? You could find yourself staring at a screen, feeling lost and nearly hopeless. Quality customer support not only resolves issues but also provides users with the confidence to groom their operations effectively.
Key advantages of dependable customer support include:
- Quick Resolutions: A team that understands the software inside and out can resolve your queries swiftly, minimizing downtime.
- Personalized Assistance: Every organization has its quirks. Custom solutions tailored to your specific setup can make all the difference.
- Proactive Guidance: Ongoing support proactively helps to prevent issues before they become real problems.
The takeaway here is clear: without a solid customer support network, users jeopardize their ability to maximize the potential of their chosen CMMS.
Training and Resources Provided by Vendors
Investing in a CMMS is only the first step; proper training and resources from the vendor can significantly expedite the learning curve. When vendors offer adequate educational materials, your team is likely to utilize the software to its fullest. Think about this: no one wants to feel like they're fumbling in the dark when using advanced technology. If the training provided is comprehensive, reducing hesitance and frustration among users becomes easier.
Typical resources that should be provided by CMMS vendors include:
- Hands-On Training Sessions: Workshops that allow users to familiarize themselves with the software can be invaluable.
- Comprehensive User Manuals: A user-friendly manual can serve as an excellent reference to clarify doubts post-training.
- Webinars and Online Tutorials: Regular updates on software tools, features, or best practices through online formats can keep everyone in the loop.
Inadequate training can leave users feeling like a fish out of water. Therefore, the quality of training directly influences the overall adoption and success of the CMMS system within an organization.
"Choosing the right vendor does not merely hinge upon the features of the software, but rather their commitment to support and ongoing education, ensuring that users can thrive."
In sum, effective evaluation of CMMS vendor support involves scrutinizing both customer assistance and training resources. A CMMS is more than a piece of software; it’s a partnership between technology and continuous support that allows businesses to effectively manage maintenance operations.
Case Studies of Successful CMMS Implementations
Examining case studies of successful Computerized Maintenance Management System (CMMS) implementations can provide invaluable insights for organizations looking to optimize their maintenance processes. These real-world examples not only highlight effective strategies but also underscore the tangible benefits that a well-integrated CMMS can bring.
Understanding these case studies helps decision-makers see that implementing a CMMS isn’t just about adopting software; it’s about transforming how maintenance is managed and making that leap successfully. Organizations of all shapes and sizes have shared their journeys, and each story reveals elements worth considering—challenges faced, solutions implemented, and the overall impact on efficiency and performance.
Industry-Specific Examples
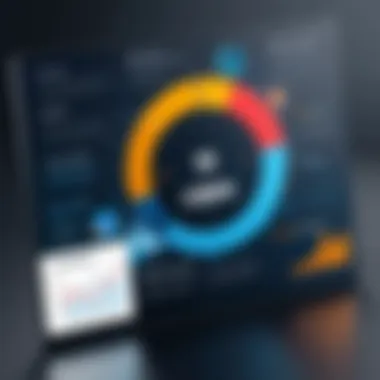
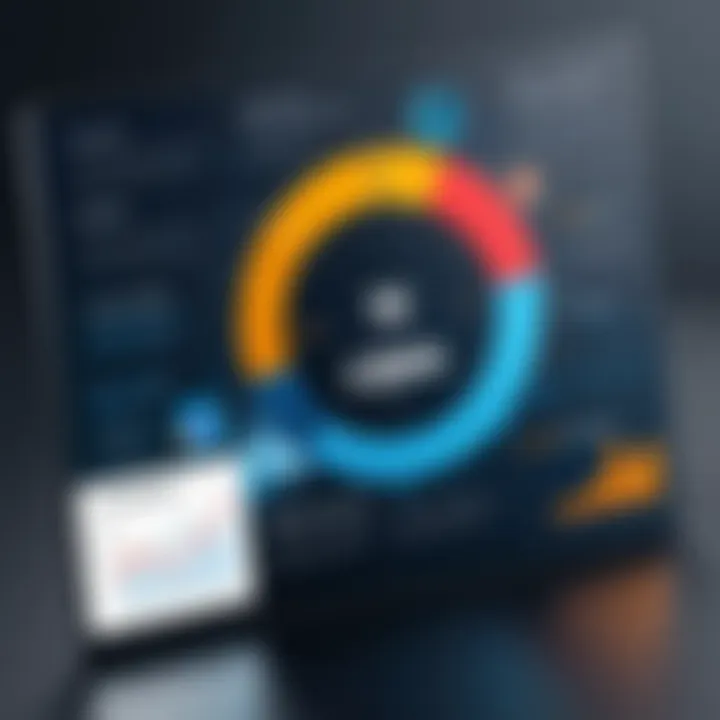
Different industries showcase varying degrees of CMMS application, emphasizing the system’s adaptability. Here are some notable illustrations:
- Manufacturing Sector: One of the largest manufacturers in the automotive sector deployed a CMMS to reduce downtime caused by equipment failures. By integrating predictive maintenance features, they reported a 30% reduction in unexpected failures over a year. This led to smoother production lines and fewer delays.
- Healthcare Facilities: A mid-sized hospital integrated CMMS to enhance their asset management for medical equipment. This implementation resulted in improved tracking of maintenance schedules and compliance reporting. They witnessed an 18% reduction in equipment downtime, allowing them to provide better care to patients.
- Educational Institutions: A large university adopted CMMS after facing issues with building maintenance. The system allowed for efficient work order management, leading to faster response times from facilities staff, improving student satisfaction from 75% to 92% in maintenance-related surveys.
These instances indicate that irrespective of the domain, a well-implemented CMMS leads to notable improvements in operational efficiency and service delivery.
Lessons Learned from Real-World Applications
From these case studies, several key lessons emerge that can guide future CMMS implementations:
- Tailored Configurations: Organizations should not merely pick a generic solution. They must assess their specific needs and tailor the CMMS functionalities accordingly. A one-size-fits-all approach often leads to underutilization of the system.
- Staff Training is Crucial: Successful adoption of any system hinges on how well staff can utilize it. Investing in comprehensive training ensures that staff is comfortable navigating the CMMS, leading to more effective use and enhanced productivity.
- Continuous Evaluation and Improvement: After initial implementation, organizations must regularly evaluate the CMMS system’s effectiveness. Gathering feedback from end users and making adjustments as necessary can keep the process agile and aligned with evolving needs.
- Integration Capabilities: Look for systems that can seamlessly integrate with existing technology stacks. For instance, a CMMS that syncs with inventory management software can provide insights that improve not just maintenance but also procurement and supply chain operations.
- Management Buy-In: For any CMMS initiative, top-level management support is essential. Decision-makers need to share the vision behind the implementation, creating a culture open to change and innovation.
"The implementation of a CMMS is not just an IT project; it’s a vital organizational transformation that requires buy-in from all levels."
Future Trends in CMMS Technology
As the landscape of maintenance management continues to evolve, the future of Computerized Maintenance Management Systems (CMMS) is intertwined with advanced technologies. Understanding these trends is crucial for organizations aiming to enhance their maintenance strategies. By keeping an eye on emerging innovations, decision-makers can pinpoint opportunities for optimization and efficiency.
One pivotal trend is the integration with the Internet of Things (IoT). With more machines and equipment becoming smart, the need for CMMS to incorporate IoT is more pronounced than ever. It allows for real-time monitoring of assets, providing valuable data about their performance and condition. Organizations can reap significant benefits from this integration:
- Predictive Maintenance: By collecting data from equipment sensors, businesses can predict failures before they occur. This proactive approach minimizes downtime and saves costs associated with unexpected breakdowns.
- Enhanced Reporting: IoT devices can relay information to CMMS platforms, which, in turn, offer advanced analytics. These insights help organizations make data-driven decisions about maintenance schedules.
- Resource Optimization: With better understanding of machinery usage patterns, resources, including labor and materials, can be utilized more effectively.
However, there are considerations to be mindful of. Implementing IoT requires a robust IT backbone and potentially significant initial investment. Organizations must evaluate their readiness for such a leap and assess how it fits into their broader strategic goals.
Another crucial trend is the adoption of artificial intelligence (AI) in maintenance management. AI has the power to revolutionize how CMMS systems operate. Here are some noteworthy elements and benefits of AI integration:
- Automated Decision Making: AI can process vast amounts of data quickly. This allows CMMS to recommend maintenance schedules automatically based on usage patterns and historical data, empowering maintenance teams to focus on other critical tasks.
- Anomaly Detection: AI algorithms are adept at detecting unusual patterns in machine performance. This capability enables organizations to address potential issues before they escalate, ensuring operational efficiency.
- Personalized User Experience: AI can learn from user interactions, streamlining the interface for greater ease of use. This adaptability enhances user satisfaction and efficiency in task completion.
Despite these advantages, the move toward AI integration isn't without challenges. Organizations must ensure they have the skill sets necessary to harness AI effectively. Training employees on new systems is essential to maximize these technologies' benefits.
"The future of maintenance management will not just be about reacting to problems but anticipating them before they occur."
Finale
In summary, staying ahead in CMMS technology by embracing IoT and AI can provide substantial edge to organizations in the maintenance sector. By transforming data into actionable insights and enhancing operational efficiencies, these trends are poised to shape the future of how maintenance is managed.
The End: Making the Right CMMS Choice
In the world of maintenance management, selecting the right Computerized Maintenance Management System (CMMS) can greatly influence the operational efficiency of an organization. This choice is not just about picking a software; it’s about aligning it with your organizational goals, understanding your maintenance needs, and ensuring a smooth transition into enhanced maintenance practices.
Choosing a CMMS is like choosing a new set of tires for your car. You wouldn’t just grab any old ones at the store because they cost less. Instead, you would consider the climate, the kind of driving you do, and how often you’ve traveled with that vehicle. Similarly, the right CMMS should fit the unique demands of your organization, boosting both productivity and cost-effectiveness.
When you look at this process, it highlights critical elements, such as user interface, functionality, and vendor support. The right system should streamline your workflows and eliminate unwarranted bottlenecks. It’s essential for decision-makers and IT professionals to take the time to weigh these factors thoroughly.
Key areas to regard include:
- The specific functionalities that will support maintenance tasks.
- Your existing budget and whether the potential ROI justifies the cost.
- The ease of use and training necessary for staff to leverage the system effectively.
By being thoughtful about these considerations, organizations can make a well-informed decision that serves them for years to come.
Summing Up Key Takeaways
Reflecting on the journey through this guide, there are several takeaways for professionals looking to choose the ideal CMMS:
- Understand Your Needs: Always start by assessing your organization’s specific requirements. This groundwork is crucial to avoid choosing a system that fails to meet expectations.
- Evaluate Features: Look for essential features tailored for your maintenance activities, particularly those that can enhance asset management and work order processing.
- Vendor Support is Key: A solid support structure can make or break the success of your CMMS. Don’t overlook this aspect when comparing different systems.
Here's a quick checklist to consider as you come to a decision:
- Have you listed down your must-have features?
- Does the CMMS offer training and support that meets your team’s needs?
- Have you calculated the total cost of ownership and not just the initial purchase price?
Final Thoughts on CMMS Selection
In wrapping up, the importance of a CMMS cannot be overstated. It’s a vital tool for any maintenance operation aiming for efficiency and efficacy. But remember, the selection process isn’t just about evaluating vendor options; it should involve a deep dive into aligning the system’s capabilities with your organization’s strategic goals.
As you stand on the brink of this decision, consider taking a phased approach. Testing out a few systems on trial can provide hands-on insight into what truly works for your team. Also, ensure to gather feedback from those who will be using the system daily, as their insights can highlight aspects that decision-makers may overlook.
Ultimately, while the path to choosing a CMMS can be laden with complexities, it’s an investment worth pursuing. Your operations will likely enjoy increased productivity, fewer downtimes, and a clearer roadmap for the future. Stay patient and diligent, as the right choice in a CMMS can transform maintenance management into a strategic advantage.